Optimized Article: How to Assemble Flexible PCBs?
Introduction to Flexible Printed Circuit Boards (Flexible PCBs)
Flexible printed circuit boards (flexible PCBs or flex circuits) are made from flexible insulating materials such as polyimide film. Unlike traditional rigid PCBs, flexible PCBs can bend and twist while maintaining electrical connectivity, making them ideal for space-constrained and dynamic applications.
Key Advantages of Flexible PCBs:
- Bendability and adaptability for compact spaces
- Lightweight and slim profile
- Ideal for high-density interconnect (HDI) designs
- Resistance to vibration and fatigue
- Commonly used in consumer electronics, automotive, aerospace, medical, and industrial equipment
Flexible PCB Assembly Process Overview
The assembly of flexible PCBs involves specialized techniques and equipment to accommodate the unique properties of flexible materials. Below is an overview of the process:
- Design and Manufacturing
- Flexible PCBs are designed using CAD software with considerations for bend radius, layer stacking, impedance control, and component spacing.
- The substrate is fabricated using materials like polyimide or polyester, and layers are bonded to form the PCB.
- Component Placement
- SMT components are mounted using solder paste, reflow soldering, and automated placement systems.
- Through-hole components may require wave soldering, selective soldering, or manual soldering.
- Board Reinforcement
- Stiffeners or temporary support plates are used during assembly to prevent warping and damage.
- Interconnects and Cables
- Wires, connectors, and harnesses are attached via soldering, crimping, or bonding techniques.
- Conformal Coating
- A protective layer is applied to safeguard the assembly from environmental factors.
- Testing and Inspection
- Assembled boards undergo thorough testing, including functional and visual inspections.
- Final Integration
- The completed assembly is integrated into the final product, with additional stress relief measures if needed.
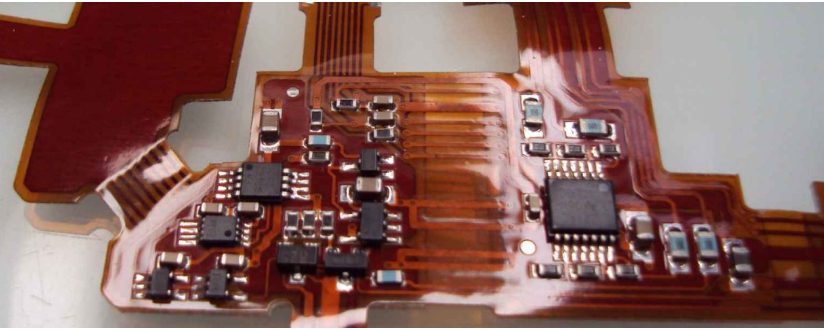
Detailed Steps in Flexible PCB Assembly
1. Design Considerations
- Bend Radius: Avoid sharp folds; define minimum bend radius to prevent cracking.
- Stiffeners: Use rigid sections in critical areas to maintain integrity.
- Impedance Control: Match trace impedance for high-speed signal reliability.
- Layer Stack-up: Optimize the number of conductive and dielectric layers.
2. Flexible PCB Fabrication
- Materials: Polyimide film, coverlay, copper foil, bonding adhesives, and solder masks.
- Processes:
- Printing and etching conductive layers onto flexible substrates
- Layer bonding through heat-press techniques
- Hole drilling and plating for vias
- Electrical testing for continuity
3. SMT Assembly
- Steps:
- Solder Paste Application: Apply solder paste using stencils for precise alignment.
- Component Placement: Use automated pick-and-place machines to position components.
- Reflow Soldering: Heat the board to melt solder paste and secure components.
- Inspection: Conduct automated optical inspection (AOI) to detect misalignments.
- Challenges:
- Warping due to the thin structure of flex boards
- Sensitivity to heat and thermal shock
4. Through-Hole Component Assembly
- Larger components are soldered into plated-through holes using:
- Wave Soldering: For bulk soldering
- Selective Soldering: For specific joints
- Manual Soldering: For detailed or small-scale operations
5. Adhesive Component Attachment
For uneven or specialized areas, components are attached using adhesives such as:
- Screen-printed adhesive paste
- Pre-applied adhesives on components
- Liquid adhesive dispensing
6. Stiffeners and Support Structures
- Types: Removable stiffeners (acrylic or metal) or permanent ones (FR4 or metal plates).
- Methods of Application: Adhesive bonding, clamping, or soldering.
7. Interconnect Attachment
- Techniques:
- Soldering wires directly to PCB pads
- Crimping wires using connectors
- Using anisotropic conductive adhesives or Z-axis elastomers
- Stress Relief: Reinforce connections with heat-shrink tubing or mechanical clamps.
8. Conformal Coating Application
Protective coatings enhance environmental resistance and mechanical durability.
- Coating Materials: Acrylic, silicone, urethane, parylene, epoxy
- Application Methods: Dipping, spraying, or brushing
9. Testing and Inspection
- Types of Testing:
- Visual Inspection: Check for placement errors or defects
- In-Circuit Testing (ICT): Verify electrical continuity
- Functional Testing: Ensure board operation matches design specifications
- X-Ray Inspection: Detect hidden issues, such as voids under BGAs
10. Final Integration
- The flexible PCB is carefully folded, wrapped, or integrated into the final device. Stress relief and secure housings ensure long-term reliability.
Flexible PCB assembly requires precision and specialized processes due to the unique properties of the material. By carefully designing, reinforcing, and inspecting the assembly, manufacturers can produce reliable, high-performance PCBs for modern electronic applications.