PCB Screen Printing Vs PCB Inkjet Printing: What’s Difference
Printed circuit boards (PCBs) serve as the foundation for electronics, providing the mechanical structure and electrical connections between components. PCB fabrication involves many steps, including printing conductive traces, solder mask, legend, and other features onto the bare boards.
Two of the most common PCB printing methods are screen printing and inkjet printing. Both techniques can accurately reproduce fine features on a PCB, but have key differences in their processes, capabilities, and applications.
This article provides a detailed comparison of PCB screen printing versus inkjet printing across various factors:
- Basic process overview
- Resolution and feature size
- Accuracy and repeatability
- Print speed
- Substrate compatibility
- Ink and soldermask compatibility
- Changeover and setup
- Volume capability
- Equipment cost
- Pros and cons
Understanding these key differences will help PCB designers and fabricators select the optimal printing method for their specific requirements and production environments.
PCB Screen Printing Overview
Screen printing, also known as silkscreen printing, is a long-established process for printing legends, markings, solder mask and other features on PCBs. The key characteristics of screen printing include:
Process Overview:
- A fine mesh screen contains the desired image pattern
- Ink is flooded onto the screen and a squeegee presses the ink through open areas
- Ink transfers to the PCB surface, reproducing the screen image
Typical Features:
- Solder mask
- Silkscreen legends and markings
- Solder paste
Key Components:
- Screens with image patterns
- Ink for the application (epoxy, solder paste)
- Printer with squeegee assembly
Screen printing has been the traditional workhorse PCB printing process and provides a straightforward method for high volume solder mask and legend printing.
PCB Inkjet Printing Overview
Inkjet printing is a digital printing technique adapted for PCB production. Its key properties are:
Process Overview:
- Ink droplets ejected from printhead nozzles
- Droplets land on desired locations to form image
- No physical contact between printer and board
Typical Features:
- Solder mask
- Silkscreen legends
- Etch resist
- Solder paste
Key Components:
- Printheads with arrays of nozzles
- UV-curable inks
- Vision alignment system
- Digital image data
Inkjet allows on-demand, non-contact digital printing well suited for rapid design iterations, prototyping, and low to moderate volumes.
Resolution and Feature Size
A key specification for any printing process is the resolution and minimum feature size that can be achieved. These determine how fine the details are that can be reproduced.
Screen Printing Resolution
- Screens have mesh counts from 43 to 355 threads/cm
- Higher mesh counts offer higher resolution
- Minimum feature size Around 100μm (0.1mm or 4mil)
Inkjet Printing Resolution
- Printhead nozzles can be 12-50μm diameter
- Droplet sizes down to 5 picoliters
- Minimum feature size 25-50μm (0.025-0.05mm or 1-2mil)
Comparison
- Inkjet capable of 2-4x higher resolution than screen printing
- Enables finer traces, spaces, text, and soldermask details
Higher resolution inkjet printing allows PCBs to implement dense, complex designs with ultra-fine features.
Accuracy and Repeatability
Precision and consistency are vital for printing Small errors or variability will degrade performance.
Screen Printing Accuracy
- Aligned manually or with pins
- Registration around 50-100μm
- Screen stretching can distort image
- Consistency relies on operator skill
Inkjet Printing Accuracy
- Vision alignment system for 10μm precision
- Digital process avoids image distortion
- Automated calibration and controls
- Registration down to 15μm or better
Comparison
- Inkjet provides 5-10x tighter registration accuracy
- Minimal human errors or screen issues
- Improved consistency across panels and batches
Inkjet’s precision alignment and digitally-driven process offer superior accuracy and repeatability for high density PCBs requiring tight tolerances.
Print Speed
Throughput is an essential productivity and cost consideration.
Screen Printing Speed
- Typical speed 500-1000mm/second
- Large batches achieve high throughput
- Flood and squeegee process limits acceleration
Inkjet Printing Speed
- Maximum velocity up to 10m/second
- No physical contact enables faster printing
- Small batches feasible without speed loss
Comparison
- Inkjet can print 5-10x faster than screen printing
- No squeeze delays allow rapid printing
- High acceleration further boosts speed
With its non-contact method and quick acceleration, inkjet offers significantly faster printing times ideal for rapid prototyping and small batches.
Substrate Compatibility
The ability to print on various board materials is important for supporting different applications.
Screen Printing Compatibility
- Epoxy, polyimide, flex, metal core PCBs
- Challenging for non-planar or warped boards
- Surface must contact screen evenly
Inkjet Printing Compatibility
- Compatible with all rigid and flex PCB materials
- Conformal printing for non-planar boards
- Tolerates warpage better than screens
Comparison
- Inkjet compatible with more substrates
- Flexible prints conform to warped/uneven surfaces
- No contact reduces material restrictions
Inkjet printing places fewer limits on board materials and shapes, allowing unconventional PCBs with flexibility, 3D geometry, and other innovations.
Ink and Soldermask Compatibility
The printing process must work with necessary specialty inks and soldermasks.
Screen Printing Compatibility
- Wide range of compatible soldermask inks
- Limited by viscosity and particle size
- Not suitable for UV-curable inks
Inkjet Printing Compatibility
- Formulated UV-curable inks required
- Lower viscosity than screen printing inks
- Prints soldermask, legend, etch resist, and paste
Comparison
- Inkjet requires specialized ink development
- Enables printing fine features in soldermask
- Compatible with a broader range of inks
With custom ink design, inkjet supports printing finer soldermasks, etch resists, and other specialty fluids.
Changeover and Setup
Fast, easy changeovers between prints allow efficient operation.
Screen Printing Changeover
- Screens must be cleaned, coated, aligned
- Significant setup time and labor
- Low changeover efficiency
Inkjet Printing Changeover
- Digital process with no screens
- Quick purge and priming of printheads
- Automated alignment and calibration
Comparison
- Inkjet changeovers are near instantaneous
- Saves time and costs for short runs
- Enables fast design iterations
Inkjet printing eliminates Screens and provides rapid digital changeovers ideal for prototyping, low volume, or highly variable production.
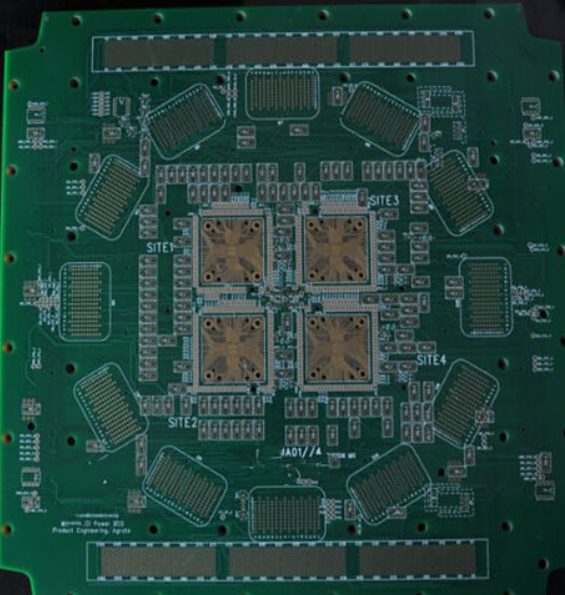
Volume Capability
The practical volume capacity is a key differentiator between printing technologies.
Screen Printing Volumes
- Highly suited for long runs >10,000 boards
- Maximum throughput with minimal changeovers
- Not practical for small lots
Inkjet Printing Volumes
- Capable of variable batches from 1-1000 boards
- Low volume prototyping to moderate production
- Small lots without compromising speed
Comparison
- Screen printing for high volume long runs
- Inkjet printing for short runs and prototyping
- Combination creates flexibility
Screen printing handles heavy production demands, while inkjet enables low volume prototyping and ramp-up leading into higher volume screen printing.
Equipment Costs
The equipment investment impacts affordability and access to the technology.
Screen Printing System Cost
- Manual presses ~$10,000
- Automated presses from ~$50,000
- Screen coating/processing equipment additional
Inkjet Printing System Cost
- Manual benchtop systems ~$20,000
- Automated systems from ~$100,000-$250,000
Comparison
- Inkjet systems cost 2-4X more than screen printing
- Justifiable for changing requirements, new capabilities
While inkjet requires greater up-front investment, it can provide value through increased adaptability along with resolution and accuracy improvements.
Pros and Cons Comparison
Printing Method | Pros | Cons |
---|---|---|
Screen Printing | – Proven, well-known process <br> – Compatible with wide range of soldermasks <br> – Capable of high volume production | – Lower resolution limits fine features <br> – Limited accuracy and repeatability <br> – Slow changeovers and limited flexibility |
Inkjet Printing | – Ultra-high resolution <br> – Excellent accuracy and precision <br> – Fast digital changeovers <br> – Low to moderate volume capable | – Requires custom inks <br> – Higher equipment cost <br> – Not suited for very high volumes |
Table 1. Major pros and cons of screen printing vs. inkjet printing
Both methods have complimentary strengths making them optimal for different applications and volumes.
Conclusion
- Screen printing and inkjet each have unique capabilities to meet different PCB printing requirements.
- Screen printing delivers proven performance for long runs, while inkjet enables digital flexibility.
- Resolution, accuracy, and setup time are key differences between the processes.
- Volume requirements, substrate compatibility, inks, and budget factor into the printing choice.
- Many shops utilize both techniques to maximize their manufacturing agility.
With in-depth understanding of the trade-offs, PCB designers and fabricators can strategically leverage screen and inkjet printing to achieve their cost, capability, and volume objectives. Utilizing the strengths of each approach provides access to a wide range of affordable, high performance PCB printing options.