Why EMC Compliance important in Motor Control PCB Design
Ensuring Electromagnetic Compatibility (EMC) compliance in motor control PCBs is essential to avoid interference issues, maintain system reliability, and ensure regulatory approval for market access. Here’s a breakdown of why EMC compliance matters and how to achieve it.
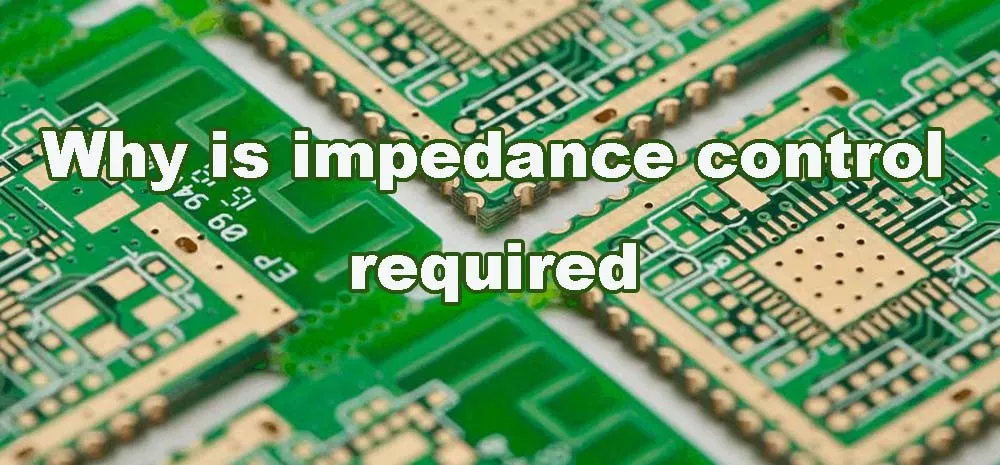
1. Why is EMC Compliance Important?
- Ensures Reliable Operation
Without proper EMC measures, Electromagnetic Interference (EMI) can disrupt nearby electronic devices, causing system malfunctions, signal errors, and even damage to components. EMC compliance ensures that motor control PCBs work as intended without external disturbances. - Prevents Device Malfunctions
EMI can introduce noise into sensitive control circuits, affecting signal integrity. This noise could cause motor control systems to behave erratically, leading to unwanted stops, slowdowns, or unpredictable movements. Ensuring EMC compliance prevents such disruptions. - Meets Regulatory Standards
Many countries have strict EMC standards (like FCC in the USA or CE in Europe) for electronic products. Non-compliance can result in fines, product recalls, or a ban on product sales in specific regions. - Boosts Product Compatibility and Market Access
EMC-compliant PCBs can be marketed globally, ensuring interoperability with other devices. This is crucial for products in industrial, medical, and consumer electronics sectors, where devices must coexist without interference.
2. Key EMI Sources in Motor Control PCBs
EMI can come from multiple components in motor control systems. Here are the most common sources of interference:
- Power Regulators
Voltage regulators, especially Switch-Mode Power Supplies (SMPS), are a primary source of EMI. Their fast-switching actions cause high-frequency noise, which can travel through PCB traces and impact nearby components. - Transmitters
Wireless communication modules used in remote motor control may generate EMI, especially if proper shielding isn’t applied. High-frequency signals from transmitters and receivers can couple with nearby circuits. - Analog Amplifiers
Analog amplifiers amplify small signals, but high-gain operation can make them more susceptible to noise. EMI from these amplifiers can couple into other sensitive areas of the PCB. - Switching Power Supplies
The rapid switching of power components (like MOSFETs and IGBTs) generates high-frequency noise. Their fast on-off switching creates strong electromagnetic fields, which can couple to nearby components. - Digital Circuits
Microcontrollers (MCUs), DSPs, and FPGAs generate high-frequency signals due to fast clocking. These clocks and high-speed data buses produce harmonics that can propagate through the PCB.
3. How to Reduce EMI in Motor Control PCBs
To achieve EMC compliance, designers must address the layout, grounding, and shielding of the PCB. Here are the key layout features that impact EMI control:
- PCB Size and Layer Stackup
- Multilayer PCBs reduce EMI by allowing for dedicated power and ground planes.
- A 4-layer PCB (with power and ground planes) provides better signal integrity and reduces emissions compared to a 2-layer PCB.
- Smaller PCBs may have less parasitic capacitance and inductance, helping to reduce noise.
- Grounding Topology
- Use a dedicated ground plane to ensure a low-impedance return path for signals.
- Apply star grounding instead of daisy-chained ground paths to avoid ground loops.
- Implement via stitching (placing multiple vias along the ground plane) to reduce impedance and create better ground connections.
- Signal Routing and Trace Layout
- Minimize loop areas of high-current paths to reduce magnetic field emissions.
- Keep high-speed traces as short as possible and avoid sharp bends.
- Route high-speed signals as differential pairs to reduce common-mode noise.
- Use controlled impedance routing for high-frequency signals.
- Component Placement
- Place noise-generating components (like switching regulators) away from sensitive analog and RF circuits.
- Keep the power section (MOSFETs, IGBTs) isolated from the control section (MCUs, sensors) on the PCB.
- Position decoupling capacitors close to power pins to filter noise.
- Shielding and Enclosures
- Use metal cans or grounded shields over sensitive circuits, such as wireless modules and amplifiers.
- Employ conductive coatings or metallic enclosures to block EMI from leaving or entering the PCB.
4. How to Minimize Ground Impedance in Motor Control PCBs
Low-impedance ground paths are critical for reducing EMI. Here are best practices for reducing ground impedance:
- Dedicated Ground Planes
- Use a full copper plane (not traces) to connect all ground points.
- Avoid cutting or fragmenting the ground plane with unnecessary slots or holes.
- Short, Direct Ground Paths
- Keep ground paths as short and direct as possible.
- Use wide ground traces or planes to handle high current without resistance issues.
- Via Stitching
- Place multiple ground vias around power components, ICs, and connectors.
- Multiple vias reduce the effective impedance and increase return path density.
- Ground-Signal Separation
- Separate analog and digital grounds to avoid cross-interference. Use ferrite beads or filters where digital and analog grounds meet.
- For mixed-signal PCBs, use a split ground plane for isolation but connect them at a single point to avoid ground loops.
- Connection Optimization
- Use multiple ground points for components like decoupling capacitors, connectors, and mounting holes.
- Solder components directly to the ground plane (especially large power components) for low-resistance connections.
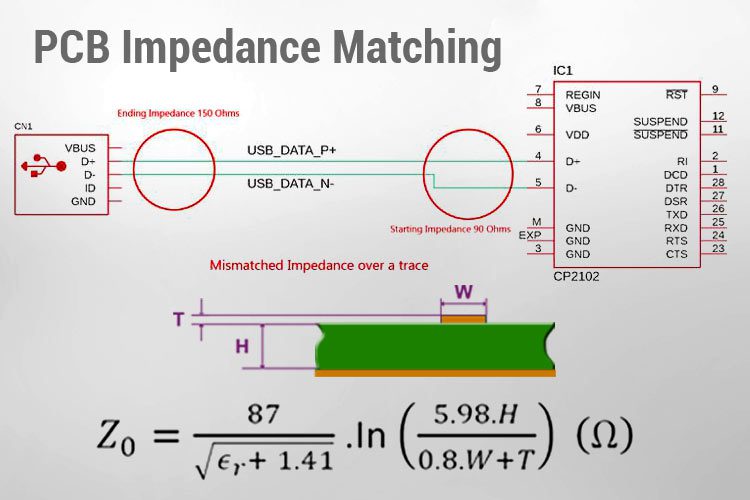
5. Applications of Motor Control PCBs
Motor control PCBs are used in a variety of industries and devices. Here are some key applications:
- Consumer Electronics
- Appliances: Fans, air conditioners, vacuum cleaners, kitchen appliances (blenders, mixers, etc.).
- Motor control PCBs regulate speed, torque, and efficiency, improving the user experience.
- Robotics
- Industrial robots, medical robots, and research robots rely on precise motor control to achieve smooth, accurate movements.
- Motor control PCBs enable precise motion control for robot arms, joints, and actuators.
- Manufacturing Equipment
- CNC machines, conveyor belts, and production lines depend on PCBs to control the movement and speed of motors.
- Accurate control ensures smooth and efficient production.
- Automotive
- Power steering, electric pumps, HVAC blowers, and windshield wipers rely on motor control PCBs.
- These PCBs enable smart energy usage, efficient power delivery, and enhanced vehicle performance.
- Electric Vehicles (EVs)
- Electric motors, battery management systems, and regenerative braking use motor control PCBs.
- They manage the speed, torque, and braking of electric motors, optimizing driving range and performance.
- Military Systems
- Unmanned Aerial Vehicles (UAVs), ground vehicles, and naval vessels rely on motor control PCBs to power propulsion systems, weapon systems, and surveillance equipment.
- The ability to operate in harsh environments with low EMI is essential for mission success.
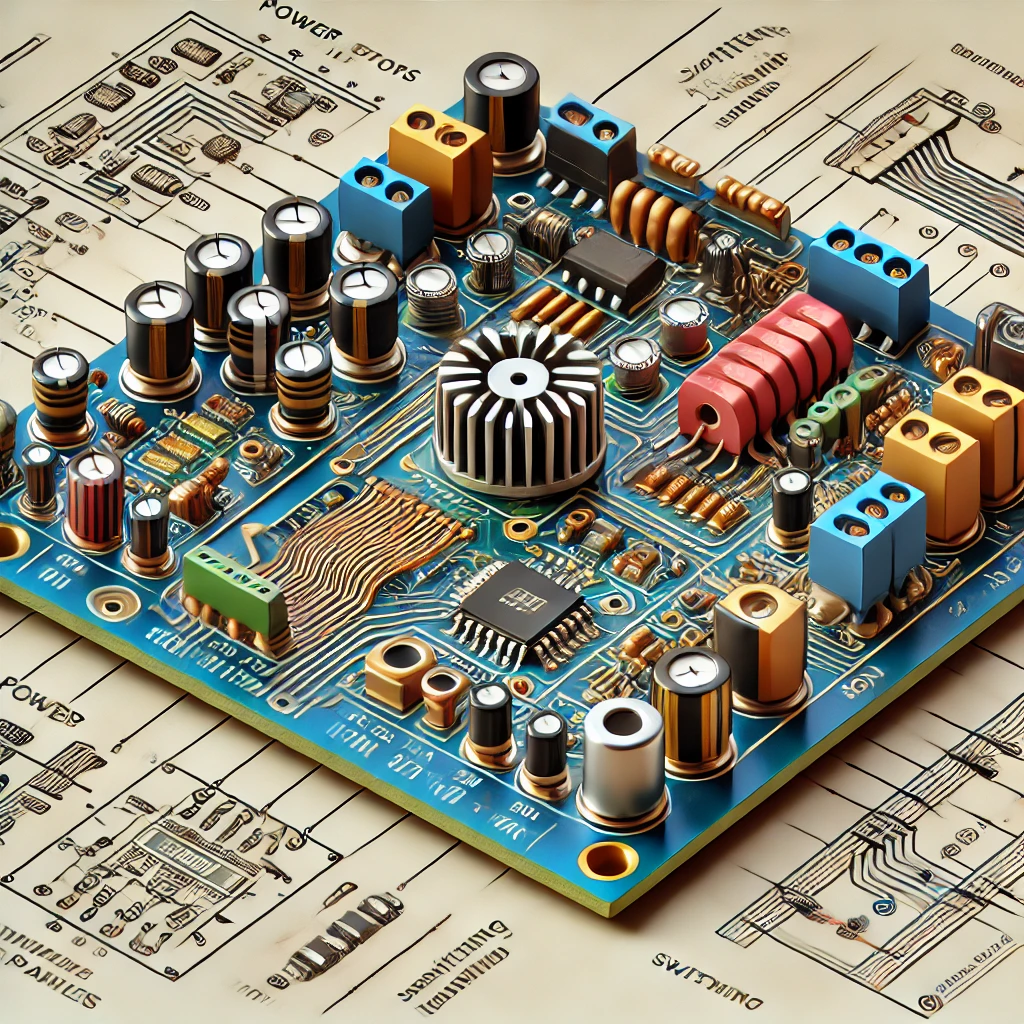
Summary
EMC compliance in motor control PCBs is crucial for system reliability, performance, and regulatory approval. By addressing EMI sources like power supplies, amplifiers, and digital circuits, designers can optimize layout features like grounding, signal routing, and shielding. Effective strategies to reduce ground impedance—like using ground planes, via stitching, and separate analog/digital grounds—help ensure smooth motor control and compliance with industry standards. Finally, motor control PCBs are used in consumer electronics, robotics, automotive, EVs, and military systems, playing a vital role in modern technological advancements.