What is the difference between Fr4 Rigid and Rigid-Flex?
Manufacturers create rigid PCB boards to provide a rigid base for electrical components. This feature makes them cost-effective. Hence, this is one of the reasons why rigid PCB boards are in high demand in the market. Fr4 Rigid and Rigid-Flex are two well-known types of rigid boards. They each have their own characteristics. Let’s discuss the differences between these two PCB boards to make your decision-making process easier.
Fr4 Rigid and Rigid-Flex General Specifications
Rigid-Flex is a hybrid PCB made of hardboard and flexible circuits. It is manufactured in a similar way to traditional hardboard circuits, except that some layers are flexible circuits that run through the hardboard. The board is manufactured by the board manufacturer, who adds plated through holes to connect the rigid board layers and the flexible board layers.
These customizations help create a rigid-flex board that is assembled in a way that serves two purposes: acting as a hardboard and fitting into space-constrained products. Well-designed rigid-flex boards can withstand thousands of flex cycles without failure. This makes them suitable for continuous flex applications, also known as dynamic flexing.
Fr4 Rigid boards are made of a non-flexible substrate that prevents them from flexing. Manufacturers use epoxy laminates and prepregs as the most common substrates when making Fr4 rigid boards. They are made of glass that has been infused with a lot of epoxy resin. Fr4 is both a name and a standard. The term refers to the name of materials that meet certain requirements defined by the NEMA LI 1-1998 standard.
These materials generally exhibit good physical, mechanical, thermal, and electrical properties. These properties make Fr4 a superior material for rigid PCBs. Therefore they are used in many applications. Fr4 is generally used to produce single-sided and double-sided PCBs. They are also used in multi-layer PCBs with fewer layers, up to 14 layers.
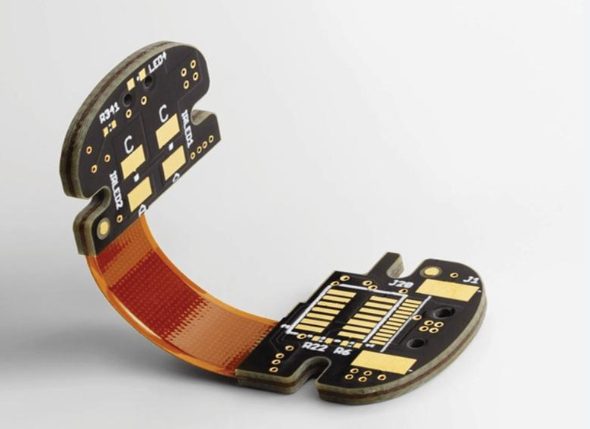
Materials Used
Fr4 rigid boards are made of Fr4, which is less of a material and more like a standard material. Fr stands for flame retardant. The material used to support the board is made by melting the raw glass material and extruding it into fiber yarn filaments, which are then woven together and coated with resins and coupling agents to make them more sticky. Once all the materials are bonded to each other, the board is laminated with copper foil. Based on the characteristics of Fr4 materials, they can be classified into different types:
Standard: They are made of special glass fibers with high bromine content, which improves flame retardancy.
High glass transition temperature: The glass transition temperature is the temperature at which the glass fiber becomes unstable. The higher the glass transition temperature, the more stable the board.
Halogen-free: They are made of bromine. This means that they do not contain halogens that are toxic to humans.
Rigid-flex boards are made using woven glass fibers, which is their main base material. This glass fiber is heavily infused with epoxy resin. However, epoxy resin sometimes cannot withstand frequent vibrations and shocks. Therefore, in some cases, other materials are used. Polyimide is one of the materials that is sometimes preferred over epoxy resin. It is versatile, hard, static, and resists bending or twisting. It also has high heat resistance.
In addition, polyester or PET is another material used for PCBs, which is about 25 to 125 microns thick. Manufacturers use PET in rigid-flex boards. In addition, due to its flexibility and chemical resistance, you can use PCBs made of this material in industrial environments that are prone to overexposure to chemicals. It is also very durable and can withstand a lot of resistance.
For the conductors of rigid-flex boards, copper is the most commonly used material. It is easily available and has good conductivity. Manufacturers choose copper foils based on the different thicknesses and weights of the material. A thin layer of zinc is coated on the foil to ensure longevity. They are also chemically treated to reduce bonding degradation, increase adhesion, and prevent oxidation.
Flexibility
Fr4 rigid boards have multiple layers of flexible substrates that are attached to rigid PCBs. It is designed to bend to fit any product. Single-sided Fr4 rigid boards have conductive copper foil and electrical components on one side. The other side is used for conductive wiring. The fact that all PCB components are mounted on one side reduces the density of the PCB, making it more flexible.
Double-sided Fr4 rigid boards can have conductive copper and all other components mounted on both sides. Therefore, it is denser than single-sided PCBs. Multi-layer Fr4 rigid boards contain two or more layers of conductive materials. It is much denser than the above types. While it is more rigid than single-sided and double-sided PCBs, it improves space efficiency and reduces overall weight because fewer PCBs need to be used.
Rigid-flex boards are hybrid PCBs that have both rigid and flexible circuits. This means that they have the qualities of both rigid and flexible boards while eliminating their limitations. Therefore, they contain both rigid and flexible materials by incorporating a layered flexible substrate within the rigid circuit board material.
This makes them more flexible and stable with the strength and circuit routing density of a rigid PCB. Therefore, complex and challenging mechanical design concepts have an opportunity. Rigid-flex boards eliminate flexible cables, connectors, and discrete wiring, making them simpler for electronic designs. For good measure, all electrical and mechanical components are contained inside the PCB, which helps improve performance, providing both rigidity and a flexible structure.
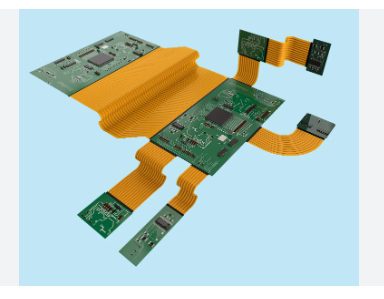
Cost
Although rigid-flex boards are more expensive than rigid PCBs, they are more cost-effective in terms of assembly expenses. For example: Due to their smaller size and fewer connections, rigid-flex boards require less material to assemble. With fewer parts and connector components, the final product has lower procurement and assembly costs, which translates to higher revenue. This means that you can reduce the overall manufacturing cost of rigid-flex boards due to the low cost of materials used in assembly and logistics.
However, rigid-flex boards are suitable for PCB designs with more complexity and precision. They are used for dynamic flexible designs and are very flexible to other designs. However, this feature of this board makes it more expensive compared to Fr4 rigid boards. Therefore, cost-effectiveness, in addition to other qualities, is also the reason why Fr4 rigid boards are more common in industrial applications. You can see that Fr4 rigid boards are a commonly used material in a variety of devices, from everyday appliances to gaming systems and computers, because it is not as expensive as other options.
Strength and Weight
Rigid PCB boards are generally very common; however, rigid-flex boards are relatively less dense because manufacturers use flexible substrates to compose them. Note that developers design electronic devices to be more flexible and smaller in size. The versatility of rigid-flex boards makes them easy to bend and fold to fit smaller devices and properly connect miniature components. This miniaturization also makes them lightweight.
The strength and weight of Fr4 rigid boards largely depends on the customization of the board. Many factors, including temperature resistance and conductivity, play a vital role in this decision. Choosing a more heat-resistant substrate means using a heavier, denser material, which affects the overall weight. The use of copper wires for conduction is another factor. The more copper wires used, the greater the conductivity and the heavier the board. Therefore, these factors should be considered when building Fr4 rigid boards.
Applications
Since rigid-flex boards have the dual characteristics of being both rigid and flexible, you can use them in a variety of environments. They are used in places prone to high vibrations, as flexible boards cannot survive there. They are also used in dynamic bending applications where objects need to bend multiple times without breaking. This makes rigid-flex boards very reliable. Therefore, they are used in more specialized industries where quality trumps all other factors.
On the other hand, Fr4 rigid boards are more versatile. Since they are cheaper and easily available, they are used in everyday devices such as computers. You can find them in some automotive devices where cost is more of a concern than reliability. Therefore, they are more versatile than rigid-flex boards, and therefore have more production.
Therefore, both types of boards have their own advantages and disadvantages. Rigid-flex boards are more flexible than Fr4 rigid boards. Fr4 has a higher flame retardancy. Therefore, it is used according to the current situation. Rigid-Flex boards have more industrial uses, which explains why they are more expensive, while Fr4 rigid boards have more universal uses and are therefore cost-effective. Both of these boards have their own characteristics that make them stand out.
KKPCB conducts research on special processing technologies such as ordinary double-sided boards, thick copper circuit boards, high-frequency circuit boards, HDI circuit boards, rigid-flexible circuit boards, FPC flexible boards, buried blind hole circuit boards, and IC carrier boards. Provides PCB design, PCB layout, PCB prototyping and PCB assembly services.