How to Choose the Right Material for Flexible LED PCB
What is a Flexible LED PCB?
Printed Circuit Boards (PCBs) are the backbone of electronic devices, connecting components seamlessly for reliable functionality. Among these, Flexible LED PCBs have gained prominence due to their adaptability, reduced size, and cost-effectiveness compared to rigid PCBs. They are widely used across industries like consumer electronics, automotive, and aerospace. Flexible LED PCBs can bend and adapt to complex shapes, providing enhanced design freedom while offering excellent thermal management and resistance to vibration and mechanical strain. These features make them a robust choice for applications requiring reliable connections and long service life.
Importance of Flexible PCBs in LED Strips
Flexible PCBs are crucial in modern LED strips, which incorporate surface-mount components like SMD LEDs. These boards efficiently dissipate heat and provide the flexibility needed for diverse applications. Flexible PCBs for LED strips can be single-layer, double-layer, or multi-layer circuits, offering versatile solutions for various design requirements.
Key Materials in Flexible LED PCBs
Flexible LED PCBs comprise several essential layers, each serving a specific purpose:
- Base Layer:
- Common materials: Fiberglass (FR-4), polyimide, insulated metal substrates.
- Key properties: High rigidity, dielectric constant, and thermal stability.
- Conductive Layer:
- Typical materials: Copper, gold, silver (copper is the most common).
- Purpose: Conducts electricity efficiently across the circuit.
- Solder Mask:
- Material: Thin polymer coating (often green).
- Function: Protects the copper layer and prevents solder bridges.
- Silkscreen Layer:
- Material: Epoxy resin.
- Role: Acts as a reference indicator for component placement.
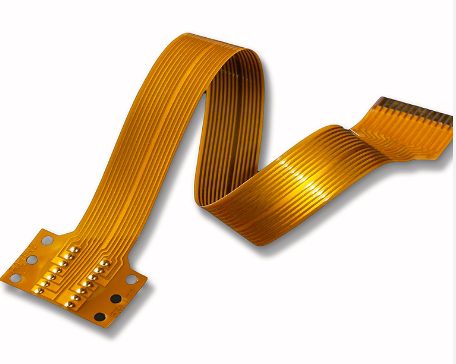
Choosing the Right Material for Flexible LED PCBs
Selecting suitable materials is critical to ensure performance, reliability, and cost-efficiency. Below are key materials and their specific advantages:
1. Film Substrate Material
- Polyimide (PI):
- Excellent thermal resistance and electrostatic properties.
- Tear-resistant with strong moisture retention.
- Adhesives:
- Types: Acrylic, PET, modified epoxy resin, PI resin.
- Benefits: Strong adhesion, essential for flexible copper-clad laminates.
2. Double-layer PI Substrate Materials
- Features lead-free, halogen-free compliance for environmental safety.
- Manufacturing methods: Film coating, lamination, electroplating.
- Advantage: Suitable for high-temperature and double-sided boards.
3. New Copper Foil
- Types: Rolled Annealed (RA) and Electrodeposited (ED) copper foil.
- Applications:
- RA copper: High elasticity for dynamic PCBs.
- ED copper: High-density circuits for static PCBs.
4. Liquid Crystal Polymer (LCP) Substrate
- Advantages:
- Low water absorption and dielectric constant.
- High-frequency compatibility and thermal stability.
- Applications: Ideal for high-performance flexible PCBs.
5. Halogen-free Materials
- Ensures compliance with WEEE and RoHS regulations.
- Reduces environmental impact while maintaining flame resistance.
6. Photosensitive PI Cover Film
- Features: High flexibility, strong bonding, good resolution.
- Applications: Meets high-density PCB standards.
7. Conductive Silver Paste
- Properties: Low resistance and strong adaptability.
- Applications: Suitable for RFID and low-resistance circuits.
Factors to Consider When Selecting PCB Materials
- Electrical Performance:
- Look for low dielectric constant and loss tangent to maintain signal integrity.
- Chemical Resistance:
- Materials must withstand exposure to flux, solvents, and corrosive environments.
- Thermal Performance:
- High thermal conductivity for heat dissipation.
- High glass transition temperature for thermal stability.
- Cost:
- Balance material performance with financial constraints for cost-efficiency.
Flexible LED PCBs are indispensable in modern electronics due to their adaptability, lightweight design, and cost-effectiveness. By selecting the right materials—such as PI substrates, advanced copper foils, and halogen-free components—you can enhance the reliability and performance of these PCBs. Consider factors like electrical performance, thermal stability, and cost to ensure optimal results for your application. With advancements in material science, flexible LED PCBs will continue to play a crucial role in innovative electronic designs.