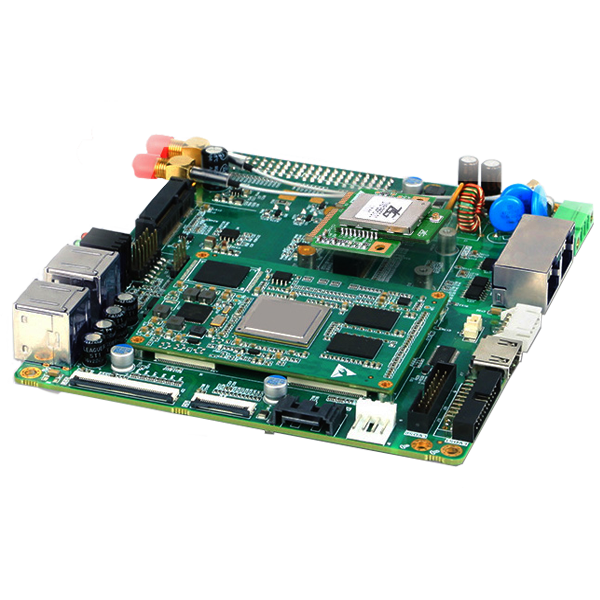
// Precision Manufacturing | Stringent Quality Control | Zero-Defect Commitment
High-Reliability PCB Assembly Solutions
✅ Surface Mount (SMT) & Through-Hole (THT) Assembly
✅ BGA, QFN, Fine-Pitch, and High-Density Component Placement
✅ Lead-Free & RoHS-Compliant Soldering
✅ X-ray, AOI, ICT & Functional Testing for Zero Defects
✅ Prototype to Mass Production with Global Delivery
Zero-Defect PCB Assembly with Strict Quality Control
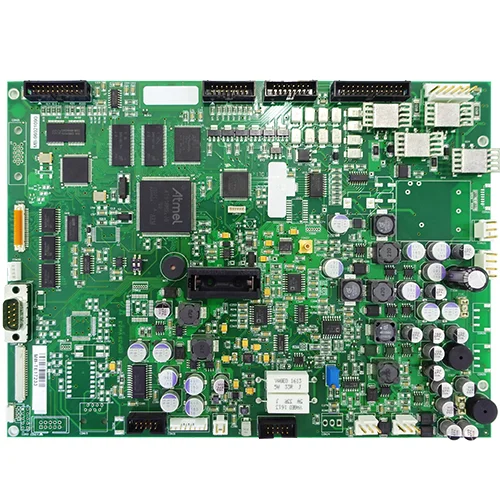
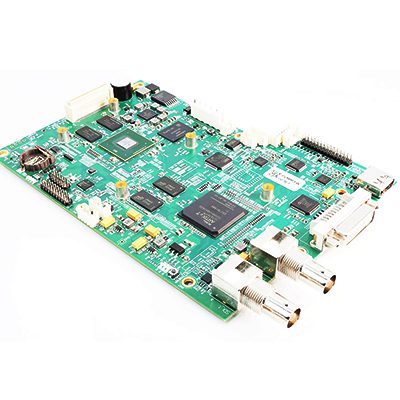
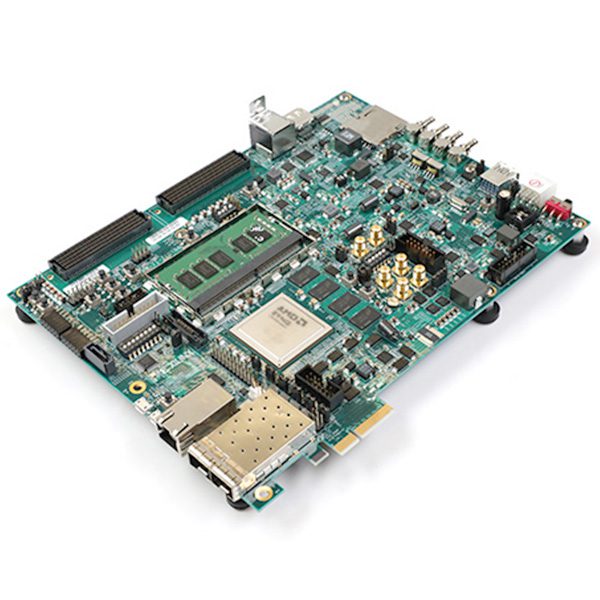
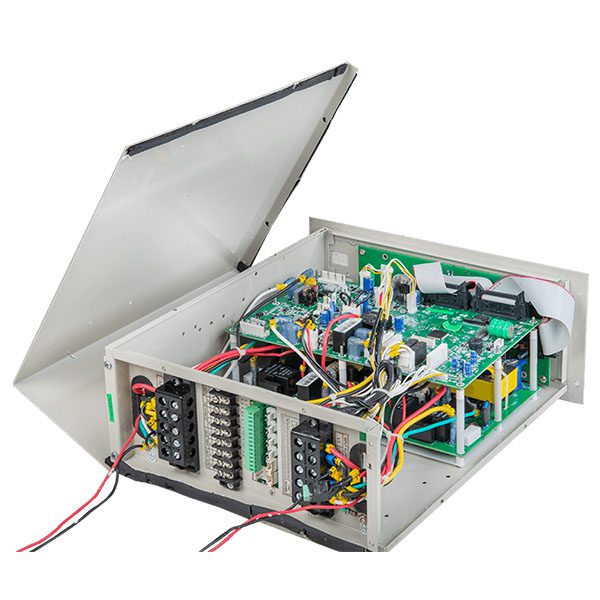
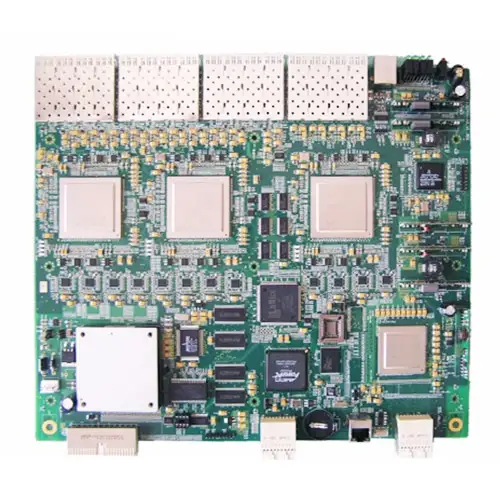
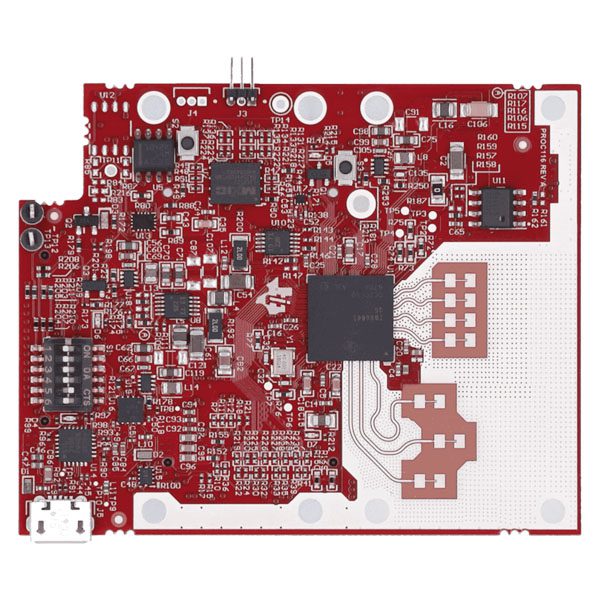
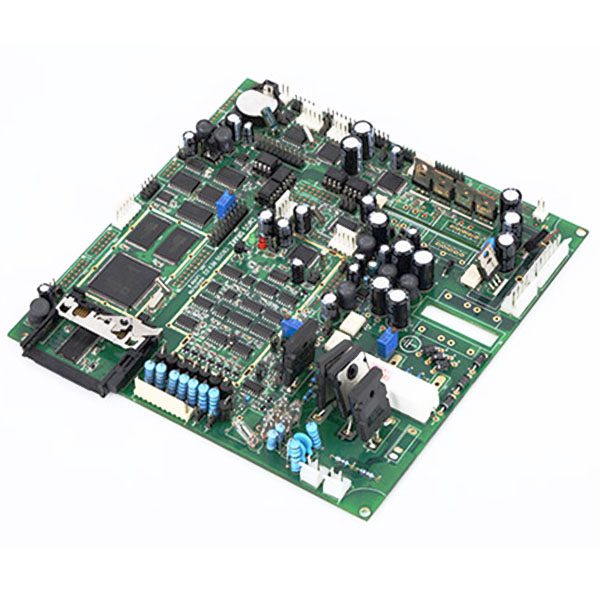
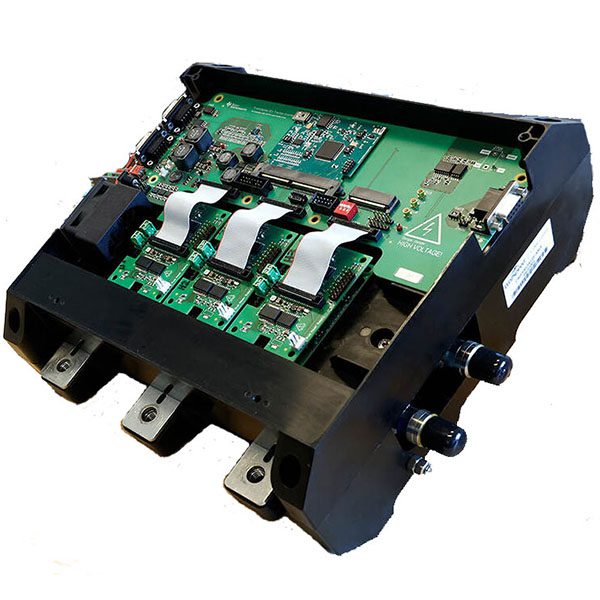

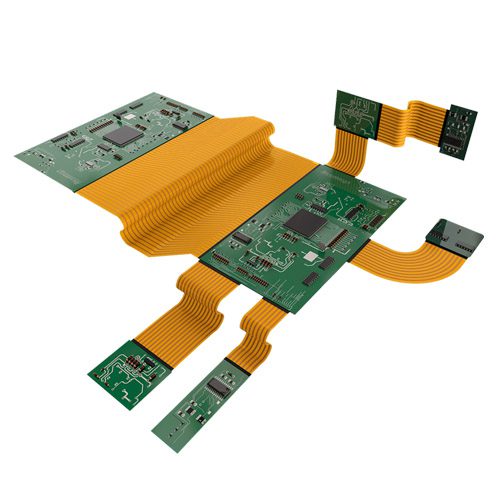
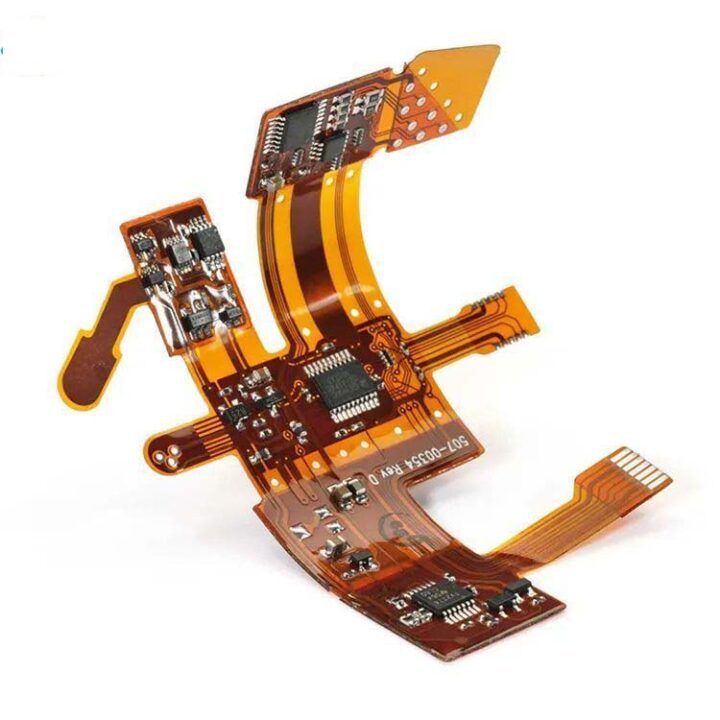
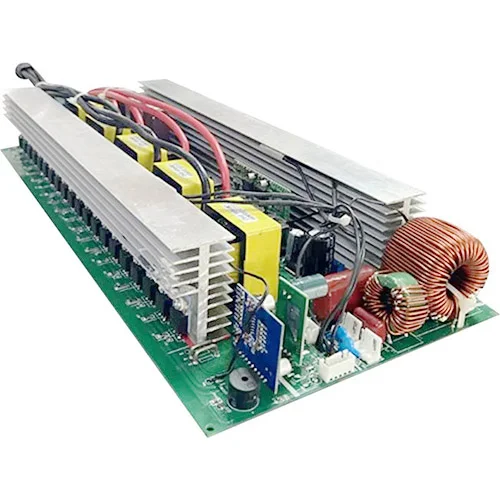
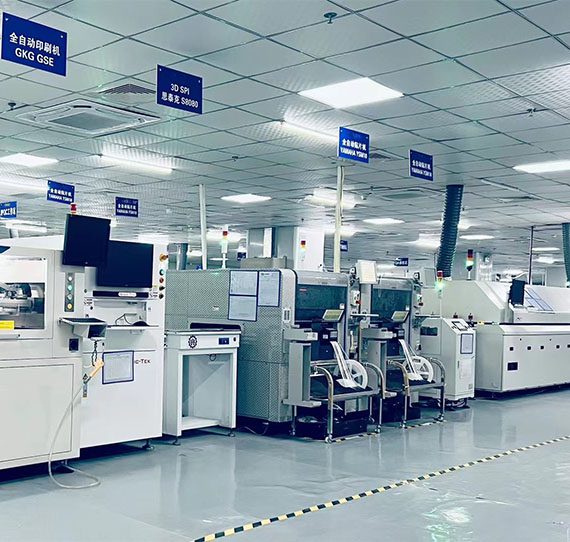
Your most reliable
PCB assembly service provider in China
DfMA Services
Parallel factories to reduce prototype iterations,improve quality and output while lowering costs,enhance product reliability.
Assembly Types
Surface mount assembly (SMT),Through-hole assembly (THT),Mixed (SMT+THT),Single/Double sided assembly
Component Procurement
Strict IQC incoming inspection, warehouse management with temperature and humidity control, and anti-static measures.
PCBA Functional Testing
Functional testing of PCBA can prevent manufacturing and quality issues, reduce unnecessary repair costs, and improve customer satisfaction.
Extremely Strict Quality
Control Production Process
- DfMA Services
- Raw Material Inspection
- Functional Testing
At KKPCB, we provide Design for Manufacturing and Assembly (DfMA) services to help customers optimize PCB designs for cost-effectiveness, manufacturability, and reliability. Our expert engineering team works closely with clients to analyze circuit layouts, material selection, and assembly processes, ensuring seamless production and enhanced product performance.
With DfMA principles, we help reduce production risks, minimize rework, and improve efficiency, leading to faster time-to-market and higher yield rates. Whether you need PCB design validation, cost reduction strategies, or manufacturing optimization, KKPCB ensures your products meet the highest quality and performance standards.
✅ Design Optimization for Manufacturing & Assembly
✅ Cost Reduction & Yield Improvement
✅ DFM, DFA & DFT Analysis for High-Reliability PCBs
✅ Prototype to Mass Production Support
📩 Partner with KKPCB for Smarter, More Efficient PCB Manufacturing!
At KKPCB, we believe that high-quality PCB assemblies start with the highest-quality raw materials. Our comprehensive Raw Material Inspection process ensures that every PCB substrate, electronic component, solder paste, and flux meets strict industry standards before production begins. By implementing rigorous incoming quality control (IQC), advanced testing technologies, and full material traceability, we eliminate defects at the source and guarantee superior reliability and performance in every assembled PCB.
✅ PCB Laminate & Solder Mask Integrity Verification
✅ Component Authenticity & Electrical Performance Testing
✅ Solder Paste, Flux, and Adhesive Composition Analysis
✅ X-ray Inspection for BGA, QFN, and Hidden Solder Joints
✅ Moisture Sensitivity, RoHS, and REACH Compliance Certification
With state-of-the-art inspection equipment such as X-ray analysis, AOI (Automated Optical Inspection), XRF (X-ray Fluorescence), and ICT (In-Circuit Testing), we ensure that only certified, high-quality materials enter our assembly lines. Our strict quality control protocols minimize the risk of defects, enhance long-term reliability, and ensure that your PCBs perform flawlessly in automotive, medical, aerospace, industrial, and consumer electronics applications.
📩 Choose KKPCB for Uncompromising Quality in Every PCB Assembly!
At KKPCB, we understand that a PCB assembly is only as good as its performance in real-world applications. That’s why we implement rigorous Functional Testing (FCT) to verify that every assembled PCB operates exactly as intended before it reaches our customers. Our comprehensive FCT process simulates actual working conditions, ensuring electrical functionality, signal integrity, and system-level performance across a wide range of industries, including automotive, medical, aerospace, industrial, and consumer electronics.
✅ Power-Up Testing & Voltage/Current Measurement
✅ Microcontroller & Firmware Verification
✅ Load Simulation & Signal Integrity Analysis
✅ RF, Wireless, and High-Speed Circuit Testing
✅ Custom Test Fixture Development for Specific Applications
With our advanced testing infrastructure, including ICT (In-Circuit Testing), Flying Probe, Boundary Scan, and Custom Test Racks, we ensure that every PCB assembly meets stringent industry standards such as IPC, ISO, and IATF 16949. Our goal is to eliminate defects, reduce field failures, and deliver reliable, production-ready PCBs that perform flawlessly in mission-critical applications.
📩 Partner with KKPCB for High-Performance, Fully Tested PCB Assemblies!
Valuing Customer We Served
For complete key-turn services, we produce everything, including manufacturing the circuit boards, finding and ordering PCB components, printed circuit board assembly, surface mount PCB assembly, quality inspections, testing, and the final circuit board and product assembly.
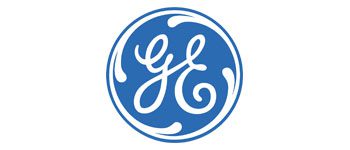
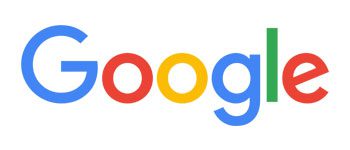
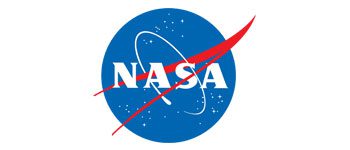
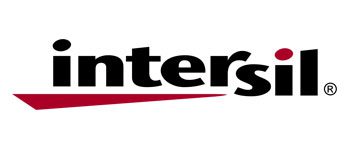
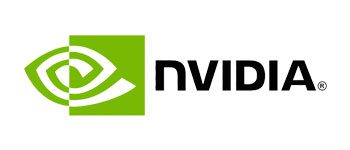
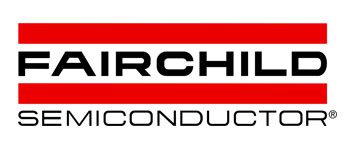
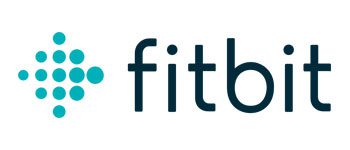
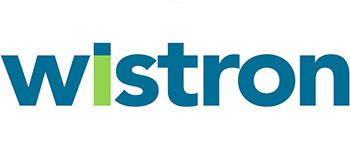
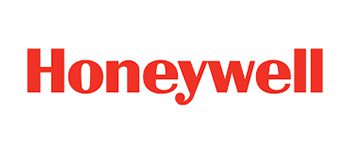
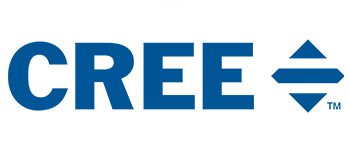
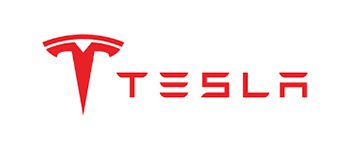
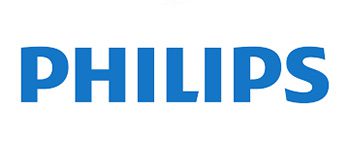
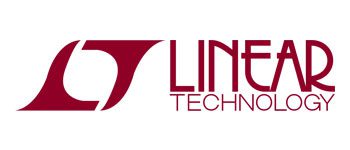
One-stop EMS solution provider
KKPCB is the preferred partner for many global leading enterprises, small and medium-sized businesses, and technology challengers. We help companies increase value through PCB design, PCB manufacturing, PCB assembly, and quality assurance.
We are Trusted
15+ Countries Worldwide
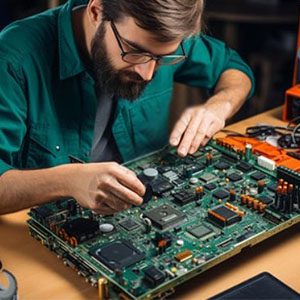
Large Industrial Control Electronics Company
Senior Engineering Expert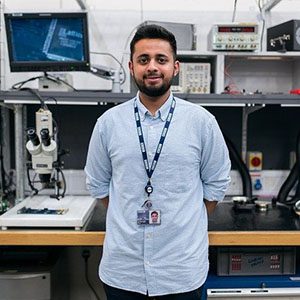
Major First Responder Electronics Manufacturer
BUYER/SPARES MANAGER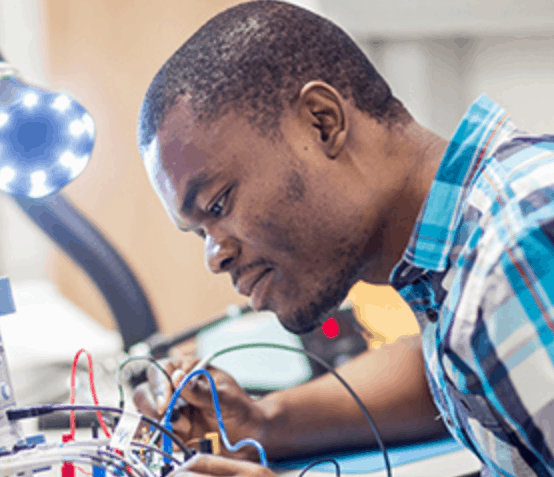
Large Consumer Electronics Company
Purchasing Engineer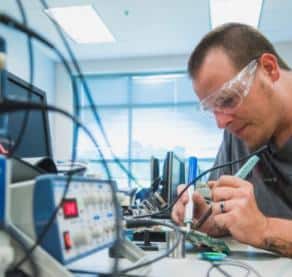
Major Medical Electronics Company
Quality ManagerPCB assembly
Frequent Questions
PCB Assembly is the process of mounting electronic components onto a printed circuit board to create a functional device. It includes component placement, soldering, inspection, testing, cleaning, and packaging. This process ensures that the components are correctly positioned, electrically connected, and the final PCB meets quality and performance standards.
A PCB assembler is responsible for placing and soldering electronic components onto printed circuit boards according to design specifications. This role includes tasks such as component placement, soldering using techniques like SMT or THT, inspecting and testing for defects, cleaning to remove contaminants, and packaging the finished PCBs. The assembler ensures that the PCB functions correctly and meets quality standards, playing a vital role in the production of electronic devices.
To assemble a PCB, start by preparing design files and components, then place the components onto the board either manually or using automated machines. Next, solder the components to establish electrical connections, followed by inspecting for placement accuracy and solder quality. Perform functional testing to ensure proper operation, clean the board to remove contaminants, and finally, package the assembled PCB for shipment or integration. This process ensures that the PCB meets quality and performance standards.
PCB Assembly service is essential because it ensures that electronic devices function correctly by accurately placing and soldering components onto the PCB. It provides quality control through inspection and testing, improves manufacturing efficiency, manages complex designs, and can be more cost-effective than in-house assembly. This service guarantees that PCBs are reliable, meet performance standards, and are produced efficiently, which is crucial for the timely and successful launch of electronic products.
Yes, we typically have a lower limit on PCB Assembly orders to ensure cost-efficiency and operational feasibility. This minimum order quantity helps cover setup costs and ensures that the assembly process is economically viable. The specific lower limit can vary depending on factors such as the complexity of the PCB, component types, and production requirements. For precise information on minimum order quantities, it's best to discuss your project details with us directly.
Our standard specification for PCB Assembly includes precise component placement within ±0.1 mm, high-quality soldering adhering to IPC-A-610 standards, and thorough inspection and testing, such as visual and functional checks. We ensure proper material handling, cleanliness of the PCB, and complete documentation, including assembly drawings and BOM. We use lead-free soldering in compliance with RoHS regulations and can handle both small-scale and large-scale production. These standards ensure that the assembled PCBs meet high performance, quality, and regulatory requirements.
Yes, we do assemble boards fabricated by other vendors. We can handle the assembly of PCBs regardless of the manufacturer, provided we receive the necessary design files, components, and specifications. Our services include placing and soldering components, inspecting for quality, and testing for functionality, ensuring that the assembled board meets the required performance and quality standards.
To reduce PCB assembly costs, focus on optimizing design to simplify the board and minimize component count, selecting cost-effective standard components, and improving layout efficiency. Utilize automation for precision and speed, increase production volumes for economies of scale, and implement lean manufacturing principles to reduce waste. Negotiate with suppliers for better terms, conduct thorough prototype testing to avoid costly revisions, and choose a cost-effective assembly service provider. These strategies collectively lower material, labor, and production costs while ensuring quality and efficiency.
When choosing a PCB assembler, consider their experience and expertise, adherence to quality standards, and range of services offered. Ensure they use up-to-date technology, can meet your lead times, and offer competitive pricing. Research their reputation through references or reviews, and assess their communication and customer support. These factors will help ensure you select a reliable assembler that meets your project requirements effectively.
We follow several key PCB assembly standards to ensure quality and reliability, including IPC-A-610 for soldering and assembly workmanship, IPC-J-STD-001 for soldering practices, IPC-2221 for PCB design requirements, and ISO 9001 for quality management. Additionally, we adhere to RoHS compliance to limit hazardous materials, IPC-7711/7721 for rework and repair, and IPC-7351 for land pattern design. These standards collectively ensure high-quality assemblies and regulatory compliance.
To inquiry about printed circuit board assembly, fill up the PCB assembly quote form with required details and submit it. We will get back to you as soon as possible. You can also send your PCB assembly requirements via email at [email protected] or call us at +86-13823765993.
Yes, we provide partial turnkey PCB assembly services, which means we can manage specific parts of the assembly process, such as component procurement, PCB fabrication, component placement, soldering, testing, inspection, and packaging, while allowing clients to handle other aspects. This flexible approach enables us to work collaboratively with clients to meet their specific needs and optimize the assembly process accordingly.
The cost of custom PCB assembly varies based on factors such as design complexity, component type and quantity, production volume, assembly process, testing and quality assurance requirements, and lead time. For an accurate quote, provide detailed project information, including design files and specifications, to receive a precise cost estimate tailored to your specific needs.
Handling BGA (Ball Grid Array) components requires specific attention to ensure proper assembly and functionality. Key requirements include precise PCB design with adequate pad sizes, accurate soldering using techniques like reflow soldering, effective thermal management, advanced inspection methods such as X-ray to check solder joints, proper handling and storage to avoid damage, and accurate placement using automated machines. These practices are essential to ensure reliable connections, prevent overheating, and maintain overall component integrity.
The estimated price for PCB assembly varies based on factors such as PCB complexity, component type and quantity, assembly volume, PCB size and thickness, and testing requirements. Larger production runs typically lower the per-unit cost, while specialized components, expedited services, and high testing standards can increase costs. For an accurate quote, detailed project information, including design files and production requirements, is necessary.
If you encounter problems with PCB assemblies, document the issues and contact the supplier with detailed information. Request an investigation to identify the root cause, seek a resolution such as rework or replacement, and provide feedback to improve future products. Follow up to ensure the issues are resolved satisfactorily. This process helps address problems effectively and ensures quality in subsequent assemblies.
We ensure the quality of our PCB assembly services by adhering to industry standards, conducting rigorous inspections and functional testing, sourcing high-quality components, and maintaining strict process controls. If you are not satisfied with the PCB assemblies, document the issues and contact us with detailed information. We will work with you to resolve the problems, which may include reworking, replacing, or issuing a refund. Follow up to ensure the resolution meets your satisfaction and provide feedback to help improve our services.