PCB solder mask
PCB solder mask is one of the important components in the PCB process. In-depth knowledge of solder mask will help engineers design PCBs with better functions and quality. This article will explore the composition of PCB solder mask and its important role.
Composition of PCB solder mask
- Resin
- Resin is the basic component of PCB solder mask ink and determines the basic performance of the ink. Common types of resins include epoxy resin, acrylic resin, polyester resin, etc.
- Pigment
- Pigments give PCB solder mask a specific color. Common colors include green, blue, black, white, etc.
- The choice of pigment not only affects the appearance of the PCB, but also is related to the light reflectivity, thermal stability, etc. of the solder mask, and also affects the manufacturing cost to a certain extent.
- Green is the most common solder mask color because it is visually comfortable and has moderate light reflection, which helps reduce light interference.
- Green ink can achieve smaller errors, smaller areas, and higher precision. The design accuracy of green, red, and blue is higher than that of other colors.
- The characteristics of green ink are better than other colors. The characteristics of green ink are better than other colors, especially the blocking characteristics of green.
-Green ink is relatively cheap. Since green is the mainstream in the production process, the process is the most mature and simple, the purchase volume of green ink will naturally be larger, so its purchase cost will be lower than other colors.
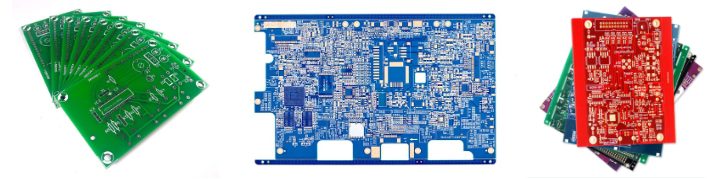
-PCB color has no effect on the function of the circuit board.
- Solvent
-The solvent plays a role in adjusting the viscosity and fluidity of the PCB solder mask to facilitate the coating and printing of the ink.
- The volatility of the solvent has an important influence on the drying speed and curing effect of the ink.
- Additives
- In order to improve the performance of the PCB solder mask, various additives are usually added, such as defoamers, leveling agents, desiccants, ultraviolet absorbers, etc.
PCB solder mask thickness standard
PCB solder mask must have good film-forming properties, and its thickness is subject to regulatory requirements. At present, most PCB circuit board manufacturers mark according to the US civil standard IPC-SM-840C specification. In this standard, the solder mask thickness of Class 1 products is not limited; the minimum solder mask thickness of Class 2 products is 10um; the minimum solder mask thickness of Class 3 products should be 18um. The flame retardancy of solder mask is usually based on the regulations of the US UL agency and must pass the requirements of UL94V-0 (UL94-Plastic Flammability Test for Components in Devices and Equipment).
The thickness of the solder mask in the middle of the general circuit is not less than 10um, and the thickness on both sides of the circuit is not less than 5um.

The role of solder mask
- Prevent short circuit and leakage
- The circuits on the PCB are dense and the spacing is small. If there is no protection of the solder mask, adjacent circuits may cause short circuits or leakage due to accidental contact. The solder mask covers the area that does not need to be soldered, forming an insulation barrier, which effectively avoids this situation.
- Provide insulation protection
- Electronic equipment will be affected by various electromagnetic interference and voltage fluctuations during operation. Good insulation performance is essential to ensure the normal operation of the circuit. PCB solder mask can isolate the circuit from the external environment, prevent moisture, dust, corrosive gases, etc. from entering, thereby improving the insulation resistance and withstand voltage performance of the PCB and ensuring the stability and reliability of electronic equipment.
- Protect the circuit from mechanical damage
- During the manufacturing, assembly and use of PCB, it is inevitable to be subjected to various mechanical stresses, such as plugging and unplugging components, collisions during transportation, etc. The solder mask can provide a tough protective film for the circuit, reduce the impact of mechanical damage on the circuit, and extend the service life of the PCB.
- Improve welding quality
- The solder mask clearly defines the welding area, making the welding process more accurate and efficient. It can prevent solder from flowing into unnecessary areas, reduce the occurrence of welding defects such as cold welding and bridging, and improve the assembly quality and production efficiency of PCB.
- Enhance corrosion resistance
- Electronic equipment may be exposed to various corrosive substances such as acids, alkalis, and salts in the use environment. The solder mask can prevent these corrosive substances from directly contacting the metal circuit on the surface of the PCB, thereby delaying the corrosion and oxidation of the circuit and improving the corrosion resistance and service life of the PCB.
- Optimize heat dissipation performance
- Some types of PCB solder mask have certain thermal conductivity, which can help components on PCB dissipate heat and improve the working stability and reliability of electronic equipment.
- Beautify the appearance
- In addition to its functional role, PCB solder mask can also provide a beautiful appearance for PCB. Solder mask with different colors and patterns can make PCB look more neat and professional, and enhance the market competitiveness of products.
What causes the PCB solder mask to fall off?
- When printing ink on PCB, the pre-treatment is not done well, such as stains, dust or impurities on the surface of PCB board, or some areas are oxidized. In fact, it is very simple to solve this problem. Just do the pre-treatment again, but try to clean the stains, impurities or oxide layer on the surface of the circuit board.
- The baking time of the circuit board is short or the temperature is not enough, because the circuit board must be baked at high temperature after printing thermosetting ink. If the baking temperature or time is insufficient, it will affect the strength of the ink on the board.
- Ink quality problems or expired ink, or purchase of unknown brand ink, will also cause the circuit board ink to fall off when passing through the tin furnace.
As an indispensable part of the PCB manufacturing process, the reasonable matching and performance optimization of the various components of PCB solder resist ink are of great significance to ensure the quality and performance of PCB. PCB solder resist ink provides a strong guarantee for the stable operation and long-term reliability of electronic equipment by preventing short circuits, providing insulation protection, protecting circuits from damage, improving welding quality, and enhancing corrosion resistance. With the continuous development and innovation of electronic technology, the performance requirements for PCB solder resist ink will continue to increase. I believe that in the future, solder resist ink technology will continue to improve and make greater contributions to the development of the electronics industry.