Rigid-Flex PCB Cost Optimization: Design and Manufacturing Considerations
As the demand for flexible and rigid-flex PCBs continues to grow, understanding the factors that influence their cost is crucial for optimizing designs and ensuring cost-effective production. Rigid-flex PCBs offer significant advantages, such as enhanced flexibility, reliability, and space-saving capabilities, but they also come with unique challenges that can drive up costs if not properly managed. This article explores key design considerations, cost factors, and strategies for optimizing rigid-flex PCB designs.
Rigid-Flex PCB Cost Factors
The cost of rigid-flex PCBs is influenced by several factors, many of which are tied to design decisions. By addressing these factors early in the design process, engineers can minimize costs while maintaining performance and reliability.
1. Component Selection
- Additional Components: Rigid-flex PCBs often require extra components like stiffeners, bolts, or adhesives to ensure structural integrity during assembly and operation. These additions can increase material and assembly costs.
- Component Type: Surface-mount devices (SMDs) are preferred for rigid sections, as they are easier to assemble and reduce the risk of damage during flexing.
2. Component Placement
- Restricted Layout Options: Components should be placed on rigid sections whenever possible to avoid stress on flex areas. This may limit layout flexibility and increase design complexity.
- Avoiding Flex Areas: Placing components on flex areas can lead to mechanical stress and failure, necessitating redesigns and increasing costs.
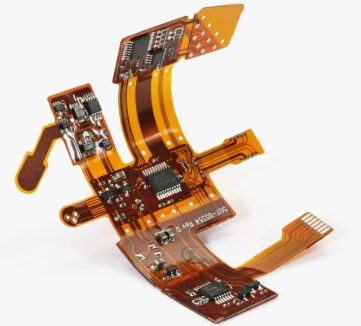
3. Material Selection
- Flexible Materials: Materials must be chosen to withstand bending and thermal stresses during manufacturing and operation. High-performance materials like polyimide are often used but can be more expensive.
- Thermal and Mechanical Properties: Materials must meet thermal and mechanical requirements, such as high glass transition temperature (Tg) and low coefficient of thermal expansion (CTE).
4. Trace Routing
- Wider Traces and Spacing: On flex sections, wider traces and increased spacing help reduce the risk of cracking and improve durability. However, this may require more space and increase layer count.
- Signal Integrity: Balancing trace width and spacing with signal integrity requirements is critical to avoid performance issues.
5. Stacking Configuration
- Layer Count: Minimizing the number of layers reduces complexity and cost. However, this must be balanced against the need for sufficient routing space and signal integrity.
- Flex Layer Placement: Proper placement of flex layers within the stack-up is essential to achieve the desired flexibility and durability.
6. Manufacturability
- Lamination Cycles: Reducing the number of lamination cycles lowers manufacturing costs and minimizes the risk of delamination or other defects.
- Thermal Management: Minimizing exposure to high temperatures during manufacturing helps maintain material integrity and reduces costs.
7. Standards Compliance
- IPC Standards: Adhering to standards like IPC 6013 (Qualification and Performance Specification for Flex/Rigid-Flex PCBs) and IPC 2223 (Design Standard for Flex/Rigid-Flex PCBs) ensures reliability but may require additional testing and validation.
8. Operational Reliability
- Thermal and Mechanical Stress: Designs must account for long-term exposure to thermal and mechanical stresses to avoid failures during the product lifecycle.
- Assembly Processes: Selecting components and processes that minimize the need for multiple soldering cycles can improve reliability and reduce costs.
Advantages and Challenges of Rigid-Flex PCBs
Advantages
- Flexibility: Enables unique form factors and installation options.
- Space Savings: Reduces the need for connectors and interconnects, leading to smaller package sizes.
- Durability: Withstands vibration, shock, and repeated bending better than rigid PCBs.
- Reliability: Fewer connectors mean fewer potential failure points.
Challenges
- Complexity: More complex designs require advanced expertise and tools.
- Cost: Higher material and manufacturing costs compared to rigid PCBs.
- Manufacturing Equipment: Specialized equipment is often required, adding to production costs.
- Structural Integrity: Maintaining integrity over the product lifecycle can be challenging.
Effective Flex Design Considerations
To optimize rigid-flex PCB designs and control costs, follow these guidelines:
- Choose Lightweight Components: Reduce mechanical stress on flex areas.
- Use Through-Hole Components Sparingly: Prefer SMDs for rigid sections to simplify assembly.
- Select High-Tg Materials: Ensure materials can withstand thermal stresses.
- Follow DFM/DFA Rules: Collaborate with your contract manufacturer (CM) to ensure designs are optimized for manufacturing and assembly.
- Use Supports and Stiffeners: Ensure reliable connections and operation without over-engineering.
- Leverage Advanced Design Tools: Use PCB design software with rigid-flex capabilities to streamline the design process and avoid costly errors.
By addressing these design considerations and cost factors, engineers can leverage the benefits of rigid-flex PCBs while keeping costs under control. Collaboration with experienced manufacturers and the use of advanced design tools are key to achieving optimal results.
KKPCB conducts research on special processing technologies such as ordinary double-sided boards, thick copper circuit boards, high-frequency circuit boards, HDI circuit boards, rigid-flexible circuit boards, FPC flexible boards, buried blind hole circuit boards, and IC carrier boards. Provides PCB design, PCB layout, PCB prototyping and PCB assembly services.