PCB for SMT (Surface Mount Technology): Choosing the Right PCB for SMD Components
What is a PCB?
A Printed Circuit Board (PCB) is a vital component in almost every electronic product. It serves as the foundation for connecting electronic components through conductive paths (traces), typically made of copper. The traces facilitate the flow of electrical current, enabling electronic devices to function.
A PCB can be made of various materials, such as glass epoxy, which provides durability and insulation. It may feature either through-hole components or Surface Mount Devices (SMD), or even a combination of both. When all components are soldered onto a PCB, the assembly is referred to as Printed Circuit Board Assembly (PCBA) or PCA (Printed Circuit Assembly).
What is PCB for Surface Mount Technology (SMT)?
Surface Mount Technology (SMT) is a widely used method for manufacturing PCBs, where Surface Mount Devices (SMD) are directly mounted onto the surface of the PCB. This technology allows for a more compact design and higher component density compared to traditional through-hole mounting.
When selecting a PCB for SMT, several key factors must be considered to ensure optimal performance and longevity. These include:
- Coefficient of Thermal Expansion (CTE)
- Cost
- Dielectric Properties
- Glass Transition Temperature (Tg)
Selecting the Right PCB Material for SMT
When designing a PCB for SMT, it’s crucial to select the appropriate material, considering factors like the types of SMD components being used. One of the most common issues in SMT PCB design is solder joint cracking. This occurs due to the mismatch in CTE (Coefficient of Thermal Expansion) between the PCB substrate and the SMD components.
For example, Leadless Ceramic Chip Carriers (LCCCs) mounted on glass epoxy substrates can experience significant stress, leading to solder joint cracking after around 100 thermal cycles. This is primarily due to the difference in thermal expansion rates between the ceramic package and the PCB material.
To avoid these problems, it’s important to carefully select the PCB substrate material based on the following:
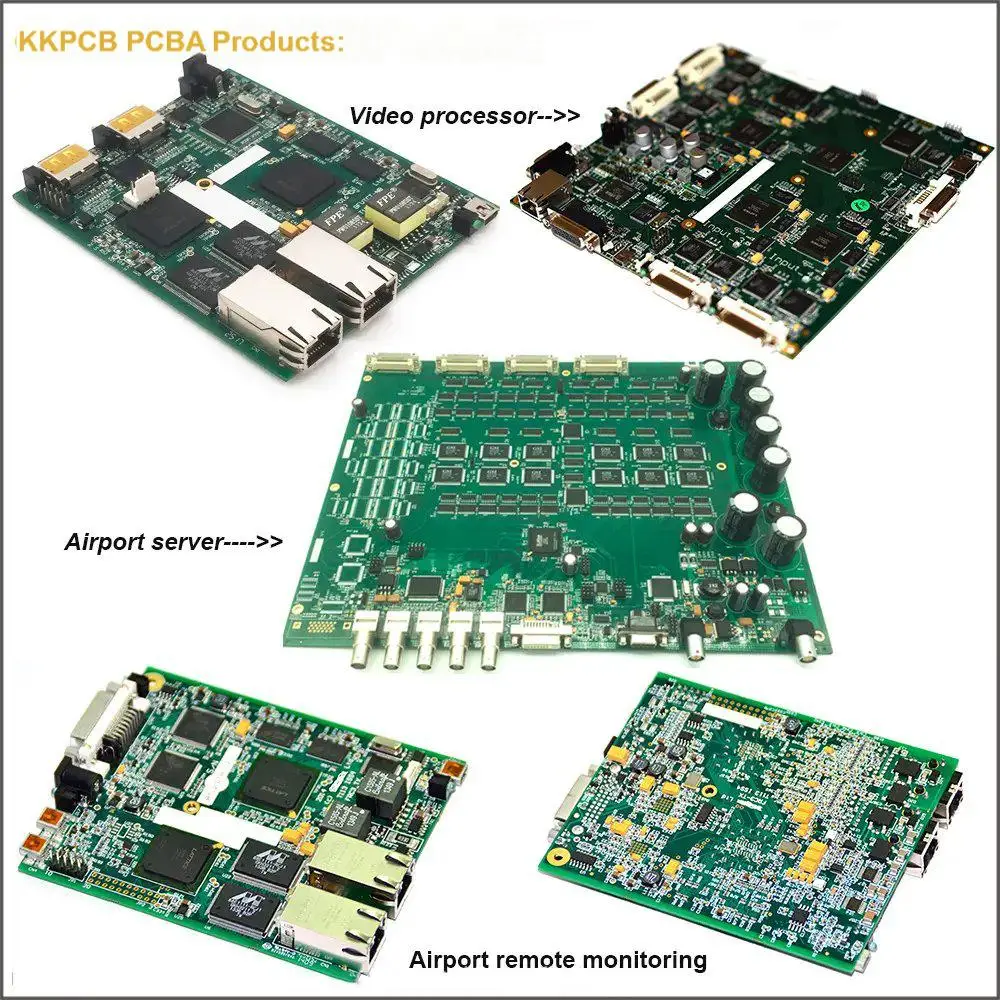
Key Factors in Selecting SMT PCBs
- CTE Compatibility: Ensuring the CTE of the PCB material is compatible with that of the components to reduce stress at solder joints.
- Tg (Glass Transition Temperature): The temperature at which the PCB material transitions from a rigid state to a more flexible one. For SMT, a higher Tg is often required for better performance under heat cycling.
- Dielectric Properties: The ability of the PCB material to insulate electrical signals. Different materials will provide varying levels of dielectric strength.
Common Problems Caused by Incorrect SMT PCB Selection
Selecting the wrong PCB for SMT can lead to several issues, most notably solder joint cracking, which can significantly affect the reliability of the finished product. The primary causes of solder joint cracking include:
- CTE Mismatch: If the PCB material and the SMD components have differing CTE values, the resulting thermal expansion during heating and cooling cycles can cause the solder joints to crack over time.
Solutions to Solder Joint Cracking
There are several ways to solve or mitigate the solder joint cracking problem:
- Use a PCB with Compatible CTE: Choose a substrate material with a CTE that matches the SMD component to minimize stress.
- Select a Compatible Top Substrate: Some SMT designs use a combination of materials to balance out the CTE differences between the PCB and components.
- Use Leaded Ceramic Packages: Replacing leadless ceramic packages with leaded packages can reduce the risk of cracking, as leaded components typically have a more flexible design and better compatibility with various substrates.
Common PCB Substrate Materials for SMT
The most commonly used substrates for SMT PCBs are:
- Glass Epoxy (FR-4): The FR-4 grade is the most widely used material for SMT boards due to its affordability, good thermal properties, and CTE compatibility with most plastic SMD components.
- Polyimide: For flexible PCBs or high-performance applications, polyimide is an excellent choice due to its superior thermal stability and flexibility.
- Ceramic Substrates: In military and high-performance applications, ceramic-based PCBs are often used because of their excellent CTE compatibility with ceramic packages and superior thermal conductivity.
Key Considerations for SMT PCB Design
- Solder Mask and Via Size: Proper selection of solder mask and via sizes is crucial to ensure effective electrical performance and to prevent issues like signal integrity problems or heat dissipation failures.
- Material Cost vs. Performance: Glass epoxy (FR-4) is cost-effective but may not be suitable for all applications. Designers should balance material costs with the required performance, especially when working on high-heat or high-reliability applications.
Selecting the right PCB material for SMT is critical to ensuring the reliability and performance of Surface Mount Technology assemblies. The CTE compatibility, Tg, and dielectric properties of the substrate material must be carefully considered to prevent common issues like solder joint cracking.
With proper material selection and design practices, SMT PCBs can provide high-density, reliable, and cost-effective solutions for a wide range of electronic applications.