The complete guide to automotive PCB assembly
In the automotive sector, electronics are increasingly becoming a decisive factor. This creates a dilemma for engineers. On one hand, their products must provide ever-improving performance, on the other hand, price per volume remains a key consideration.
Automotive PCBAs help replace diesel injection pump chips, which include immobilizers and ZDCAN. People should choose automotive PCBAs correctly because they can help them keep the stock control unit in place while making simple replacements.
What is the difference between PCB and PCBA?
These multi-layer interconnected printed circuit boards form the basis of PCBs and PCBAs. PCB refers to the design stage of a product, while PCBA refers to the assembled product.
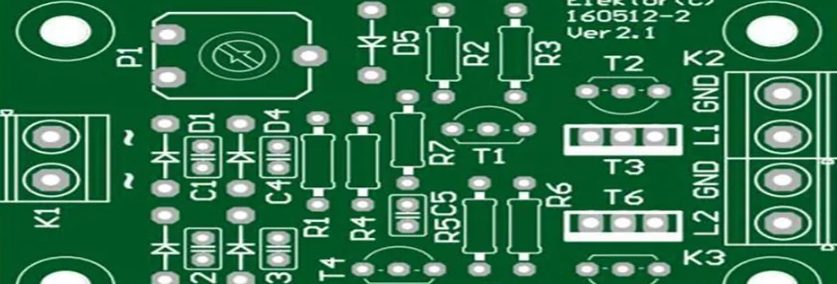
PCB: Printed Circuit Board
Printed Circuit Board
A printed circuit board (PCB) is a flat copper plate. It contains a pattern of conductive traces formed using various techniques (e.g., screen printing, electroplating) to form a circuit. These conductive traces route signals throughout the product and connect to other components. The purpose of the PCB determines whether it is single-sided or double-sided.
PCBA: Printed Circuit Board Assembly
Printed Circuit Board
Printed Circuit Board Assembly (PCBA) involves mounting components onto a PCB before assembly. The machine operator follows the engineer’s instructions to ensure that all components are securely connected and properly placed on the layers of the board. After quality control testing, the assembly is ready to be installed into the final product.
Types of Automotive PCBs
Automotive PCBAs come in several different types and sizes. The most common types include:
LED PCBs: These are used for automotive backlighting or other lighting applications. They are also used in front-end applications such as instrument clusters and displays.
Flexible PCBs: These are flexible boards that can bend at corners, making them ideal for front-end applications where space is limited.
Thick Copper PCBs: Thick copper PCBs have thicker copper layers than standard PCBs, so they run hotter and dissipate heat more efficiently. Thick copper PCBs are also made of materials that are more durable than traditional circuit boards, making them ideal for high-temperature applications such as engine control units (ECUs).
What does automotive PCBA mean?
An automotive PCBA is a printed circuit board assembly (PCBA) used in the automotive industry. The term PCBA refers to the fact that the circuit board is made of multiple layers of PCB material and uses solder or other conductive materials to create connections between these layers. This type of automotive PCBA is designed for vehicles and can be found in cars and trucks.
Application of PCB Assembly in Automotive Industry
Automotive PCBA assembly is a very important process. Engineers handle it with great care, especially in the automotive industry. The automotive electronics market is on the rise, and PCBs play an important role in this growth.
Here are some of the applications of automotive PCBA assembly in the automotive industry:
Airbag Control: Airbags are an integral part of the car safety system and can save lives in the event of an accident. The control unit of an airbag usually consists of a PCB that connects all the components, which makes it easier to install and test them before use.
Airbag Control
Anti-lock Braking System: Helps prevent skidding when braking, thereby improving vehicle stability and reducing fuel consumption. The system uses sensors to detect any skidding and then controls the brake pressure accordingly to prevent it from happening again.
Anti-lock Braking System
Climate Control: The main function of an electronic climate control system is to provide comfort to the driver and passengers by keeping the temperature inside the car constant. It also has other functions such as automatic defogger, seat heating, and ventilation control, all of which are controlled by buttons or knobs on the dashboard.
Man manually turns on the car’s air conditioning system
Digital Display: Most modern vehicles use digital displays to provide accurate information about vehicle speed, fuel level, and other parameters. The data is displayed on an LCD or LED screen using an IC (an integrated circuit containing multiple transistors and resistors). These ICs can be mounted on a PCB using surface mount technology (SMT).
Digital Display
What performance characteristics do automotive PCBs have?
In the automotive industry, automotive PCBAs are used in a variety of applications. Here is a list of performance characteristics of automotive PCBs:
Suitable for complex systems: Automotive circuit boards must be able to handle complex systems such as engine control computers, airbag controls, and steering wheels. It must also be able to handle high temperatures and vibrations.
Chemical Resistance: PCBs must be resistant to chemicals such as salt water, oil, and gasoline. It must withstand these chemicals without causing any damage or malfunction to the vehicle’s electrical system.
High Reliability: Automotive circuit boards have many components that make up their functionality, such as switches, relays, and sensors. These components must always work properly to avoid causing any problems with the performance or safety features of the car.
Dirt Resistance: Automotive circuit boards are susceptible to dust and dirt due to their proximity to other parts of the car’s interior, such as seats. Therefore, the component needs to withstand harsh environments and resist dust accumulation that would affect its functionality.
What are the manufacturing characteristics of automotive PCB assembly
Manufacturing characteristics of automotive PCBAs include:
High reliability: The automotive industry is highly regulated and has strict requirements, especially in the automotive electronics market. Automotive PCBs must withstand extreme temperatures, vibration, shock, and harsh chemicals.
High reliability
Low cost: To meet the stringent price requirements of the automotive market, manufacturers must reduce costs by using automation and reducing assembly time. Automated assembly also ensures consistent production quality and reduces defects that may lead to recalls.
Small size: Smaller parts are easier to fit into the tight spaces of the car, thereby reducing overall weight.
Small
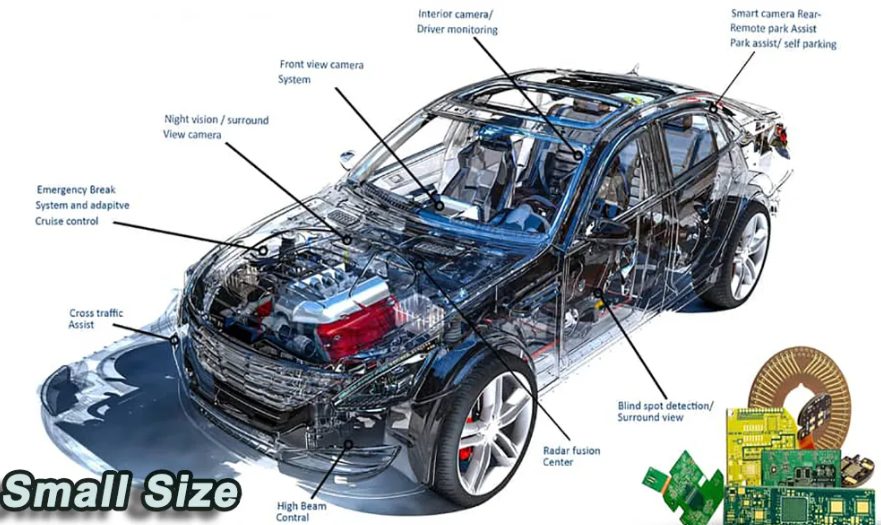
High performance: For safety reasons, the performance of automotive PCBs is critical – if the control unit fails at a critical moment, such as during emergency braking or sharp turns, it can lead to disaster. Therefore, automotive PCBs need to take into account high reliability and high performance characteristics from the beginning of the design process.
What are the processes for automotive PCB assembly?
Automotive PCBA assembly is a complex process involving multiple steps and components. The following article will give you an overview of the processes involved in automotive PCB assembly.
Solder Paste Stencil
Solder paste stencil printing is the first step in the assembly process. Once the stencil is ready, a dispenser applies solder paste to it. The stencil is then placed on top of each component on the automotive PCBA. Once all components are added to the board, they are placed in an oven at high temperature for several minutes until all bubbles between the components and the pads are eliminated.
Solder Paste Stencil
Pick and Place
Once the solder paste stencil is complete, a pick and place machine places all components on their respective pads. This step is done by placing a vacuum nozzle over each component and lowering it into place with a robotic arm. If a component does not fit properly or falls off during this stage, it is discarded and replaced with another correctly mounted component.
Reflow Soldering
Reflow soldering is used to solder components on a printed circuit board (PCB). Many types of components can be soldered using this method, including through-hole components, surface mount components, BGA packages, and more. Reflow soldering requires trained technicians to perform the process and ensure proper quality control.
Reflow Soldering
Inspection and Quality Control
Once all the necessary steps in the assembly process have been completed, it is time to inspect and verify the quality of each product. This requires testing each product to ensure that everything is functioning as expected. This can include testing electrical signals and physically inspecting each product before it leaves the factory for shipment.
Final Inspection and Functional Testing
Final inspection ensures that each product meets your specifications before it is shipped for use in a final product or device. This process includes functional testing and visual inspection to ensure that each product meets all functional and appearance requirements before it is shipped to its final destination.
PCB Functional Testing
How to choose automotive PCB substrate?
Substrate Materials
The most common substrate materials for automotive PCBA are FR4 and Rogers, which have good thermal stability, electrical properties, and mechanical strength. The advantages of FR4 are low cost, high thermal stability, good strength, and good flame retardancy, but the disadvantage is poor dielectric properties. Rogers has good dielectric properties, but the cost is higher than FR4 and the thermal stability is also poor.
Substrate Thickness
The thickness of the substrate can be determined based on the size of each component on the circuit board, ensuring that each component has enough space and does not affect each other’s performance. The thickness of the substrate should also meet the requirements of the product and processing, such as drilling and etching holes on the PCB during production.
Thickness tolerance
The thickness tolerance allows a deviation of 0.05mm~0.10mm, which is determined based on the experience of the production process and the requirements of different customer uses; this tolerance can be adjusted according to the actual needs of the customer when the customer purchases materials or when the factory directly purchases the produced PCB.
Cost
More expensive materials have more advantages than cheaper materials, but may not be required for all applications.
Mechanical properties
This includes strength, stiffness, and thermal expansion coefficient. These factors are important because they affect the performance of the PCB over time under various environmental conditions (such as temperature changes, humid environments, etc.).
What factors affect the quality of automotive PCBs?
The quality of automotive PCBA is the key to determining the overall performance of the car. In order to meet the needs of different markets, these PCBs must be made of high-quality materials and have the best performance.
What are the factors affecting the quality of automotive PCBs?
Many factors affect the quality of automotive PCBs. These include:
Materials used to make automotive PCBA
Types of circuit board technology used to make it
Environmental conditions for PCB manufacturing
Things to consider when designing automotive PCBs
Five factors to keep in mind when designing automotive PCBA boards
Power and ground planes
Track design
Pad and hole size
Signal integrity and RF issues
Thermal issues.
FAQs about automotive PCBA
What role does PCB assembly play in automobiles?
The role of PCB assembly in automobiles is crucial to the performance and reliability of the vehicle. PCBs are essential for operating various electronic modules such as engine management systems, airbags, power windows, etc. As automakers strive for higher safety standards and fuel efficiency, the demand for high-quality PCBs has also increased.
PCBA is crucial in automobiles
What are the effects of the environment on automotive PCBA?
Automotive PCBA is also affected by environmental factors to a certain extent.
The pressure of multiple loads on automotive PCBAs can easily cause circuit boards to crack, resulting in product failure and waste of resources.
Climate temperature can affect the quality of automotive PCBAs. When the temperature is high, solder joints and components may expand excessively, resulting in increased thermal stress on the circuit board and component terminals.
Climate Temperature
Moisture can also cause damage to electronic components. When moisture enters through the holes of electronic components, it can cause corrosion or oxidation, thereby reducing their reliability.
Vibration is another factor that affects the quality of automotive PCBA. Vibration during transportation or installation may affect the welding between terminals and connectors, causing short circuits, failure of operating control signals, etc.
The automotive PCBA market is growing. This can be attributed to the growing demand for automotive technology around the world, especially the adoption of automobiles in developing countries due to their comparative advantages over other means of transportation in some cases.