Advanced Insights into IoT’s Impact on PCB Design and Manufacturing
Introduction
As IoT technology advances, so do the requirements for Printed Circuit Board (PCB) design and manufacturing. This blog extends the discussion on how IoT is driving innovations in PCB design, exploring deeper insights into new design techniques, material advancements, manufacturing challenges, and future prospects.
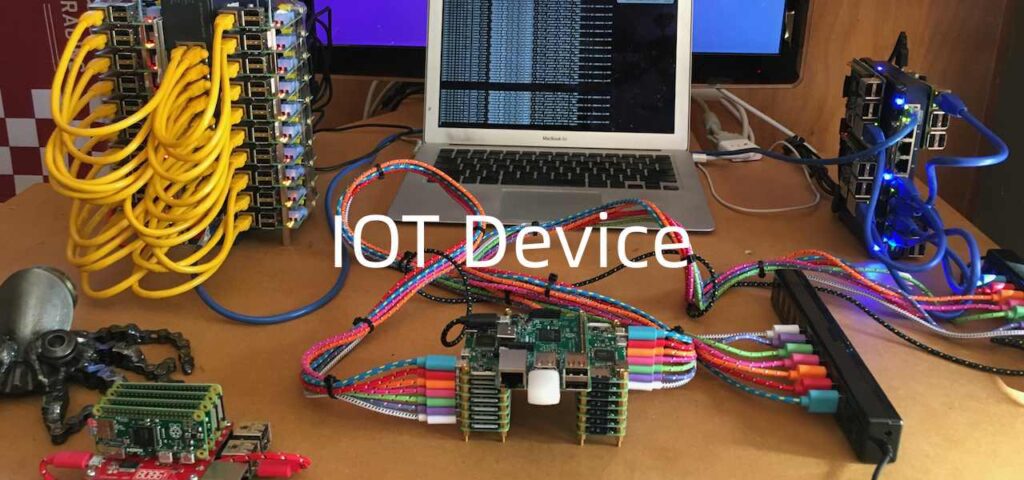
Advanced Design Strategies for IoT-Enabled PCBs
- Design for Manufacturability (DFM) and Assembly (DFA)
- Simplification of Complex Designs: As IoT devices become more sophisticated, ensuring that designs are simple and manufacturable is essential. Techniques like panelization and design rule checks (DRC) reduce errors and manufacturing costs.
- Component Placement and Trace Routing: Compact IoT devices necessitate highly strategic component placement and precise routing. Advanced CAD tools use AI-driven optimization to ensure efficient layouts with minimal crosstalk.
- IoT-Specific Design Considerations
- Thermal Management: The miniaturization of IoT devices increases heat density. Incorporating thermal vias, heat sinks, and thermally conductive materials helps dissipate heat effectively.
- EMI/EMC Compliance: IoT devices must comply with strict electromagnetic interference (EMI) and electromagnetic compatibility (EMC) regulations. Designers employ shielding techniques, grounding strategies, and optimized trace layouts to ensure compliance.
- Signal Integrity and High-Speed Design: With high-speed data transfers in IoT applications, signal integrity becomes crucial. Designers use simulation tools to analyze and correct signal degradation issues, ensuring stable device communication.
- Embedded Components and System-in-Package (SiP) Integration
- On-Board Components: Embedding passive components (like resistors and capacitors) directly into PCB layers reduces space, weight, and production costs.
- System-in-Package (SiP) Solutions: SiP technology integrates multiple ICs and passive components into a single package, enabling higher functionality within a smaller form factor, crucial for wearable and portable IoT devices.
- Design for Flexibility and Adaptability
- Modular Design Approaches: Modular PCBs allow for easier upgrades and repairs, reducing electronic waste. This approach is gaining traction in consumer IoT devices, such as smart home hubs.
- Flexible and Rigid-Flex PCBs: Wearable IoT devices demand flexibility, achieved through rigid-flex PCBs that combine the durability of rigid boards with the adaptability of flex circuits.
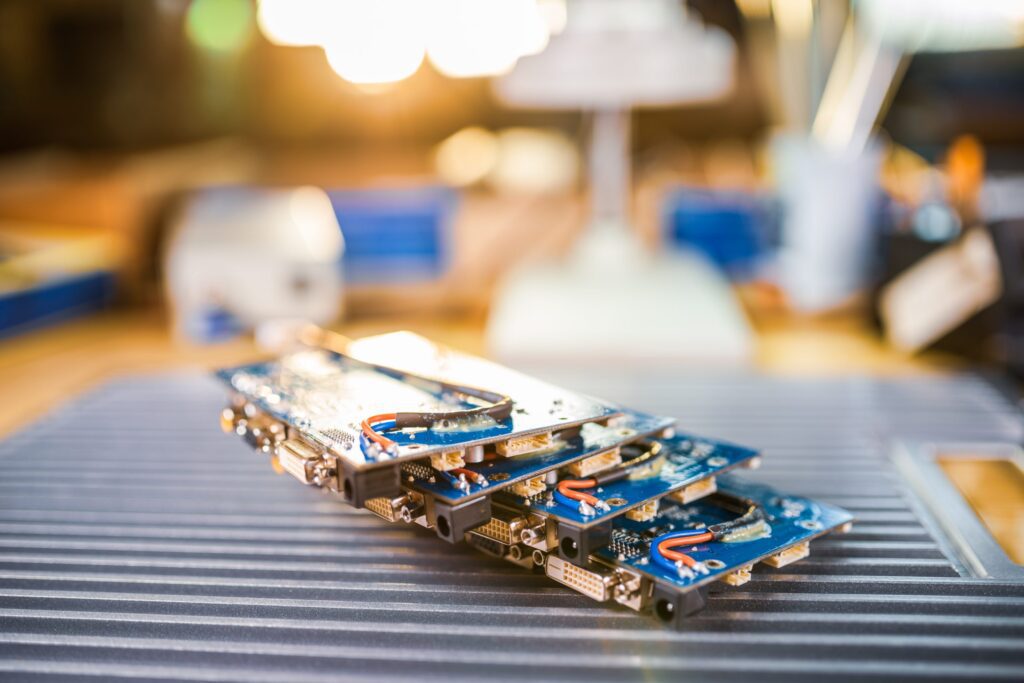
New Material Innovations for IoT PCBs
- Advanced Substrate Materials
- Low-Dielectric Materials: Materials with low dielectric constants support high-frequency communication, a requirement for 5G-enabled IoT devices.
- Flexible Polymers: Polyimide and liquid crystal polymer (LCP) are commonly used for flexible PCBs, ensuring durability and stability in challenging environments.
- Environmentally Sustainable Materials
- Eco-Friendly Laminates: With increasing focus on sustainability, manufacturers are shifting to halogen-free and lead-free laminates.
- Biodegradable PCB Materials: Emerging research explores biodegradable PCBs that reduce electronic waste, aligning with global sustainability goals.
- Conductive Inks and Additive Manufacturing
- 3D Printing of PCBs: Additive manufacturing enables the direct printing of conductive traces onto flexible substrates, reducing production time and waste.
- Conductive Polymer Inks: These inks are used to print circuits on flexible substrates, supporting the production of ultra-thin and lightweight IoT devices.
Advanced Manufacturing Techniques for IoT PCBs
- Automation and Smart Factories
- Industry 4.0 Integration: IoT-enabled smart factories employ sensors, data analytics, and AI-driven decision-making to optimize production and predict maintenance needs.
- Robotic Process Automation (RPA): Robots perform tasks such as soldering, pick-and-place assembly, and quality inspection with unparalleled speed and accuracy.
- Precision Drilling and Laser Technology
- Microvias and Blind/Buried Vias: The rise of high-density interconnect (HDI) PCBs requires precision laser drilling to create smaller and more efficient vias.
- Laser Direct Structuring (LDS): LDS enables the direct formation of 3D circuit paths on complex surfaces, allowing IoT devices to have PCBs that conform to non-traditional shapes.
- Real-Time Quality Control and Defect Detection
- Inline Automated Optical Inspection (AOI): AOI systems use cameras and AI to detect flaws in real time, minimizing production defects.
- X-Ray Inspection: This technique is vital for multilayer PCBs, as it allows non-destructive inspection of hidden solder joints and internal layers.
Future Trends in IoT and PCB Design
- Integration with 6G and Ultra-Wideband (UWB) Technologies
- High-Frequency PCBs: As 6G networks become a reality, PCBs will require materials and designs that support ultra-high frequencies with minimal loss.
- Advanced Antenna Integration: IoT devices that leverage UWB for precise location tracking will require embedded antennas with improved sensitivity and performance.
- Wearable and Biocompatible PCB Design
- Skin-Mountable Sensors: Future wearables will require ultra-thin, stretchable PCBs that can be worn directly on the skin for health monitoring.
- Biocompatible Materials: Research is being conducted into PCBs that can be safely implanted in the human body, opening new frontiers in medical IoT.
- AI-Driven Design and Customization
- AI-Assisted PCB Layout: AI-driven design software predicts optimal trace routing, via placement, and component arrangements, significantly reducing design time.
- Customizable Consumer Electronics: Consumers will demand personalized IoT devices, and PCB manufacturers will leverage AI and agile manufacturing to meet these expectations.
- Sustainable Manufacturing and Circular Economy
- Closed-Loop Recycling: IoT PCBs are being designed for disassembly, enabling the recovery of valuable materials at the end of a device’s life.
- Green Factories: As environmental regulations tighten, factories will adopt clean energy, smart waste management, and energy-efficient production lines.
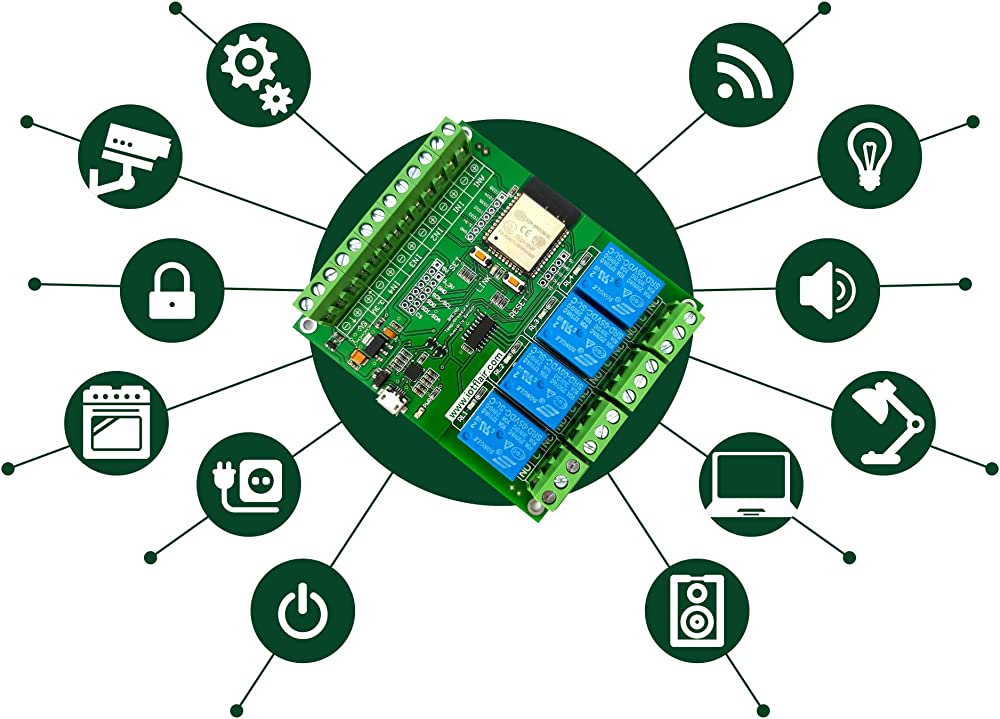
Conclusion
The rapid evolution of IoT continues to push the boundaries of PCB design and manufacturing. Advanced design techniques, material innovations, and manufacturing processes are enabling the creation of smaller, more powerful, and more sustainable IoT devices. As the industry moves towards 6G connectivity, wearables, and circular economy initiatives, IoT PCBs will play a pivotal role in driving technological progress.