SMT Soldering Process and Assembly Technology
SMT soldering process and technology are slightly different from through-hole technology.
SMD soldering or surface mount technology assembly requires different SMT equipment and more experience and expertise. SMT PCBs have flat tin-lead or gold-plated copper pads without any holes. These traces are called “pads”.
SMT Soldering Process
Semi-solid solder called solder paste, which consists of very fine solder and flux, is dispensed on the pads. 2.Solder paste can be dispensed using stencils and screen printing processes, using SMT screen printers.
After the paste is dispensed, the board is moved to the conveyor belt of the placement machine. The placement machine picks up the SMD components and places them on the PCB.
3.After all the electronic components are placed on the SMT circuit board, the board is conveyed to the reflow oven. The SMT reflow oven has different chambers. The first chamber or zone is called the preheating zone, where the temperature of the circuit board and all components is gradually and evenly increased to prevent the PCB from cracking due to thermal shock.
- The next area is the high temperature zone, where the temperature is high enough to melt the solder paste to solder the component leads to the pads on the circuit board. The surface tension of the molten solder keeps the component in place. The surface tension also automatically aligns the component to the pad.
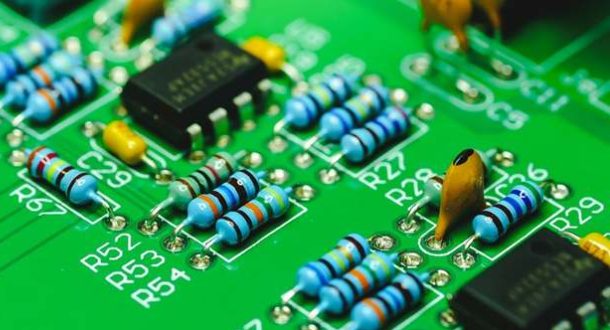
SMT Soldering Techniques
Reflow soldering can be performed using different techniques:
Infrared reflow;
Hot air convection;
Vapor phase reflow
After the SMT Soldering Process
After the soldering process, the PCA or PCB assembly (PCBA) needs to be cleaned to remove flux residue and any stray solder balls that could short closely spaced component leads. This can be done using an SMT solvent cleaning machine. Rosin flux can be cleaned with fluorocarbon solvents, high flash point hydrocarbon solvents, or low flash point hydrocarbon solvents. Water soluble flux is removed with deionized water and detergent, followed by an air stream to quickly remove any residual water. No-clean flux does not require any cleaning.
Inspection
Finally, the printed circuit assembly is visually inspected for any missing or misplaced components or solder bridging. This can be done using an SMT inspection machine. If any faults are found during the inspection, the board is sent for rework. Finally the board is sent for testing to verify whether it is working properly.
KKPCB has a state-of-the-art SMT assembly line to ensure the reliability of the circuit boards.
Production-ready components for high turnaround.
Assemble the following types of single-sided and double-sided SMT PCBs:
Ball Grid Array (BGA)
Ultra Fine Ball Grid Array (uBGA)
Quad Flat No-Lead Package (QFN)
Quad Flat Package (QFP)
Small Outline Integrated Circuit (SOIC)
Plastic Leaded Chip Carrier (PLCC)
Package on Package (PoP)
Small Chip Package (0.2mm pitch)
Our stringent testing protocols for surface mount assembly include:
Automated Optical Inspection
X-ray Test
In-Circuit Test
Functional Test
Thus, we ensure a high level of accuracy even with high-density surface mount (SMT) PCB assembly.