SMT vs Thru-Hole Manufacturing
At the heart of nearly every electronic product today is a printed circuit board (PCB), which supports and electrically connects the electronic components needed for an electronic device to function.
Manufacturing a printed circuit board is a complex process that involves many steps that are different for every project. First, you need to design the board according to your project requirements. Then, you need to manufacture the PCB according to the design, which involves a complex process of depositing copper onto the board and combining its various layers together.
Once you have your PCB made, your job is far from done. You still need to assemble the board by attaching the electronic components to it. Once you are done, you have a complete printed circuit board assembly, or PCBA. Sometimes, this assembled board is simply called a PCB. There are two main methods for assembling circuit boards – surface mount technology and through-hole technology.
Overview of the PCB Assembly Process
Once the PCB assembler has the bare board and the design, they need to complete several steps to prepare for the actual assembly, which is the process by which they mount the components onto the bare board. The design that the customer provides to the assembler will tell the assembly professional where to place the components and which method (through-hole or surface mount) to use to place the components. They can also use the design instructions and other information about specific requirements to guide themselves through the assembly process.
Before assembly begins, many assemblers will review the design files for potential issues that could affect the manufacturability and functionality of the PCB. This process is called a design for manufacturability check, or DFM. During this check, the assembler will look for missing or redundant features, component spacing issues, and other problems. It is critical to perform this check before assembly begins because the earlier problems are discovered, the less they will increase the cost and time required to complete the project. It can also prevent potential failures in the final product.
Once these checks are completed, the actual assembly process can begin. The specifics of this process depend on whether surface mount technology or through-hole technology is being used. In the following sections, we will look at the steps for both assembly methods in more detail. Assembly may involve only one of these methods, or a combination of both.
Once assembly is complete, the PCBA will undergo additional inspections. These quality control checks are designed to find any errors or problems in the PCBA. The thoroughness of the testing depends on the customer’s requirements for completion time, project details, and other factors. At EMSG, we visually inspect all of the PCBAs we produce under a magnifying glass. We can also perform optical inspections on PCBAs using automated optical inspection (AOI) equipment, which can detect both component-level and lead-level defects. Assemblers can also provide in-circuit testing to check the functionality of components.
These types of quality control inspections are important because faulty parts after assembly can lead to increased expenses and reduced time to market. They can also result in financial losses, damaged reputations, and even safety hazards if defects make it into the final product. Quality control inspections can prevent many of these undesirable outcomes.
After the inspection phase, PCBAs typically go through a series of cleaning processes to remove dirt, oil, and residual flux residue. Assembly companies may use deionized water applied by a high-pressure cleaning tool. Deionized water is used because the ions in the water can damage electronic circuits.
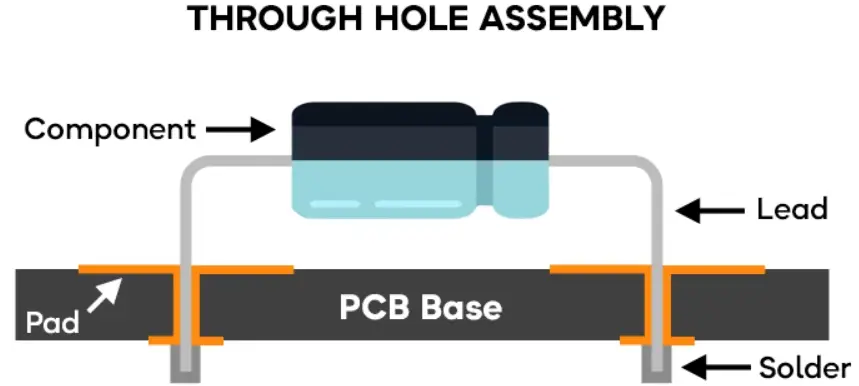
What is Through-Hole Technology and Through-Hole Mounting Process?
One of the two most common methods of attaching electronic components to PCBs is the through-hole or through-hole process. This technology is older than SMT, and for many years, it was the standard technology for PCB assembly. When surface mount technology became popular in the 1980s, many people thought it would make through-hole PCB assembly obsolete. However, through-hole technology has several advantages that make it still a preferred choice for certain applications.
The through-hole manufacturing process, as the name implies, involves drilling holes in a PCB. The board manufacturer drills holes where the components will be located based on the customer’s design. Once the holes are drilled, the leads are threaded through these holes. It is critical that the leads are placed consistently and correctly in the holes. Assemblers need to ensure that they have the correct polarity and orientation when they are manufacturing through-hole boards.
Next, the assembler must inspect the components and make any necessary adjustments.
Finally, the assembler will solder the leads securely in place, possibly using wave soldering, where the PCB is slowly passed through liquid solder at high temperatures.
Originally, workers performed all of these steps manually. Today, automated insertion mounters and other equipment can assist with many parts of the process. There are two main types of through-hole components – axial leaded and radial leaded. Axial leaded components have leads on both ends. They extend out of the component in a straight line. Radial leaded components have leads on both sides. The leads run through the entire board, so they can connect the various layers of the PCB.
What is SMT technology and surface mount process?
Originally called flat mount, surface mount technology became popular in the 1980s and is used today for most electronic components. As the name implies, surface mount components are mounted on the surface of the PCB, rather than inserted into holes on the board as in through-hole assembly. During surface mount assembly, assemblers solder components to pads on the board.
Initially, most surface mount processes were done manually, but today, the process is highly automated thanks to modern technology. In the first step of the SMT technology process, assemblers apply solder paste to the portion of the board where the components will be mounted. A template, called a stencil or solder mesh, helps ensure that the solder paste is applied to the correct location.
After solder paste printing is completed, the board is usually inspected to check for defects in the solder paste. If the inspection reveals any problems, the assembler will rework it or remove the solder paste and apply it again. These steps are important because the quality of the solder paste printing is correlated to the quality of soldering later in the assembly process.
Next, during the SMT technology process, assembly professionals will place the components on the board according to the customer’s design. Initially, workers did this manually with tweezers. Today, the process is largely automated and uses advanced pick-and-place machines. Components are then soldered to pads on the board to hold them in place. This stage is usually done with reflow soldering, where the board is fed into an oven and the high temperatures liquefy the solder paste.
Since surface mount components do not use holes to connect different layers of the board, they require a different method to achieve this. That method is the use of vias, which are small holes that connect different layers of the board. However, unlike through-hole technology, these holes do not have leads directly connected to them. There are several different types of vias, including through-hole, blind and buried vias.
Through-hole Mounting Advantages
Surface mount technology has some advantages over through-hole technology, such as cost, which has contributed to its growing popularity. However, through-hole mounted components have some unique characteristics that help them remain the technology of choice for certain industries and applications.
The most commonly cited advantage of through-hole mounting processes is that through-hole mounted components have higher reliability. Since the leads are not only soldered in place, but also pass through the board, the bond is stronger. As a result, products using them are more resistant to environmental stresses such as shock and impact.
Some types of components are not yet available in surface mount versions, so through-hole must be used in some cases.
Disadvantages of Through-Hole Mounting
There are also some disadvantages to using the through-hole process. Through-hole components are larger than surface mount devices and take up more space, which can increase costs because the board needs to be larger. This difference makes through-hole technology unsuitable for high-density boards.
Advantages of Surface Mount Technology
Using surface mount technology is generally more cost-effective than using through-hole technology, which is the main reason why this technology is so popular in today’s electronics manufacturing industry. As more surface mount devices are developed, the technology can be used for more types of products.
Part of the reason that the surface mount process can reduce costs is that surface mount devices are smaller and take up less space than through-hole components. A big advantage of surface mount technology is that the method can reduce the size of boards assembled using through-hole technology by one-third and the weight by one-tenth.
Another advantage of surface mount technology is that it allows for a higher connection density, which means they can have more electrical connections than other types of PCBs. You can also mount components directly on both sides of the board, making the most of the board space.
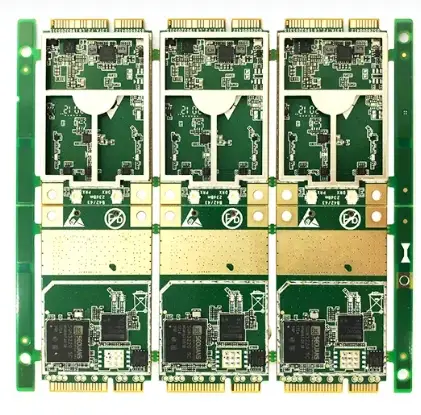
In addition, surface mount PCBs are generally faster and easier to assemble than through-hole PCBs. One of the biggest advantages of SMT is that more of the process can be automated, further reducing costs.
Disadvantages of SMT
Components mounted on the surface of a PCB are not as securely attached as leads that run through the entire board. Therefore, one of the disadvantages of SMT is that components are not suitable for boards exposed to high environmental stress or conditions where reliability is particularly important.
Applications of Through-Hole Technology
Through-hole technology is well suited for products that require high reliability even under high environmental and mechanical stresses, as well as high voltage, power, and temperature conditions. Large units are also more likely to use through-hole technology, as reducing costs through smaller components is not a problem. In addition, through-hole technology is very useful for testing and prototyping, as you can manually adjust and replace leads with relative ease, allowing you to try out various layouts.
Transformers, semiconductors, electrolytic capacitors, and plug connectors may all use through-hole technology. The military, aerospace, and industrial equipment sectors often use this technology because it is reliable and resistant to harsh conditions. Light-emitting diodes (or LED lights) used in outdoor applications, such as billboards and displays in sports stadiums, may also use through-hole technology because it can withstand outdoor conditions.
Applications of Surface Mount Technology
Today, most electronic hardware uses surface mount technology. The process has become dominant in the electronics field because it is increasingly cost-effective compared to through-hole technology. The trend of making smaller electronic devices has also made surface mount components more common.
Smartphones, tablets, laptops, Internet of Things (IoT) devices, and other electronic products are often made using the surface mount process. It can be used to manufacture telecommunications and communication equipment, medical equipment, transportation components, lighting, industrial and commercial hardware, etc.