PCB Warpage: Causes, Prevention & Solutions Explained
When designing and manufacturing Printed Circuit Boards (PCBs), one common yet often overlooked issue is warpage. Warping occurs when the PCB bends or twists, leading to alignment issues during assembly. This deformation can cause misalignment of components, poor solder joints, and even failure of the final product.
In this article, we will explore what causes PCB warpage, how to detect it, and simple ways to prevent it. By understanding these factors, you can ensure your PCBs remain flat and function properly.
What is PCB Warpage?
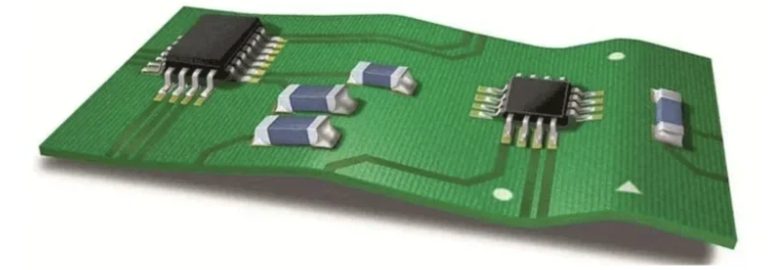
PCB warpage occurs when the board does not remain flat and starts to bend or twist, often due to thermal stress, material issues, or manufacturing errors. The flatness of the board is essential for the correct placement of components and proper soldering. When warpage happens, it can affect the overall functionality of the PCB and increase the risk of defects.
Common Causes of PCB Warpage
Understanding the common causes of PCB warpage is crucial for preventing this issue during manufacturing. Several factors can contribute to warpage, from thermal stresses to material choices and manufacturing techniques.
Let’s dive into some of the most significant causes of warping in PCBs.
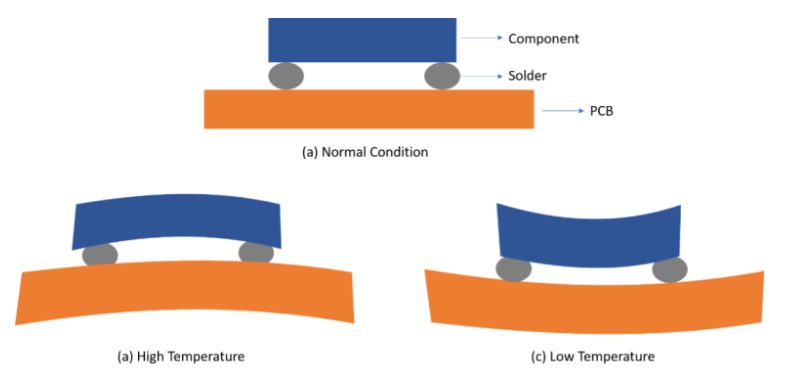
Thermal Stresses
One of the primary causes of PCB warpage is thermal cycling during processes like reflow and curing. As the PCB heats up and cools down, it undergoes thermal expansion and contraction.
If the heating or cooling rate is too fast or uneven, it can lead to thermal gradients, where different parts of the board expand at different rates. This differential expansion can cause the PCB to bend or twist, leading to warpage.
How Thermal Cycling During Reflow and Curing Can Cause Warpage
During the reflow soldering process, PCBs are exposed to high temperatures, which causes the material to expand. When the board cools, the materials contract.
If the cooling process is too rapid or uneven, it can create stresses on the board, resulting in warpage. This is especially problematic for multi-layer PCBs, where different layers may experience different thermal expansions.
The Effect of Thermal Gradients and Differential Expansion
Thermal gradients occur when different areas of the PCB experience varying temperatures. The outer layers of the board may cool faster than the inner layers, causing uneven contraction.
This differential expansion is particularly noticeable in thick or multi-layer PCBs and can lead to significant warping if not carefully controlled during manufacturing.
Material-Related Causes
The materials used in PCB construction play a major role in warpage. Certain materials, especially those with low glass transition temperature (Tg), are more susceptible to deformation under heat.
ow-Tg materials soften at lower temperatures, making them prone to warping during processes like soldering.
Use of Low-Tg Materials (Glass Transition Temperature) and Their Susceptibility to Warping
Low-Tg materials have a lower temperature threshold where they transition from a hard, rigid state to a more flexible, soft state. When exposed to high temperatures during soldering or reflow processes, these materials can bend or warp easily.
Using high-Tg materials, which have a higher heat resistance, can help prevent this issue and reduce the likelihood of warpage.
Moisture Absorption and Its Impact on Warping During Soldering
Moisture absorption is another significant factor that contributes to PCB warpage. When PCBs absorb moisture from the environment, the moisture turns to steam during the soldering process, leading to expansion of the board.
This can cause the PCB to warp, especially if the moisture is unevenly distributed. It’s important to dry the boards before soldering to avoid this issue.
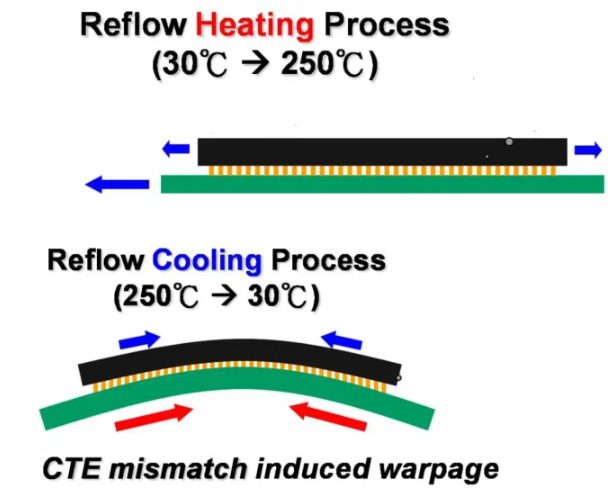
Manufacturing and Process Issues
Issues during the manufacturing process can also contribute to warpage. For instance, inconsistent heating and cooling can cause different parts of the PCB to expand and contract at different rates.
Poor lamination during the PCB manufacturing process can also lead to warping. If the layers aren’t bonded properly, it can result in a weak structure that is more prone to warpage.
Inconsistent Heating, Cooling, and Poor Lamination
Inconsistent heating and cooling during the manufacturing process can cause differential expansion, leading to warping. If the PCB is not heated evenly, some parts of the board may expand or contract more than others.
Similarly, poor lamination can create weak spots in the board, making it more vulnerable to deformation. Ensuring consistent temperatures and proper lamination can significantly reduce the risk of warpage.
Asymmetrical Design and Material Imbalance in Multi-layer PCBs
Multi-layer PCBs are especially prone to warpage if the design or material distribution is asymmetrical. If the layers are not evenly balanced in terms of material thickness and type, the board can warp during thermal cycling. It’s essential to design multi-layer PCBs with symmetry in mind to prevent uneven expansion and reduce the risk of warping.
Environmental Factors
Finally, environmental factors like humidity and moisture absorption can also contribute to PCB warpage.
If the PCB is stored or handled improperly, exposure to moisture can cause the board to absorb water, leading to swelling and eventual warping.
Environmental conditions should always be monitored, and PCBs should be stored in dry, controlled environments to avoid these issues.
Humidity and Moisture Absorption
Humidity is a major environmental factor that can cause PCB warpage. If a PCB absorbs moisture, the material can expand unevenly during soldering, leading to warping.
Proper storage in dry conditions and pre-baking the boards to remove moisture can prevent this. It’s crucial to keep the boards in sealed containers or use moisture barriers to protect them.
Consequences of PCB Warpage
PCB warpage can cause a range of problems during the manufacturing and assembly process. When a board warps, it becomes harder to align components correctly, and the risks of failure increase. Understanding the consequences of warpage is key to preventing issues and ensuring your PCBs are reliable and functional.
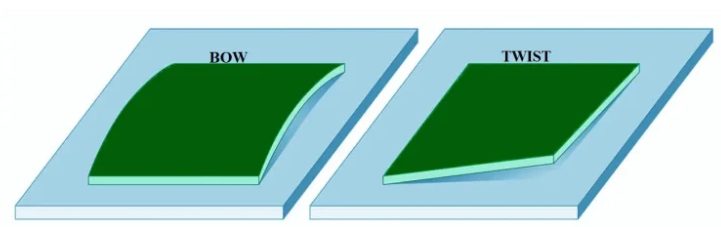
Assembly Challenges
When a PCB warps, component placement and alignment become a real challenge. During assembly, especially in automated processes, the misalignment can result in components not being placed accurately. This can lead to failed connections and ultimately, a defective board that doesn’t function as intended.
Difficulty in Component Placement and Alignment
If a PCB is warped, it can shift during the pick-and-place process, making it difficult to position components properly.
Even small misalignments can cause issues during the soldering process, leading to improper connections. This makes assembly much more time-consuming and increases the risk of defects.
Effect on Automated Assembly Processes Like Pick-and-Place
Automated assembly machines, like pick-and-place robots, rely on the PCB being flat to place components precisely.
Warping disrupts this process, causing misplacement of parts and leading to costly rework. In some cases, automated machines may even reject warped boards, adding delays to production.
Component Issues
Warpage not only affects assembly but can also cause component issues. When the PCB bends, components may not seat correctly, which increases the risk of damage during assembly.
Broken components or misaligned parts can result from improper seating, further affecting the board’s overall quality.
Improper Component Seating and Risk of Damage
When a PCB warps, the components on it may not fit snugly into their designated slots. This can cause mechanical stress on the parts, which might lead to damage.
Even minor bending can break sensitive components or displace them from their correct positions, causing permanent damage to the board.
Risk of Electrical Contact Problems
Warpage can also create electrical contact issues, such as broken vias or poor solder joints.
If a PCB is not flat during the soldering process, solder may not properly flow into joints, leading to unreliable electrical connections.
Intermittent connections or signal integrity problems can arise, affecting the performance of the final product.
Functional Failures
The long-term effects of PCB warpage can be catastrophic for the functionality of a product. Even if the board seems to work at first, warping can cause issues that worsen over time, leading to functional failures.
The board may experience electrical reliability problems, resulting in the complete failure of the device.
Long-Term Impact on PCB Reliability and Performance
Warpage doesn’t just cause immediate assembly issues—it can also impact the reliability and performance of the PCB over time.
Constant stress and misalignment can cause gradual failures, leading to diminished performance and early product failure.
By preventing warpage, you ensure your PCBs last longer and perform better throughout their life cycle.
How to Prevent PCB Warpage
Preventing PCB warpage requires a combination of design adjustments, careful material selection, and following the best manufacturing practices.
By taking a proactive approach to each stage of the PCB creation process, you can minimize the risk of warping and ensure your boards perform as expected.
Design Adjustments
One of the first steps in preventing PCB warpage is to focus on the design. Ensuring symmetry in the PCB layout helps to balance thermal stresses during the manufacturing process.
Uneven thermal expansion can cause boards to warp, so symmetrical designs ensure that heat is distributed evenly across the board.
Symmetry in PCB Design to Balance Thermal Stresses
Designing your PCB with symmetry in mind helps to distribute thermal stress more evenly. By placing components, traces, and pads in a balanced way, you reduce the chances of certain areas expanding or contracting more than others during thermal cycling. This minimizes the risk of warping that could result from uneven stress.
Use of Uniform Materials and Proper Layer Stacking
Using uniform materials and carefully considering layer stacking is another key to reducing warpage. In multi-layer PCBs, make sure the materials are balanced across layers.
Improper stacking or mismatched materials between layers can cause differential expansion, which leads to warping.
A consistent material choice across layers helps maintain uniform stress distribution and prevents warpage.
Material Selection
The materials you choose for your PCB play a huge role in determining whether it will warp. By selecting the right materials from the start, you can greatly reduce the chances of warpage occurring during both the manufacturing and assembly processes.
High-Tg Materials for Better Thermal Stability
When choosing PCB materials, opt for high-Tg (glass transition temperature) materials. These materials have a higher resistance to heat, making them more stable under high temperatures.
High-Tg materials are particularly beneficial in environments where thermal cycling is a concern. They help maintain dimensional stability, reducing the likelihood of warpage.
Moisture-Resistant Coatings and Careful Material Sourcing
Moisture absorption can lead to warping during soldering or reflow, so consider using moisture-resistant coatings on your PCBs.
These coatings help prevent moisture from penetrating the board, which could cause material expansion and ultimately, warping.
Additionally, sourcing materials from trusted suppliers ensures you receive high-quality materials that are less prone to warping issues.
Manufacturing Best Practices
Even with the best design and material choices, manufacturing best practices are essential to ensure your PCBs stay flat and free from warpage. Thermal management during the reflow and curing processes plays a critical role in preventing warping.
Optimal Thermal Management During Reflow and Curing
Proper thermal management is key during reflow and curing processes. Ensure that heating and cooling cycles are controlled carefully to avoid creating thermal gradients that can cause uneven expansion.
By maintaining a consistent temperature throughout the process, you can reduce the risks of warping that can occur when areas of the PCB heat or cool at different rates.
Stress Relief Techniques Such as Pre-Baking and Post-Assembly Treatment
To further reduce the risk of warpage, you can implement stress relief techniques. Pre-baking the PCB before assembly helps to remove moisture, which can reduce the chance of warping.
Additionally, post-assembly treatment can help relieve internal stresses that might have built up during the production process, leading to more stable final products.
Handling and Storage
After the PCB is manufactured, proper handling and storage are crucial to avoid introducing any physical stress that could lead to warping.
By ensuring correct handling procedures and proper storage conditions, you can maintain the integrity of the PCB and keep it free from warpage during transport and storage.
Proper PCB Storage to Reduce Moisture Absorption
Storage plays a vital role in preventing warpage caused by moisture absorption. Always store PCBs in a dry, controlled environment to prevent the material from absorbing moisture from the air.
Moisture can lead to expansion during reflow or soldering, contributing to warpage. By storing the boards in sealed bags or moisture-controlled environments, you help maintain their flatness and stability.
Best Handling Practices to Avoid Physical Damage
Physical damage during handling can cause warping, so always follow best practices when transporting or moving PCBs.
Use proper supports when handling boards, and avoid putting pressure on the edges or corners.
By using gentle handling techniques, you reduce the risk of deformation and ensure the boards stay flat during the assembly process.
Detection and Measurement of PCB Warpage
Accurately detecting and measuring PCB warpage is essential for ensuring the quality and functionality of your boards.
Whether you’re performing a quick visual check or using advanced measurement tools, there are several methods to detect warping before it affects the assembly process.
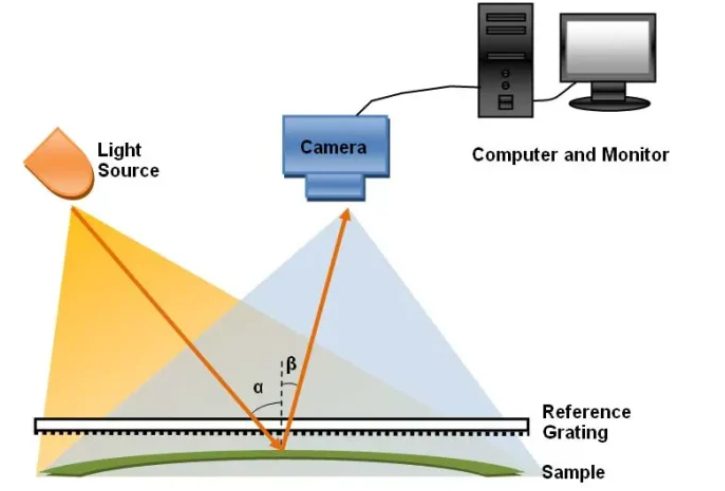
Visual Inspection Techniques
The simplest method of detecting PCB warpage is through visual inspection. A quick look at the board can reveal visible warping such as bowing or twisting.
Bow refers to a slight upward or downward curve along the PCB’s surface, while twisting means the board has become uneven along multiple axes, leading to an angular shift.
These deformations can easily be seen with the naked eye and may be an early sign of issues that need further investigation.
Simple Checks for Visible Warping (e.g., Bowing, Twisting)
A visual inspection is often the first line of defense when checking for warpage. To perform a simple check, place the PCB on a flat surface and observe the edges. If the board is bowed, the edges will lift off the surface in the middle.
For twisting, you might see the board become visibly crooked along one or more axes. These issues can often be detected with basic tools like a ruler or caliper to measure the deviation from flatness. Catching these visible signs early can help prevent assembly problems down the road.
Advanced Measurement Methods
While visual inspections are useful, advanced measurement methods are required to get precise, quantifiable data about the warpage. These techniques can detect even minute deformations that might go unnoticed with a basic inspection.
Tools like optical systems and precision measuring instruments are commonly used in these cases. One such method is Moire pattern analysis, which creates a pattern of interference lines when applied to a warped PCB, revealing even subtle warping.
Using Precision Tools and Optical Techniques Like Moire Pattern Analysis
For high-precision measurements, you can use optical techniques like Moire pattern analysis.
This method involves projecting a grid pattern onto the surface of the PCB and analyzing how the pattern changes when the board warps. The distortion of the pattern directly correlates to the degree of warping.
This technique provides high-resolution insights into the exact extent of warpage, allowing for more accurate corrections during production.
Testing During Production
Warpage detection should not be an afterthought—integrating it into the quality control process during production is crucial. By performing routine checks throughout the manufacturing process, you can catch warpage issues early, before they affect the final assembly.
How Warpage Detection Should Be Integrated into Quality Control
Warpage detection should be incorporated at multiple stages during the production process, especially after key manufacturing steps like lamination, reflow soldering, and curing.
During these stages, use both visual inspections and advanced measuring tools to monitor the quality of the boards.
This proactive approach helps to catch any warping before it progresses to a point that could impact the functionality or performance of the PCB. Integrating warpage checks into quality control ensures higher yield rates and fewer defects.
Fixing PCB Warpage
If your PCB has suffered from warping, don’t panic! There are effective methods to fix the warpage and bring your board back to its intended state.
Whether it’s rebaking, heat treatment, or following best practices, careful handling is essential to restore functionality and avoid further damage.
Rework Methods
One of the most common ways to fix PCB warpage is through rebaking and pressing. Rebaking involves heating the PCB to a specific temperature to release built-up thermal stresses.
Afterward, pressing the PCB under controlled pressure can help flatten the board. This method is effective for mild warping, but it’s crucial to monitor the temperature closely to avoid overheating, which could cause additional damage.
Heat Treatment
For more severe warping, controlled heat treatment can provide a more effective solution. This method involves heating the PCB to relieve the internal stresses that cause the warping.
The goal is to gently apply heat in a controlled manner, allowing the material to relax and return to its more stable form. However, it’s important to monitor the process carefully to avoid thermal shock, which could worsen the warping.
Best Practices for Rework
During any rework process, caution and care are key. If you don’t handle the board with proper attention, you might accidentally introduce new stresses or cause delamination.
When performing rebaking or heat treatment, always follow manufacturer guidelines and avoid overdoing the heat or pressure.
Taking your time and using precise equipment can help ensure that the repair is successful without causing further damage.
FAQs About PCB Warpage
What are the signs of PCB warpage?
The signs of PCB warpage include visible bending, twisting, or bowing of the board. This can be seen by eye or with a flat surface check. Additionally, component misalignment during the assembly process is often a clear indication of warpage.
How does PCB warpage affect soldering?
PCB warpage can lead to improper solder joints due to misalignment of components during reflow soldering. Warped boards can cause poor electrical connections, especially when components are not placed flat, increasing the risk of faulty joints and unreliable performance.
Is PCB warpage common in multi-layer PCBs?
Yes, multi-layer PCBs are more prone to warpage because of the complex structure. Differences in material thickness and thermal expansion between layers can lead to uneven thermal stresses, which causes the PCB to warp. Proper layer stacking and material selection are crucial in these designs.
What is the role of moisture absorption in PCB warpage?
When PCBs absorb moisture, it can cause uneven expansion during the soldering process, contributing to warping. Moisture-sensitive materials are particularly vulnerable. This is why pre-baking or drying the boards before assembly is important to reduce warpage risks caused by moisture absorption.
Can PCB warpage be prevented during the reflow process?
Yes, controlling thermal gradients during the reflow process can help prevent warpage. Use uniform heating and ensure the temperature profile is stable to avoid thermal stress. Proper cooling rates and even heat distribution will reduce the chances of warping during this critical stage.
In summary, PCB warpage is a common issue in manufacturing that can cause significant assembly and performance problems.
By understanding the causes and detection methods of warpage, you can prevent it through proper design, material selection, and manufacturing practices.
When warpage does occur, methods like rebaking, pressing, and heat treatment can effectively fix the problem, ensuring your boards stay functional and reliable.