Rigid-Flex PCB Cost Optimization: Key Considerations and Strategies
As the demand for more compact, reliable, and flexible electronic devices grows, rigid-flex PCBs are becoming increasingly popular. These boards combine the best of both rigid and flexible circuits, offering unique advantages such as enhanced durability, reduced package size, and fewer connectors. However, the cost of designing and manufacturing rigid-flex PCBs can be significantly higher than traditional rigid boards. To optimize costs while maintaining quality, it is essential to understand the key factors that influence rigid-flex PCB cost and implement effective design strategies.
Key Factors Affecting Rigid-Flex PCB Costs
1. Design Considerations
- Component Selection: Rigid-flex PCBs often require additional components like stiffeners or bolts to aid assembly and restrict movement. These add-ons can increase material and assembly costs.
- Component Placement: Placing components on rigid surfaces is recommended, as flexible areas are prone to stress and damage. This may limit layout options and increase design complexity.
- Material Selection: The materials used must comply with bend radius requirements and withstand thermal stresses during manufacturing. High-performance materials like polyimide are often more expensive.
- Trace Routing: Maximizing trace width and spacing on flex areas is crucial to prevent signal integrity issues, but this can increase the board size and cost.
- Stacking Configuration: Minimizing the number of layers reduces complexity and cost, but it must balance the required flexibility and functionality.
2. Manufacturability
- Lamination and Thermal Cycles: Excessive lamination and thermal cycles during manufacturing can drive up costs. Reducing the number of layers and simplifying the stack-up can help.
- Assembly Complexity: Rigid-flex PCBs often require specialized assembly processes, such as sequential lamination or selective soldering, which can increase production costs.
3. Standards Compliance
- IPC Standards: Adhering to standards like IPC 6013 (Qualification and Performance Specification for Flex/Rigid-Flex PCBs) and IPC 2223 (Cross-sectional Design Standard) ensures reliability but may add to the cost due to stricter manufacturing requirements.
4. Operational Reliability
- Thermal Exposure: Prolonged exposure to high temperatures during manufacturing can affect long-term reliability. Minimizing thermal cycles and selecting components that do not require multiple soldering stages can reduce costs and improve durability.
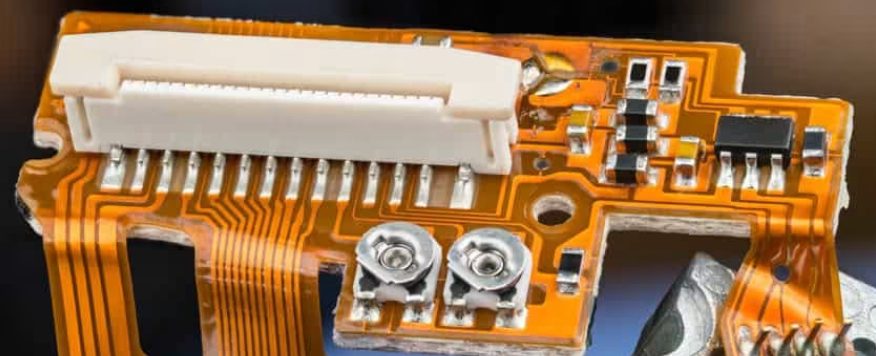
Advantages and Challenges of Rigid-Flex PCBs
Advantages
- Flexibility: Enables unique mounting possibilities and reduces the need for connectors.
- Leaner Installation: Simplifies assembly and reduces the overall package size.
- Durability: Withstands mechanical stress and vibrations better than rigid boards.
- Fewer Failure Points: Eliminates connectors, reducing potential failure points.
Challenges
- Higher Complexity: Designing and manufacturing rigid-flex PCBs requires specialized expertise and equipment.
- Additional Components: Stiffeners, bolts, and other supports add to the cost.
- Expensive Materials and Equipment: High-performance materials and specialized manufacturing tools increase production costs.
- Structural Integrity: Ensuring the board maintains its integrity over its lifecycle is critical but challenging.
Strategies for Rigid-Flex PCB Cost Optimization
To balance the benefits of rigid-flex PCBs with cost considerations, follow these design and manufacturing strategies:
1. Effective Design Considerations
- Choose Lightweight Components: Reduce the overall weight and stress on flexible areas.
- Use Through-Hole Components When Possible: These are often more cost-effective and reliable for rigid sections.
- Select High-Tg Materials: Materials with high glass transition temperatures (Tg) offer better thermal stability and durability.
- Follow DFM and DFA Rules: Collaborate with your contract manufacturer (CM) to ensure the design is optimized for manufacturability and assembly.
2. Optimize Stack-Up and Layer Count
- Minimize the number of layers to reduce complexity and cost.
- Use symmetrical stack-ups to improve manufacturability and reliability.
3. Simplify Trace Routing
- Maximize trace width and spacing on flex areas to reduce the risk of damage and signal integrity issues.
- Avoid sharp bends and use curved traces to distribute stress evenly.
4. Leverage Advanced Design Tools
- Use PCB design software with rigid-flex capabilities to streamline the design process and ensure compliance with industry standards.
- Simulate thermal and mechanical stress to identify potential issues early in the design phase.
5. Collaborate with Experienced Manufacturers
- Work with manufacturers who specialize in rigid-flex PCBs to ensure high-quality production and cost-effective solutions.
- Discuss design constraints and cost-saving opportunities during the prototyping phase.
Rigid-flex PCBs offer significant advantages in terms of flexibility, durability, and space savings, making them ideal for innovative electronic products. However, their higher costs can be a barrier if not managed effectively. By understanding the key cost factors, addressing design challenges, and implementing cost optimization strategies, engineers can leverage the benefits of rigid-flex PCBs while keeping costs under control. Partnering with experienced manufacturers and using advanced design tools are critical steps in achieving this balance.
By focusing on rigid-flex PCB cost optimization, you can create high-performance, reliable, and cost-effective solutions that meet the demands of modern electronics.
KKPCB conducts research on special processing technologies such as ordinary double-sided boards, thick copper circuit boards, high-frequency circuit boards, HDI circuit boards, rigid-flexible circuit boards, FPC flexible boards, buried blind hole circuit boards, and IC carrier boards. Provides PCB design, PCB layout, PCB prototyping and PCB assembly services.