How to Remove Flux from PCB?
Manufacturers use flux to solder components on PCBs. Depending on the PCB components, flux also varies and is used to fix them on the board. It ensures uninterrupted and strong electrical connections between devices. However, it is crucial to remove excess flux so as not to blur signal traces or damage connections. In this article, we have introduced various methods and basic steps to remove flux from PCBs. So, let’s get started.
Types of Flux from PCB
Manufacturers use flux to chemically solder components on PCBs. It is good for fixing components, but excessive use is like a chronic poison for PCBs. Here are three types of flux on PCBs:
- Rosin
Rosin flux is a pine extract that contains a lot of resin. This flux is divided into different types. For example, rosin flux is suitable for soldering on clean circuit boards without leaving any residue, thus ensuring cleanliness. RMA flux can also wet the circuit board before soldering, thus cleaning the circuit board. RA is an active flux that leaves excessive residue.
- No-clean flux
These fluxes allow manufacturers to use them with confidence without worrying about post-use cleaning. Compared to other fluxes, it does not require more cleaning. It ensures that the circuit board is dry after soldering by absorbing residues and acids. However, it usually contaminates the PCB. So, it is best to use it with caution.
- Water-soluble flux
This flux contains resins and organic compounds. Water-soluble flux ensures better performance under all conditions.
Does the flux need to be cleaned during PCB soldering?
During the PCB soldering process, a lot of solder slag may appear on the PCB board. This is because the flux (solder paste) is generally not completely volatilized during the soldering process and will remain on the board. Do these residues need to be removed?
To comprehensively consider various factors such as the quality of the selected flux, product requirements, and production costs, before knowing whether it needs to be removed, we must first understand two concepts: cleaning and no-cleaning.
No-clean flux in the PCB industry means that there is no need to clean after wave soldering, and it will not cause electrical performance problems. It does not mean that there is no residue after soldering.
In addition, no-clean flux cannot allow residues to accumulate together, so it is easy to produce white residues, such as lead oxide or bromide, which are the reaction products of flux and solder.
If you are doing PCBA services and customers must remove the residues on the PCBA, then cleaning must be done during the PCBA process.
If there is conductivity and white residue after cleaning, it is caused by cleanliness. Cleaning flux can generally be divided into two categories: manual cleaning and ultrasonic cleaning.
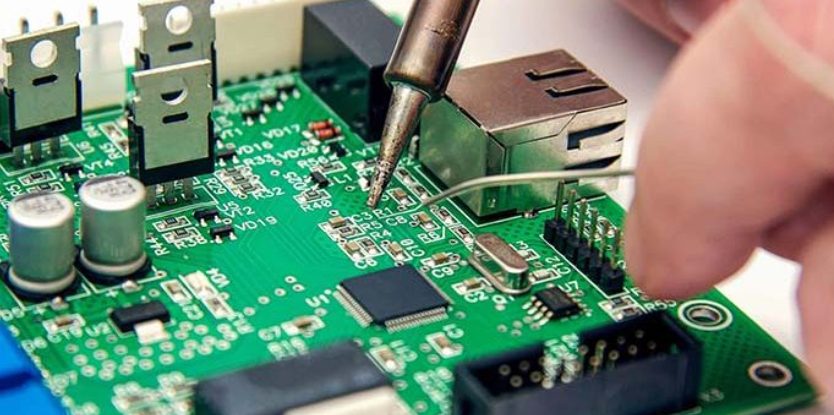
Methods for removing flux from printed circuit boards
Manual cleaning:
Use manual tools to remove residual flux and dirt from solder joints. Manual cleaning is suitable for all types of solder joints.
Advantages and disadvantages:
Simple and easy, good cleaning effect, but low efficiency.
Common manual cleaning tools include brushes, tweezers, cotton yarn, etc. The following items need to be prepared for cleaning:
Do not damage solder joints and components. Clean gently, do not twist and pull the wires on the solder joints or the leads of the components.
The cleaning fluid should not be scattered, do not use excessive cleaning fluid to prevent the cleaning fluid from scattering inside the product and reducing product performance.
When the cleaning fluid becomes dirty, it should be replaced in time. Cleaning fluid is usually a flammable chemical, and attention should be paid to fire prevention when using it.
Use daily essential tools at home for cleaning
You can clean the flux with just an old toothbrush. All you need is an old toothbrush, a clean cloth, and isopropyl alcohol or acetone. Dip the brush in the cleaning fluid and brush it on the board to clean the flux. Wipe off the moisture with a rag and let it dry.
Get an acid brush
You can also clean the flux with an acid brush by dipping its bristles in a solvent and brushing it thoroughly on the board. Wipe it off later and let it dry.
Use Poly Clens
You can also use poly clens to brush the flux off the circuit board. It allows you to apply poly clens cleaning solvent directly to the PCB, keep stirring for at least 30 seconds, then rinse it off and wipe the PCB dry before reassembly.
Cleaning steps
Dip:
Dip the tool you are going to use (such as a toothbrush or acid brush) into isopropyl alcohol or acetone. Make sure it is clean. Flick the brush after dipping to remove excess cleaning liquid.
Brush all around:
Brush all corners and edges with a brush, cover it with alcohol or acetone, and remove the flux on the PCB. Brush the board gently to avoid breaking the solder. Repeat the same process until it is completely clean.
Wipe:
Wipe the circuit board with a clean cloth to remove excess liquid. Dip the brush in distilled water for cleaning and let the PCB dry before operation. You can also use canned air or air blow to remove the remaining flux to ensure that the PCB is 100% clean of flux.
Ultrasonic cleaning:
Ultrasonic cleaning is done by using the high-frequency oscillation of ultrasound to produce ultrasonic cleaning, and there are ultrasonic cleaners.
The principle of ultrasonic cleaning is that under the action of ultrasound, the cleaning liquid produces a cavitation effect. The high-intensity shock wave generated by the cavitation effect can separate the dirt on the welding points and in the tiny gaps, and accelerate the process of the cleaning liquid dissolving these dirt.
Advantages:
Fast cleaning speed, good cleaning quality, can clean the dirt in complex welding parts and gaps, and easy to realize cleaning automation.
The effect of ultrasonic cleaning is related to many factors, mainly ultrasonic frequency, sound intensity, the nature of the cleaning liquid, temperature, cleaning time, etc.
Flux is an essential step in PCB manufacturing, but anything in excess is not good; the same is true here. After soldering and assembly, remove the remaining flux and place the components on a clean, transparent circuit board. In addition, there are many types of flux. Therefore, it is very important to use the flux that suits you and your needs.