HDI PCB
- Home
- HDI PCB
Professional HDI PCB Manufacturing | Prototype, Small Batch, and Mass Production Services
KKPCB provides end-to-end PCB solutions, from design support and rapid prototyping to mass production of HDI, rigid-flex, aluminum, and RF circuit boards. Serving global clients across telecommunications, automotive, industrial, medical, aerospace, and instrumentation sectors, we specialize in solving complex PCB challenges with advanced technologies such as HDI structures (1+N+1, 2+N+2, 3+N+3), embedded/blind vias, and multilayer designs. Utilizing high-TG materials and low Dk/Df dielectrics, we ensure superior performance and reliability. Our manufacturing adheres to IPC-6012 Class 3 standards and holds ISO 9001, IATF 16949, UL, and other international certifications, guaranteeing compliance with industry requirements.
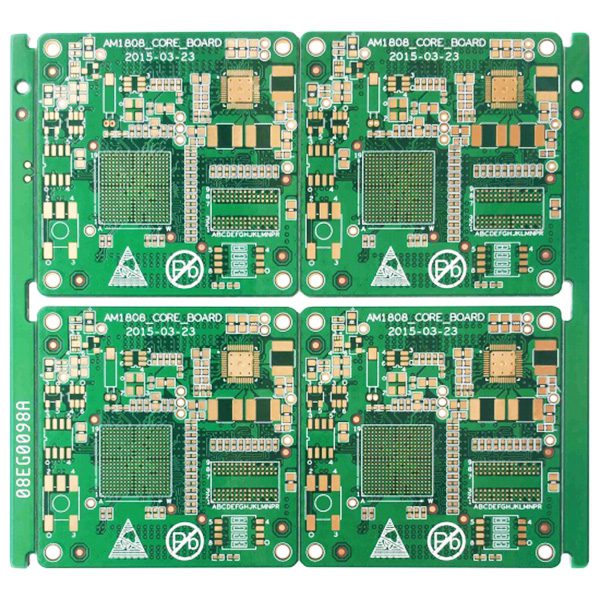
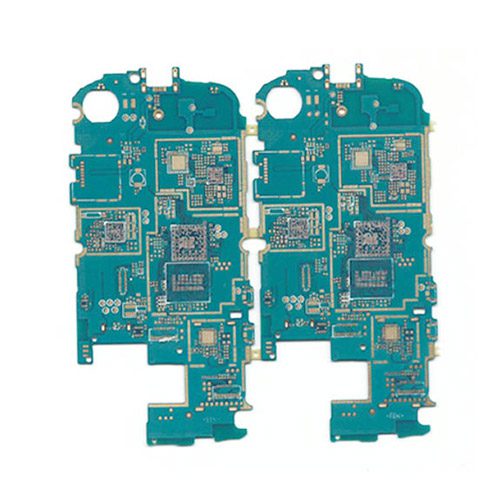
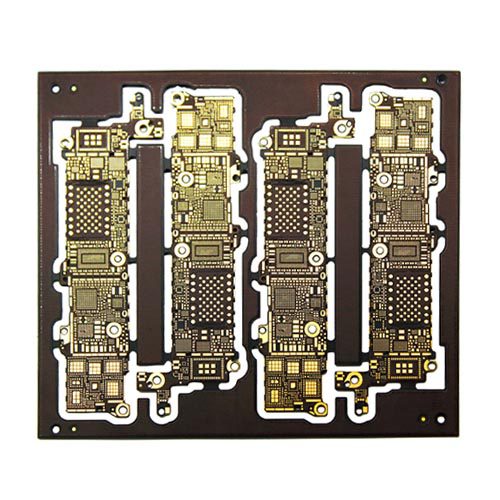
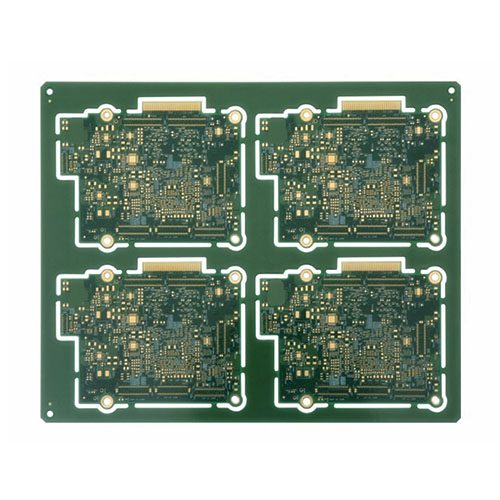
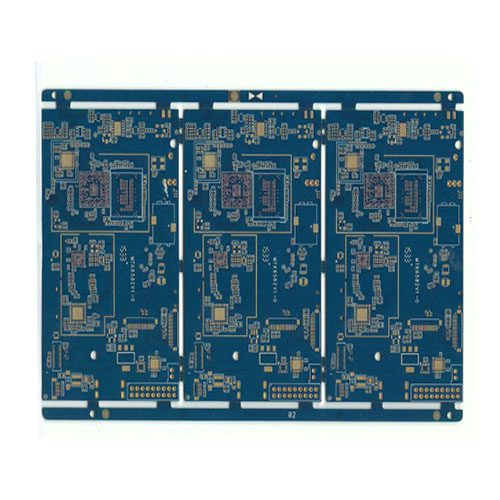
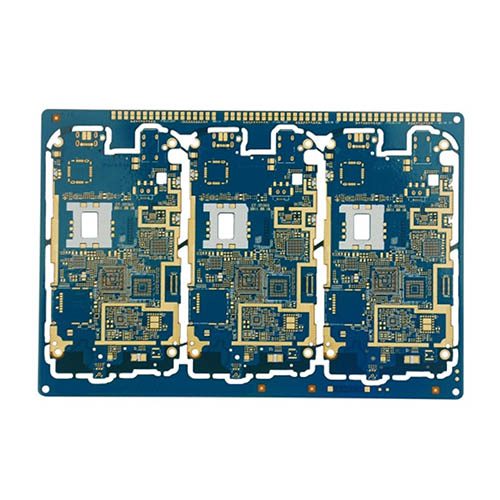
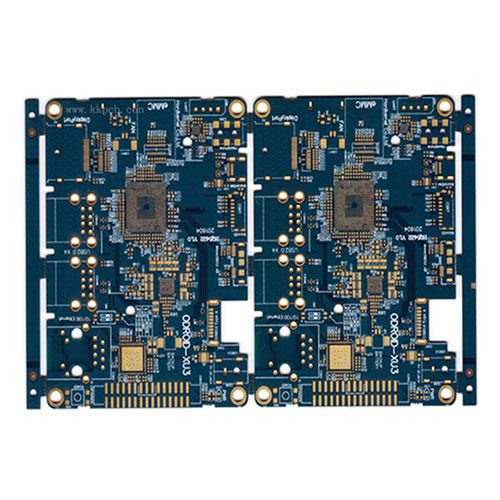

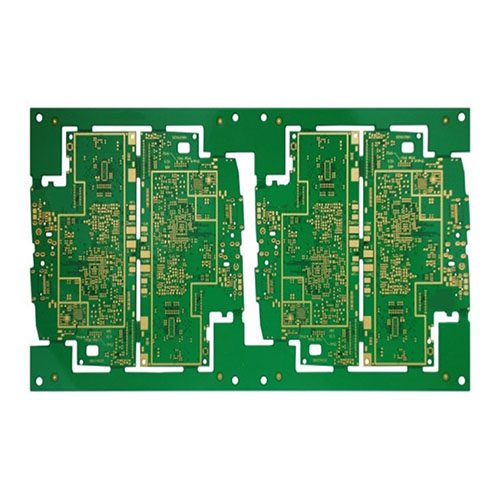
What is HDI PCB?
HDI PCB is the abbreviation of the high-density interconnector PCB. It is a technology for producing printed circuit boards. It is a high-density distributed circuit board using micro blind buried hole technology. HDI board has an internal circuit and an external circuit and then uses hole drilling and Metallization Technology to realize the internal connection of each layer of the circuit.
Generally, using build-up manufacturing. The more laminations, the higher the technical level of the board. The common HDI board is basically a one-time buildup. Advanced HDI adopts secondary or multiple lamination technology and adopts advanced PCB technologies such as hole stacking, electroplating hole filling, and laser direct drilling. With the development of science and technology, electronic design is not only continuously improving the performance of the whole machine, but also trying to reduce the size. From mobile phones to smart weapons, “small” is the eternal pursuit.
High density interconnects (HDI) PCB is an indispensable part of the electronics industry. Electronic components become smaller and lighter, but performance needs to be improved. To accommodate this situation, you need to pack more features into a smaller area. This is what HDI PCB provides.
Compared with traditional PCB, HDI PCB has a higher unit circuit density. They use a combination of buried and blind holes, as well as microvia with a diameter of 0.006 inch or less.
The strict tolerances involved in using HDI printed circuit boards mean that you need to work with experienced suppliers. Even small defects or layout accidents can lead to serious problems. As a leading supplier of HDI printed circuit boards, KKPCB PCB provides a first-class circuit board, and its circuit density is much higher than that of traditional PCB.
HDI processing capacity comes from KKPCB
HDI PCB manufacturing is the core manufacturing service of KKPCB. It has various functions, qualifications, certification, and professional knowledge, and can meet the most stringent requirements of HDI PCB manufacturing. Our extensive PCB manufacturing capabilities support the stringent requirements for advanced HDI PCB design in all industries, including medical, aerospace, defense, and commercial markets. (For more processing capabilities of PCB types, please refer to our PCB capability table)
Circuit Constructions | Single-Sided / Double-Sided / Multi-Layer / Flex / Rigid Flex |
Material | FR-4 / Rogers / Arlon / Polymide / Aluminum / Kapt/etc |
Copper weights | 0.5oz~10oz |
Layer Count | 1-64 layers |
Stack up | Control Dielectric/Control Impedance/TDR Testing/4+N+4/any layer |
Minimum Hole size | 4 mil |
Minimum trace space | 3mil/3mil |
Surface finish | Lead-Free/HASL/ENIG/ENEPIG/Hard Gold/Wire Bonded Gold/Immersion Silver/OSP/selective osp |
Vias | Blind-buried/via-in-pad/pofv/Filled-vias/epoxy resin filled vias |
Advanced tech | Embedded/Laser drill/Multi-level cavity/Bulid-up HDI/Long-short staged gold finger/Hybrid/metal core/press-fit |
KKPCB has advanced advantages in HDI PCB manufacturing. Advanced technology and equipment ensure that we can produce advanced HDI PCB. Would you like to know how much your HDI PCB manufacturing cost is? Please submit a quotation request on this page at any time and describe your HDI PCB requirements in detail. We will make a quotation for your HDI PCB soon.
HDI types we support
We support up to 40 layers of lamination, laser drilling, microvias, stacked micro vias, blind vias, buried vias, vias in pads, laser direct imaging, sequential lamination, 00275 “trace/space, controlled impedance, etc. We are able to produce HDI PCB without minimum order requirements and flexible turnaround time options. Each design is carefully reviewed by our cam engineers before production to ensure that there are no worries about the manufacturing process. The support team provides you with HDI PCB manufacturing order assistance 24 hours a week from Monday to Saturday.
KKPCB has a scientific and perfect procurement chain. In order to ensure the quality from the source, we always insist on selecting high-quality PCB materials to produce all kinds of printed circuit boards. It has high safety and has passed the national compulsory certification. We provide customers with a worry-free purchase experience. KKPCB has a professional production workshop and exquisite production technology. Our HDI PCB meets the national quality Testing standard and high reliability. Various types include rigid board HDI 4 + N + 4 structure, any layer interconnection HDI technology, flexible board HDI and rigid-flex HDI board, which can fully meet the diversified needs of customers.
Advantages of HDI PCB
Reduce PCB manufacturing costs
Although the number of layers of PCB has reached more than eight, the manufacturing cost of HDI PCB is lower than that of the traditional complex lamination process.
Circuits density increase
The interconnection between traditional printed circuit boards and components must be around QFP (Quad Flat Package) and through-hole conductors (fan in and fan out) However, micro via technology can embed interconnect wiring into the next layer without a fan in and fan out. Therefore, some pads (such as mini BGA or CSP ball welding) can be placed on the surface of the outer panel By integrating more components, the density of the printed circuit board can be increased. At present, this new stack and layout method has been used in many small and powerful phones.
It is conducive to the use of advanced construction technology
The traditional mechanical drilling technology cannot meet the needs of the new generation of fine-grained small parts because the size of pads is too large. With the progress of microporous technology, designers can use the latest high-density IC construction technologies, such as Array Package, CSP (chip scale packaging) and DCA (direct chip attach).
Better electrical performance and signal correctness
In addition to reducing signal reflection and crosstalk interference between lines and increasing the space of circuit board design, the use of micro via interconnection can reduce the influence of inductance and capacitance and switching noise in signal transmission, because the structure of physical micro via is small and short.
Improve thermal performance
Glass transition temperature (TG) refers to the temperature at which the physical properties of plastics change to glassy or crystalline state. HDI dielectrics have higher glass transition temperatures, so they have better thermal properties.
Improvement of RFI / EMI / ESD
Microvia technology can shorten the distance between the grounding layer and the signal layer, reduce the interference of radio frequency and electromagnetic wave, and increase the number of grounding wires to avoid instantaneous discharge damage to parts in the circuit due to electrostatic accumulation.
Improve design efficiency
Microvia technology allows the lines to be arranged in the inner layer, so that the design efficiency benefits from more design space.
What is the application of HDI PCB?
HDI is widely used in mobile phones, digital cameras, MP3, MP4, household appliances, notebook computers, automotive motors, automotive control systems, automotive sensor applications, communication systems, network systems and other digital products, aerospace, among which mobile phones are the most widely used. One of the most critical areas for great progress in high-density PCB is the medical field. Medical equipment often needs high transmission Only HDI PCB can provide a small package of the transmission rate. For example, the implant needs to be small enough to fit the human body, but any electronic equipment involved in the implant must absolutely effectively allow high-speed signal transmission. In addition, other medical equipment, such as emergency room monitors, CT scans, etc., can also be used to HDI PCB.
Typical features of HDI PCB
1. The routing distribution is excellent, and the routing width/spacing can be less than 0.1mm;
2. The diameter of the electroplating hole can be as small as 0.07-0. 3mm;
3. The thickness of the finished 6-layer PCB can be less than 0.7mm.
4. Micro blind hole ring less than 6mil
5. The inner and outer wiring width shall be less than 4mil, and the pad diameter shall not be greater than 0. 35mm.
Types of microvias
1) PTH (electroplated through-hole): the hole connecting each layer of conductor.
2) Buried via: through-hole between local layers in multilayer board, called buried guide hole or buried hole.
3) Blind via (blind hole): part of the through holes in the multilayer board are deliberately not fully drilled because only a few layers are required to conduct, and some of them are connected to the hole ring of the outer board.
A. Stack via (stacked blind hole): the blind hole made in the first layer shall be plated with copper fill to connect with the blind hole in the second layer
B. Stage via (stepped blind hole): the second layer of the blind hole is punched on the receiving pad next to the first layer of the blind hole
C. Skipped via: the blind hole skips several layers and conducts a specific layer
D. Via on PTH: the blind hole is located on the buried hole, which needs to be plated flat to undertake radium perforation
E. Via in PTH: the hole in the hole. Fill the large hole first, and then make a small conducting hole in the middle. The plate made by the layer increasing method is named a + N + a. there is an interlayer of the core between them, which is added layer by layer outside. The plate can be added to two layers every time it is pressed.
How to define the stage of HDI
In the 6 laminates, the first and second stages are for the boards requiring laser drilling, i. e. HDI plates.
The first stage HDI board (1 + N + 1 HDI) refers to,
Blind holes: 1-2, 2-5, and 5-6, i. e. laser drilling is required for 1-2 and 5-6.
Two stage HDI PCB (2 + N + 2 HDI) refers to,
Blind holes: 1-2, 2-3, 3-4, 4-5, and 5-6. First drill 3-4 buried holes, then laminate 2-5, then drill 2-3 and 4-5 laser holes for the first time, drill 1-6 for the second time, and then drill 1-2 and 5-6 laser holes for the second time. Finally, drill through holes. It can be seen that the two sections of HDI PCB undergo two pressing and two laser drilling.
In addition, the two-order HDI board can also be divided into staggered two-order HDI boards and stacked two-order HDI boards. Staggered hole 2-order HDI board refers to the staggering blind holes 1-2 and 2-3, while stacked hole 2-order HDI board refers to the stacking of blind holes 1-2 and 2-3, such as blind holes: 1-3, 3-4 and 4-6. By analogy, 3-order and 4-order are the same.
Typical HDI structure / Stack up
Anylayer(ELIC)HDI PCB
HDI PCB production process
Learn the detailed HDI manufacturing process from our pdf file, HDI PCB process.pdf.
Material of HDI PCB
HDI PCB puts forward some new requirements for PCB materials, including better dimensional stability, antistatic mobility, and non-viscosity. The typical material of HDI PCB is RCC (resin-coated copper). RCC includes polyimide metalized film, pure polyimide film, and cast polyimide film.
RCC (resin-coated copper) is a new product without glass fiber, which is convenient for plasma etching and makes the multilayer board light and thin. The copper foil of RCC is generally 18μm 12μm. Even 8. 75μm. Easy to process
There are two main types: B stage (Mitsui) and B + C stage (polyclad)
The advantages of RCC include small thickness, lightweight, flexibility and flammability, compatibility characteristic impedance, and excellent dimensional stability. In the process of HDI Multilayer PCB, it can replace the traditional adhesive chip and copper foil as an insulating medium and conductive layer. Traditional suppression technology can be used to suppress RCC. Then, non-mechanical drilling methods (such as a laser) can be used to form micro via interconnection.RCC promotes the emergence and development of PCB products from SMT (surface mount technology) to CSP (chip-level packaging), from mechanical drilling to laser drilling, and promotes the development and progress of PCB micro vias. All these make RCC a leading HDI PCB material.
In the actual PCB manufacturing process, FR-4 standard TG 140C, FR-4 high Tg 170C, and FR-4 and Rogers combined lamination is usually used most. With the development of HDI technology, HDI PCB materials must meet more requirements.
So, the main trends of HDI PCB materials should be:
Development and application of adhesive-free flexible materials;
The thickness of the dielectric layer is small and the deviation is small;
Development of LPIC;
The dielectric constant becomes smaller and smaller.
The dielectric loss is getting smaller and smaller.
High welding stability;
Strictly compatible with CTE (coefficient of thermal expansion);
Main manufacturing technologies of HDI
Special equipment and processes are required to produce HDI PCBs. These include laser drilling, plugging, laser direct imaging, sequential lamination cycles, and laser drills. HDI boards are thinner and have tighter lines. They also use smaller specialty materials. This type of board requires more time and significant investments in manufacturing equipment and processes to produce.
The difficulties of HDI PCB manufacturing lie in micropore manufacturing, through-hole metallization, and thin wire.
Micro via fabrication
Micro through-hole manufacturing has always been the core issue of HDI PCB manufacturing.
There are two main drilling methods:
1. For ordinary through-hole drilling, mechanical drilling has always been the best choice with its high efficiency and low cost.
2. There are two types of laser drilling: photothermal ablation and photochemical ablation. The former refers to the process of heating the working material after high-energy laser absorption, melting it, and evaporating through the formed through-hole. The latter refers to the result of high-energy photons in the ultraviolet region and laser length exceeding 400 nm.
Laser drilling technology
Unlike mechanical drilling, the laser drilling process does not physically contact the PCB material being used. Drilling the smallest pores can use more technology on the PCB surface. The high-impact beam of the UV laser can drill through copper and electromechanical media (PP, epoxy resin, adhesive, PI, EMI shielding film, etc.) To create tiny through holes. UV laser has excellent reflection, absorption, and transmission capabilities for different materials. The amount of laser drilling per square meter of HDI PCB has been very large. The density has even exceeded 50K/SQM and the drilling capacity of laser machine has always reached 4. 3 million pieces/day.
There are three types of laser systems for rigid-flex HDI PCB board: excimer laser, UV laser drilling, and CO2 laser. Laser technology is not only suitable for drilling, but also for cutting and forming. Although laser drilling equipment has a high cost, it has higher precision, stable technology, and mature technology. The advantages of laser technology make it the most commonly used method in blind / buried hole manufacturing. Today, 99% of HDI micro-holes are obtained by laser drilling.
Through-hole metallization
The biggest difficulty of through-hole metallization is the difficulty of uniform coating. For micro through-hole deep hole electroplating technology, in addition to using the electroplating solution with strong dispersion ability, the electroplating solution on the electroplating device should be upgraded in time, which can be sprayed horizontally through strong mechanical stirring or vibration, ultrasonic stirring, and horizontal spraying. In addition, the humidity of the through-hole wall must be increased before electroplating.
In addition to the process improvement, the HDI through-hole metallization method also sees the main technical improvements: electroless plating additive technology, direct plating technology, etc.
VCP-Vertical continuous plating
Thin circuit
The realization of the thin lines includes traditional image transmission and laser direct imaging.
Laser direct imaging (LDI) technology
For LDI technology, there is no need for photographic film, and the image is directly formed on the photosensitive film by laser. UV wave lamp is used to avoid the adverse effects caused by film defects. CAD / CAM can be directly connected to shorten the manufacturing cycle, which is suitable for the production of a limited number of small-batch PCBs.
Imaging with finer or ultra-fine trajectories to process these HDI boards is expensive but necessary. Finer routing, spacing, and loops require stricter control. Modification, rework, or repair becomes an impossible task by using finer traces. Photographic tool quality, laminated prepreg, and imaging parameters are necessary for a successful process. LDI(laser direct imaging) is a better choice for this fine routing and spacing. The laser direct imaging (LDI) function ensures accurate registration, and all multi-layer cores are thoroughly inspected using automatic optical inspection (AOI) units for excellent defect detection of the finest features.
HDI PCB design guide
When designing HDI design, you should first refer to some available specification references, and IPC-related materials and specifications are one of the introductory materials for readers. IPC has four specifications that are highly relevant to HDI design:
1)IPC / JPCA-2315 – Guidelines for the design of high density interconnect structures and micro vias
2)IPC-2226-part of design criteria for high density interconnect (HDI) printed circuit boards
3)IPC / JPCA-4104 – Specification for verification and performance of dielectric materials for high density interconnect (HDI) structures
4)IPC-6016, specification for verification and performance of high density interconnect (HDI) structures
Readers who use HDI technology can refer to these specifications for technical planning and serve as an important reference for HDI design methods. IPC-2226 is a specification for educators on how to select pore-forming technology, circuit density, design criteria, interconnection structure and material characteristics. It attempts to provide some standards for the use of micro vias in circuit board design.
HDI board layout must take into account the minimum line width during production, the control of safety spacing (including line to line, line to pad, pad to pad, line to copper surface, etc.) and the uniformity of wiring, because the spacing is too small, in the inner dry film process (i. e. the process of transferring the inner pattern to PCB board) If the film cannot fade completely, it will cause short circuit of the line. The line width is too small and the adhesion of the film is insufficient, resulting in open circuit of the line. The uneven distribution of the lines on the same surface, that is, the uneven distribution of the copper surface, will cause inconsistent resin flow velocity at different points. The final result is that the copper thickness will be slightly thinner where the copper surface is less, and the copper thickness will be slightly thicker where the copper surface is more, so it should be noted in the design uniformity of wiring and copper laying.
The following are other related matters needing attention during wiring
1) The devices arranged in top layer and BOT layer have better isolation effect, so the mutual crosstalk between the inner layer change signals shall be avoided and reduced as far as possible;
2) For important signals such as RF and analog areas, ensure that there is a short return path of ground channel (up / down / left / right) around each signal, and more ground vias are drilled around such signals, so as to realize the nearest jump of return current and reduce the loop area.
3) Wiring area of important signals (such as clock / RF) (3w area with line width better) Blind holes without physical connection conflict shall not be added to avoid mutual interference, but blind holes of ground network can be added. This is because the insulation layer of HDI is thin, so it is difficult to press the plate. Where there are buried blind holes in the inner layer, the line is more likely to open circuit due to depression. Therefore, during design, the line shall try to avoid the position of buried blind holes, at least not from the middle of buried blind holes, if it is really unavoidable. Key signals and important signals must be avoided, such as clock signals, RF signals and high-speed signals, not only to ensure good process capacity, but also to avoid mutual interference between plates or other media although there are no physically connected holes and lines;
4) Due to the limited wiring space in the board, priority should be given to ensuring important signals and signals with impedance requirements The line width and line spacing of other signals can be appropriately reduced according to the actual space;
5) On the premise that the power supply meets the current capacity, the whole pavement shall be avoided as far as possible to reduce the interference to other signals;
6) If the production cost of PCB is given priority, the fan out of blind holes in the same network shall be kept at a distance of more than 3. 5mil from the pad, and the limit is 3mil; the distance between buried holes and blind holes, blind holes and through holes in the same network shall be more than 3. 5mil, and the limit is 3mil. The distance between holes and lines in different networks shall be more than 4mil, and the limit is 3mil. However, it is not recommended to set the limit value between holes, holes and pads, and holes and lines at the same time. However, if it is not directly connected to the pad, try to avoid hitting it below the pad and in the empty area as much as possible; the line width is preferred to be more than 4mil, the line to hole, and the line to pad spacing is preferred to be more than 4mil. The limit can be 3mil, but it can not be 3mil at the same time. Here is the limit value recommended by the general, which can be smaller in special cases, but the production cost will increase a lot.
7) If the signal quality is given priority, the blind hole can be directly punched on the pad. In BGA area, if it is worried that the blind hole will affect BGA welding, the blind hole can be tangent to the pad.
8) The buried blind hole is used, and the impedance continuity is worse than that of the through hole. Therefore, for the signal with impedance requirements, the lead length between the pad and the blind hole and between the blind hole and the buried hole shall be reduced as far as possible, and the upper and lower planes of the signal shall be ensured to be as complete as possible. Appropriately increasing the ground through hole at the layer change is helpful to the impedance continuity. The corresponding buried blind hole shall be used for the ground hole to avoid the through hole, mainly because a through hole will affect the impedance. The signal return path of all layers, and one end of the buried blind hole ends in a metal wall, not through the whole PCB.
9) For signals with large interference, such as crystal, crystal oscillator, vc0 and RF circuit, the adjacent ground plane can be hollowed out, and the ground plane of the next adjacent layer can be selected as the reference plane. For high-power channels, the adjacent multi-layer ground plane can be hollowed out to reduce the interference of the circuit to the whole circuit system
10) The wiring of the switching layer of the blind hole shall be as short as possible and shall not overlap with the signal lines of the adjacent layers. If it is really unavoidable, it must be vertically intersected. If important signal lines and lines with impedance requirements are distributed in the adjacent layers and cannot be avoided, they shall be distributed to other layers not adjacent to the switching layer of the blind hole. Here, Special attention should be paid here that the important signal lines of the TOP/BOT layer and the signal lines with impedance requirements and the blind hole layer are easy to be ignored.
11) On the premise of ensuring the performance, buried holes and blind holes are not recommended where through holes can be used. If there are too many buried holes between the second layer and the penultimate layer during pressing, a channel will be generated during the pressing process, resulting in the thickness of the upper dielectric layer being thinner than that of the lower dielectric layer. Therefore, the number of these holes should be minimized in PCB design.
Order HDI PCB
KKPCB, as a reliable HDI PCB manufacturer in China, has been very skilled engineers working with customers to achieve economic perfection in the process of manufacturing any type of multi-layer board, rigid-flex board or HDI board. Want to know how much will your HDI PCB fabrication cost? Feel free to submit a quote request on this page with a detailed description of your HDI PCB requirements. We will quote your HDI PCB very quickly.
High-Density Interconnect (HDI) PCB FAQs
HDI (High-Density Interconnect) PCB refers to a type of printed circuit board that has a higher wiring density per unit area compared to traditional PCB designs. HDI PCBs are characterized by finer lines and spaces, smaller vias and capture pads, and higher connection pad density. They are typically used in applications where space is limited and performance is critical.
Key Features of HDI PCBs:
Microvias:HDI PCBs use microvias, which are smaller vias (typically less than 150 microns in diameter) that allow for more complex routing and higher density of connections.
Laser Drilled Vias:The vias in HDI PCBs are usually drilled using laser technology, allowing for precision and smaller diameters compared to mechanical drilling.
Stacked and Staggered Vias:HDI PCBs can feature stacked and staggered vias, enabling multiple layers to be interconnected more efficiently and compactly.
Thin Dielectrics:HDI PCBs often use thin dielectric materials between layers, which contributes to their high-density interconnections and allows for closer spacing of traces.
Buried and Blind Vias:These types of vias are commonly used in HDI PCBs to connect different layers without passing through the entire board, optimizing space and enhancing performance.
HDI PCBs are applied in various industry sectors, including:
Telecommunications:
- Used in smartphones, tablets, and networking equipment such as routers, switches, and 5G base stations due to their compact size and high performance.
Automotive Electronics:
- Found in advanced driver assistance systems (ADAS), infotainment systems, and various control units, benefiting from the high-density and reliability of HDI PCBs.
Medical Devices:
- Employed in diagnostic and monitoring equipment, such as MRI machines, CT scanners, and portable medical devices, where space and performance are critical.
Aerospace and Defense:
- Utilized in avionics, communication systems, radar, and other military applications that require robust, high-performance, and reliable electronics.
Consumer Electronics:
- Integral to products like wearable devices, gaming consoles, cameras, and other gadgets that demand small form factors and high functionality.
Industrial Automation:
- Used in control systems, sensors, and machinery where precision and reliability are essential for industrial processes and automation.
Computing and Data Centers:
- Essential for high-performance computing systems, servers, and storage solutions that require dense interconnections and efficient heat dissipation.
IoT (Internet of Things):
- Found in various IoT devices, including smart home devices, wearable tech, and industrial IoT applications, where compact and efficient PCB designs are necessary.
HDI PCBs' ability to offer high performance, compact size, and reliability makes them indispensable across these diverse and technologically advanced industry sectors.
HDI PCBs (High-Density Interconnect PCBs) are made from materials that support the high performance, miniaturization, and reliability required in advanced electronic applications. Here are some common materials used in HDI PCB fabrication:
1. FR-4 (Flame Retardant 4):
- Description: A widely used fiberglass-reinforced epoxy laminate.
- Characteristics: Good thermal and mechanical properties, cost-effective.
- Applications: General-purpose HDI PCBs, consumer electronics.
2. High Tg FR-4:
- Description: A variant of FR-4 with higher glass transition temperature (Tg).
- Characteristics: Improved thermal stability and reliability.
- Applications: High-performance HDI PCBs, automotive electronics.
3. Polyimide:
- Description: A high-temperature resistant polymer.
- Characteristics: Excellent thermal stability, flexibility, and chemical resistance.
- Applications: Flexible HDI PCBs, aerospace, and military applications.
4. Rogers Materials:
- Description: A series of high-frequency laminates, such as RO4000, RO3000, and RO4350.
- Characteristics: Low dielectric constant (Dk), low loss, high frequency performance.
- Applications: RF and microwave HDI PCBs, telecommunications, and medical devices.
5. BT Epoxy (Bismaleimide-Triazine):
- Description: A type of epoxy with enhanced thermal and mechanical properties.
- Characteristics: High thermal stability, good electrical properties.
- Applications: HDI PCBs in high-performance computing and telecommunications.
6. Teflon (PTFE):
- Description: Polytetrafluoroethylene, a high-frequency laminate.
- Characteristics: Low dielectric constant, low dissipation factor, high frequency stability.
- Applications: Microwave and high-frequency HDI PCBs, radar systems.
7. Ceramic-filled Laminates:
- Description: Laminates filled with ceramic materials.
- Characteristics: High thermal conductivity, low dielectric constant.
- Applications: High-power and high-frequency HDI PCBs, RF applications.
8. Metal Core PCB (MCPCB):
- Description: PCBs with a metal core (usually aluminum or copper) for better heat dissipation.
- Characteristics: Excellent thermal management, mechanical strength.
- Applications: LED lighting, power electronics, high-heat dissipation applications.
9. Aramid Fiber (Kevlar):
- Description: A type of synthetic fiber known for its strength and heat resistance.
- Characteristics: Lightweight, high tensile strength, good thermal properties.
- Applications: Lightweight HDI PCBs, aerospace, and defense.
10. Glass-Reinforced Epoxy (Tg150/Tg170):
- Description: Epoxy laminates with different glass transition temperatures (150°C and 170°C).
- Characteristics: Varying levels of thermal stability and mechanical strength.
- Applications: Different performance requirements in HDI PCBs, from consumer electronics to industrial applications.
Selecting the appropriate material for HDI PCBs depends on the specific requirements of the application, including thermal performance, electrical properties, mechanical strength, and cost considerations.
To choose a professional HDI PCB manufacturer for producing your PCBs, consider the following factors:
Experience and Expertise:
- Ensure the manufacturer has extensive experience and expertise in HDI PCB manufacturing, including familiarity with the latest technologies and design complexities.
Technical Capabilities:
- Verify that the manufacturer possesses advanced manufacturing equipment and technologies, such as laser drilling, microvia technology, and precision plating processes.
Quality Control and Certifications:
- Ensure the manufacturer has a robust quality control system and adheres to international standards like ISO 9001, IPC standards, and other relevant industry certifications.
Material Selection and Supply Chain:
- Evaluate their expertise in selecting appropriate materials for HDI PCBs and their management of the supply chain to ensure material consistency and reliability.
Production Capacity and Lead Time:
- Assess the manufacturer’s production capacity and lead times to ensure they can meet your project timelines and volume requirements.
Design Support and Engineering Services:
- Look for manufacturers that offer design support and engineering services, including DFM (Design for Manufacturability) reviews, to optimize your PCB design for production.
Testing and Inspection Capabilities:
- Check if the manufacturer has comprehensive testing and inspection capabilities, such as electrical testing, X-ray inspection, and other quality assurance processes.
Customer Service and Communication:
- Evaluate their customer service and communication responsiveness to ensure smooth collaboration throughout the production process.
By carefully considering these factors, you can select a professional HDI PCB manufacturer that meets your requirements and ensures the production of high-quality PCBs.
When producing HDI (High-Density Interconnect) PCBs, several surface finish processes are commonly used to ensure optimal performance, reliability, and solderability. Here are the main surface finish processes for HDI PCBs:
- ENIG (Electroless Nickel Immersion Gold):
- Process: Involves a layer of nickel followed by a layer of gold deposited on the copper surface.
- Characteristics: Provides a flat, smooth surface suitable for high-frequency circuits, excellent solderability, and corrosion resistance.
- HASL (Hot Air Solder Leveling):
- Process: The PCB is coated with molten solder and then leveled with hot air to remove excess solder.
- Characteristics: Cost-effective and provides a reliable solder joint, but may not be as flat as other finishes, potentially impacting high-frequency performance.
- Immersion Tin:
- Process: The copper surface is coated with a thin layer of tin through a chemical process.
- Characteristics: Provides a flat surface suitable for fine-pitch components, good solderability, and is environmentally friendly.
- Immersion Silver:
- Process: The copper surface is coated with a layer of silver through a chemical process.
- Characteristics: Offers excellent electrical performance and corrosion resistance, suitable for high-frequency applications.
- OSP (Organic Solderability Preservatives):
- Process: Applies a thin, organic layer to protect the copper surface from oxidation.
- Characteristics: Simple and cost-effective, provides a flat surface, but may have a shorter shelf life compared to other finishes.
- ENEPIG (Electroless Nickel Electroless Palladium Immersion Gold):
- Process: Involves layers of nickel, palladium, and gold deposited on the copper surface.
- Characteristics: Offers excellent electrical performance, corrosion resistance, and is suitable for high-reliability applications.
Choosing the appropriate surface finish process for HDI PCBs is crucial for ensuring the performance and reliability of the final product. The selection depends on factors such as the specific application requirements, environmental conditions, and cost considerations.
Testing HDI (High-Density Interconnect) PCB boards involves several steps to ensure their reliability and performance. Here are the key methods used to test HDI PCB boards:
Automated Optical Inspection (AOI):
- Visual Inspection: AOI uses cameras and image processing software to inspect the PCB for defects such as misaligned components, solder bridges, and insufficient solder joints. It is a non-contact method and can be used for pre- and post-reflow inspection.
X-ray Inspection:
- Internal Examination: X-ray inspection allows for the examination of internal structures, such as BGA (Ball Grid Array) solder joints, stacked vias, and filled vias. It helps identify hidden defects like voids, misalignments, and solder joint quality.
Electrical Testing:
- Flying Probe Test: This method uses probes to contact the PCB pads and vias to test for continuity and isolation. It is suitable for low to medium volume production and prototype testing.
- In-Circuit Testing (ICT): ICT uses a bed-of-nails fixture to make contact with test points on the PCB. It tests for shorts, opens, resistance, capacitance, and other electrical characteristics. It is highly accurate but more suitable for high-volume production due to the cost of the fixtures.
Functional Testing:
- Performance Verification: Functional testing involves powering up the PCB and verifying its performance under real operating conditions. It checks the board's functionality as a whole, ensuring that it meets the design specifications.
Microsection Analysis:
- Cross-Sectioning: This destructive test involves cutting a cross-section of the PCB to examine the internal structure under a microscope. It helps in analyzing the quality of vias, plating, and layer alignment.
Environmental Stress Testing:
- Thermal Cycling: The PCB is subjected to repeated heating and cooling cycles to test its reliability under thermal stress.
- Humidity and Temperature Testing: The board is exposed to varying levels of humidity and temperature to ensure it can withstand environmental conditions it might encounter during its lifecycle.
Solderability Testing:
- Surface Finish Evaluation: This test evaluates the solderability of the PCB surface finishes to ensure reliable solder joints. It involves dipping the PCB into molten solder and assessing the quality of the solder joints.
Impedance Testing:
- Signal Integrity Check: For high-frequency HDI PCBs, impedance testing ensures that the transmission lines have the correct impedance values to maintain signal integrity.
Burn-In Testing:
- Long-Term Reliability: The PCB is powered and operated for an extended period to identify early failures and ensure long-term reliability. It is often used for critical applications where reliability is paramount.
Electromagnetic Compatibility (EMC) Testing:
- EMC Compliance: This testing ensures that the PCB does not emit excessive electromagnetic interference (EMI) and is immune to external EMI, which is crucial for meeting regulatory standards.
By employing these testing methods, manufacturers can ensure that HDI PCBs meet the required performance, reliability, and quality standards before they are deployed in end-user applications.
HDI (High-Density Interconnect) PCBs offer several advantages over traditional PCBs, making them highly suitable for advanced and compact electronic applications. Here are the key advantages:
Increased Density and Miniaturization:
- Higher Component Density: HDI PCBs support higher component density due to finer lines and spaces, smaller vias, and closer pad spacing. This enables more compact and miniaturized designs.
- Space Savings: The ability to incorporate more components and interconnections within a smaller area allows for the creation of smaller and lighter electronic devices.
Improved Electrical Performance:
- Shorter Signal Paths: The use of microvias and advanced stack-up configurations reduces signal path lengths, leading to improved signal integrity and reduced signal loss.
- Lower Signal Delays: Shorter interconnections result in lower signal delays, which is crucial for high-speed and high-frequency applications.
Enhanced Design Flexibility:
- Complex Interconnects: HDI technology allows for complex interconnects with multiple layers and various via structures (e.g., blind, buried, and stacked vias), enabling more intricate and efficient designs.
- Advanced Layer Stack-Up: The ability to use sequential lamination and build-up processes provides designers with greater flexibility in creating multi-layered, high-performance PCBs.
Better Thermal Management:
- Efficient Heat Dissipation: HDI PCBs often use advanced materials with better thermal properties, improving heat dissipation and overall thermal management.
- Thermal Vias: The use of microvias and other advanced via technologies can enhance thermal conductivity and help manage heat more effectively.
Higher Reliability and Durability:
- Enhanced Mechanical Strength: The smaller and more tightly packed interconnections in HDI PCBs can lead to improved mechanical strength and durability.
- Reduced Risk of Defects: Advanced manufacturing processes and materials used in HDI PCBs can reduce the risk of defects, such as delamination and thermal stress failures.
Improved Signal Integrity:
- Lower Electromagnetic Interference (EMI): Shorter signal paths and better material choices can reduce EMI and crosstalk, leading to improved signal integrity and performance.
- Controlled Impedance: HDI PCBs allow for better control over impedance, which is critical for high-speed and high-frequency signal transmission.
Cost-Effectiveness for High-Volume Production:
- Reduced Layer Count: Despite the higher initial manufacturing costs, the ability to achieve higher density and functionality with fewer layers can lead to cost savings in high-volume production.
- Integration of Advanced Features: The capability to integrate advanced features, such as embedded components and complex interconnects, can reduce the need for additional components and assemblies, further lowering overall costs.
Suitability for Advanced Applications:
- Mobile and Wearable Devices: HDI PCBs are ideal for mobile phones, tablets, and wearable devices where space is limited, and high performance is required.
- High-Speed Communication: HDI PCBs are well-suited for high-speed communication devices, including networking equipment and RF applications.
- Automotive and Aerospace: The reliability and performance of HDI PCBs make them suitable for demanding automotive and aerospace applications.
These advantages make HDI PCBs a preferred choice for many modern electronic applications, where performance, miniaturization, and reliability are critical factors.
HDI (High-Density Interconnect) PCBs involve several special processes that differentiate them from traditional PCBs. Here are some of the key processes involved in HDI PCB manufacturing:
Laser Drilling:
- Microvias: HDI PCBs use microvias, which are small vias with diameters typically less than 150 microns. Laser drilling is used to create these microvias, enabling higher component density and better electrical performance.
Sequential Lamination:
- Build-up Layers: HDI PCBs often have multiple layers added sequentially. This involves laminating additional layers of dielectric material and copper to the core PCB and drilling and plating vias in multiple steps.
Via Filling:
- Filled and Capped Vias: Microvias and other vias in HDI PCBs are often filled with conductive or non-conductive materials and then plated over to provide a smooth surface for further processing.
Stacked and Staggered Vias:
- Stacked Vias: In some designs, vias are stacked on top of each other across multiple layers, requiring precise alignment and filling techniques.
- Staggered Vias: Vias can also be staggered, where they are offset from layer to layer to avoid alignment issues and improve reliability.
Advanced Materials:
- High-Performance Substrates: HDI PCBs often use advanced materials with lower dielectric constants and lower loss tangents to support high-frequency signals and improve signal integrity.
Copper Thickness Control:
- Thin Copper Layers: Precise control over copper thickness is crucial in HDI PCBs to ensure fine line and space requirements are met.
Surface Treatments:
- Surface Finishes: HDI PCBs may use various surface finishes such as ENIG (Electroless Nickel Immersion Gold), OSP (Organic Solderability Preservative), or immersion silver to ensure good solderability and reliability.
Solder Mask and Silkscreen:
- Precision Application: Applying solder mask and silkscreen with high precision is important to avoid covering fine features and to ensure accurate component placement.
Testing and Inspection:
- Advanced Testing Methods: HDI PCBs undergo rigorous testing and inspection processes, including automated optical inspection (AOI), X-ray inspection, and electrical testing to ensure all connections and features are intact and functioning.
These processes collectively allow HDI PCBs to support higher component density, finer lines and spaces, and improved electrical performance, making them suitable for advanced electronic applications like smartphones, tablets, and other high-performance computing devices.
HDI (High-Density Interconnect) PCBs differ from ordinary PCBs in several significant ways. These differences enable HDI PCBs to support advanced electronic applications requiring higher performance, greater component density, and better signal integrity. Here are the key differences:
Layer Structure:
- HDI PCBs: Often have multiple layers with advanced stack-up configurations, including microvias, buried vias, and blind vias. They may use sequential lamination processes to add additional layers.
- Ordinary PCBs: Typically have simpler layer structures with through-hole vias that go through the entire board.
Via Technology:
- HDI PCBs: Use microvias (very small vias with diameters less than 150 microns), blind vias (connecting outer layers to inner layers without going through the entire board), and buried vias (connecting inner layers without reaching outer layers).
- Ordinary PCBs: Mostly use through-hole vias that extend from the top to the bottom layer of the board.
Density and Miniaturization:
- HDI PCBs: Support higher component density due to finer lines and spaces, smaller vias, and closer pad spacing. This allows for more compact and miniaturized designs.
- Ordinary PCBs: Have lower component density and are generally used for less complex designs.
Material Selection:
- HDI PCBs: Often use high-performance materials with lower dielectric constants and lower loss tangents to support high-frequency applications and improve signal integrity.
- Ordinary PCBs: Typically use standard FR4 materials, which may not be suitable for high-frequency or high-speed applications.
Signal Integrity and Performance:
- HDI PCBs: Offer improved signal integrity and performance due to the shorter and more direct signal paths provided by microvias and advanced materials.
- Ordinary PCBs: May suffer from signal degradation over longer paths and through thicker boards.
Manufacturing Complexity:
- HDI PCBs: Require more advanced manufacturing processes, such as laser drilling for microvias, sequential lamination, and precise copper thickness control. These processes add complexity and cost to the manufacturing.
- Ordinary PCBs: Use more straightforward manufacturing processes, making them less expensive and easier to produce.
Applications:
- HDI PCBs: Used in advanced applications such as smartphones, tablets, wearable devices, high-frequency RF circuits, and other compact, high-performance electronic products.
- Ordinary PCBs: Used in a wide range of general applications, including consumer electronics, industrial equipment, and automotive electronics, where extreme miniaturization and high performance are not as critical.
Thermal Management:
- HDI PCBs: Often have better thermal management due to the use of advanced materials and the ability to design more efficient thermal paths.
- Ordinary PCBs: May require additional thermal management solutions, such as heat sinks or thermal vias, to handle heat dissipation.
These differences enable HDI PCBs to meet the demands of modern electronic devices that require high performance, miniaturization, and reliability, whereas ordinary PCBs are suited for less demanding applications.
Designing and manufacturing HDI (High-Density Interconnect) PCBs present several challenges due to the advanced technologies and processes involved. Here are the primary difficulties:
Design Challenges
Complex Layouts:
- High Component Density: Achieving high component density requires precise placement and routing, which can be challenging.
- Fine Line/Space: Designing with very fine lines and spaces increases the risk of shorts and opens.
Thermal Management:
- Heat Dissipation: Managing heat in densely packed PCBs can be difficult, requiring careful thermal analysis and design.
Signal Integrity:
- High-Frequency Signals: Maintaining signal integrity at high frequencies necessitates meticulous impedance control and minimizing signal loss.
- Electromagnetic Interference (EMI): Preventing EMI and crosstalk in high-density designs requires careful layer stacking and shielding.
Stack-Up Configuration:
- Complex Layer Stacking: Determining the optimal layer stack-up to balance performance, cost, and manufacturability is complex.
- Sequential Lamination: Incorporating multiple lamination cycles can complicate the design process.
Via Design:
- Microvias: Designing reliable microvias and managing their placement and size can be challenging.
- Via-in-Pad: This technique can improve routing but complicates manufacturing due to potential solderability issues.
Material Selection:
- Advanced Materials: Choosing materials with suitable dielectric properties and thermal stability is crucial but can limit design flexibility.
Manufacturing Challenges
Advanced Drilling Techniques:
- Laser Drilling: Creating precise microvias with lasers is more challenging and costly compared to mechanical drilling.
- Via Filling: Filling and plating microvias and via-in-pad structures require advanced processes and quality control.
Sequential Lamination and Registration:
- Multiple Lamination Cycles: Each additional lamination cycle increases the complexity and risk of misalignment.
- Layer-to-Layer Registration: Ensuring precise alignment between layers is critical and more difficult with complex stack-ups.
Precise Etching and Imaging:
- Fine Lines and Spaces: Achieving the required resolution for fine lines and spaces demands advanced photolithography and etching techniques.
- Uniform Copper Thickness: Maintaining uniform copper thickness is crucial for impedance control and reliability.
Material Handling:
- Specialized Materials: Handling and processing advanced materials with specific dielectric and thermal properties require specialized equipment and processes.
- Dimensional Stability: Ensuring materials remain stable through multiple thermal cycles and processing steps is challenging.
Solderability and Assembly:
- Surface Finishes: Achieving consistent and reliable surface finishes (e.g., ENIG, OSP) for fine-pitch components is more difficult.
- Component Placement: Placing and soldering small components on high-density boards require precise machinery and techniques.
Quality Control and Testing:
- Inspection: Inspecting high-density designs for defects (e.g., AOI, X-ray) is more complex and time-consuming.
- Electrical Testing: Ensuring thorough electrical testing for continuity, isolation, and performance is crucial but more difficult with dense and complex designs.