Annular Ring in PCB: Key Considerations for Design and Manufacturing
The annular ring is a critical aspect of printed circuit board (PCB) design and manufacturing. It plays a vital role in ensuring the electrical conductivity and mechanical reliability of vias, which connect different PCB layers. Understanding what constitutes a good or bad annular ring and adhering to IPC standards is essential for achieving optimal PCB performance.
What is an Annular Ring?
An annular ring refers to the area of copper that surrounds the drilled hole (via) in a PCB. In multi-layer PCBs, vias are essential for connecting various layers. The annular ring ensures strong electrical conductivity between these layers, as it provides the necessary copper coverage around the hole.
Good vs. Bad Annular Rings
To achieve a good annular ring, the drill hole must be perfectly centered within the copper pad, ensuring complete copper coverage. Deviations can result in poor connectivity or board failure.
Types of Annular Rings
- Good Annular Ring
- The hole is precisely centered in the copper pad.
- Ensures strong and reliable electrical connections.
- Tangent Annular Ring
- The hole is slightly offset, with the outer edge touching the pad’s edge.
- May still function but poses a higher risk of electrical failures.
- Breakout Annular Ring
- The hole partially overlaps the pad’s edge, leaving some copper missing.
- Leads to unreliable connections and potential short circuits.
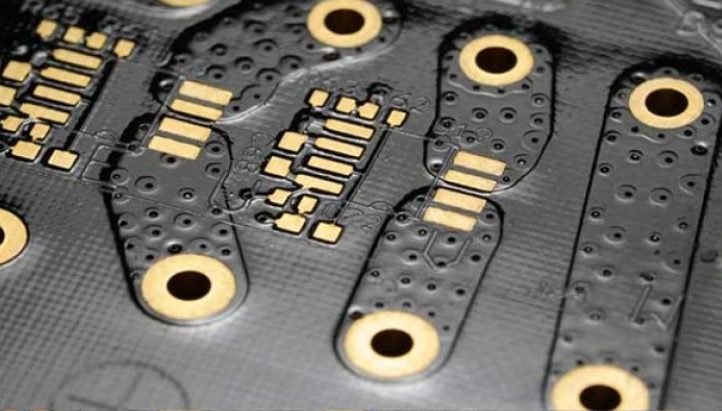
IPC Standards for Annular Rings
The IPC (Association for Connecting Electronics Industries) defines specific standards for PCB manufacturing, including annular ring dimensions. These standards are categorized into three classes based on the application and reliability requirements.
Class 1: Basic Standards
- Applications: Low-cost and low-complexity boards.
- Annular Ring Size: Minimum 1–2 mil.
- Tolerances: Allows tangency and even breakout due to minimal inspection requirements.
- Use Case: Consumer electronics with less stringent reliability needs.
Class 2: Standard Quality
- Applications: Most common for general-purpose electronics.
- Annular Ring Size: Minimum 3–5 mil.
- Tolerances: Accepts tangency but not breakout.
- Use Case: RF boards, high-density interconnects (HDI), and moderate-reliability applications.
Class 3: High Precision and Reliability
- Applications: Critical industries like medical, aerospace, and military.
- Annular Ring Size: Minimum 3–10 mil.
- Tolerances: No tangency or breakout allowed.
- Requirements:
- Use of high-Tg materials.
- Precise manufacturing processes adhering to IPC-6012 and IPC-A-610 standards.
- Special considerations for specific industries, e.g., IPC-6012 ES for aerospace.
- Use Case: Long-term reliability in harsh environments.
Why Annular Ring Standards Matter
The reliability of vias depends on maintaining adequate annular ring dimensions. Poorly designed or manufactured annular rings can lead to:
- Electrical Failures: Breakouts can disrupt current flow, leading to intermittent or complete failure.
- Mechanical Weakness: Insufficient copper coverage compromises the board’s durability.
- Short Circuits: Exposed or misaligned vias can cause shorts.
By adhering to IPC standards, manufacturers ensure the long-term functionality and reliability of PCBs across various applications.
The annular ring is a cornerstone of PCB design, directly impacting the board’s performance and durability. Whether producing basic consumer electronics or mission-critical aerospace systems, understanding the differences between IPC Class 1, Class 2, and Class 3 standards is crucial.
For high-reliability applications, investing in precise Class 3 boards with larger annular rings ensures long-term performance and justifies the higher manufacturing cost. By following IPC standards and focusing on good annular ring design, manufacturers can deliver PCBs that meet the demands of today’s increasingly complex technologies.