Pressure Sensor PCBA Solution Case Study for Industrial Control Equipment
1.Background Overview
A client from Europe, engaged in the development of industrial automation systems, required integration of a high-precision pressure sensor module in their next-generation process control system. The module needed to detect subtle changes in gas or liquid pressure in real time to enable dynamic control and safety alerts.
Given the complex environment in which the equipment would operate, the client emphasized strict standards for PCB heat resistance, soldering reliability, and circuit stability.
KKPCB was selected as the PCBA manufacturing partner for this project due to our rich experience in industrial control applications and our proven ability to deliver high-reliability solutions.
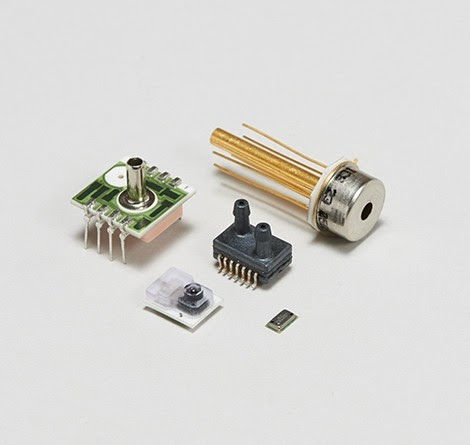
2. Application Scenarios
The pressure sensor PCBA module is widely used in various types of industrial control equipment, including:
- Pressure monitoring and feedback in air compressor systems
- Smart detection of pipe pressure in fluid transfer systems
- Pressure control loops in factory automation processes
- Safety monitoring modules for industrial gas processing equipment
By capturing environmental pressure changes in real time, the module transmits accurate signals to the host system to enable threshold alerts, logic interlocking, and system feedback.
3. Product Specifications (PCBA Overview)
Item | Specification |
---|---|
PCB Layers | 4 layers |
Base Material | High Tg FR4 (TG170) |
Board Thickness | 1.6mm |
Surface Finish | Lead-free HASL (RoHS compliant) |
Pressure Sensor Type | Micro pressure type, with built-in amp & temp. compensation |
Total Accuracy | ±2.5% FS (micro-pressure type) |
Rated Pressure Range | 6 kPa (customizable) |
Operating Voltage | 5V DC constant voltage |
Output Signal | Analog voltage (MCU ADC compatible) |
Sensor Package Size | 10.4 mm × 10.4 mm (P-type package) |
EMC Protection | Integrated power filtering and ESD protection |
Operating Temp Range | 0°C ~ +85°C |
4. Application Results
KKPCB’s pressure sensor PCBA passed full-cycle performance testing and EMC certification in the client’s control system. Test results showed significant improvements in signal stability and electromagnetic interference resistance, reaching industrial-grade EMC standards. The system maintained reliable linear response even after 3,000+ hours of continuous operation.
During mass production, KKPCB delivered multiple batches on schedule with a pass rate of 99.95%, greatly shortening the client’s integration and debugging cycle and accelerating the product’s time to market. The client expressed high satisfaction with both product quality and service responsiveness.
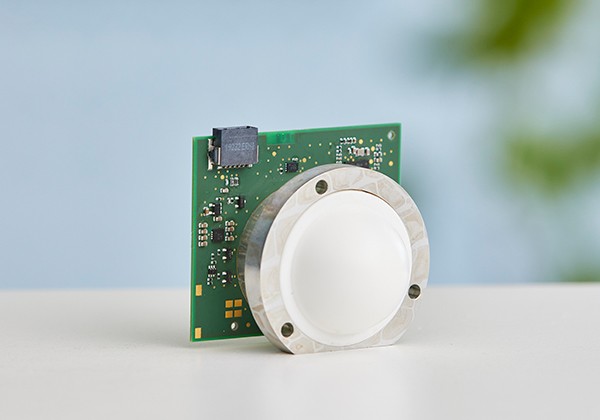
5. KKPCB’s Advantages in This Project
KKPCB stood out as a trusted manufacturing partner thanks to several core strengths:
- Industrial-Grade Quality: Strict compliance with IPC-A-610 Class 2 standards ensures high reliability under harsh environments.
- High-Precision Assembly: Capable of mounting ultra-small components (01005, QFN) for compact and optimized layouts.
- Comprehensive Process Compatibility: Supports various surface finishes (ENIG, HASL, OSP, etc.) to meet specific anti-corrosion and soldering needs.
- Rapid NPI Capability: Sample production within 5 days and a fast-response system to support project iteration.
- Mass Production Experience: Monthly output of over 50,000 high-density, multi-layer PCBs ensures reliable mass delivery.
6. KKPCB’s Custom Manufacturing-Focused Solution
Based on the product and installation requirements, KKPCB offered a tailored solution from the manufacturing perspective, including:
- Customized PCB Material Selection: High Tg FR4 boards improved thermal stability and warping resistance in high-temperature conditions.
- Optimized Layout & Stackup: Efficient use of space to integrate sensor circuitry, power supply, filtering, and signal interface while preserving signal integrity.
- Enhanced EMC & Filtering Design: Added power line filtering and ESD protection to support high-voltage environments.
- High Assembly Precision: Automated Optical Inspection (AOI), X-ray solder joint inspection, and functional testing ensure consistency and completeness.
- Full Traceability System: Each PCBA labeled with a unique ID, enabling complete production traceability and batch tracking.
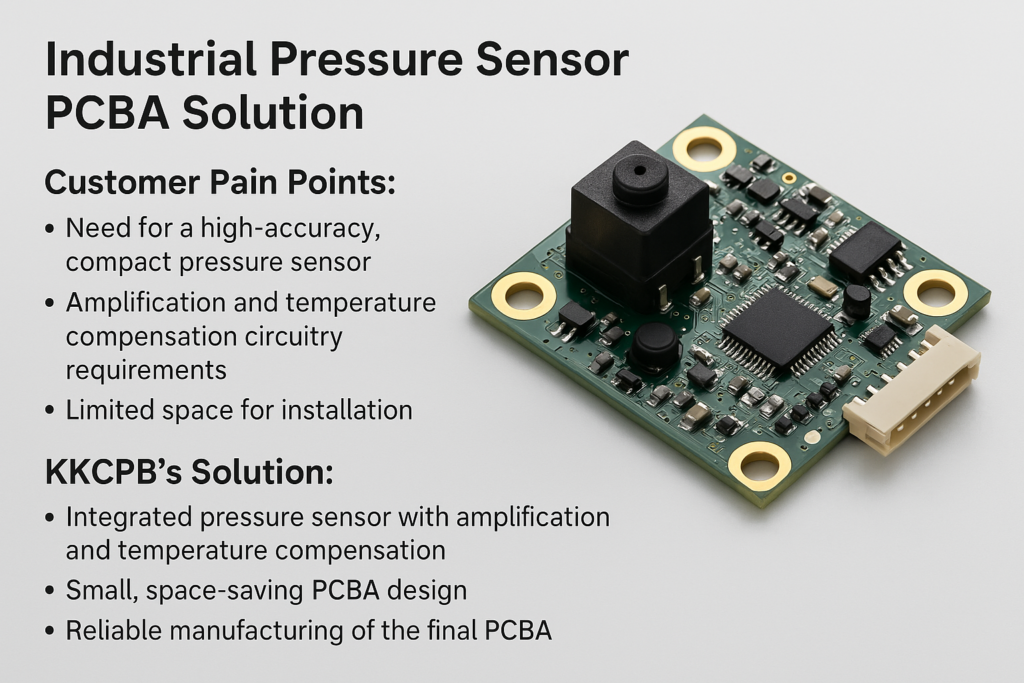
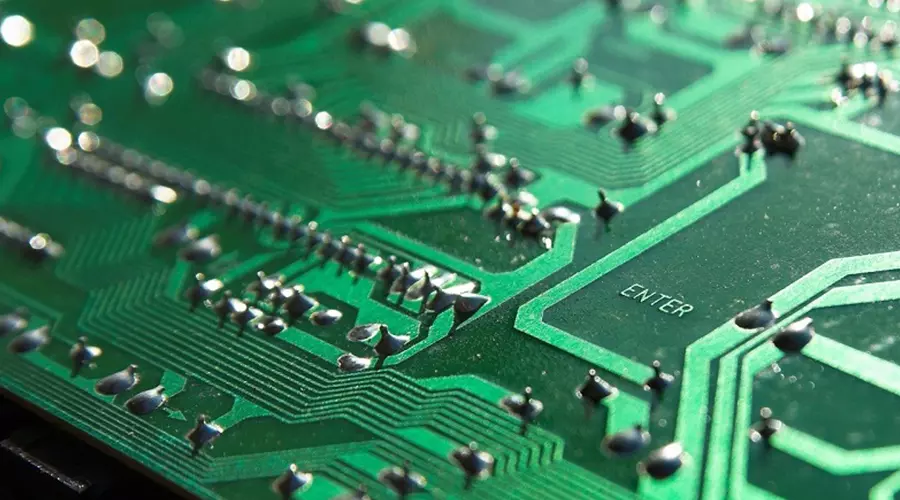
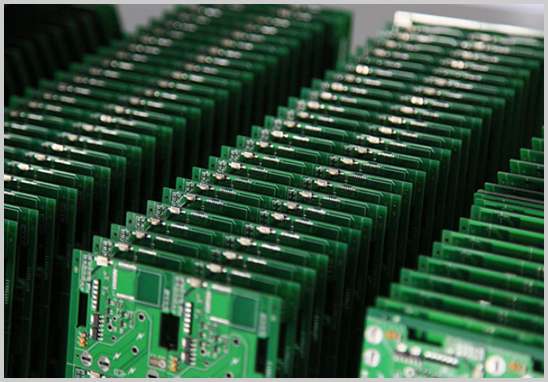
7. Actual Results of the Applied Solution
The delivered PCBA modules performed exceptionally in client-side testing. Installed in multiple end-user systems, they operated stably for over six months in environments characterized by vibration, humidity, temperature variation, and electromagnetic interference—without signal distortion or sensor failure.
Thanks to KKPCB’s efficient production and testing process, the client reduced their overall delivery cycle by 30%, enabling them to win competitive bids and onboard more B2B customers. As a result, KKPCB was added to the client’s global preferred PCBA vendor list, with further collaborations already underway in industrial control applications.