Pros and Cons of Through-Hole PCB Assembly vs. SMT PCB Assembly
In recent years, electronic products have become increasingly complex and integrated into people’s daily lives. However, there are still two popular methods for soldering electronic components together to build circuits:
- Surface Mount Technology (SMT) for PCB Assembly
- Through-Hole (PTH) PCB Assembly
Both SMT PCB assembly and PTH assembly have unique advantages and disadvantages. Understanding these differences can help in selecting the best approach for specific projects. This article will explore the features, benefits, and limitations of each method.
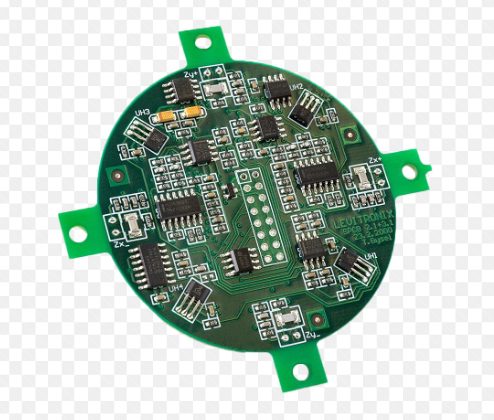
Understanding PCB Design and Components
A printed circuit board (PCB) consists of thin copper traces supported by layers of FR-4 fiberglass or similar materials. Copper traces connect various electronic components, such as capacitors, resistors, and microchips, to create circuits. In multi-layer PCBs, through-holes plated with copper allow connections between layers. These boards can range from simple single-layer designs to complex 20-layer configurations used in smartphones or motherboards.
Plated Through-Hole (PTH) Assembly
PTH Assembly involves inserting component leads into copper-plated holes on the PCB and soldering them in place. This method is especially suitable for hand soldering and prototyping but is less common in modern consumer electronics due to its bulkier components.
Key Features of PTH Assembly
- Power Generation: Ideal for applications requiring high heat or power.
- Durability: Withstands greater physical and thermal stress due to strong connections formed by soldering leads through holes.
- Revisions: Easier to remove and replace components during prototype revisions.
Advantages of PTH PCB Assembly
- Easy to assemble for basic circuits.
- Suitable for rugged and high-power applications.
- More resistant to heat and mechanical stress.
Disadvantages of PTH Assembly
- Higher costs due to additional drilling and manual assembly.
- Not suitable for compact designs or high-density PCBs.
- Declining popularity makes sourcing components more challenging.
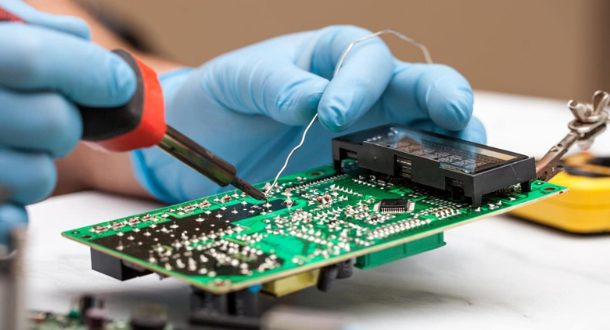
Surface Mount Technology (SMT) Assembly
SMT Assembly involves soldering components directly onto the PCB surface without the need for through-holes. SMT components are smaller, lighter, and better suited for high-density designs.
Key Features of SMT Assembly
- Compact and Lightweight: Ideal for miniaturized designs.
- Efficient Production: Automated processes reduce assembly time and costs.
- Complex Procedures: Requires precise equipment for accurate placement and soldering.
Advantages of SMT Assembly
- Lower production costs due to automation.
- Components can be mounted on both sides of the PCB.
- Widely used, with a large selection of available components.
Disadvantages of SMT PCB Assembly
- Hand assembly is challenging and requires specialized tools.
- Solder joints are more prone to cracking under stress.
- High initial setup costs for equipment.
Comparison: Through-Hole PCB Assembly vs.SMT PCB Assembly
Feature | PTH Assembly | SMT Assembly |
---|---|---|
Size | Larger components, bulkier designs | Smaller components, compact designs |
Durability | High resistance to stress | More prone to stress damage |
Cost | Higher due to manual processes | Lower for large-scale production |
Production Speed | Slower | Faster with automation |
Applications | Rugged, high-power circuits | Consumer electronics, small devices |
Rework/Prototyping | Easier to revise | More challenging to modify |
Frequently Asked Questions (FAQ)
What is SMT Repair?
SMT repair involves using specialized tools, such as conductive tips or hot air blowers, to remove and replace components on a PCB.
What is SMT Soldering?
SMT soldering is the process of soldering components directly onto the PCB surface, typically using a reflow oven.
Is SMT Cost-Effective?
Yes, SMT is cost-effective for mass production due to its smaller component size and faster assembly process.
SMD vs. SMT: What’s the Difference?
- SMD (Surface Mount Device): Refers to the electronic components mounted on a PCB.
- SMT (Surface Mount Technology): Refers to the method used to mount SMDs onto the PCB.
What is the Purpose of SMT Inspection?
SMT inspection checks the accuracy and quality of processes like solder paste printing, chip placement, and reflow soldering to ensure fault-free assembly.
Both PTH and SMT assembly methods have their own merits. For high-stress or high-power applications, PTH assembly remains a strong choice due to its durability and ease of modification. On the other hand, SMT is the preferred method for modern electronics, offering compact designs, cost-efficiency, and fast production.
Selecting the appropriate assembly method depends on the application requirements, production scale, and budget. Understanding these differences ensures that your PCB design meets the desired performance and cost objectives.