Optimized Article: Multilayer FR4 PCB Substrate Material and Ceramic PCB Comparison
FR4, often written as FR-4, is a widely recognized and high-performing substrate material used in PCB manufacturing. Its affordability, insulation properties, and structural integrity make it the foundation for most PCB designs. FR4 boards are coated with copper foil using adhesive to create conductive layers, either single or double-sided, depending on the design. This flexibility allows for the development of complex multilayer PCBs, making FR4 the default choice for many applications.
Ceramic vs. FR4 PCB: Key Differences and Applications
Ceramic PCBs
Ceramic materials, including aluminum oxide, aluminum nitride, and beryllium oxide, are vital in industries requiring robust and high-speed PCBs. These boards excel in harsh environments, such as aerospace and heavy industrial applications, due to their excellent thermal and mechanical properties.
Thermal Conductivity
One of the primary differences between FR4 and ceramic PCBs is thermal conductivity.
- FR4: Low thermal conductivity, requiring additional structures like thermal vias or cooling mechanisms to manage heat.
- Ceramics: High thermal conductivity minimizes hotspots and ensures consistent heat transfer, reducing the need for external cooling components.
Thermal Expansion and Reliability
FR4 boards face challenges like via fractures during thermal cycling due to mismatched coefficients of thermal expansion between copper and FR4. In contrast, ceramic boards experience less stress due to better alignment of expansion rates, resulting in higher reliability, especially in multilayer designs.
Electrical and Mechanical Strength
While ceramics resist electrical conduction slightly, their low electrical conductivity makes them suitable for PCB substrates. Their superior mechanical strength and lower deformation under stress make ceramic boards ideal for applications with strong vibrations or shocks.
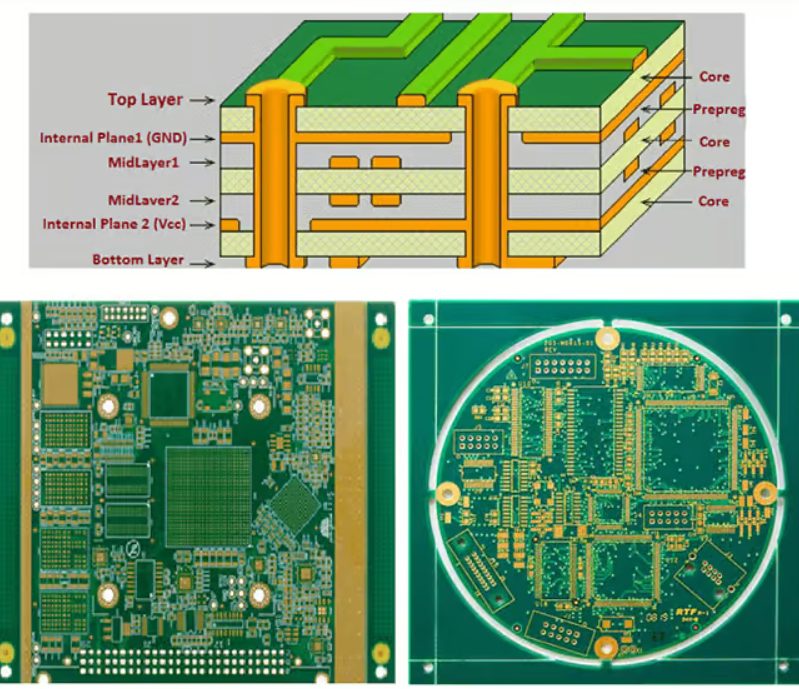
Advantages of Multilayer FR4 PCBs
Customizable Thickness
The thickness of multilayer FR4 PCBs is a critical design parameter. Common thicknesses range from 0.1 to 3 inches, depending on the project requirements.
Factors Affecting FR4 Thickness:
- Space Constraints: Compact FR4 boards are ideal for small devices like Bluetooth accessories and USB connectors.
- Edge Connectivity: The thickness must match edge connector specifications to ensure a snug fit and avoid damage.
- Impedance Matching: Thickness affects insulator width, capacitance, and inductance, crucial for high-frequency applications like RF/microwave designs.
Manufacturing Process: FR4 vs. Ceramic Multilayer PCBs
FR4 Multilayer PCB Manufacturing
FR4 boards are fabricated using copper foil, heat, and adhesive. For thermal management, metal layers and active cooling systems are integrated.
Ceramic Multilayer PCB Manufacturing
Ceramic PCBs use conductive pastes, such as silver or gold, applied through screen printing. Layers are baked at temperatures below 1000°C, enabling high-density connections and analog component integration within inner layers.
Conclusion
The choice between FR4 and ceramic PCBs depends on application requirements. FR4 is cost-effective and versatile, while ceramics offer superior thermal, electrical, and mechanical performance for demanding environments. Designers must weigh factors like thermal demands, mechanical stress, and impedance requirements when selecting the appropriate material for their PCB projects.