Relationship Between Current and Line Width in PCB Design
PCB design is a delicate balance of electrical and thermal considerations, with the relationship between current and line width being a cornerstone of reliable circuit functionality. While many empirical formulas, tables, and software tools exist online to guide this aspect of design, this article consolidates the most useful references to assist engineers in optimizing PCB layouts.
1. PCB Current Carrying Capacity and Line Width
The current-carrying capacity of a PCB trace depends on trace width, copper thickness, and the allowable temperature rise. While experienced engineers can estimate this relationship intuitively, newcomers often face challenges.
Key Considerations:
- Wider traces carry more current.
- Increasing copper thickness (e.g., 1 OZ to 2 OZ) enhances current capacity.
- Temperature rise is critical: exceeding limits affects reliability and performance.
Data Reference from MIL-STD-275
The MIL-STD-275 standard provides a guideline for current-carrying capacity based on trace width and thickness. For example:
- A 10MIL trace can carry approximately 1A.
- Wider traces do not scale linearly (e.g., a 50MIL trace does not carry 5A).
2. Relationship Between Copper Foil Thickness, Trace Width, and Current
In PCB design, copper thickness is often measured in ounces (OZ), where:
- 1 OZ corresponds to a thickness of 35µm.
- 2 OZ equals 70µm.
Empirical Formula for Current Carrying Capacity
You can use the following formula for approximation:I=0.15×Line Width (W)(in MILs)I = 0.15 \times \text{Line Width (W)} \quad \text{(in MILs)} I=0.15×Line Width (W)(in MILs)
Where III is the current in amperes.
For example, a 10MIL width trace with 1 OZ copper at room temperature can handle approximately 1A.
Key Notes:
- Derate the table values by 50% for higher reliability when designing high-current paths.
- Adding a solder layer can significantly increase current capacity, especially in high-current single-sided boards.
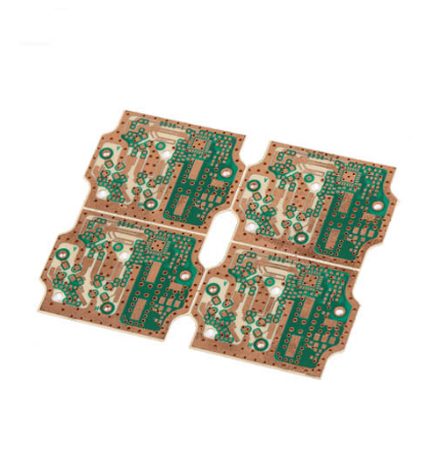
3. Practical PCB Design Considerations for Current and Line Width
A. Factors Affecting Current Capacity
- Environment: Temperature fluctuations can impact performance.
- Pads and Vias: Pads and vias along a trace may bottleneck current flow.
- Tinning: Applying a solder layer enhances current handling.
B. High-Current Design Adjustments
- Solder Layer Addition: Adding a layer of solder increases the effective width and reduces resistance. For example, a 1mm trace with a solder layer may behave like a 2mm trace.
- Heat Dissipation: Use appropriate copper pouring and via designs to dissipate heat effectively.
4. PCB Design Tools and Software
Modern tools like PCBTEMP allow precise calculations for current, line width, impedance, and temperature rise. By inputting parameters like trace location (external or internal), copper thickness, and desired temperature, engineers can determine the optimal line width for a given current.
5. Empirical Formulas and Examples
One widely used empirical formula is:I=K⋅T0.44⋅A0.75I = K \cdot T^{0.44} \cdot A^{0.75} I=K⋅T0.44⋅A0.75
Where:
- K=0.024K = 0.024K=0.024 (inner layer) or 0.0480.0480.048 (outer layer)
- TTT: Maximum temperature rise (°C°C°C)
- AAA: Cross-sectional area of copper trace (in square MILs)
- III: Current capacity (amperes)
6. Practical Challenges and Solutions in PCB Design
A. Thin Traces and High Current
Thin traces can burn under high current due to energy overload. Use wider traces or consider thicker copper (e.g., 2 OZ or 3 OZ) for power-intensive sections.
B. Pad and Via Connection
Different connection methods (e.g., straight laying, right-angle spokes, 45-degree spokes) affect current capacity and heat dissipation:
- Straight Laying: Maximizes current capacity but dissipates heat quickly, making soldering harder.
- Right-Angle or 45-Degree Spokes: Reduces heat dissipation, simplifying soldering but lowering current capacity.
7. Case Study: Motor Driver Design Challenge
A motor driver circuit with an H-bridge device frequently burned out due to improper trace design. Investigation revealed the issue:
- The power pad used right-angle spokes with only two connections, drastically reducing current capacity.
- Instantaneous current spikes (~100A) during H-bridge operation burned the traces.
Solution:
Switching to straight copper plating significantly increased the current capacity of the trace, resolving the issue.
8. Key Recommendations for PCB Design
- Use Empirical Data: Follow reliable current-line width tables and formulas.
- Leverage Software Tools: Simulate current and temperature profiles for critical traces.
- Consider Manufacturing Processes: Ensure design choices align with manufacturing capabilities (e.g., solderability).
- Optimize Pad Design: For high-power circuits, use straight connections to maximize current handling.
By understanding the relationship between current and line width, engineers can create robust PCB designs that perform reliably under varying conditions. Always prioritize testing and simulation to validate assumptions in high-current designs.