Infrared Thermal Imaging in the Electronics Industry: Optimizing Thermal Management and Enhancing Performance
With the continuous development of electronic components, thermal management in modern electronic products has become increasingly important. Especially in highly integrated and miniaturized electronic devices, ensuring that circuit boards and components operate within the proper temperature range is a critical task for enhancing product performance and reliability. Infrared thermal imaging technology, as a non-contact temperature measurement tool, has been widely applied in the design, validation, fault diagnosis, and thermal management processes of electronic products. This article will explore the basic principles, advantages, and applications of infrared thermal imaging in the electronics industry, specifically how it helps optimize thermal management and improve product performance.
What is Infrared Thermal Imaging?
Infrared thermal imaging technology is based on the principle of infrared radiation, where all objects emit infrared energy proportional to their temperature. Thermal cameras use two-dimensional detectors to capture this infrared radiation, which is then converted into electrical signals and displayed as thermal images. These thermal images show areas with different temperatures, helping us visually observe the heat distribution of circuits or components.
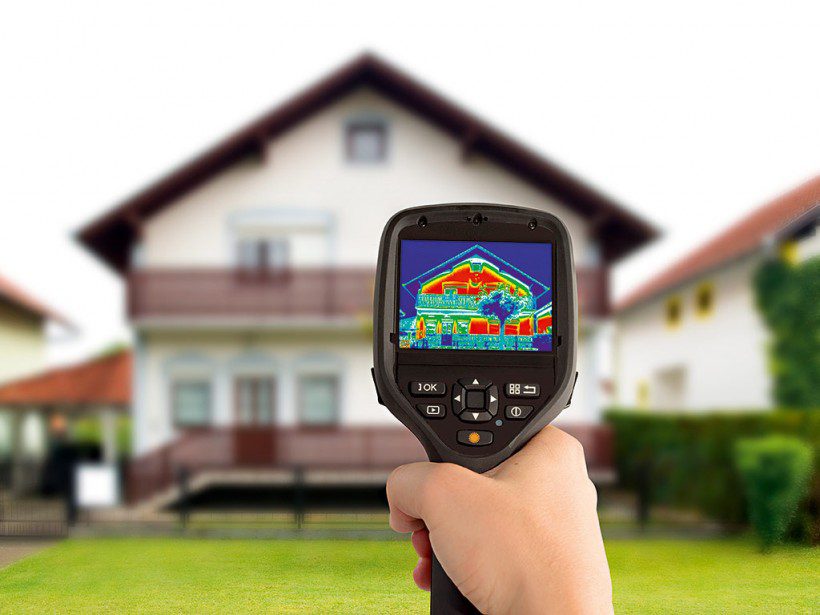
Two Major Advantages of Infrared Thermal Imaging
- Non-contact Temperature Measurement: Unlike traditional contact-based temperature measurement methods, thermal imaging technology does not require direct contact with the circuit or component. This prevents any temperature change or interference caused by direct contact. It allows for real-time monitoring without affecting the normal operation of the product.
- Wide-area Monitoring: Thermal imaging can simultaneously monitor the temperature of an entire circuit board or multiple components, as opposed to traditional temperature sensors that only measure temperature at a single point. This provides a global view, making it an indispensable tool for assessing the thermal performance of complex circuits or systems.
Applications of Thermal Imaging in the Electronics Industry
As the functionality and miniaturization of electronic products increase, thermal management becomes more complex. Many electronic components, such as resistors, capacitors, and transistors, consume power and generate heat when in operation. If heat cannot be effectively dissipated, overheating may occur, affecting the performance and reliability of the circuit. Therefore, thermal imaging technology plays a critical role in the following stages:
1. Design Phase
During the design phase, thermal imaging helps engineers identify potential thermal issues early on. For example, by analyzing the thermal patterns of components on the circuit, engineers can optimize designs to avoid problems like uneven current distribution or improper thermal resistance that may lead to overheating. Identifying these issues early reduces the need for costly corrections later in the process.
2. Validation Phase
In the validation phase, thermal imaging technology is used to check if the circuit board and components are free from overheating, ensuring the design meets thermal management requirements. If a component’s temperature is too high, thermal imaging helps engineers quickly locate the problem and take corrective actions, such as optimizing the cooling system or adjusting the circuit layout.
3. Fault Diagnosis Phase
During the actual operation of the product, thermal imaging technology provides continuous monitoring of the temperature distribution on the circuit board. It can help engineers quickly identify hot spots and potential faults. For example, if an area’s temperature rises abnormally, it may indicate a component failure. Thermal imaging can pinpoint the issue, minimizing downtime and preventing more severe damage.
Thermal Imaging Optimizing Thermal Management: Case Studies
Case 1: Discovering Thermal Issues in the Design Phase
A resistor manufacturer used thermal imaging technology during the design phase to test the thermal pattern of its resistors. They discovered that one of the resistors had uneven heat distribution. Upon further analysis, engineers found that the right side of the resistor was significantly hotter than the left side, indicating uneven current distribution. By using thermal imaging, the manufacturer was able to adjust the design early, preventing this issue from causing failures during later production.
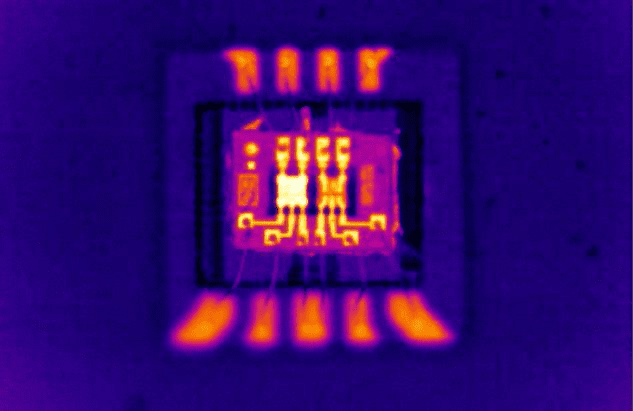
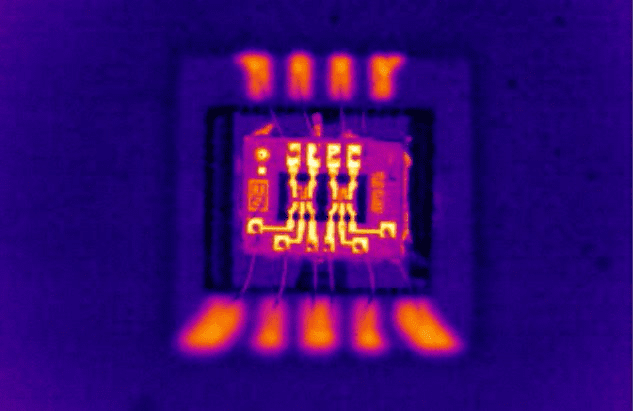
Case 2: Overheating Issues Found in the Validation Phase
A sensor company used thermal imaging technology to inspect its sensor circuit boards during the validation phase. They found that a power control chip had a hot spot, with temperatures reaching 85°C—much higher than other components. Thermal imaging helped engineers identify that this issue was caused by excessive current. As a result, they optimized the heat dissipation design, preventing overheating and ensuring the product’s normal operation.
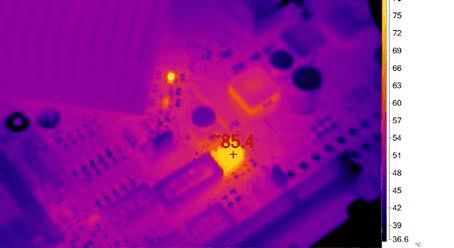
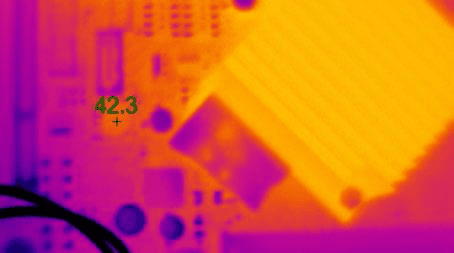
Conclusion
Infrared thermal imaging technology not only helps identify potential thermal issues in the design phase but also provides real-time monitoring and fault diagnosis during product validation and operation. This technology allows engineers to visualize the temperature distribution of circuits, optimize thermal management designs, and prevent overheating from compromising performance or causing component failures, thereby enhancing the overall quality and reliability of electronic products.
As the demand for effective thermal management in electronic devices continues to increase, thermal imaging technology will play an even more significant role in future product development. Whether in the design, validation, production, or fault diagnosis stages, thermal imaging will remain a crucial tool for improving product performance, reliability, and safety.