What is HDI Printed Circuit Board?
High Density Interconnect PCBs are becoming more and more important in the field of PCBs and electronics. However, there is an increasing need for smaller and lighter electronic components to operate. You need to add more functions in a smaller space to handle this. HDI boards help you achieve this goal.
What is HDI Printed Circuit Board?
HDI Printed Circuit Board have a higher density of circuits per unit compared to traditional PCBs. Depending on the purpose, they are manufactured using various materials, such as FR4, metal, fiberglass, etc. In addition to microvias with a diameter of less than 0.006 inches, they also adopt buried vias and blind vias. High-density circuit boards have all of the following characteristics:
Use tunnels and underground tunnels.
Use straight through tubes from one surface to another.
At least two layers should have through holes.
Layer-by-layer structure without central core
Electrically inert structure, also known as passive substrate
Use layer pairs instead of coreless build structure
Many of the modern electronics we use, especially those that have been greatly reduced in size and weight in recent years, are attributed to HDI technology in printed circuit boards and elsewhere. HDI technology is more likely to be used in smaller devices.
High-density interconnect PCBs have very tight tolerances, so experienced suppliers are needed. Even minor defects or layout errors can have a significant impact. Millennium Circuits Limited, a leading HDI printed circuit board supplier, can provide high-quality boards with much greater circuit density than standard PCBs.
Advantages of HDI Technology
HDI technology offers several advantages over other options that can help your project reach its full potential. If you use the right design and appropriate sources, HDI boards can improve the overall quality and performance of your product, as well as customer satisfaction and profits.
Better Functionality
HDI boards allow you to fix additional components on both sides of the bare PCB, thereby squeezing more functions into a smaller area and improving the overall functionality of your device. HDI technology allows you to increase the functionality of your product while reducing its size and weight.
Reduced Power Consumption
The increase in the number of transistors and the reduction in the distance between components may improve electrical performance. These features reduce power consumption, which enhances signal integrity. Smaller size means faster signal transmission, less total signal loss, and less crossover delay.
Cost-effective
HDI boards may be more cost-effective than other solutions because they are smaller in size and require fewer layers, so less raw materials are used. You can use a single HDI board for products that previously required multiple standard PCBs. Less space and less material are needed to achieve the same functionality and value.
Multiple Outcomes of Limited Material Use
By using less material in your product, you gain many benefits, including reduced manufacturing time and faster time to market, as HDI technology is able to reduce the number of components used in your product. High-density interconnect (HDI) PCBs are easy to use, and their high electrical performance minimizes testing and troubleshooting time.
HDI PCB Concept Design Considerations
It is not uncommon for HDI Printed Circuit Board to be produced differently than other PCB types. You should know the following about HDI board manufacturing and specific design issues to keep in mind during production:
Sequential Lamination
Multilayer PCBs require the use of heat and pressure to connect the PCB core and any prepreg layers before adding subsequent laminate layers. The heat and pressure required vary greatly from board to board.
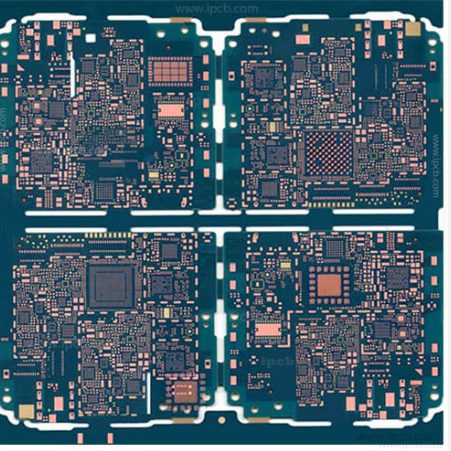
Via-in-Pad Process
After lamination is complete, they are drilled into the PCB. HDI boards require this process more than other types of PCBs. Using continuous lamination avoids shifting and breaking, making drilling more efficient.
Types of Via Fill
Your PCB planes can be filled with one of several fill types and then plated using a via-in-pad manufacturing process that enables you to surface mount vias in a via-in-pad. The standard via-in-pad process involves approximately 10 to 12 steps, which requires specialized equipment and trained experts.
The type of via fill you choose must match the needs of your application and PCB. Electrochemical plating, silver fill, copper fill, conductive epoxy, and non-conductive epoxy are the basic fill materials used by PCB manufacturers on a daily basis. Non-conductive epoxy is the most common fill material for vias. It is critical to select a complete fill layer, including pads and solder.
The fill must enable blind, buried, or drilled vias for both microvias and regular holes that may subsequently be plated to hide behind SMT pads. To verify that the drilling operation is completed correctly every time, PCB manufacturers will often repeat the drilling cycle at precisely controlled depths. Achieving this level of control requires specialized equipment and longer development times.
HDI Structures
There are several different layout variations for high-density interconnect PCBs. The most common are 1-n-1 PCBs and 2-n-2 PCBs. 1-n-1 PCBs consist of a single high-density interconnect layer; thus it is the “simplest” version of an HDI printed circuit board.
It requires one continuous lamination on each side of the core. 2-n-2 PCBs contain two HDI layers and allow microvias to be staggered or stacked across layers. Complex designs often use copper-filled stacked microvia structures. Structures can reach extremely high XnX levels; however, complexity and cost often limit construction.
Another prominent option is any-layer HDI. This requires a very dense arrangement of HDI so that conductors on any given layer of the PCB can freely connect with the laser microvia structure. These architectures are found in GPU and CPU processors in smartphones and other mobile devices.
Laser Drilling Technology: Any-layer HDI systems typically require the use of laser drilling to generate the laser microvias. These drills produce lasers up to 20 microns in diameter, cutting through metal and glass to create tiny, clean holes. By using materials like uniform glass with a low dielectric constant, you can achieve even smaller holes.
LDI and Contact Imaging: You can’t fix anything in this process, so proper operation is critical. LDI is the preferred choice for fine lines and tiny pitches. This allows for continued functionality while allowing for smaller form factors.
Applications for HDI Boards
HDI technology is a critical component in many of today’s most advanced technologies. Electronic components, especially printed circuit boards (PCBs), have shrunk in size and cost due to advances in miniaturization. HDI Printed Circuit Boardcan be used in a variety of industries, here are some examples:
Smart Watches
Smart watches are essentially miniature personal computers, and today’s smart watches are made possible in part by HDI technology, whereas in the past, personal computers would have taken up an entire room. HDI boards can be used in a variety of consumer electronics, including computers, smartphones, tablets, and wearables.
IoT Devices
HDI boards are critical in bringing these advanced technologies to the masses. Home IoT devices, such as smart thermostats and refrigerators, also rely on these components to function. As smart devices become more popular, so too are HDI boards.
For Electronic Communications
HDI Printed Circuit Board may also be found in routers, switches, modules, and semiconductors. All electronic communications, computerized devices, and devices that use radio waves may be powered by HDI boards at some point in their existence. HDI technology is also found in digital video and audio equipment. These boards are common in both personal and enterprise devices.
Automotive and Other Transportation
Automotive and aerospace manufacturers can use HDI Printed Circuit Board to integrate more functionality into smaller, lighter devices. This is especially useful in the automotive and aerospace sectors, where lighter components can improve operational efficiency and save costs. Automotive PCBs are becoming more electronic and interconnected, just like nearly everything else.
For the functionality of various devices
Today, there are about 50 microprocessors in cars, all of which contribute to smooth engine operation, diagnostics, safety, and other amenities. The functionality of in-car WiFi and GPS, rearview cameras, and backup sensors all rely on HDI PCBs. As automotive technology further develops, high-density interconnect PCBs are expected to play an increasingly important role in automotive technology.
Applications in Medical Devices
Monitoring, imaging, surgical, and laboratory analysis equipment may employ HDI boards in advanced electronic medical devices such as MRI machines. High-density technology enables smaller, more economical devices that can improve the accuracy of monitoring and medical tests.
The use of HDI boards is increasing day by day, especially in IoT devices, due to cost-effectiveness and other additional advantages. With the increasing automation of industrial equipment, IoT devices are becoming more popular in manufacturing, warehousing, and different industrial environments. Many high-tech devices have adopted HDI technology.
The low material consumption and ability to provide more functions make HDI boards a good choice for utilizing a variety of devices.