Industrial PCB Assembly; Delivering Reliability and Precision!
Industrial PCB Assembly
KKPCB has become a one-stop shop when it comes to high-quality industrial PCB assembly. With over 10 years of experience in manufacturing and assembling a wide range of PCBs, KKPCB is a trusted choice for many customers. With the latest technology, equipped with a team of experts and industry best practices, we ensure that we develop cutting-edge industrial printed circuit board assembly that is ahead of the times.
Among our other products, we specialize in providing industrial PCB assemblies that require high reliability and precision. Since electronic devices used in industrial applications need to be very stable and suitable for use in harsh conditions, industrial printed circuit boards also need to follow strict standards to thrive in industrial environments. In addition, industrial PCBs also need to be resistant to extreme temperatures, moisture and dust, shock, vibration, etc. We are able to provide solutions for a wide range of industrial applications, from sensing systems and monitors to heavy equipment and home appliances. We have the ability to provide low, medium and high volume PCB assembly, box assembly, cable and harness assembly, complete turnkey assembly and more solutions for industrial applications.
We offer everything from single-layer PCBs to multi-layer PCBs, depending on the complexity of the circuit. Different industrial applications also require rigid, flexible or rigid-flex PCBs. You can count on us to provide custom PCBs that meet your customized needs.
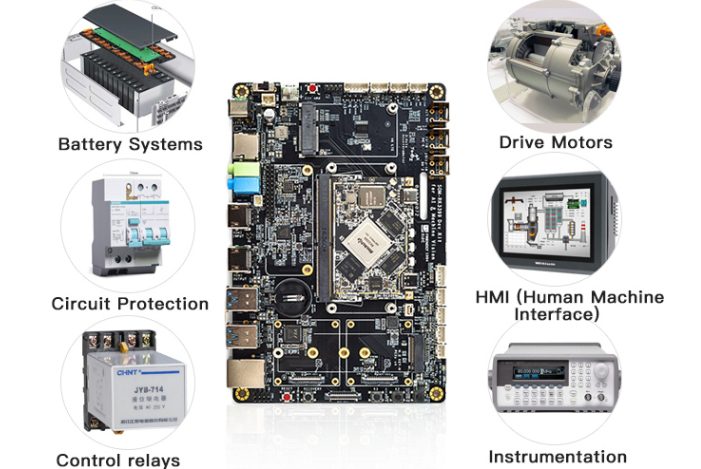
Industrial PCB Manufacturing Process
The industrial PCB manufacturing process involves the following steps:
PCB Design and Layout – This is one of the most critical stages in the entire manufacturing process. A successful design supports the functionality of the device, so full attention needs to be paid to this stage. Of course, PCB design is influenced by the exact requirements of the industrial application and the environment in which it needs to work. It is also influenced by the nature of the user as well as access to resources.
Prototyping – Having a fully functional PCB prototype can go a long way in reducing the chances of any costly mistakes at a later stage. Prototypes ensure that both functionality and features are tested. It is worth spending more time and investment on prototypes because once the prototype is in place, you can proceed with assembly.
Industrial PCB Assembly – This is the stage where the necessary components are etched on the board as per the design. The steps in this process include:
Solder Paste Stencil Printing – This step involves applying solder paste to the board. Using a stencil allows the assembler to apply solder paste only to certain parts of the PCB. Using an applicator, solder paste is applied to the target area in precise amounts.
Pick and place – Next, a pick and place machine places the surface mount components on the PCB. The components are then soldered to the surface of the board.
Reflow soldering – This process involves moving the PCB board onto a conveyor, which passes through a large reflow oven. This, in turn, melts the solder paste. Next, the PCB passes through a cooler, which allows the melted solder to solidify. This connects the surface mount components to the PCB. For double-sided PCB assembly, stencil printing, placement, and reflow are first performed on the side with fewer and smaller parts, followed by stencil printing on the other side.
Inspection and quality control Once the surface mount components are soldered, the assembled boards need to be tested for functionality. Common inspection methods include:
Manual inspection: This method is particularly useful for low-volume production because on-site visual inspection can be performed. However, this method becomes impractical when the number of boards increases.
Optical inspection: This method is suitable for high-volume production. AOI machines use an array of high-powered cameras to inspect the PCB. Different quality solder connections reflect light in different ways, allowing the AOI to detect low quality solder.

X-ray Inspection: This method is used for complex or layered PCBs. It allows the observer to see through the layers to identify any potential problems.
Through-hole component insertion – In addition to surface mount components, the board can contain other components. In this case, plated through holes are inserted through the entire board. Instead of solder paste, manual through-hole insertion is used. Wave soldering can also be performed, where once the plated through-hole components are in place, a conveyor passes through a specialized oven and a wave of molten solder washes through.
Final Inspection and Functional Testing – This step tests the functionality of the PCB. It simulates the environment in which the PCB will operate.
The main differences between industrial and commercial PCB manufacturing processes are as follows:
Industrial PCB manufacturing requirements are generally of Class 2 or Class 3, while commercial PCBs are of Class 1 or Class 2.
In terms of material quality, industrial PCBs usually use high Tg materials, while commercial PCBs usually use standard FR4 materials.
Industrial PCBs may need to balance heavy copper and normal copper weight, while commercial PCBs may not.
For industrial PCBs, consistent temperature distribution is critical to ensure uniform flow of PCBA solder.
Industrial PCBs require moisture protection, while commercial PCBs may not.