PCB Manufacturing Packaging Process
Proper packaging plays a crucial role in ensuring the safe delivery of PCBs, particularly in competitive markets where quality and presentation are key factors. Though packaging may not generate direct added value, it impacts customer satisfaction and reflects professionalism, particularly for high-precision products like PCBs.
This article discusses the importance of packaging, the evolution of packaging practices, and the modern packaging processes used in PCB manufacturing. It also highlights best practices for optimizing efficiency, material use, and customer satisfaction.
1. Importance of Packaging in PCB Manufacturing
While packaging may not contribute to the technical performance of a PCB, it is vital for the following reasons:
- Customer Perception: Thoughtful and robust packaging enhances customer confidence and reinforces the quality of the product.
- Product Protection: Prevents damage during transportation, ensuring the board’s integrity upon delivery.
- Compliance: Many electronics manufacturers demand specific packaging standards to ensure compatibility with their production lines.
Japanese companies excel in packaging, often designing custom molds or containers for fragile or high-quantity products like flexible PCBs, enhancing both protection and usability.
2. Early PCB Packaging Practices and Their Drawbacks
Traditional packaging methods often fell short in terms of protection and efficiency. Some small factories still use outdated techniques, leading to problems like:
- Insufficient protection against physical and environmental damage.
- Higher material and labor costs due to inefficient processes.
- Poor customer experience, particularly for export orders.
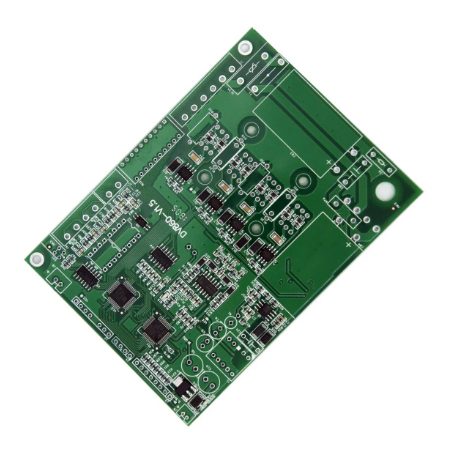
3. Modern PCB Packaging Processes
Modern packaging focuses on vacuum skin packaging and other methods to ensure durability, efficiency, and adherence to customer specifications.
3.1. Vacuum Skin Packaging Process
Vacuum skin packaging involves covering PCB stacks with PE film and securing them through vacuum sealing. This process minimizes movement during transit and protects the boards from external damage.
Steps in the Process:
- Preparation:
- Position the PE film.
- Test the machinery for proper functioning.
- Set parameters like PE film heating temperature and vacuum suction time.
- Stacking Boards:
- Stack boards to optimize material use and prevent wastage.
- Spacing Guidelines:
- Spacing between stacks should be twice the thickness of the PE film to ensure adhesion and ease of cutting.
- Outer spacing between the boards and the edge should equal the thickness of the board.
- Alternative Methods:
- For smaller panels, mold-specific containers may be used for bulk packaging, subject to customer approval.
- Cardboard layers can separate stacks for added protection.
- Vacuum Sealing:
- Heated PE film is pressed down and vacuumed to adhere tightly to the boards and bubble wrap.
- Cool and separate stacks by cutting the film after sealing.
- Packing:
- Adhere to customer-specified packing methods.
- Ensure cartons protect boards from transportation forces.
- Labeling and Documentation:
- Clearly mark the package with product details, including part number (P/N), revision, batch cycle, quantity, and origin (e.g., “Made in Taiwan” for exports).
- Attach quality certificates like solderability reports, test records, and other customer-required documents.
4. Best Practices for PCB Packaging
Efficiency and Protection
- Custom Molds: For small or flexible PCBs, custom packaging molds save materials and improve protection.
- Material Optimization: Use materials effectively by adhering to spacing standards and customer specifications.
- Export Packaging: Ensure exported products meet durability and weight specifications to avoid damage during international transit.
Documentation
- Include all necessary information and certificates in a format specified by the customer.
- Use clear external labeling to streamline inventory and logistics processes.
5. Advantages of Modern Packaging Practices
Aspect | Traditional Packaging | Modern Packaging |
---|---|---|
Protection | Minimal, prone to damage | High, with vacuum sealing |
Material Use | Wasteful | Optimized through precise stacking |
Efficiency | Time-consuming | Streamlined processes |
Customer Satisfaction | Low | High, with compliance to standards |
Cost | Higher in the long run | Balanced for quality and quantity |
KKPCB conducts research on special processing technologies such as ordinary double-sided boards, thick copper circuit boards, high-frequency circuit boards, HDI circuit boards, rigid-flexible circuit boards, FPC flexible boards, buried blind hole circuit boards, and IC carrier boards. Provides PCB design, PCB layout, PCB prototyping and PCB assembly services.