PCB Design For Military & Aerospace Applications
Military and aerospace PCBs must adhere to intensely high standards to ensure their safety and functionality in the extreme conditions they’re used in. For this reason, PCB design for military and aerospace applications requires incredibly stringent guidelines with built in redundancy, extra safety, and stringent tolerances, minimizing risk of failure.
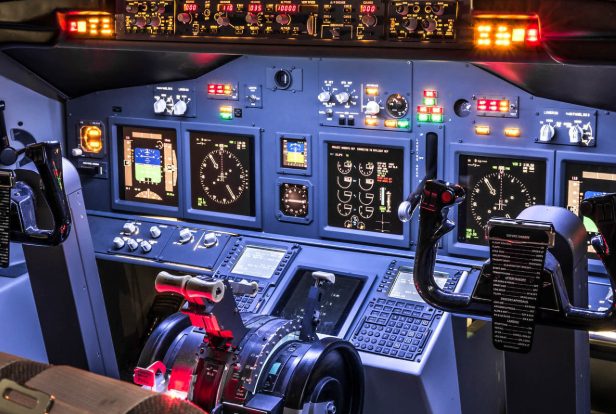
General PCB Design Tips for Military and Aerospace Applications
Category | Tips and Considerations |
Component Selection | Use mil-spec components with low tolerances (1-2%) rather than standard 5~10% tolerance components. |
Current Capacity | Design with additional current capacity to manage unexpected spikes. Handle maximum current load with shorter traces, heavy copper (3-4 ounces per square foot), and heat dissipation techniques. |
Aspect Ratio | Maintain a low aspect ratio (1:10 or less) to ensure reliability and stability in harsh environments.Recommended through-hole aspect ratio is 10:1 with a maximum board thickness of 100 mil. |
Plane Separation | Separate power and ground planes; segregate low-frequency components from high-frequency ones to reduce interference. Minimum dielectric thickness between planes should be 3.5 mil. |
Signal Protection | Shield clock signals using materials like aluminumProtect other critical signals especially in RF applications. Guarding the clock signal with an aluminum enclosure can resolve EMI issues. |
Annular Ring | The copper pad area around the drilled hole should have a defined width of 6-7 mils minimum for the external and internal layers.Recommended drill to copper clearance is 7-8 mil. |
Performance and Testing Standards for Military & Aerospace Applications
In PCB design for military & aerospace applications, adhering to standards is critical. Key IPC documents such as IPC-2610 Series, IPC-D-325, and IPC-J-STD-001, including the Space Addendum, provide comprehensive guidelines for PCB documentation, manufacturing, and assembly. Specific applications, including those for the Navy, FAA, and satellites, require compliance with IPC standards for materials and stack-ups.
Performance and testing standards such as MIL-PRF-50884, MIL-PRF-31032, MIL-PRF-55110, and MIL-PRF-19500 are mandatory for military PCBs, while AS9100 and AS9100D apply to aerospace PCBs. Additionally, compliance with the International Traffic in Arms Regulation (ITAR) is essential for military and aerospace PCB assembly. Regulated by the Department of State, ITAR mandates strict control over sensitive information related to the design and production of military and intelligence devices, ensuring the highest level of security and reflecting current technological, political, and security climates.
Wrap Plating
Wrap plating involves extending copper plating from the drilled hole onto the board surface. The IPC-6012 and IPC-A-600 standards define three classes for electrolytic hole plating thickness:
- Class I: Thickness agreed upon between user and supplier (AABUS).
- Class II: Continuous wrap plating through filled plated holes, extending onto the PCB surface, with a minimum thickness of 5 μm [197 μin]. Processes like planarization should not reduce this thickness.
- Class III: Minimum wrap plating thickness of 12 μm [472 μin] for through-holes and vias greater than 2 layers. Buried via cores require at least 7 μm [276 μin], and blind/buried microvias need a minimum of 6 μm [236 μin].
Challenges in wrap plating include knee cracking from thermal cycles, butt joint failures, and maintaining minimum thickness standards during the planarization process, which can vary by ±0.3 mils.
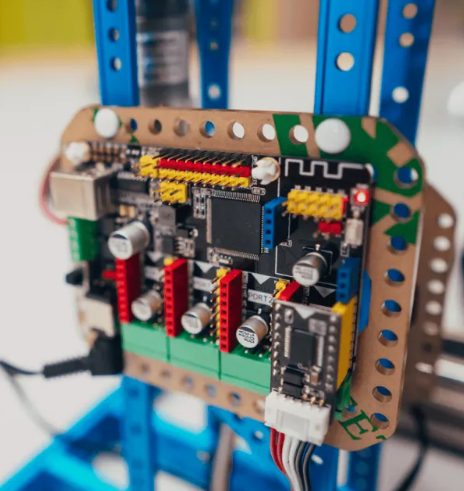
Military & Aerospace Applications Require PCB Design for Harsh Conditions
Category | Tips and Considerations |
Acceleration and Vibration | Design to withstand forces from rapid accelerations. Use through-hole assembly for strong component adherence, which also improves signal transmission.Mount military-grade components to minimize vibration effects. Design a symmetrical stackup with uniform copper distribution for enhanced stability. |
Lightning Protection | Include surge protection circuits and use materials that are resistant to high transient voltages to safeguard against lightning strikes. |
Radiation Effects | Employ radiation-hardened designs to protect from ionizing radiation in space and high-altitude applications.Use rad-hard components as per military standards (MIL-PRF-38535), and incorporate antifuse technology in aerospace PCB assembly for enhanced reliability and security. |
Packaging Challenges | Design rugged packaging to protect the electronics from shocks, vibrations, and environmental factors. This includes creating enclosures that can withstand external pressures and impacts. |
Test Coverage and Access | Ensure comprehensive test coverage and facilitate easy test access by incorporating test points and in-circuit testing to verify functionality and durability under test conditions. |
Material Considerations for Military & Aerospace Applications
Category | Tips and Considerations |
Resins and Foils | Select resins and foils that perform well under extreme conditions for optimal electrical and thermal performance. Suitable materials include high-temperature laminates with substrates like copper or aluminum.Recommended materials are FR408, Pyralux AP, and Nelco N7000-2HT, all known for their high Tg (glass transition temperature) values. |
Moisture, Salt, and Sand Effects | Opt for materials that resist corrosion and environmental degradation. To safeguard PCB components from moisture, humidity, and extreme temperatures, a conformal coating of acrylic resin applied via spray is advised.Preferred surface finishes include electroless nickel with immersion gold coating (ENIG) or hot air solder leveling (HASL). |
Conformal Coatings, Potting Compounds, Staking Compounds | Utilize these materials to protect components from environmental damage while improving insulation and thermal management. |
Conformal Coating
For extreme operating conditions, choose PCB finishing materials like electrolytic nickel gold, ENIG, chemical silver, HASL, and lead-free HASL. Conformal coatings protect against heat, humidity, water, and vibrations, crucial for aerospace applications. Additionally, applying an acrylic-based spray protects the PCB from contamination and short circuits.
Applications of PCB for Aerospace Electronics
KKPCB offers extensive PCBA, wire harness, cable, and box build assembly services for commercial and industrial markets, with a strong focus on the aerospace industry. Our experienced team works with customers to fully realize their aerospace designs, regardless of the complexity