PCB Design Best Practices: Key Considerations for Optimized Performance
When designing printed circuit boards (PCBs), a well-structured approach and attention to detail are essential to ensure functionality and avoid potential design errors. Here are some key PCB design tips based on practical experience:
1. Pay Attention to Pin Definitions and Package Names in the Schematic Library
When creating the schematic library, ensure that each schematic pin corresponds correctly to its package pin. Mismatches between pins in the schematic and PCB layout can lead to component isolation and connectivity issues during the board assembly process.
2. Manage High-Frequency Signals with Proper Trace Design
Every trace on a PCB causes signal delay, especially when handling high-frequency signals. Serpentine traces are commonly used to compensate for delays in signals within the same group, such as clock signals. On computer motherboards, serpentine traces serve dual functions: impedance matching and acting as a filter inductor to reduce interference and improve stability.
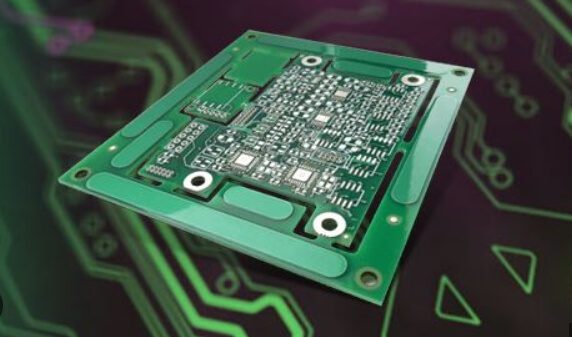
3. Wave Soldering and Component Orientation
For components on the welding surface undergoing wave soldering, the orientation matters. Resistors and capacitors should be perpendicular to the direction of wave soldering, while SOP components and resistor arrays should be parallel to the transmission direction. Certain ICs and components with a pin spacing of less than 1.27mm should avoid wave soldering.
4. Component Spacing Guidelines
Maintain appropriate spacing between components to facilitate manufacturing and prevent short circuits. For BGA packages, ensure a minimum distance of 5mm from adjacent components. Patch components should have at least 0.7mm spacing, and components near crimped connectors should have a 5mm clearance around them.
5. IC Decoupling Capacitors Placement
Place decoupling capacitors as close to the IC power pins as possible to minimize noise and ensure signal integrity. The loop formed between the power supply and ground should be as short as possible to reduce electromagnetic interference (EMI).
6. Group Components Based on Power Supply
When arranging components, group those that use the same power supply together. This simplifies power distribution and allows for easier separation of power planes if necessary.
7. Proper Placement of Impedance Matching Resistors
Impedance matching resistors should be placed based on their function. Series resistors should be close to the driving end of the signal, ideally within 500mil. For multi-load terminal matching, place resistors at the farthest end of the signal.
8. Cross-Check Layout with the Schematic
After completing the layout, print an assembly drawing to verify the accuracy of component placement and signal integrity. This ensures that the device package and signal correspondence between the single board, backplane, and connectors are correct before starting the wiring process.
9. Setting Wiring Constraints
After the layout is determined, use the PCB design tool’s statistical functions to assess parameters such as the number of networks, pin density, and the number of signal layers required. Proper constraints help ensure design efficiency and reduce post-production errors.
10. Via Hole Specifications
When designing via holes, consider the board thickness-to-aperture ratio, which should generally be between 5:1 and 8:1. Standard hole sizes range from 8mil to 24mil, and pad diameters should be appropriately chosen based on the hole size. Ensuring correct via hole dimensions helps avoid issues in the manufacturing process.
11. Blind and Buried Vias
Blind vias connect the surface layer to the inner layers without penetrating the entire PCB, while buried vias connect internal layers only. Both types of vias require specific size considerations and a full understanding of the PCB fabrication process. Coordination with the PCB manufacturer is necessary to prevent complications.
12. Test Holes for ICT
Test holes are typically used for In-Circuit Testing (ICT) and can also serve as via holes. Test hole pad diameters should be at least 25mil, with a center-to-center distance of no less than 50mil. Avoid using component soldering holes as test holes.
Engineering Process Application:
- Problem-Solving: Address specific design challenges, analyze issues, and apply solutions or improvements based on design needs.
- Progress Monitoring: Track the project timeline to ensure deadlines are met and quality standards maintained.
Conclusion:
Proper PCB design requires careful planning and attention to detail, from schematic creation to component layout and wiring. Following these best practices ensures optimized signal integrity, reduces interference, and minimizes manufacturing issues, leading to higher-quality and more reliable PCB designs.