Flexible PCBs: Advantages and Disadvantages
Flexible PCB technology, also known as FPC (Flexible Printed Circuit), continues to develop and is used in major electronics sectors such as consumer electronics, automotive, electronic medical devices, wearables, telecommunications and aerospace. The introduction of flexible PCBs has revolutionized conventional electrical interconnect technology, which was traditionally used to connect multiple parts of the same circuit or multiple electronic devices. Due to the flexibility of the connections, compactness and the high electrical connection density that can be achieved, solutions based on flexible PCBs can significantly reduce space, weight and cost compared to equivalent solutions based on rigid PCBs. Flexible printed circuits have replaced many types of wiring (usually done by hand) in a variety of applications, reducing the overall cost of electrical wiring by up to 70%. At the heart of FPCs are flexible films and thin layers of conductive materials that enable electrical connections (for example, between a microcontroller board and an LCD or OLED display) by replacing traditional wires, to which electronic components can be directly attached by soldering or conductive adhesives. Figure 1 shows an example of a flexible printed circuit.
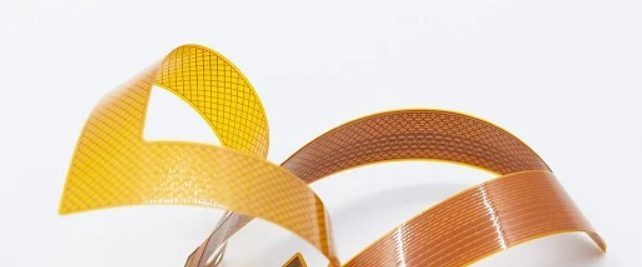
Figure 1: Flexible Printed Circuit (Source: Hoyogo)
Structure of Flexible PCB
Like rigid PCBs, FPCs can be classified as single-layer, double-layer or multi-layer circuits. The main elements of a single-layer flexible printed circuit are as follows:
Dielectric substrate film: The base material of the PCB. The most commonly used material is polyimide (PI), which is characterized by high resistance to traction and high temperatures;
Electrical conductors: Made of copper, they represent the traces of the circuit;
Protective coating, made of coverlay or covercoat;
Adhesive material (polyethylene or epoxy), used to connect the various parts of the circuit together.
The first stage of FPC manufacturing involves etching the copper to obtain the traces, while the protective coating (coverlay) must be drilled out to make contact with the pads. After a cleaning process, the components are connected together by rolling. The external terminals/pins required for the electrical connection of the circuit are immersed in tin or gold to prevent oxidation. If the circuit complexity is high, or a copper ground shield is required, it is necessary to switch to a double-layer or multi-layer FPC. The manufacturing technology is very similar to single-layer flex circuits, except that in multilayer FPCs, PTHs (plated through holes) need to be inserted to create electrical connections between different conductive layers when needed. The combination of these materials forms a flexible circuit, where adhesive materials are used to connect the conductive tracks to the dielectric substrate or, in the case of multilayer flex circuits, to connect the layers together. In addition, adhesive films can also be used for protective purposes to prevent moisture, dust or other external factors from corroding or oxidizing the flexible circuit. In Figure 2, we can observe the structure of a multilayer FPC. The example shown in Figure 2 includes four conductive copper layers, PTHs (on the right side of the image), and holes for accessing conductive materials (on the left side of the image, on the two outer layers).
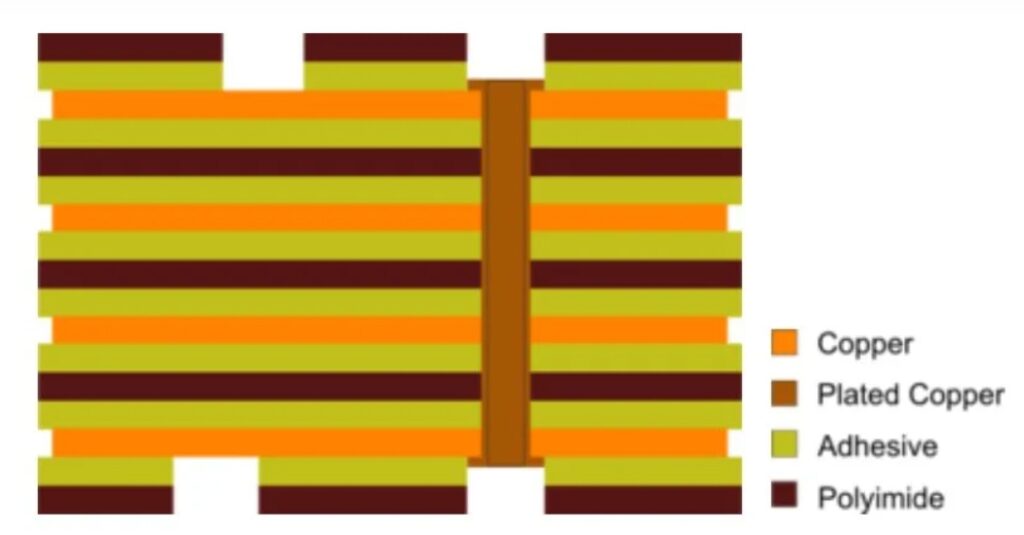
Figure 2: Structure of a multilayer FPC (Source: Altium)
Advantages of flexible PCBs
Because of their flexibility, FPCs can bend and bend, providing greater freedom in the design and operation of applications. Flexible circuits can also fit into small spaces or spaces with irregular shapes, a feature that standard rigid circuits do not support. Another advantage of flexible circuits is that they take up less space, thus reducing the weight of the application motherboard. Optimal use of the available space also allows for better thermal management, reducing the amount of heat to be dissipated.
Flexible printed circuits are also more reliable and durable than rigid PCBs, especially in applications where the circuits are subject to continuous vibrations and mechanical stress. Standard interconnect technologies based on soldered wires and hand-wired connectors have been replaced by flexible printed circuits, which are characterized by extremely low weight and thickness, combined with high mechanical resistance, resistance to high temperatures and atmospheric media, and good electromagnetic immunity (EMI). For example, the wiring of multiple electronic devices in the automotive sector, such as instrument panels, displays and human-machine interfaces (rotating ry controls, buttons, etc.). All these devices require a reliable connection in all operating conditions of the vehicle, being furthermore subjected to continuous mechanical stresses and vibrations. In the automotive sector, flexible printed circuits guarantee reliability, durability and maintenance interventions tending to zero.
Figure 3 shows an automotive application of the FPC technology, here used in a car light switch. figure-3-application-fpc-industrie-auto Figure 3: example of FPC application in the automotive industry
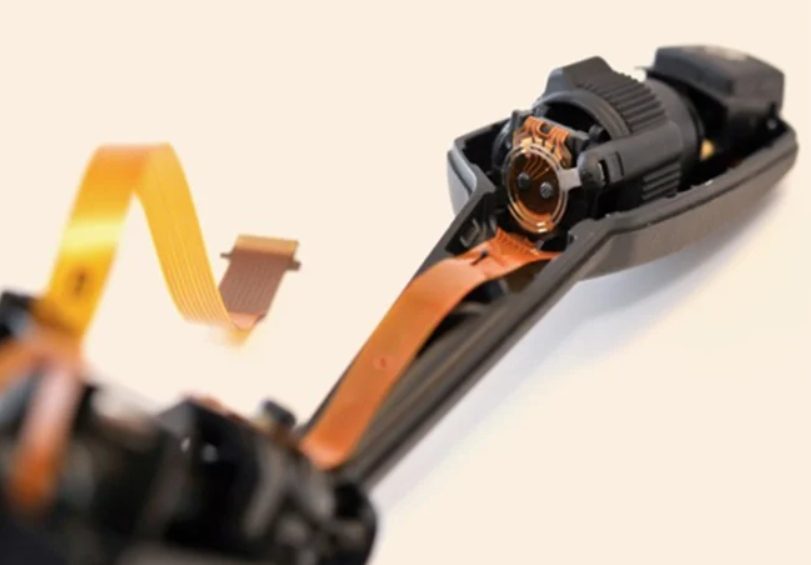
In addition, the use of FPC can reduce the incidence of human errors during wiring, with consequent improvement in quality and reduction of costs. FPC technology contributes to significantly reduce both the size and weight of the application, a key factor for the creation of reliability , compact and highly integrated electronic devices. Disadvantages of flexible PCBs Although there are several and meaningful advantages, the FPC technology has also some drawbacks, or disadvantages. First of all, compared to traditional rigid PCBs, FPCs have a high one-time initial cost. Since flexible circuits are designed for very specific applications, the initial costs related to circuit and prototype design are higher than for rigid PCBs. If the cost is a determining factor in the choice of the type of PCB, it is better to use the FPC technology only for production volumes that are not too low. Another disadvantage is the difficulty of repairing or modifying the PCB when it needs to be reworked. In this case, in fact, it is first necessary to remove the protective film that wraps the circuit, perform the intervention and then restore the protection. Flexible PCBs are a relatively new technology and not all manufacturers are equipped to provide this type of product to their customers.
Furthermore, during the assembly phase, great care must be taken, as the circuit can be easily damaged if handled incorrectly, or by unauthorized personnel. Conclusion Flexible printed circuits are used in several applications that we encounter in everyday life, such as smartphones, tablets, cameras, printers and laptops. They can even be hosted inside our body, being a fundamental component for the creation of pacemakers, cochlear implants and defibrillators . Over the past few years, the FPC industry has grown considerably, driven by the spread of increasingly smaller and lighter wearable and electro-medical devices. In many applications, flexible PCBs can eliminate the need (and cost) of connectors and cables, improving connection reliability and reducing assembly time, assembly costs and overall device dimensions. In conclusion, we can affirm that flexible PCBs have allowed the implementation of new and interesting applications, not achievable with traditional rigid PCBs. However, during the preliminary analysis of every new design, it is necessary to carefully evaluate the advantages and Disadvantages deriving from the use of a flexible PCB, compared to a rigid one; for many applications, the choice of a flexible PCB is mandatory, for others it depends on results of the costs and benefits analysis.
KKPCB conducts research on special processing technologies such as ordinary double-sided boards, thick copper circuit boards, high-frequency circuit boards, HDI circuit boards, rigid-flexible circuit boards, FPC flexible boards, buried blind hole circuit boards, and IC carrier boards. Provides PCB design, PCB layout, PCB prototyping and PCB assembly services.