PCB Substrate and Core Materials: A Comprehensive Guide
The Printed Circuit Board (PCB) is a fundamental component in all modern electronics, providing the platform for the electronic components and circuits. The performance, durability, and overall quality of a PCB are heavily influenced by the materials used for its substrate and core. This comprehensive guide explores the different types of PCB substrate and core materials, their properties, applications, and why they are important for engineers, PCB manufacturers, and students.
What are PCB Substrate and Core Materials?
In a PCB, the substrate is the foundational material that provides mechanical support for the electronic components and circuits. It acts as the base layer upon which all other materials are applied.
The core typically refers to the material that is sandwiched between the copper layers in a multilayer PCB. It serves as a dielectric medium to separate the conductive layers while maintaining structural integrity.
Difference Between PCB and Package Substrate
While both PCBs and package substrates are integral to electronic devices, they have different roles and applications.
Feature | PCB | Package Substrate |
---|---|---|
Definition | A base for mounting and connecting components | A special PCB that serves as a base for IC packages |
Structure | Multiple layers of copper, insulation, etc. | Used in advanced semiconductor packaging (e.g., BGA, CSP) |
Function | Supports and electrically connects components | Connects ICs to the main PCB |
Applications | Found in a variety of electronic devices | Used in high-performance semiconductor devices |
Types of PCB Substrate Materials
- FR4 (Flame Retardant 4)
FR4 is a glass-reinforced epoxy laminate and the most widely used PCB substrate.- Features:
- Excellent strength-to-weight ratio
- Good electrical insulation
- Fireproof
- High mechanical and dielectric strength
- Applications:
- Consumer electronics, automotive, industrial equipment, telecommunications
- Features:
- CEM-1 (Compound Epoxy Material)
CEM-1 is a paper-based material with a single layer of glass weave, a cost-effective alternative to FR4.- Features:
- Moderate mechanical strength
- Good electrical insulation
- Fireproof
- Applications:
- Low-cost consumer electronics, basic circuit boards, single-sided PCBs
- Features:
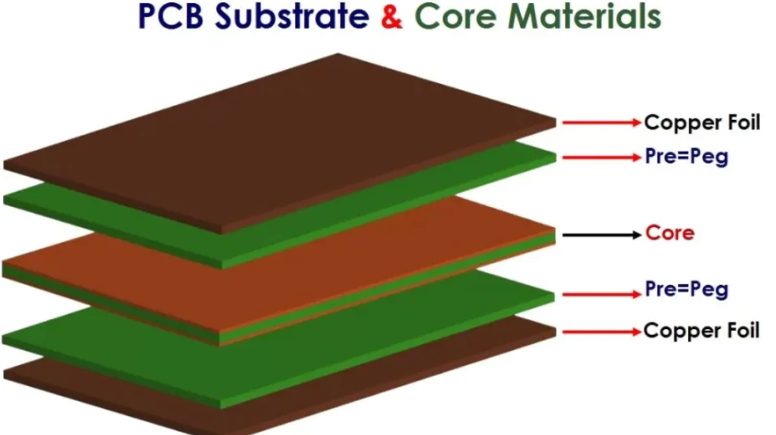
- Polyimide
Polyimide is a high-performance plastic known for its excellent thermal stability.- Features:
- Excellent heat resistance
- High flexibility
- Excellent chemical resistance
- Applications:
- Aerospace, military, medical devices, flexible PCBs
- Features:
- Rogers Material
Rogers materials are high-frequency laminates with excellent electrical properties.- Features:
- Low dielectric constant
- Minimal signal loss
- Excellent thermal management
- Applications:
- RF/microwave PCBs, high-speed digital applications, communication systems
- Features:
- PTFE (Polytetrafluoroethylene)
PTFE (Teflon) is used in high-frequency and microwave applications due to its low signal loss.- Features:
- Low dielectric constant
- High chemical resistance
- Excellent thermal stability
- Applications:
- High-frequency circuits, RF/microwave PCBs, aerospace applications
- Features:
Types of PCB Core Materials
- Copper Clad Laminate (CCL)
CCL is the most common core material, comprising a thin layer of copper foil bonded to a dielectric material.- Features:
- High electrical conductivity
- Excellent thermal conductivity
- Good mechanical strength
- Applications:
- Multilayer PCBs, high-density interconnects, general electronics
- Features:
- Metal Core PCB (MCPCB)
MCPCB uses a metal base (such as aluminum or copper) for better heat dissipation.- Features:
- Excellent heat dissipation
- Enhanced durability
- Improved thermal management
- Applications:
- LED lighting, power electronics, automotive electronics, smart home lighting
- Features:
- Ceramic Core
Ceramic cores offer excellent thermal properties, making them ideal for high-temperature environments.- Features:
- Excellent thermal conductivity
- High mechanical strength
- Excellent heat resistance
- Applications:
- Power modules, RF circuits, high-frequency applications
- Features:
Comparison: PCB Substrate vs. Core Materials
Material Type | Dielectric Constant | Thermal Conductivity |
---|---|---|
FR4 (Substrate) | 4.5 | 0.3 W/m·K |
CEM-1 (Substrate) | 4.8 | 0.25 W/m·K |
Polyimide (Substrate) | 3.5 | 0.12 W/m·K |
Rogers (Substrate) | 3.0 | 0.5 W/m·K |
PTFE (Teflon, Substrate) | 2.1 | 0.25 W/m·K |
Copper Clad Laminate (CCL, Core) | Not Applicable | Excellent |
MCPCB (Core) | Not Applicable | Excellent |
Ceramic Core | Not Applicable | Superior |
Choosing the Right Substrate and Core Materials
Selecting the proper substrate and core materials is essential in PCB design because they directly impact performance, durability, and cost. Here are some key considerations:
- FR4 is commonly chosen for general applications due to its balance between performance and cost.
- Rogers or PTFE substrates are better for high-frequency circuits or harsh environments.
- Ceramic cores are ideal for high-temperature or high-power applications.
- MCPCBs are excellent for thermal management and are commonly used in LED lighting and power electronics.
The choice of PCB substrate and core materials has a significant influence on the performance and cost of the final product. By understanding the characteristics and applications of each material, engineers and designers can select the best combination for their specific needs, ensuring that the PCB performs optimally in its intended environment.