PCB Materials: Building Blocks of Electronic Devices
Printed circuit boards (PCBs) are at the heart of modern electronic devices, powering everything from smartphones to aerospace systems. The journey of PCB materials has evolved significantly since their inception in the early 20th century. This article explores the composition, types, and advancements of PCB materials, essential for understanding the foundation of today’s electronic innovations.
Evolution of PCB Materials
Early PCBs were made from materials such as wood, cardboard, bakelite, and fiberboard. Conductive traces were manually etched from copper foil, and components were connected using wires and hand-drilled holes. While bakelite provided excellent insulation, its brittleness and susceptibility to moisture presented challenges.
The introduction of phenolic resin-based laminates in the 1930s improved mechanical stability and insulation. However, the game-changer was the development of glass-reinforced epoxy laminates (FR-4) in 1940, offering superior electrical insulation, moisture resistance, and mechanical durability.
As technology advanced, PCB materials diversified to support complex functionalities and miniaturized designs, catering to industries such as aerospace, medical, and defense.
Basic Composition of PCB Materials
A PCB comprises multiple layers, each designed for specific roles, such as insulation, conductivity, or protection. These include:
- Substrate Material
Acts as an insulating base for copper layers. The substrate choice depends on electrical performance, thermal requirements, and environmental conditions.- FR-4:
- Made of woven glass fiber and epoxy resin.
- Cost-effective, excellent insulation, and high heat resistance.
- Suitable for most consumer and industrial applications.
- Polyimide (PI):
- High-performance polymer known as “Kapton.”
- Offers thermal stability, chemical resistance, and flexibility.
- Used in aerospace, automotive, and flexible PCBs.
- Metal Core PCBs (MCPCBs):
- Use aluminum or copper as base layers for heat dissipation.
- Ideal for power electronics, high-power LEDs, and automotive systems.
- FR-4:
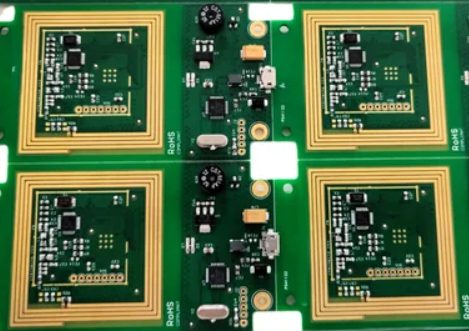
- Conductive Materials
Provide the pathways for electrical signals.- Copper Foil:
- Commonly used due to its excellent electrical and thermal conductivity.
- Thickness varies based on application, measured in ounces per square foot (Oz/ft²).
- Plated Through Holes (PTH):
- Establish connections between PCB layers.
- Copper plating thickness typically ranges from 0.8 to 1 mil.
- Copper Foil:
- Surface Finish
Prevents oxidation and enhances solderability. Common finishes include:- ENIG (Electroless Nickel Immersion Gold):
- Offers a smooth surface, ideal for HDI and multi-layer PCBs.
- HASL (Hot Air Solder Leveling):
- Traditional tin-lead alloy or lead-free alternatives like tin-copper or tin-silver.
- OSP (Organic Solderability Preservative):
- A water-based compound providing temporary oxidation protection.
- Immersion Silver:
- Uses silver coating for improved conductivity and solderability.
- ENIG (Electroless Nickel Immersion Gold):
- Solder Mask
- Protects copper traces from oxidation and environmental damage.
- Facilitates soldering and enhances moisture and corrosion resistance.
- Available in colors like green, blue, black, white, and red.
- Silkscreen
- Provides component identifiers and design details on the PCB surface.
- Uses non-conductive epoxy ink in various colors, including white, black, and yellow.
Applications of PCB Materials
Modern PCB materials are designed to cater to diverse applications:
- Consumer Electronics: Smartphones, laptops, and wearable devices rely on lightweight and cost-effective materials like FR-4.
- Aerospace & Automotive: High-performance materials like polyimide withstand extreme temperatures and mechanical stress.
- Medical Devices: Flexible PCBs and metal core PCBs provide durability and heat dissipation.
- Power Electronics: Metal core PCBs manage high thermal loads effectively.
Conclusion
PCB materials have come a long way since their early days, evolving to meet the demands of increasingly sophisticated electronic devices. From cost-effective FR-4 to advanced materials like polyimide and KKPCBs, each type plays a crucial role in shaping the functionality and reliability of modern technology. As electronics continue to miniaturize and diversify, innovations in PCB materials will undoubtedly keep pace, driving the next wave of technological breakthroughs.