What is a High Frequency PCB?
High-frequency PCBs are specialized circuit boards designed to transmit signals over a gigahertz (GHz) frequency range, ensuring quick and reliable communication in devices ranging from military radar systems to smartphones.
These boards maintain signal integrity even at high frequencies, which is crucial for the functionality and efficiency of modern electronic devices.
Stick around, and let’s explore what makes high-frequency PCBs a cornerstone of contemporary electronics!
Understanding High-Frequency PCBs
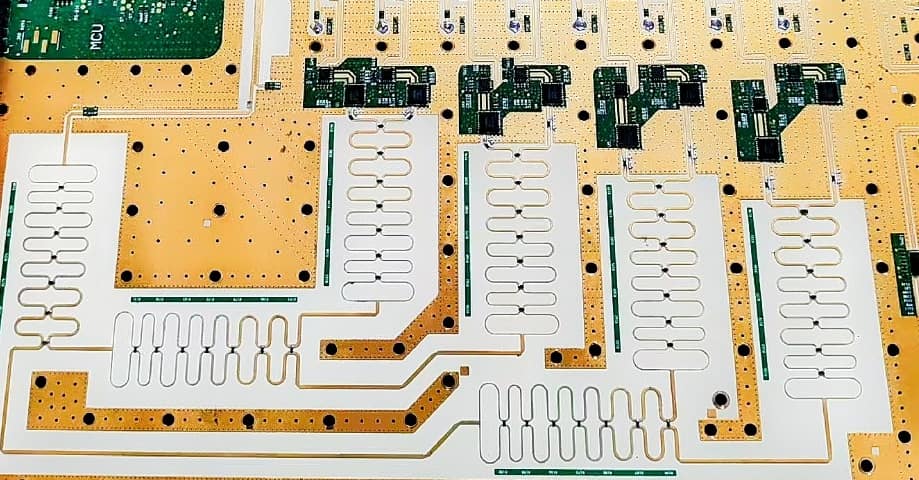
What Defines a High-Frequency PCB?
A High-Frequency PCB is a printed circuit board that operates at high frequencies. But what exactly does “high-frequency” mean? In simple terms, it refers to any frequency typically above 1 GHz.
This is much higher than what standard PCBs handle. These higher frequencies allow for faster data transmission, which is crucial for modern technology.
A PCB operating at such high frequencies must be specially designed to ensure the signals remain clear and accurate.
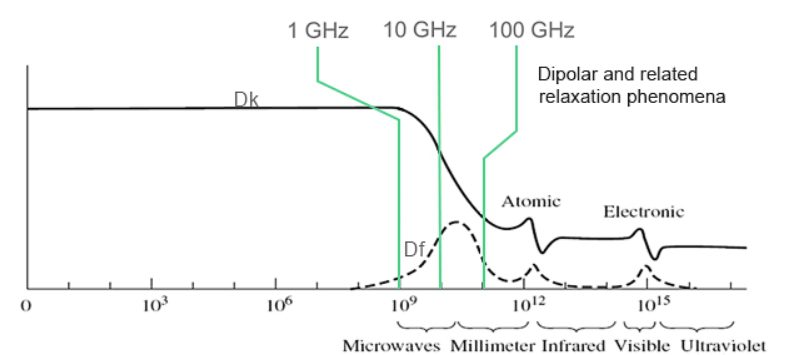
Key Characteristics
High-frequency PCBs have a few key characteristics that set them apart from regular PCBs. Let’s break them down:
Dielectric Constant (Dk)
One of the most important factors is the dielectric constant, often called Dk, Which measures how much the PCB material can store electrical energy. A low Dk is essential for high-frequency applications.
Why? Because a low Dk helps maintain signal integrity. In other words, it keeps the signal strong and clear as it travels through the board. If the Dk is too high, the signal can get distorted, leading to errors and slower performance.
Learn more about The Benefits of High Dk Materials.
Dissipation Factor (Df)
Another critical characteristic is the dissipation factor or Df. This measures how much energy is lost as the signal moves through the PCB. A low Df is crucial because it minimizes signal loss.
Imagine trying to have a conversation in a noisy room. The lower the noise, the easier it is for them to understand each other. Similarly, a low Df reduces the “noise” in the signal, keeping it clear and strong.
Thermal Stability
Thermal stability is another critical aspect of High-Frequency PCBs. Electronic devices generate heat as they operate. If the PCB material expands too much with heat, it can cause problems like signal distortion or even physical damage to the board.
That’s why High-Frequency PCBs need materials with low thermal expansion. These materials ensure the PCB remains stable, even in high-heat environments, keeping the signal consistent.
Moisture Absorption
Finally, we have moisture absorption. High-frequency PCBs must have low moisture absorption.
Why?
Because moisture can alter the electrical properties of the PCB, leading to signal loss or interference. Learn more about What is Signal Integrity in PCB Design?
Using materials that resist moisture, these PCBs maintain their performance, even in humid conditions.
Materials Used in High-Frequency PCBs
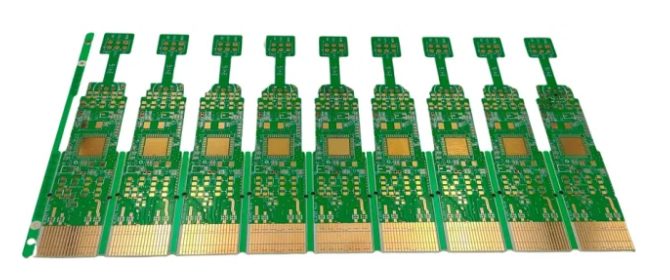
Commonly Used Materials
High-frequency PCBs require unique materials to perform well. Let’s examine some of the most commonly used ones.
PTFE (Teflon)
PTFE, commonly known as Teflon, is a favorite in high-frequency PCBs. Its very low dielectric constant (Dk) and dissipation factor (Df) make it ideal for these applications.
This means it can handle high-speed signals without losing much energy. It keeps the signal strong and clear.
PTFE is also stable, meaning it doesn’t change much with temperature, which is a big plus in electronics.
Rogers Materials
Another popular choice is Rogers materials. Specifically, the Rogers 4000 and 3000 series are widely used.
These materials are designed for high-frequency applications. Like PTFE, they offer a good balance of low Dk and low Df.
Rogers materials are known for being easier to work with during manufacturing, making them a go-to option for many engineers.
Other High-Frequency Materials
Other materials are also used. For example, Isola and Taconic are known for producing high-quality PCB materials.
These materials are also designed to have low Dk and Df, making them suitable for high-frequency applications.
Although they may not be as common as PTFE or Rogers, they are still excellent choices depending on the project’s specific needs.
Design Considerations for High-Frequency PCBs
Routing Techniques
Routing is vital to designing High-Frequency PCBs. One important concept is controlled impedance routing, which means keeping the electrical impedance of the PCB traces stable.
Why does this matter? If impedance varies, it can cause signal reflections. These reflections can distort the signal and hurt performance. So, stable impedance is crucial for clear signals.
Another thing to watch is trace width and spacing. Wider traces carry more current, which helps reduce signal loss. But spacing is essential, too. Traces need enough space to avoid interference.
Sharp angles in the traces should also be avoided. Sharp turns can cause reflections and weaken the signal. Gentle curves or 45-degree angles are better.
Learn more about Why Is Controlled Impedance So Important in PCB Design?
Impedance Matching
Impedance matching is vital in high-frequency PCB design. So, what does it mean? It’s about ensuring the signal path has consistent impedance from start to finish.
Learn more about Comprehensive Guide to PCB Design and Basics.
If there’s a mismatch, part of the signal can bounce back, degrading it. That’s why matching impedance is so important.
How do you achieve this? Designers adjust trace width and spacing to match impedance. Sometimes, they add resistors or capacitors to fine-tune it. The goal is a smooth path for the signal, with no loss of strength or clarity.
Grounding and Shielding
Grounding and shielding protect high-frequency signals from interference. A solid ground plane is critical. It gives the signals a stable reference point and helps cut down noise. It also provides a path for return currents, keeping the signals clean.
Shielding is also crucial. High-frequency signals are sensitive to electromagnetic interference (EMI). EMI can distort or destroy signals.
To prevent this, designers use shielding techniques. This could mean adding metal shields around sensitive parts or using ground planes to block unwanted signals. Good shielding keeps the signals intact.
Component Placement
Where you place components on a high-frequency PCB makes a big difference. Poor placement can degrade signals and increase noise. To avoid this, follow some simple rules.
First, keep high-speed components close together. This shortens the traces between them and reduces signal loss.
Also, keep traces short and direct. Long, winding traces pick up noise and hurt the signal. Place noisy components, like oscillators, away from sensitive parts. This helps keep noise from interfering with the signal.
Finally, place the decoupling capacitors close to the chips’ power pins. These capacitors smooth out voltage and keep the signals steady.
Learn more about How do PCB Capacitor Work and Why is it Important?
In short, designing high-frequency PCBs means paying close attention to routing, impedance matching, grounding, shielding, and component placement. Each step is crucial for keeping signals clear and the PCB working well in high-speed applications.
Applications of High-Frequency PCBs
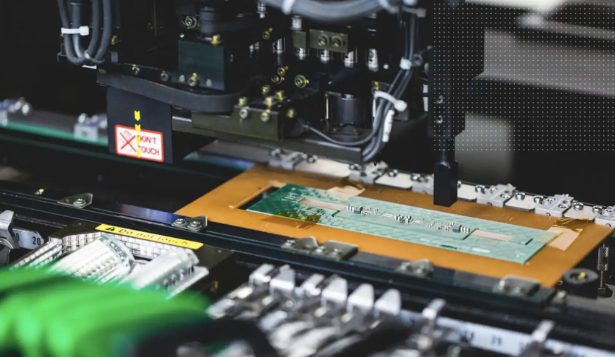
Telecommunications
High-frequency PCBs are vital in telecommunications and are essential to 5G infrastructure. 5G requires fast and reliable data transmission, and high-frequency PCBs make this possible. They ensure clear signals and quick communication.
These PCBs are also used in other communication technologies, such as Wi-Fi routers and mobile devices. They make our connections faster and more reliable. In a world that’s always connected, High-Frequency PCBs keep everything running smoothly.
Military and Aerospace
Precision is critical in the military and aerospace sectors. High-frequency PCBs are used in radar systems, which detect objects from far away, even in challenging conditions. The PCBs help ensure that the radar signals are accurate and reliable.
They are also essential in satellite communications. Satellites must send and receive data over vast distances, and high-frequency PCBs help maintain the integrity of these signals.
These PCBs are found in various defense systems equipment. They ensure that everything works flawlessly, from communication devices to advanced weaponry.
Medical Devices
Medical devices require high precision and reliability. High-frequency PCBs are used in diagnostic tools like MRI machines. Clear and accurate signals are a must in these devices, which help create detailed images of the human body.
Ultrasound machines also rely on High-Frequency PCBs. They provide the speed and clarity needed for real-time imaging, and doctors depend on them to diagnose and treat patients effectively.
Other medical devices, like heart monitors, also use these PCBs. They ensure that vital signs are accurately tracked and recorded.
Other Industries
High-frequency PCBs are not limited to just telecommunications, military, or medical fields. They are also widely used in other industries.
These PCBs are found in industrial automation equipment. They help control machines that require precise and fast communication.
They are used in the automotive industry’s advanced driver assistance systems (ADAS), which help keep drivers safe by providing real-time alerts and controls.
Consumer electronics, like high-end audio systems, also benefit from High-Frequency PCBs. They ensure clear, distortion-free sound quality.
Challenges in High-Frequency PCB Design
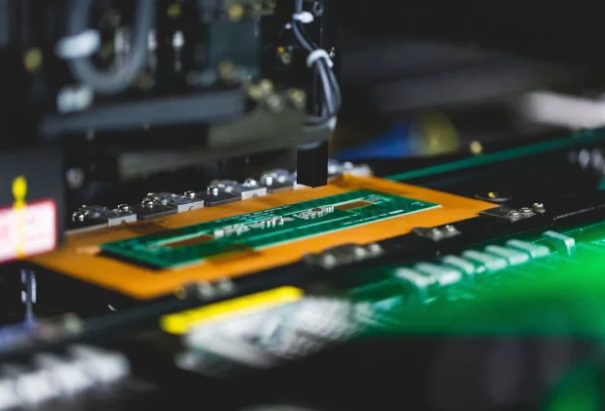
Signal Integrity Issues
Designing High-Frequency PCBs comes with its own set of challenges. One of the biggest issues is maintaining signal integrity.
Signals can quickly become distorted at high frequencies. Signal reflection is a common problem. This happens when the signal bounces back instead of moving forward smoothly. It can lead to errors and data loss.
Crosstalk is another issue. This occurs when a signal from one trace interferes with another. It’s like trying to have a conversation in a noisy room. The signals can get mixed up, causing confusion and reducing performance.
Both signal reflection and crosstalk need careful attention during design to keep the PCB functioning properly.
Material Costs
Another challenge is the cost of materials. High-frequency PCBs often require advanced materials like PTFE (Teflon). These materials are chosen for their excellent performance at high frequencies but are more expensive than standard PCB materials.
The high cost can be a barrier, especially for projects with tight budgets. However, the benefits of using these materials often outweigh the costs.
They provide better signal integrity and reliability, which are crucial for high-frequency applications. Still, managing these costs is a challenge designers and manufacturers must consider.
Manufacturing Complexity
Manufacturing High-Frequency PCBs is also more complex. These PCBs require tight tolerances, meaning everything must be made to exact specifications. Even a small mistake can affect the performance of the entire board.
Specialized materials like PTFE are harder to work with. They need careful handling during the manufacturing process. This adds to the complexity and requires specialized equipment and skilled workers.
Learn more about A Complete Guide To The PCB Manufacturing Process.
Another challenge is the need for precision. High-frequency PCBs often have very fine traces and small components.
This makes the manufacturing process more demanding. Ensuring that everything is placed and connected correctly is crucial for the board’s performance.
Future Trends in High-Frequency PCBs
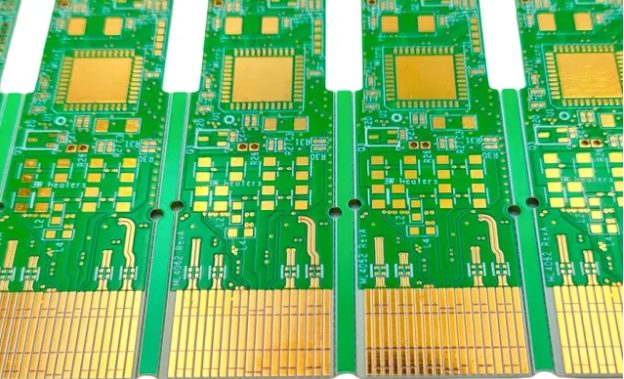
Emerging Materials
The future of High-Frequency PCBs looks promising. One exciting area is the development of new materials. Researchers are working on materials that can handle even higher frequencies.
These materials will offer better performance and more stability. They are designed to reduce signal loss even further.
As technology advances, these materials will play a crucial role. They will allow for faster and more reliable electronic devices.
Advanced Applications
High-frequency PCBs are about more than just current technology. They are paving the way for future innovations. One area to watch is artificial intelligence (AI). AI systems require fast and efficient data processing, and high-frequency PCBs will help make AI more powerful and responsive.
Another area is the Internet of Things (IoT). IoT devices need to communicate quickly and reliably.
High-frequency PCBs will ensure that these connections are strong and stable. As more devices connect to the internet, the demand for these PCBs will only grow.
Technological Advancements
The tools and processes used to design and manufacture PCBs are also improving. New design software is making it easier to create complex circuits, and these tools help designers optimize the layout for high-frequency signals.
On the manufacturing side, new techniques are emerging. These processes allow for more precise and efficient production.
This means fewer errors and better-quality PCBs. As these technologies advance, High-Frequency PCBs will become more accessible and reliable.
High-frequency PCBs are crucial for advancing modern technology, enabling the development of systems that require high-speed and high-quality signal transmission.
Their design carefully considers material properties, routing techniques, impedance matching, and effective grounding to ensure optimal performance in demanding applications.
Are you working on a project that requires high-speed, reliable performance? High-frequency PCBs might be just what you need. They are designed to meet the demands of modern technology. Consider using them in your next project for the best results.