Industrial PCB Production
In the modern industrial system, printed circuit boards (PCBs) are the cornerstone of electronic products. From simple household appliances to complex aerospace equipment, PCBs are everywhere, assuming functions such as connection, support, and integrated circuits. With the advent of Industry 4.0, the mass production of PCBs not only needs to meet demand in terms of quantity, but also needs to integrate new trends such as intelligence, automation, and informatization.
Industrial PCB Production Process
Industrial PCB production is a complex and delicate process that usually includes the following main steps:
PCB Design
The first step in the PCB manufacturing process is PCB design. PCB design is created by professional designers using PCB design software such as Altium. This PCB design is the blueprint for the actual finished product.
PCB design is usually completed by the customer, and then the design file is sent to the PCB manufacturer for production. The most widely used PCB design file format is the Gerber format. The Gerber file format is an open vector image file format and is the de facto industry standard.
Inspection and DFM Review
After the manufacturer receives the PCB design file, the engineer will conduct a second process inspection. The inspection process includes a DFM (Design for Manufacturability) review. During this process, trace width, trace spacing, hole size, and other design parameters are verified. This is done to ensure that the design is error-free and meets the company’s manufacturing capabilities.
After the design is verified, multiple instances of the same design are combined and manufactured on a single large panel. This reduces cost and complexity and enables faster production.
Cleaning and Cutting
After the design verification and inspection is completed, the large PCB board is thoroughly dry cleaned to remove contaminants that may interfere with the manufacturing process or the quality of the PCB. The board pieces are then cut into smaller PCB boards suitable for manufacturing. The cutting and cleaning of the PCB boards are done using specialized machines.
Drilling
After the larger PCB board is cut into smaller panels, the next process step is to drill holes in these boards. Drilling serves two purposes. The first purpose of drilling is to place through-hole components on the board. The second purpose of drilling is to create connections between the various copper layers of the PCB.
During the drilling process, the operator takes a piece of MDF (Medium Density Fiberboard) and fixes the PCB panel on the MDF board. Aluminum sheets are also attached to the board as entry foils, which enables burr-free drilling.
Once the board is prepared, it is fed into a computer-controlled machine that automatically drills holes in the PCB board according to a program. After the drilling process is completed, the sharp edges of the board are smoothed with a grinder.
Electroplating
The different copper layers on the PCB board are isolated from each other by layers of non-conductive materials such as fiberglass. Therefore, in order to create connections between the isolated copper layers, an electroplating process is required.
During the electroplating process, the panel is immersed in an electrolyte. The copper on the panel acts as a cathode. A variety of chemicals are used in this process. The entire process is controlled by a computer and a thin layer of copper is deposited in the drilled holes.
Printing
In this process step, a film with a printed circuit diagram is placed above the PCB panel. The panel is then fed into a printer along with a UV lamp. The printer prints the circuit design on the film onto the PCB panel.
After the pattern is printed on the panel, the panel is treated with a chemical developer to remove unhardened residues.
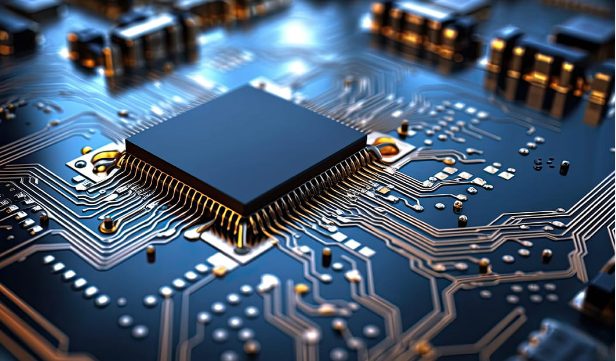
Etching
The next process step in PCB manufacturing is etching. The purpose of this process is to remove unwanted copper on the circuit board using an alkaline agent. After the copper is removed, the board is cleaned to remove all chemicals.
Automated Optical Inspection
After etching, the panel is inspected and scrutinized using an automated optical inspection machine. The purpose of this inspection is to ensure quality standards to detect any errors that may have occurred in the previous process. The machine uses computer vision technology to scan the PCB panel and detect faults.
Solder Mask
The next process is called solder masking. In this process, both sides of the PCB board are coated with an epoxy solder mask. The solder mask protects the copper surface and prevents solder shorts between components. After the solder mask is applied, the PCB board is dried and baked to firmly fix the solder mask.
Surface Finish
To prevent the pad copper from oxidation, the surface finish uses hot air solder leveling. Other surface finish methods include HASL, immersion gold, hard gold, and OSP.
Electrical Testing
This is one of the last few process steps during which all connections on the board are electrically tested as per the original board design. This automated testing method ensures that all connections are as per the original design and there are no open or short circuits on the PCB.
Milling
This is the last process, which involves separating all the individual PCBs from the large panel. This process is performed by a CNC milling machine. After cutting, the circuit boards are washed, cleaned and dried again. Now, the PCBs are vacuum sealed and wrapped with bubbles to prevent dust and moisture. These PCBs can now be shipped to customers after proper packaging.
Key technologies for industrial PCB production
- Multilayer board technology
As the functions of electronic products become increasingly complex, the requirements for PCB wiring density and number of layers are getting higher and higher. Multilayer board technology effectively improves the integration and performance of PCBs by stacking multiple conductive layers on the substrate and connecting the layers through vias. - High-density interconnect (HDI) technology
HDI technology uses processes such as micro blind holes and buried holes to further reduce the line width and line spacing of PCBs, improve wiring density and signal transmission speed, and is suitable for the needs of high-end electronic products. - Rigid-flex technology
Rigid-flex combines rigid PCBs with flexible PCBs. It has both the stability and support of rigid boards and the bendability and adaptability of flexible boards. It has a wide range of applications in portable electronic devices, automotive electronics and other fields. - Lead-free process
For environmental protection and health considerations, lead-free process has gradually become the mainstream in PCB production. Lead-free welding requires higher welding temperature and stricter process control to ensure welding quality and reliability.
Development trend of industrial PCB production
- Smaller, thinner and lighter
With the trend of miniaturization and portability of electronic products, PCB is also developing in the direction of miniaturization, thinness and lightweight, which puts higher requirements on the accuracy of production process and the performance of materials. - Higher integration and performance
With the rapid development of technologies such as 5G communication, artificial intelligence, and the Internet of Things, the performance requirements for PCB signal transmission speed, frequency response, and anti-interference ability are constantly increasing, which promotes the continuous innovation and upgrading of PCB technology. - Green and environmental protection
Increasingly stringent environmental regulations have forced PCB manufacturers to adopt more environmentally friendly materials and processes, reduce the emission of harmful substances, and achieve sustainable development. - Intelligent manufacturing
With the advent of the Industrial 4.0 era, PCB production has gradually moved towards intelligent manufacturing. By introducing automation equipment, big data analysis and artificial intelligence technology, production process optimization, real-time quality monitoring, predictive maintenance, etc. are achieved.
Summary
As an important part of the electronic manufacturing industry, the continuous progress and innovation of industrial PCB production technology plays a vital role in promoting the development of the electronic information industry. With the continuous development of science and technology and the continuous changes in market demand, PCB manufacturers need to continuously improve their technical level and innovation capabilities to adapt to the development trend of the industry and make greater contributions to the prosperity of the global electronic information industry.