Comparing Ceramic Substrate Cutting Technologies: Laser Cutting vs. Waterjet Cutting
With the widespread adoption of new energy vehicles, more people are recognizing the excellent performance of ceramic substrates, and the demand for these materials is steadily increasing. Compared to traditional fiberglass boards, ceramic substrates offer superior mechanical strength, high-temperature resistance, and excellent thermal conductivity. In addition, ceramic substrates also exhibit excellent dimensional and chemical stability. However, they come with certain drawbacks, including high costs, processing difficulties, and substantial interface stress between the conductive layer and the substrate. Therefore, selecting the appropriate cutting method during the processing of ceramic substrates is crucial to ensuring product quality and performance.The commonly used cutting methods for ceramic substrates are laser cutting and waterjet cutting. Each method has its own advantages and disadvantages, as outlined below:
Laser Cutting
Laser cutting uses a focused, high-power density laser beam to irradiate the workpiece, causing the material to rapidly melt, vaporize, or ablate. A high-speed airflow, coaxial with the beam, blows away the molten material, achieving the cutting process. Laser cutting is a thermal cutting method.
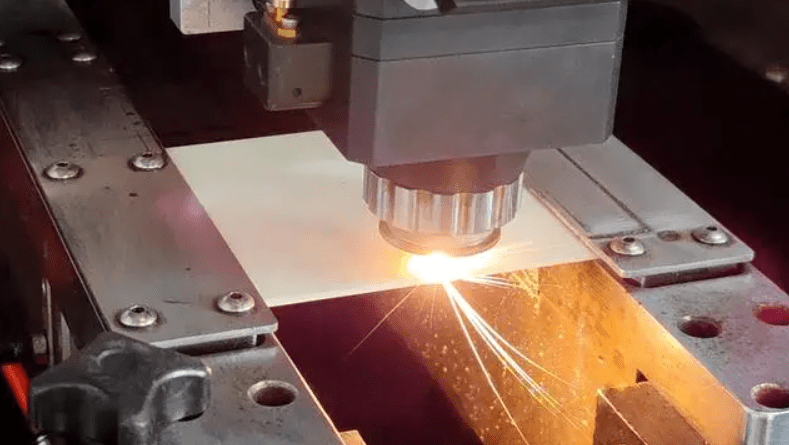
Advantages:
- Fast cutting speed, high efficiency, and suitable for automated operations.
- High cutting precision, smooth edges, and no burrs.
- Capable of cutting a wide range of materials, including metals, non-metals, and composite materials.
- No contact with the workpiece surface, avoiding mechanical deformation or damage.
- Low cleanliness requirements during cutting, generating minimal waste.
Disadvantages:
- High cutting costs, expensive equipment, and high operating and maintenance expenses.
- Being a thermal cutting process, it creates a heat-affected zone (HAZ) on the material, potentially altering or degrading material properties.
- Cutting performance may be poor on certain materials (such as aluminum, copper) or thick materials, potentially leading to cracking, oxidation, discoloration, or blackening.
- Light pollution and metal vapor emissions may be generated.
Waterjet Cutting
Waterjet cutting uses a high-speed rotating blade to remove material, achieving cutting through a combination of water and abrasive particles. The blade has a certain thickness, so the cutting line width is wider. Deionized water is used to cool the blade and remove ceramic debris after cutting.
Advantages:
- Lower cutting cost, small equipment investment, and low operating and maintenance costs.
- Cold cutting method that avoids the creation of a heat-affected zone, preserving the original properties of the material.
- No material or thickness restrictions; capable of cutting almost any material with thicknesses up to 300mm.
- No harmful substances or pollutants are produced, making the process environmentally friendly.
Disadvantages:
- Slower cutting speed and lower efficiency compared to laser cutting.
- Lower cutting precision, with rougher edges and possible burr formation.
- Requires large amounts of water and abrasives, generating waste and requiring cleanup.
- Grinding waste may contain toxic substances and requires special disposal.
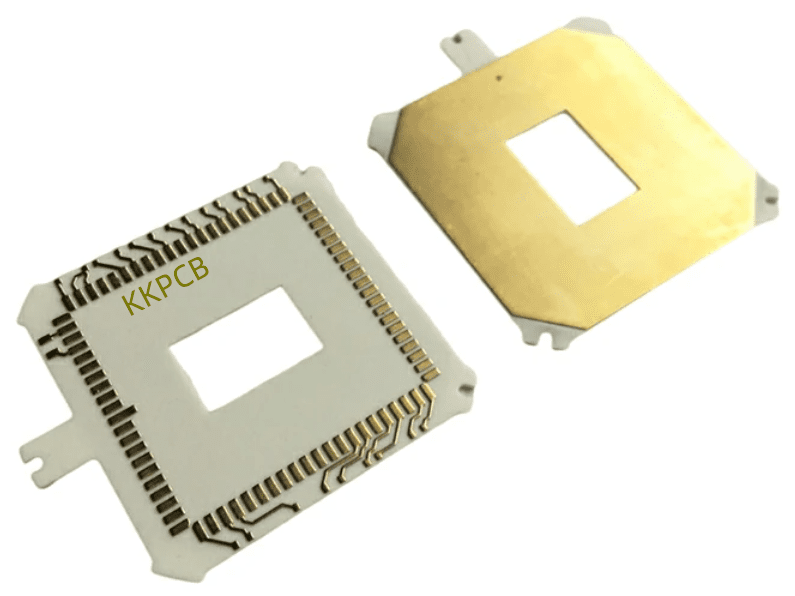
Conclusion
In summary, both laser cutting and waterjet cutting have their advantages, and the choice between the two should be made based on product design requirements, budget, material properties, and performance needs. Generally, if high cutting speed, precision, and smoothness are required, and the material can tolerate some heat-affected zone, laser cutting is a good choice. If cutting costs, environmental considerations, and preserving material properties are more important, especially for thicker or difficult-to-cut materials, waterjet cutting is a better option.