Experience Sharing in Multi-Layer PCB Impedance Line Routing
With the rapid advancement of modern electronics, devices like smartphones, computers, and high-definition TVs rely heavily on the intricate design of circuit boards to achieve high-speed data transmission. A key component of this functionality is impedance matching, which ensures reliable and stable signal transmission. This article explores practical insights and best practices for impedance-controlled PCB routing, with a focus on differential signal lines such as those used in USB interfaces
Importance of Impedance Control in PCB Design
In USB protocol definitions, differential signal pairs—such as (D+, D-), (TX+, TX-), (RX+, RX-)—are vital for transmitting digital signals. Proper impedance control helps:
- Ensure transmission stability.
- Offset external common-mode interference.
- Suppress electromagnetic interference (EMI).
To maintain signal integrity, KKPCB recommends adhering to strict differential signal wiring principles.
Best Practices for Impedance Line Routing
1. Optimize Device Layout
- Goal: Minimize the distance between connected devices to reduce differential line length.
- Implementation: Place devices as close as possible, and reduce the number of vias.
2. Symmetrical and Parallel Routing
- Ensure that differential lines are parallel and symmetrical.
- Avoid sharp 90° corners; instead, use 45° angles or smooth arcs.
- Maintain a line spacing of 2W or less (where “W” is the line width).
3. Series Resistor and Capacitor Placement
- Components should be placed in a straight line—either horizontally or vertically.
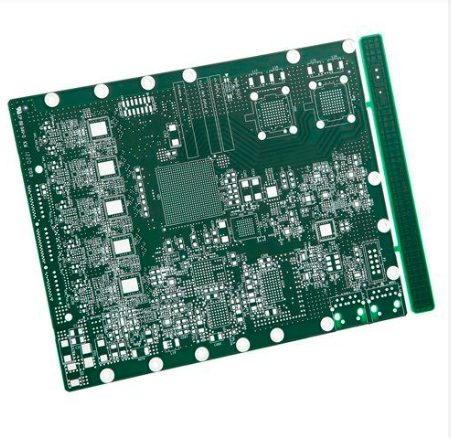
4. Equal Length and Spacing
- Maintain equal length and distance for differential lines to prevent timing deviation and common-mode interference.
- Compensate for mismatched lengths in differential pairs, ensuring the length difference is within 5 mils.
5. Length Compensation
- Address mismatches where they occur. Unequal line lengths introduce timing shifts and reduce signal quality.
- Compensation should align with the differential pair’s physical path, minimizing interference and ensuring signal synchronization.
Factory Impedance Calculation Parameters
KKPCB employs the Polar Si9000 tool for impedance calculations. Here are the standard parameters used:
Parameter | Description | Value |
---|---|---|
H1 | Dielectric thickness (between impedance line and reference layer) | As per design specs |
Er1 | Dielectric constant of the board | 4.2–4.6 |
W1 | Design line width | As per routing spec |
W2 | Upper line width (W1 minus 0.5 mil) | Calculated |
S1 | Spacing between differential lines | Design-dependent |
T1 | Copper thickness (1oz = 1.4 mil) | 1.4 mil |
C1/C2/C3 | Green oil thickness (substrate/copper/substrate) | As required |
CEr | Dielectric constant of green oil | 3.5 |
Key Benefits of Proper Impedance Control
- Enhanced Signal Integrity: Accurate routing ensures minimal signal distortion and loss.
- Reduced EMI: Following best practices suppresses unwanted interference.
- Improved Reliability: Proper compensation and control contribute to consistent device performance.
Impedance line routing in multi-layer PCBs is both an art and a science. Adhering to the principles of short lines, symmetry, equal length, and precise compensation ensures high-speed data transmission and robust device performance. By leveraging tools like the Polar Si9000 and applying best practices in design, engineers can effectively address challenges in modern PCB impedance routing.