The Important Role of PCB Assembly in Aerospace Technology
Printed circuit boards (PCBs) are essential components in aerospace technology, playing a critical role in aircraft, satellites, and spacecraft. PCB assembly in aerospace requires high reliability, durability, and strict adherence to safety standards due to the extreme environmental and operating conditions encountered by aerospace systems.
Understanding PCB Assembly in Aerospace
PCB assembly is critical in the aerospace industry, requiring components that can withstand extreme conditions. Meeting stringent quality standards such as AS9100 is essential to ensure reliability and safety. Automated assembly processes such as surface mount technology (SMT) and through-hole technology (THT) ensure precision and consistency in manufacturing. Rigorous testing methods such as in-circuit testing (ICT) and automated optical inspection (AOI) guarantee the quality of assembled PCBs. Complying with regulations and maintaining a secure supply chain are important considerations to ensure the integrity of aerospace systems. Continuous improvement efforts drive innovation and reliability in aerospace PCB assembly processes.
Critical Steps in Aerospace PCB Assembly
Aerospace printed circuit board (PCB) assembly involves several critical steps to ensure the reliability and performance of electronic systems in aerospace applications. The following are the key stages involved in the assembly process:
Component Selection: Components that meet the stringent requirements of the aerospace environment are carefully selected first. Components must be able to withstand the extreme temperatures, vibrations, and radiation encountered during flight.
PCB Design: Aerospace PCBs are designed with special considerations for signal integrity, impedance control, and thermal management. Design engineers optimize the layer stackup and layout to minimize electromagnetic interference (EMI) and ensure reliability in harsh conditions.
Component Placement: Surface mount components are placed on the PCB using a placement machine. This step requires precision to ensure that the components are properly positioned and aligned according to the PCB design.
Through-hole component assembly: Through-hole components are inserted into pre-drilled holes on the PCB and then soldered manually or using an automated process. These components are mechanically strong and are typically used in high-power or ruggedized applications.
Inspection and Testing: Once assembled, the PCBs are thoroughly inspected and tested. Automated Optical Inspection (AOI) and X-ray Inspection are used to detect defects such as misalignment, solder bridges, or solder joint voids. In-circuit Testing (ICT) verifies the functionality of the assembled PCB.
Conformal Coating: Aerospace PCBs can be coated with a protective conformal coating to protect against moisture, chemicals, and environmental factors. This coating increases the durability and reliability of the PCB in an aerospace environment.
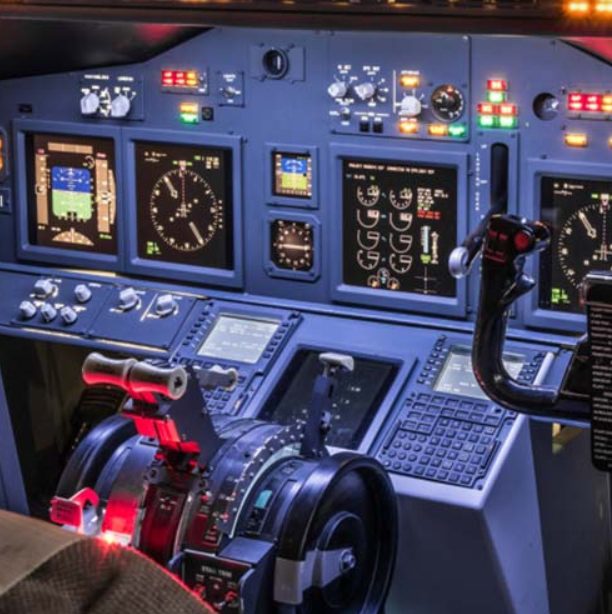
Key Applications of PCB Assembly in Aerospace
Systems: Facilitate communications between the aircraft and ground control centers as well as onboard communication systems. These systems support data transmission, voice communications, and navigation signals, which are essential for safe and efficient flight.
Avionics: Vital to navigation, guidance, and monitoring systems to ensure safe and efficient flight operations. Avionics PCBs integrate GPS, inertial navigation systems, radar systems, etc. to provide pilots with important information required for navigation and flight control.
Power Distribution Systems: PCBs are used to distribute power between various systems within the aircraft, ensuring consistent, reliable power is provided to critical components.
Flight Instruments: PCBs play a vital role in providing real-time data to pilots through flight instrument systems, assisting in navigation, altitude control, and aircraft system monitoring.
Weapon Systems: In military aerospace applications, PCBs are used for guidance, targeting, and control of weapon systems, ensuring accurate deployment of weapons during missions.
Challenges in Aerospace PCB Assembly
Extreme Conditions: Aerospace PCBs must withstand extreme temperatures, pressure changes, and mechanical stresses, including vibration and shock, during flight.
Size and Weight Constraints: PCBs must remain compact and lightweight while maintaining high performance to fit into space-constrained aircraft areas.
High Reliability Standards: Meeting stringent safety and reliability standards is critical to ensure trouble-free operation and prevent catastrophic failures.
Radiation Exposure: Aerospace PCBs are exposed to ionizing radiation at high altitudes and in space, requiring radiation-hardened components to ensure reliability.
EMI/RFI Shielding: PCBs require effective shielding to minimize electromagnetic interference and ensure reliable operation of critical systems.
Harsh Environmental Factors: Proper conformal coating is critical to protect PCBs from moisture, chemicals, and salt spray in aerospace environments.
Lifespan and Obsolescence: Managing component obsolescence is critical to ensure PCBs remain functional over the extended life of aerospace systems.
Overcoming Challenges in Aerospace PCB Assembly
Advanced Materials: High-temperature laminates and metal core PCBs withstand extreme conditions.
Surface Mount Technology (SMT): enables smaller components and denser layouts, optimizing space and weight.
Rigorous Testing and Quality Control: ensures PCBs meet stringent reliability and safety standards.
As we wrap up our exploration, it’s clear that PCB assembly is a cornerstone of aerospace innovation. From guiding navigation systems to facilitating communications, these tiny circuit boards play a critical role in pushing the boundaries of aerospace and space exploration. They enable us to achieve extraordinary feats, enable safe and efficient flight, and explore the unknown frontiers of the universe