The Impact of IoT on PCB Design and Manufacturing
Introduction
The Internet of Things (IoT) is revolutionizing industries worldwide, and its influence on Printed Circuit Board (PCB) design and manufacturing is profound. As IoT devices become more compact, efficient, and interconnected, the demand for innovative PCB designs has surged. This blog delves into how IoT is transforming PCB design and manufacturing, the challenges it poses, and the opportunities it presents.
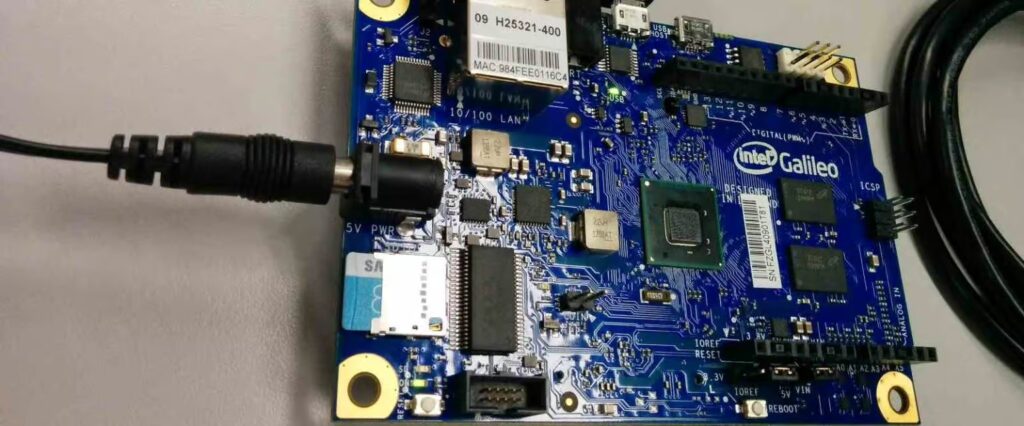
Key Changes in PCB Design Due to IoT
- Miniaturization and Compact Design
- Smaller Footprint: IoT devices like wearables, smart sensors, and health monitoring gadgets require compact PCBs with minimal space utilization.
- Multi-layered Boards: To maximize functionality in limited space, designers are adopting multi-layered PCBs, allowing more components to be integrated into smaller areas.
- Increased Flexibility and Durability
- Flexible PCBs: IoT devices often have unconventional shapes and use cases, such as wearables that need to conform to the human body. Flexible PCBs, which can bend and twist, have become essential.
- Robust Material Selection: With IoT devices being exposed to various environmental conditions, the materials used in PCBs must endure extreme temperatures, moisture, and mechanical stress.
- Enhanced Connectivity and Wireless Capabilities
- RF and Antenna Integration: Many IoT devices rely on wireless communication (Wi-Fi, Bluetooth, Zigbee), necessitating PCBs with integrated antennas and optimized RF design.
- Signal Integrity: Ensuring seamless communication between devices requires PCBs to support high-speed data transfer with minimal interference.
- Power Efficiency and Low Energy Consumption
- Energy Harvesting: IoT devices, especially those operating in remote locations, need to consume minimal power. PCB designers are now integrating energy-harvesting circuits directly onto the boards.
- Low-Power ICs: Designers must select components and ICs (Integrated Circuits) that operate on ultra-low power while still providing optimal performance.
- High-Density Interconnect (HDI) PCBs
- Fine Pitch Components: IoT devices require smaller components and tighter trace routing, which has driven the adoption of HDI PCBs.
- Microvias: These tiny holes allow for better routing between PCB layers, enabling more compact and efficient designs.
Manufacturing Challenges and Innovations
- Precision and Complexity
- Advanced Fabrication Methods: Traditional PCB manufacturing processes are being upgraded to handle smaller vias, tighter tolerances, and higher aspect ratios.
- Automation and AI Integration: The use of AI and machine learning in production helps detect defects, optimize manufacturing processes, and improve overall efficiency.
- Material and Cost Considerations
- Specialized Materials: IoT PCBs require specialized substrates, such as polyimide for flexible PCBs or ceramic for high-temperature applications.
- Cost Control: As IoT devices become more affordable, PCB manufacturers face pressure to reduce production costs while maintaining high quality.
- Sustainability and Eco-Friendly Manufacturing
- Green Materials: Eco-friendly and recyclable materials are being used to meet regulatory and consumer demands for sustainable products.
- Waste Reduction: Advanced manufacturing techniques, such as additive manufacturing (3D printing of PCBs), are minimizing material waste.
- Increased Quality Control and Testing
- Automated Testing Equipment (ATE): Automated testing tools ensure that PCBs meet stringent quality standards.
- Real-Time Monitoring: IoT-enabled smart factories use sensors and data analytics to monitor the health of production lines and detect issues in real-time.
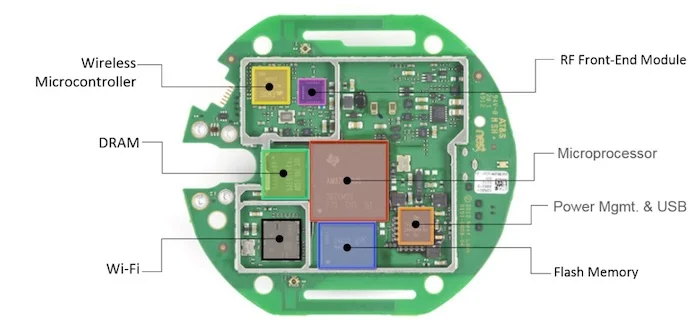
Future Trends in IoT and PCB Design
- Wearable and Implantable Devices
- The healthcare sector is driving demand for ultra-small, biocompatible PCBs for wearables and medical implants.
- 5G and Edge Computing
- The rollout of 5G networks is driving demand for high-frequency PCBs that can support ultra-fast data transfer rates and low-latency connections.
- Sustainable Manufacturing Practices
- The push for sustainability is expected to grow, leading to wider adoption of green materials and energy-efficient manufacturing processes.
- Increased Use of AI and Predictive Analytics
- AI-driven PCB design software will enable faster prototyping, smarter design recommendations, and more efficient manufacturing processes.
Conclusion
The rise of IoT has significantly reshaped PCB design and manufacturing, requiring smaller, smarter, and more energy-efficient PCBs. While these changes present challenges, they also create opportunities for PCB manufacturers to innovate. As IoT adoption continues to grow, the demand for advanced PCB solutions will rise, driving further advancements in technology, design, and production methods.