Understanding Motor Controllers and Their Role in Modern Technology
1. What is a Motor Controller?
A motor controller is an electronic or electrical device used to regulate the speed, torque, and position of a motor. It can automatically or manually start, stop, and protect the motor from issues like overloads. Without a motor controller, motors would be at risk of electrical faults due to the high current requirements.
Why are motor controllers essential? Most microcontrollers (MCUs) can only supply around 0.1 Amps, but many motors require several Amps to operate. Motor controllers bridge this gap by enabling the proper amount of current to power the motor safely and efficiently.
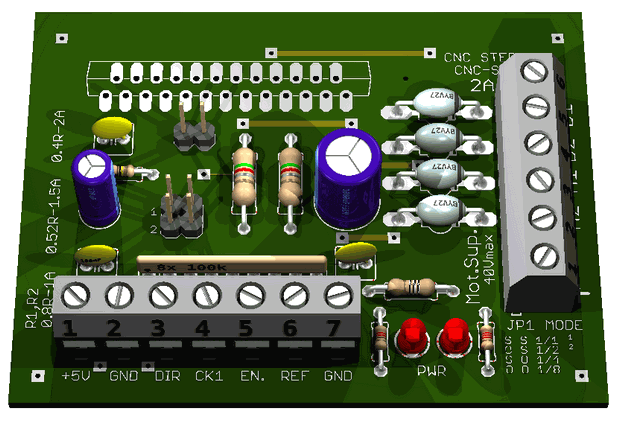
2. Types of Motor Controllers
Motor controllers can be categorized based on the type of motor they control. Here are the most common types:
- AC Motor Controllers: Used for controlling motors in household appliances and industrial equipment. They handle synchronous and asynchronous (induction) motors.
- DC Motor Controllers: Essential for devices requiring precise speed control, such as electric vehicles and robotics. These include brushed and brushless DC motors (BLDC).
- Servo Motor Controllers: Used in motion control systems like robotics, CNC machinery, and conveyor systems. They adjust the input power using pulse-width modulation (PWM) or current adjustments for high-precision control.
- Stepper Motor Controllers: Used for applications like 3D printers and CNC machines. They deliver precise position and speed control using stepped current outputs.
3. PCB Design Options for Motor Controllers
A motor controller requires a well-designed printed circuit board (PCB) to support its components and ensure stable performance. Here are six commonly used PCB types for motor controllers:
- Metal Core PCB (MCPCB): Known for excellent heat dissipation, often used in high-power circuits like power modules and IGBT modules.
- High-Frequency PCB: Used when high-speed communication or control signals are required, commonly found in power system feedback circuits.
- Heavy Copper PCB: Designed to handle high currents and withstand large power loads. It’s used for current paths in high-power motor controllers.
- Multilayer PCB: Offers multiple conductive layers, often used in microcontroller (MCU), FPGA, and DSP control units for better signal integrity and smaller design footprints.
- Flexible PCB (FPC): Flexible and lightweight, but not widely used in motor controllers due to lower current capacity.
- Hybrid PCB: Combines features of other PCB types to handle high power, heat dissipation, and high-frequency signals. Used in advanced drive modules and power correction circuits.
4. Key Components of a Motor Control PCB
A typical motor controller PCB includes the following key components:
- Microcontroller (MCU): Manages system logic and control signals.
- Gate Driver (ICs): Controls power switching devices like MOSFETs and IGBTs.
- Op-Amps: Used for feedback and sensing motor parameters like current and temperature.
- Comparators: Provides overcurrent protection, shutting down power when needed.
- Power Stage (MOSFETs & IGBTs): Drives the motor based on control inputs.
- Low-Voltage Power Supply: Powers the control and logic components.
- Voltage Regulators: Ensures stable voltage levels across the system.
5. Soldering Exposed Pads of IC Packages
Many motor control PCBs use ICs with exposed pads (like QFN or TSSOP) for better heat dissipation. Here’s a simple guide to solder them properly:
- Stencil Design: Design a stencil with cutouts matching the IC pads.
- Solder Paste Deposition: Apply solder paste evenly on the PCB pads.
- Component Placement: Place ICs carefully on the solder paste.
- Reflow Soldering: Heat the assembly in a reflow oven to melt and bond the solder.
- Thermal Management: Monitor the temperature to avoid overheating.
- Inspection: Inspect solder joints for quality, looking for solder bridges or voids.
- Cleaning: Clean off any residue to prevent electrical shorts.
6. Case Study: The MoonRanger Motor Controller
The MoonRanger’s motor controller is a great real-world example of a modern motor control system. It is housed in the Power Electronics Unit (PEU) and designed to control each brushless DC (BLDC) actuator for precise control of speed and torque.
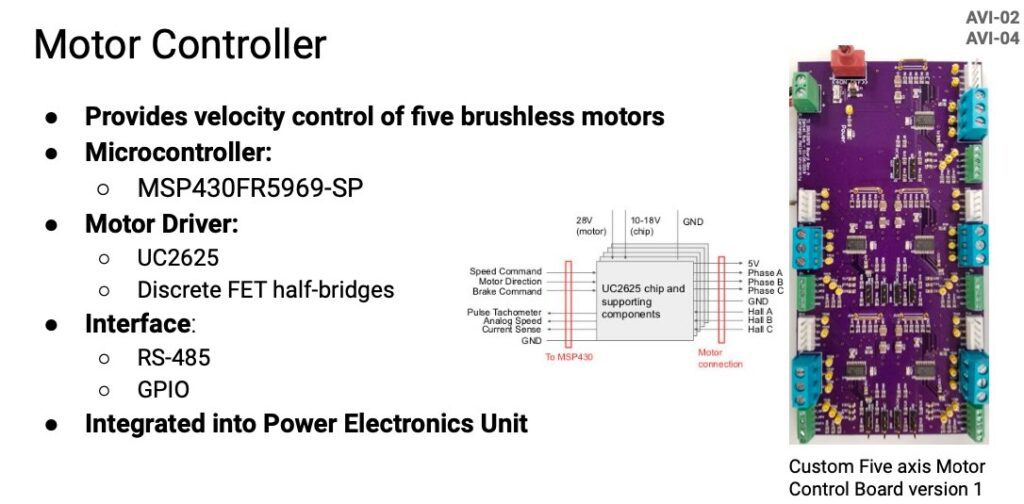
Key design features include:
- Gate Driver: Uses the space-rated TI UC1625-SP gate driver chip, which has a cost-effective alternative (TI UC2625) for prototyping on Earth.
- Microcontroller: An MSP430 microcontroller provides PID control to ensure precise speed adjustments and system stability.
- Protection: Overcurrent protection prevents actuator gearhead damage during high-torque events.
- Current Monitoring: Low-side current sense resistors provide real-time power draw feedback for each actuator.
- Design Philosophy: Conservative design, careful analysis, and rigorous testing ensure the hardware is reliable for spaceflight.
Summary
Motor controllers are essential for managing the performance of motors in devices like robots, electric vehicles, CNC machines, and home appliances. With different types like AC, DC, Servo, and Stepper controllers, each system is tailored to specific application needs. PCBs play a critical role in motor control systems, and their design choices impact efficiency, thermal management, and reliability. The MoonRanger’s motor controller is an advanced case study, demonstrating how proper design and testing can prepare motor controllers for spaceflight.