Ultimate Guide to Flexible PCBs: Types, Designs, and Applications
Flexible Printed Circuit Board (FPCB or Flexible PCB) is a PCB designed to be flexible and can be bent, folded, or twisted. FPC has a combination of multiple printed circuits as well as components located on a flexible substrate. It is usually made of polyimide film material, which ensures high flexibility and thermal stability. Thanks to its miniaturized design, it has increased innovation and applications in major electronic fields such as consumer electronics, automobiles, medical devices, wearable devices, telecommunications, and aerospace.
Flexible circuit boards take up less space and have higher reliability. You can bend it 360 degrees, and most of them are designed to bend 500 million times. The technology has been used in various forms to interconnect electronic devices since the 1950s. It is now one of the most important interconnect technologies in the manufacturing of many of today’s most advanced electronic products.
Types of Flexible Circuit Boards:
1) Single-Sided Flexible PCB:
Single-Sided Flexible Circuit Board is the most basic of the flexible PCB types. It consists of a substrate layer, a conductive copper layer, a cover layer, and a screen printing layer.
It has only one layer of flexible polyimide or polymer film, and the conductive copper layer is only on one side of the PCB, so the other side can be used to place various electronic components. Its simple design makes it suitable for a variety of applications and more affordable. Therefore, this is also the main reason why it has become the most widely used flexible circuit.
2) Double-sided flexible PCB:
Unlike single-sided flexible circuits, double-sided flexible circuit boards allow the creation of routing patterns on the top and bottom copper layers. You can use copper-plated through-holes to connect each side to wherever you want. It also allows electrical connections through the layers.
One advantage of double-sided flexible circuit boards is that it can be used for more complex electronic products with more functions. Manufacturers find it useful in manufacturing dashboard components, lighting, and other industrial fields.
3) Multi-layer flexible PCB:
Several layers of copper in a multi-layer flexible PCB board are connected together through plated through-holes, similar to the copper layers in a double-sided board. Multi-layer flexible PCBs contain multiple separate copper layers and dielectric layers.
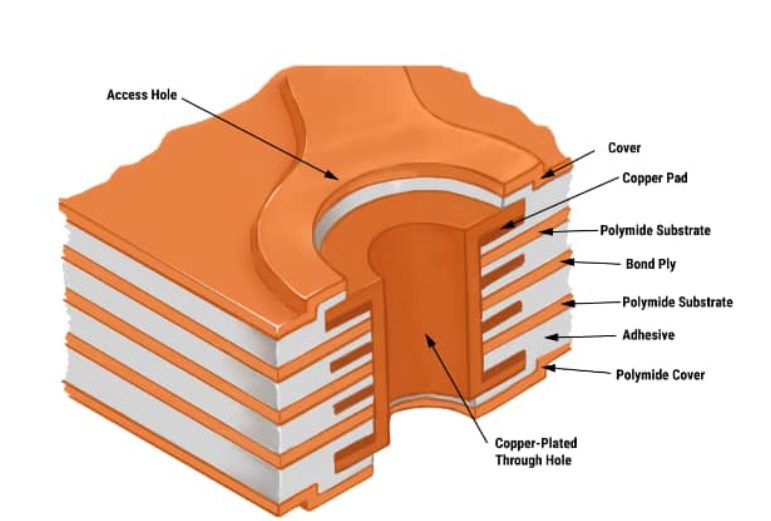
Schematic diagram of multi-layer flexible PCB
One of the benefits of using multi-layer flexible circuit boards is the high degree of design freedom and versatility. Manufacturers can use it for products with complex design requirements. It is used to manufacture components for mobile phones, satellites, cameras, and hearing aids.
Currently, the services of JLCPCB Manufacturing Division are capable of designing flexible PCBs up to 2 layers with high precision and quality control.
How many degrees can you bend a PCB?
The question of “How many degrees can a PCB be bent?” may seem easy to answer, but it is not so simple. Bending a PCB may damage the strength of the board, copper tracks, and pads. The maximum bending radius of a PCB depends on the design material and thickness of the PCB. 0.4mm is enough to bend a PCB 90 degrees. Some PCBs can be bent up to 20 times, but it is best not to bend the board more than once. The formula for the maximum bending angle of a PCB based on the thickness of the substrate is as follows:

For example, bending 90 degrees increases the possibility of damage to the circuit. Finally, make sure that the bending radius does not exceed one millimeter. With flexible materials, you can bend a PCB up to 180 degrees. However, if you try to bend beyond its recommended limit, you may end up damaging the board.
Structure of Flexible PCB:
Three types of flexible PCBs include: single-layer, double-layer, and multi-layer circuits. The main elements of a single-layer flexible PCB are:
1) Dielectric substrate film: It can be regarded as the substrate of the PCB. Its common material is polyimide (PI), which is characterized by high temperature resistance.
2) Electrical conductor: It includes the routing of the circuit. In the production of single-layer/multi-layer printed circuit boards, copper foil is used as the surface conductor layer.
3) Cover film: It is composed of organic film and adhesive. The function of the cover film is to protect the completed flexible circuit conductor part.
4) Adhesive material: An adhesive film with different adhesive types and thickness specifications. The adhesive film is used for interlayer bonding and insulation of multilayer boards.
The role of stiffeners in flexible PCB design:
The stiffener in a flexible printed circuit (FPC) is a rigid layer, usually made of materials such as polyimide or FR4, added to specific areas of the flexible PCB. It provides mechanical support and reinforcement to prevent bending or flexing in fragile areas such as connector areas or mounting points. Ribs improve durability, enhance reliability in high stress areas, and help maintain the overall form factor of the FPC in critical sections.
Ribs in Flexible Printed Circuits
Design Tips for Flexible Printed Circuit Boards:
- Keep in mind the maximum bend radius when using FPCs of varying thicknesses.
- Avoid discontinuities in areas where the substrate or coverlay bends.
- Teardrops can be added to make vias more stable and strong.
- Use ribs underneath the main electronic circuitry of the PCB.
Effects of Using Ribs
- Round the corners and make them slightly larger to avoid any corner tearing of the PCB.
Large rounded corners to avoid PCB tearing
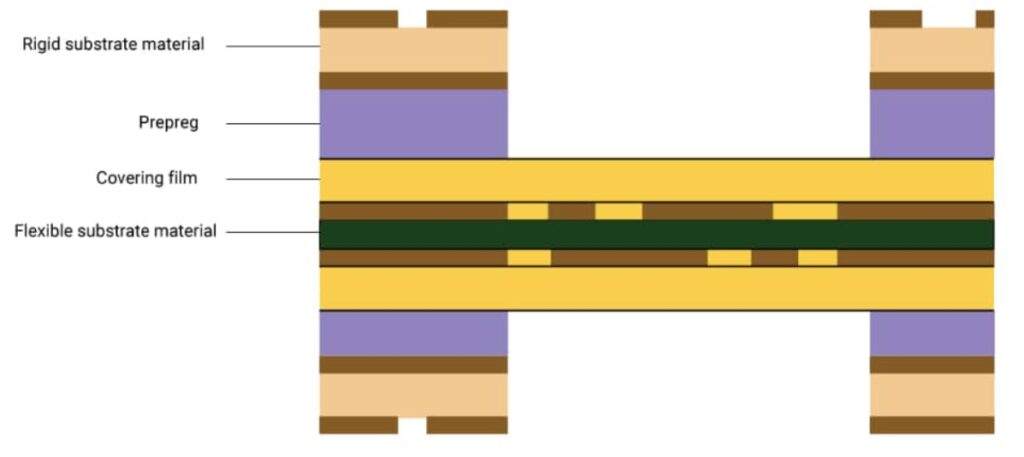
- Around the ribs, etched markings are allowed, while on the other hand, silkscreen markings are not allowed.
Advantages of Flexible PCBs:
Flexible circuit boards offer many advantages, which is why they are a popular choice among electronics manufacturers when it comes to PCBs. Here are some of the key advantages of using flexible circuits in electronic components:
Flexibility: This type of PCB can be easily bent and twisted. Hence, it can move and expand in 3D space, making it easier to integrate components with efficient line connections.
Lightweight: FPCs are less in size and weight compared to rigid PCBs, making them suitable for high reliability and high density products.
Durability: Flexible circuits can be bent up to 360 degrees. They can withstand the effects of vibration and shock, thus improving performance in any application.
Thermal stability: Since the substrate is thin and lightweight, it can easily dissipate heat. Flexible circuits can be exposed to high temperatures up to 400 ° C.
Signal integrity: It provides high mechanical resistance and resistance to high atmospheric factors, and has better EMI (electromagnetic immunity).
Disadvantages of Flexible PCBs:
Despite the many advantages of flexible circuit boards in modern electronics, there are still some issues to consider:
● The assembly process of this flexible PCB is complex.
● Any work and failure that occurs on the PCB board is difficult to repair.
● The probability of damage during handling is high.
● Flexible PCBs are slightly more expensive than traditional PCB designs.
● Flexible PCBs are sensitive to scratches.
● Sulfur-free plastics require proper storage conditions.
Applications of Flexible PCBs:
Flexible PCBs are used in various fields due to their versatility, reliability, and space-saving features:
Consumer Electronics: Flexible PCBs are used in compact, lightweight designs to efficiently connect components. Used in smart watches, fitness trackers, and other wearable technologies for flexibility and durability. Integrate into compact digital and analog mixed-signal units for high-performance connectivity.
Automotive Industry: Ensure efficient communication between automotive sensors and control units equipped with Advanced Driver Assistance Systems (ADAS). Provide reliable connectivity for in-car entertainment systems. Used in LED headlights and interior lighting for compact design and flexibility.
Medical and Healthcare Devices: FPC high-density connections help reduce the size of equipment such as MRI and CT scanners. Provide compact and reliable connections in small, complex designs, including hearing aids and other wearable monitoring devices, providing comfort and flexibility.
Industrial Applications: Provide flexibility and durability for robotic arms and machines with moving parts. Ensure efficient, compact connections in automation systems containing industrial sensors and control units for reliable performance.
Why not use flexible PCBs all the time?
Flexible PCBs offer advantages such as design flexibility and space saving, but they are not suitable for all applications due to their higher cost than traditional rigid PCBs. Flexible PCBs are also more complex to manufacture and can be easily damaged if not handled properly. Flexible PCBs may not be necessary for simple designs that do not require bending or folding, in which case rigid PCBs are a more economical and durable option. In addition, flexible circuits often have limitations in high-power handling and mechanical stability.
Conclusion
It is no wonder that flexible circuit boards have become a must-have material for manufacturing more powerful yet portable products in many industries. Other traditional options cannot compare to the flexibility and accuracy of flexible circuits. Aircraft, medical devices, automobiles, and even components used in daily life rely on flexible circuit boards to reduce weight without compromising functionality. With the advancement of technology and the continuous innovation of products, flexible PCBs will continue to be the first choice for manufacturing product circuit boards in various industries