HDI PCB Design: Comprehensive Guidelines, Processes, and Considerations
In today’s world, electronic products have become more complex than before to achieve better performance and thus transfer data faster than ever before. HDI (High Density Interconnect) is a technology used in PCBs to achieve miniaturization of circuit boards with higher component density. Therefore, HDI PCB design considerations are particularly important in HDI PCB manufacturing. In this article, let’s explore some of the considerations and guidelines that need to be followed during HDI PCB design.
What is HDI PCB Design?
HDI PCB design, or High Density Interconnect PCB design, is a type of printed circuit board (PCB) design that focuses on maximizing the density of electronic components and circuit interconnections within a small area. In order to accommodate more components and increase the wiring density of the board, HDI PCB design uses more complex features such as microvias, blind vias, and buried vias, which allows for the design of compact circuit boards.
The manufacturing of HDI PCBs began in the late 1980s. With the successive production of PCBs, the first HDI production began in 1984. Since then, designers and manufacturers have been looking for ways to pack more components in a smaller area. HDI boards are designed and manufactured to comply with IPC-2315 and IPC-2226 standards.
Considerations and guidelines to follow during HDI PCB design
Designing layer stackup in HDI PCB design
HDI PCB design (high-density PCB design) has stricter requirements for signal integrity, and designing a board with proper stackup is critical to ensure signal integrity of HDI boards. Choosing the right material is important not only for signal integrity issues but also for impedance and heat dissipation characteristics. In addition, the number of layers and the order of layers built in sequence play a vital role in HDI PCB design.
Typically, HDI stackup is made in sequence with a symmetrical structure. It consists of prepreg, core board, and copper foil. The design of the stackup depends on the components used in the HDI PCB design, impedance requirements, and signal integrity requirements. For HDI boards, microvias, blind vias, and buried vias are used to reduce the thickness of the board and accommodate more routing density on the layers.
Improper stack-up construction can lead to poor performance, causing EMI issues, crosstalk, and increased susceptibility to surrounding noise. To overcome these issues, the stack-up must be constructed in such a way that all high-speed signals must be provided with a ground plane above or below to facilitate the signal return path.
The following points need to be considered while designing an HDI board stack-up:
Aspect ratio in HDI PCB design: Maintain the aspect ratio of through-hole drill (1:10) and HDI drill (1:0.75)
Lamination cycles in HDI PCB design: Limit the lamination cycles to less than 3 cycles.
Board thickness in HDI PCB design: Use microvias, blind vias, and buried vias to reduce board thickness.
Signal return path: Place a ground or power plane layer to provide a signal return path.
Minimum inductance path: The signal return path should be determined by taking the minimum inductance path return.
By considering all the above factors, a balanced stack-up constructed with proper signal and power ground planes will minimize crosstalk and EMI effects in the board.
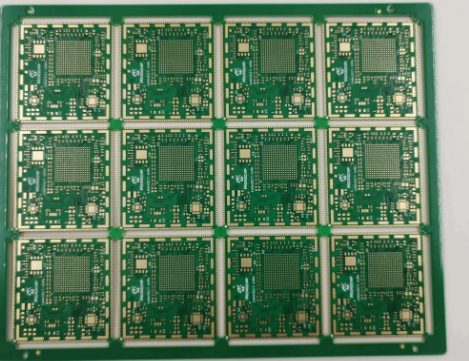
Different Types of VIA Technologies Implemented in HDI PCB Design
Any conductor of an HDI board is considered as part of that circuit. The size and depth of the vias and the length of the traces, all these factors are considered in HDI PCB design. Via size is the main factor that needs to be considered before the high-density PCB layout process. The smaller the vias, the better the performance of high-speed signals.
For high-speed designs, trace lengths should be shorter, and to achieve this, vias should be close to pads, or partially land on pads, or even land inside SMD pads.
Now, let’s explore different types of via technologies used in HDI PCB design based on their functions
Blind Vias
Via holes that connect an external layer to one or more internal layers are called blind vias. This connection may be from the top or bottom of the HDI PCB design, but in either case, these drill holes are not visible from the other side of the board after lamination is completed. The IPC standard for blind vias is 6 mil and below.
Buried Vias
Via holes that connect only the inner layers of the board are called buried vias. They are not visible on either side of the board because they are completely covered after lamination is completed. The IPC standard for buried vias is 6 mil and below.
Microvias
These are very small vias, often called laser vias or laser ablated vias or microvias. An ideal microvia has an aspect ratio of 0.75:1 and a maximum depth of 0.25 mm between the surface and the target pad. The standard drill size, according to IPC, is 75-150 microns and can be drilled mechanically or using laser technology.
Typically, these drills are no deeper than two layers because plating copper inside the walls of these vias is a tedious process.
In addition, these microvias are classified into the following two types:
Staggered vias: vias that are offset from each other and have separate axes.
Stacked vias: vias that are located on top of each other on the same axis.
Via-in-pad technology
Via-in-pad is used when component density is high and PCB board size is limited. Unlike traditional vias, these vias are located on the SMD component and then filled and plated with copper to avoid solder flowing into the via during assembly. This method is called VIPPO (Via-in-Pad Plated-Over). This method is suitable for fine pitch BGA components.
Common Routing Guidelines for HDI Board Routing
As the density of components increases, routing of HDI boards will also become very complex. Trace width, via size, and spacing must be minimized to accommodate high density routing in HDI PCB design. All critical signal components, decoupling capacitors, and ICs must be routed first, and then the rest of the components must be completely routed in HDI PCB design.
The best practice is to create a multi-layer board and provide ground and power planes as inner layers to minimize the noise and crosstalk caused by high-speed signals. These ground and power planes are placed in such a way that the ground plane is right below the signal layer, which acts as the return path and reference layer for the differential signals on the top layer. The power plane is placed after the ground plane to reduce impedance.
To provide a separate ground plane for each signal, copper must be laid out as per the split plane concept. This will avoid noise generated by different signals and components, resulting in better performance without interference from adjacent signals in HDI PCB design.
Additional Routing Guidelines for Routing HDI Boards
In addition, when routing differential pair signals, they must be routed symmetrically with specified distances to achieve specified impedance. Improper routing of these differential pairs can cause signal delays at the receiver end. There should not be any components or vias between these signals. Placing components or vias between these signals can cause EMI/EMC issues and impedance mismatch in HDI PCB design.
In addition, differential pairs require very tight delays between positive and negative signals. To achieve these tight delays, serpentine geometry must be used in HDI PCB design to match the length of the traces.
Component Placement in HDI PCB Design
The placement of components plays an important role in HDI PCB design (high density PCB design) as it directly affects the routing density and signal integrity of the board. Planning the placement of components is necessary to maintain the shortest paths. Always group components according to the schematic workflow and separate sensitive and critical components and place them accordingly.
As an initial step, read the schematic and divide the circuit into different sections based on the following factors: Analog, Digital, High-Speed Signal, Mixed Signal and High Frequency, Power Supply, etc…
After grouping the components, place the major components like microprocessor or microcontroller, Ethernet and storage devices in the center of the board as they are connected to most of the components in the circuit. Next, place all the decoupling capacitors, crystal oscillators and resistors as close to these components as possible to allow for a smooth signal flow between them.
Some of the major considerations to be followed while placing the components are as follows:
Orientation of components in HDI PCB design: The components must be placed in the same direction to allow for efficient and error-free routing during HDI PCB design and error-free soldering process during assembly.
Layout surface of components: Place all SMD components on the same side, either top or bottom. Place all through-hole components on the top to simplify the assembly process.
Separate analog and digital circuit sections: Separate the analog and digital sections to avoid noise interference generated by them.
Placement of decoupling and bypass capacitors: Place all decoupling and bypass capacitors as close to the corresponding circuit sections as possible.
Placement of sensitive components: Place all sensitive components away from the edge of the board to reduce the impact of EMI radiated by peripheral devices.
Now, place all peripherals at the edge of the board for communication with external devices.
Signal integrity
Signal integrity is a measure of the quality of the signal’s distortion-free transmission on the transmission line.
Boards operating at low and medium frequencies are rarely affected by signal integrity issues, while in high-speed designs, since they usually operate in the high-frequency range, the signal rise time is short and the signal integrity problem is relatively prominent. Signal integrity issues can cause the PCB to not work properly and reduce the performance of the board.
Here are some design considerations that must be implemented during HDI board design:
SI effect: HDI signals require controlled impedance routing to minimize SI effects. To achieve this, trace width, spacing, and appropriate dielectrics must be maintained to obtain the desired impedance value in the HDI board design.
Signal reflection and impedance mismatch: Reduce the through-hole stub length to avoid signal reflection and impedance mismatch in HDI PCB design. Use blind and buried vias to route signals and connect directly to the inner layers.
Signal crosstalk: Use ground shielding and proper trace spacing to avoid signal crosstalk caused by coupling between adjacent signal traces.
Power supply noise: Place decoupling capacitors as close as possible to HDI components to reduce power supply noise. Effectively separate the ground and power layers to distribute power smoothly across the board.
Signal loss at the receiving end: Maintain proper spacing between differential pair signals and match the length of the traces to avoid signal loss at the receiving end.
EMI and ground bounce effects: Maintain a proper return path for high-speed signals to reduce EMI and ground bounce effects. In HDI board design, solid ground should be used under high-speed signals and keep low impedance to prevent signal distortion.
Potential problems: In HDI board design, use simulation to identify signal integrity issues at the design level to avoid potential problems and fix them accordingly.
Thermal management
Thermal management in HDI PCB design
During the HDI PCB design process, it is very challenging to dissipate the heat generated by the components due to the dense arrangement of components in the HDI board. In order to produce a reliable and durable circuit board, it is crucial to manage heat dissipation issues at the HDI PCB design stage.
Let’s explore some of the things to consider when it comes to thermal management for HDI boards:
Thermal Conductive Materials: In HDI board design, use thermally conductive materials such as metal core or thermally conductive dielectric materials to dissipate heat from critical areas of the PCB.
Thermal Vias: Implement thermal vias to dissipate heat from high-power components to inner or outer layers. Place these vias close to the heat source to transfer the heat to the other side of the board.
Heat-generating component placement: In HDI board design, place all heat-generating components close to the edge of the board to facilitate heat dissipation and optimize airflow.
Proper Enclosure: Design the enclosure to promote proper airflow to the PCB, especially around heat-generating components.
Optimize Layout and Design: In HDI board design, use thermal analysis simulation tools to identify temperature distribution across the board, which will help optimize component placement, via placement, and stackup design for maximum thermal performance.
Design for Manufacturing (DFM)
Design for Manufacturing (DFM) in HDI PCB Design
To ensure that HDI boards are produced without errors, it is necessary to work with the PCB manufacturer before releasing the Gerber to avoid any problems on the production site. Some of the key considerations to implement while designing HDI boards are as follows:
Communication before board design: Communicate with the PCB manufacturer before board design and get familiar with the manufacturing guidelines.
Design-related issues: Understand the minimum trace width, spacing, annular ring, and via sizes to avoid causing manufacturing issues.
Aspect ratio: Make sure that aspect ratios are met as they are the key factors affecting manufacturing. Improper aspect ratios may cause plating issues and drilling problems during manufacturing.
Choice of materials: Choose materials that are compatible with high-speed signals.
Choice of vias: Choose the appropriate via type (blind, buried, or microvia) based on the complexity of the HDI PCB design and avoid placing more vias at fine pitch components to avoid plating issues.
KKPCB conducts research on special processing technologies such as ordinary double-sided boards, thick copper circuit boards, high-frequency circuit boards, HDI circuit boards, rigid-flexible circuit boards, FPC flexible boards, buried blind hole circuit boards, and IC carrier boards. Provides PCB design, PCB layout, PCB prototyping and PCB assembly services.