Exploring the Current Carrying Capacity of Flexible PCBs
Flexible PCBs, commonly made from polyimide materials, are known for their amber color and ability to withstand high temperatures, often comparable to or exceeding those of FR4 boards. The current carrying capacity of flexible PCBs is primarily determined by factors such as copper thickness, trace width, and material properties. With a relative tracking index (CTI) typically above 600 volts, these PCBs are suitable for applications up to 300 volts DC. Higher CTI values indicate greater resistance to electrical breakdown, especially under humid or contaminated conditions.
However, achieving high current levels, such as 30A, can compromise the flexibility of the PCB due to the need for increased material thickness. This article explores the factors influencing the current carrying capacity of flexible PCBs and provides insights into design considerations and alternatives for managing high-current requirements.
Factors Affecting Flexible PCB Current Carrying Capacity
The current carrying capacity of flexible PCBs is influenced by several key factors. Understanding these factors is essential for optimizing design and performance.
1. Line Width and Thickness
- Influence: Wider and thicker traces reduce resistance, allowing them to handle higher currents by minimizing heat generation.
- Design Consideration: Flexibility constraints may require adjustments to conductor widths, impacting current handling.
2. Copper Weight
- Influence: Thicker copper layers (e.g., 2 oz or 3 oz) have lower resistance and can carry higher currents but increase rigidity.
- Design Consideration: Electrodeposited copper used in surface plating may cause micro-cracking, reducing flexibility and capacity.
3. Temperature Rise
- Influence: Excessive heat increases resistance, reducing performance. Poor heat dissipation in flexible PCBs can exacerbate temperature-related issues.
- Design Consideration: Ensure adequate heat dissipation to maintain optimal current handling.
4. De-rating Factors
- Influence: Conditions such as conductor thickness exceeding 3 oz require de-rating to account for increased resistance and heat generation.
- Design Consideration: Adjust current capacity calculations to accommodate de-rating requirements.
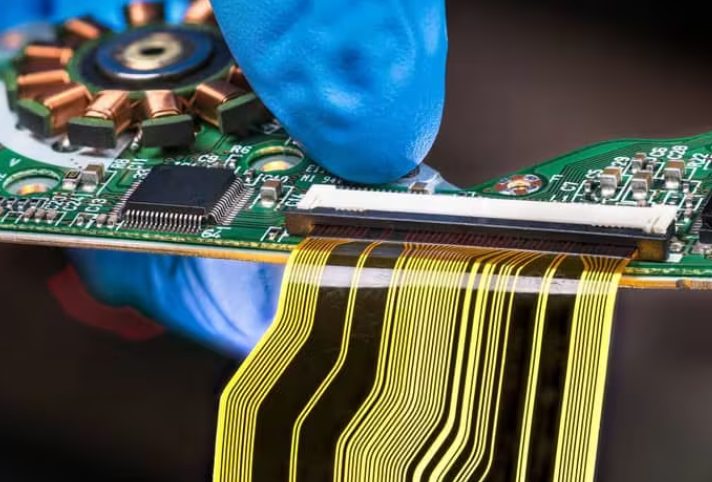
5. Copper Foil Type
- Influence: Higher-quality copper foils, such as rolled annealed copper, offer better conductivity and current handling.
- Design Consideration: Choose copper foil types that balance flexibility and conductivity.
6. Trace Length
- Influence: Longer traces increase resistance and heat, reducing current capacity.
- Design Consideration: Optimize trace lengths to minimize resistance and improve current handling.
7. Operating Environment
- Influence: Ambient temperature and airflow affect heat dissipation. Higher temperatures reduce current capacity.
- Design Consideration: Design for operating conditions to ensure reliable performance.
8. Number of Parallel Traces
- Influence: Distributing current across multiple parallel traces increases total capacity and prevents overloading individual traces.
- Design Consideration: Use parallel traces to manage high-current requirements effectively.
9. Manufacturing Process
- Influence: Techniques such as etching and plating affect trace size and copper uniformity, impacting current capacity.
- Design Consideration: Ensure precise manufacturing processes to enhance capacity.
Using a Nomogram for Current Rating Estimation
Engineers often use a current rating nomogram to estimate the current carrying capacity of flexible PCBs. This graphical tool considers parameters such as trace width, copper thickness, and temperature rise.
How to Use a Nomogram:
- Identify the trace width and copper thickness on their respective axes.
- Draw a line connecting these points and extend it to the desired temperature rise.
- The intersection on the current axis provides an estimated current rating.
Limitations:
- The nomogram offers an approximate starting point.
- Designers must also consider parallel trace configurations, operating conditions, manufacturer data sheets, and industry standards.
Current Carrying Capacity vs. Flexibility
Flexible PCBs typically use copper thicknesses of 2 oz or less to maintain flexibility. However, designs requiring higher currents may need thicker copper, which can reduce bendability. Below are alternatives for managing high-current requirements:
1. Special Order Materials
- Pros: Use glueless construction to reduce flex thickness.
- Cons: High cost and longer lead times.
2. Increase Copper Thickness via Surface Plating
- Pros: Achieve copper thickness up to 3 oz (2 oz base + 1 oz plating).
- Cons: Plated copper is less flexible and prone to micro-cracking.
3. Manufacture Core Materials In-House
- Pros: Use only rolled annealed copper, which is more flexible.
- Cons: Increased core thickness due to bond layer requirements.
Design Considerations for High-Current Flexible PCBs
1. Controlled Impedance Requirements
- Designs requiring controlled impedance may increase flex thickness, reducing bendability.
- Thicker cores are necessary to meet specific impedance requirements.
2. Wider Line Widths
- Increased copper thickness often necessitates wider line widths, further increasing core thickness.
- Balance current handling and flexibility by optimizing trace dimensions.
3. Heat Dissipation
- Ensure adequate heat dissipation through proper material selection and design.
- Use thermal vias or heat sinks if necessary.
The current carrying capacity of flexible PCBs is influenced by factors such as trace width, copper thickness, temperature rise, and material properties. While achieving high-current levels can compromise flexibility, careful design and material selection can help balance performance and bendability. Tools like the current rating nomogram provide valuable estimates, but designers must also consider operating conditions and manufacturing processes. By understanding these factors, engineers can optimize flexible PCB designs for high-current applications without sacrificing reliability or performance.
KKPCB conducts research on special processing technologies such as ordinary double-sided boards, thick copper circuit boards, high-frequency circuit boards, HDI circuit boards, rigid-flexible circuit boards, FPC flexible boards, buried blind hole circuit boards, and IC carrier boards. Provides PCB design, PCB layout, PCB prototyping and PCB assembly services.