Efficient Automatic PCB Wiring: Skills and Key Points
The rapid evolution of PCB design, with increasingly compact layouts, higher device densities, and stringent performance requirements, has necessitated the adoption of advanced EDA tools. However, achieving high routing efficiency and optimizing the design still requires strategic planning and manual intervention. This guide outlines practical skills and key points for efficient automatic PCB wiring, emphasizing design planning, layout, and routing.
1. Planning the PCB Design
Determine the Number of Layers
- Initial Analysis:
Decide the PCB size and layer count early, especially if high-density BGAs or advanced components are involved. The number of layers directly impacts routing and signal impedance. - Layer Distribution:
Use more layers to ensure even copper distribution and to avoid last-minute additions that disrupt design consistency. - Cost Consideration:
Modern manufacturing has reduced the cost disparity between multi-layer and fewer-layer boards, making multi-layer designs more feasible.
2. Setting Design Rules and Constraints
Define Signal Classes
- Classify signal lines based on requirements such as width, parallelism, vias, and layer constraints.
- Assign priorities to different signal classes, with stricter rules for higher-priority signals.
Establish Routing Rules
- Key Parameters: Define rules for line width, via usage, layer restrictions, and spacing.
- Simulation and Adjustment: Use simulation tools to validate and adjust rules as necessary.
3. Component Layout Optimization
DFM (Design for Manufacturability) Rules
- Ensure components are placed to optimize assembly and routing pathways.
Routing Paths and Via Areas
- Visualize Routing Channels: Plan for signal routing paths and via areas during layout to minimize congestion.
- Optimize Fan-Out: Allocate sufficient vias to ensure connectivity to inner layers and facilitate testing.
4. Fan-Out Design
Enable Connectivity
- Assign at least one via to each pin of SMT devices for layer connectivity and testing.
Optimize Via Design
- Use the largest feasible via sizes and trace widths.
- Position vias close to component pins to minimize inductive reactance, particularly for power and ground connections.
Testing Considerations
- Plan for in-circuit testing (ICT) during the design phase to avoid costly adjustments later.
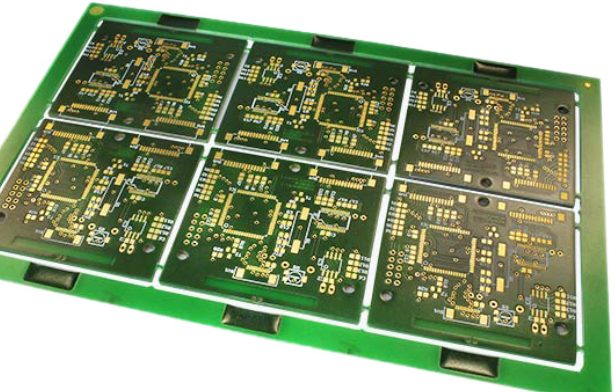
5. Routing Strategies
Manual Routing for Key Signals
- Focus on Critical Paths: Key signals require precise routing to meet performance criteria like reduced inductance and minimized EMC.
- Fix Routed Paths: Secure manually routed critical signals before proceeding with automatic routing.
Automatic Routing Techniques
- Set Constraints: Limit the number of layers and vias to control routing complexity.
- Iterative Refinement: Experiment with different routing parameters, such as spacing, line widths, and via types (blind, buried).
Finish and Edit
- Use automatic tools to route less critical signals, followed by manual editing to optimize routing lengths and reduce via counts.
6. Post-Routing Optimization
Analyze Routing Results
- Check for unreasonable routing paths and adjust them to reduce signal lengths and improve performance.
Verify Signal Integrity
- Validate signal lengths, impedance, and spacing using EDA tool reports.
- Optimize areas with excessive vias or long traces.
Refinement Process
- Continue adjusting routing layers and constraints for remaining signals, gradually easing restrictions as the design progresses.
7. Key Points for Efficient Automatic Routing
- Iterative Experimentation:
Modify routing settings, such as layer restrictions, line widths, and via types, to explore alternative routing paths. - Flexibility for Low-Priority Signals:
Allow greater freedom for the routing tool when handling less critical signals to expedite the process. - Integrated Testing Considerations:
Incorporate testability in the early design phase to avoid production delays. - Monitor and Optimize:
Use software tools to review routing metrics and fine-tune designs for maximum efficiency.
Achieving efficient automatic PCB wiring involves a blend of strategic planning, tool utilization, and manual refinement. By setting robust design rules, optimizing layout, and leveraging EDA tools effectively, engineers can create high-quality PCB designs that meet performance and manufacturability requirements. The iterative approach of routing, validating, and refining ensures that even the most complex designs achieve high routing rates and functionality.