Comprehensive Guide to IC Substrates and Their Role in Electronics
Integrated Circuit (IC) substrates are essential components in modern electronics, acting as the primary interface between semiconductor chips and printed circuit boards (PCBs). Their rapid adoption is driven by advanced IC packaging types like Chip Scale Packaging (CSP) and Ball Grid Array (BGA), which demand innovative solutions to meet increasing performance and miniaturization requirements.
What is an IC Substrate?
IC substrates are specialized PCBs used to house and interconnect IC chips. They provide:
- Electrical connectivity: Linking chips to circuit boards.
- Mechanical support: Protecting, reinforcing, and stabilizing IC chips.
- Thermal management: Offering pathways for heat dissipation.
IC substrates enable the high-density interconnection required for modern semiconductor devices, exceeding the capabilities of traditional PCBs in design complexity and precision.
Types of IC Substrates
IC substrates are classified by package type, material properties, and bonding technology:
By Package Type
- BGA IC Substrate
- High electrical and thermal performance.
- Supports ICs with over 300 pins.
- CSP IC Substrate
- Lightweight and compact.
- Common in telecommunications and memory products.
- FC IC Substrate
- Employs flip-chip packaging for minimal signal interference and superior heat dissipation.
- MCM IC Substrate
- Multi-Chip Module substrate for integrating multiple chips in a single package.
- Lightweight and compact but with limitations in heat dissipation and signal interference.
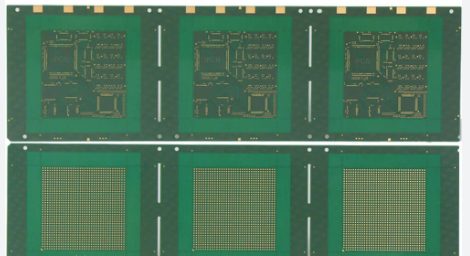
By Material Properties
- Rigid IC Substrates
- Made from materials like ABF resin, BT resin, or epoxy resin.
- Thermal expansion coefficient: ~13-17 ppm/°C.
- Flexible IC Substrates
- Made from PE or PI resins.
- Thermal expansion coefficient: ~13-27 ppm/°C.
- Ceramic IC Substrates
- Composed of materials like aluminum nitride or silicon carbide.
- Low thermal expansion coefficient: ~6-8 ppm/°C.
By Bonding Technology
- Tape Automated Bonding (TAB)
- Wire Bonding
- Flip-Chip (FC) Bonding
Importance of IC Substrates in Packaging
IC substrates are integral to IC packaging, which safeguards semiconductor devices while ensuring efficient signal transfer to PCBs. Packaging protects the IC from environmental factors like corrosion and physical damage while facilitating electrical connections.
Applications of IC Substrates
IC substrate PCBs are pivotal in industries demanding compact, high-performance devices. They are widely used in:
- Consumer Electronics: Smartphones, tablets, laptops.
- Medical Devices: Advanced diagnostic and therapeutic equipment.
- Telecommunications: Network infrastructure and 5G devices.
- Aerospace & Military: High-reliability electronics.
- Industrial Control Systems: Automation and robotics.
Characteristics of IC Substrates
- Lightweight and compact.
- Highly reliable with fewer solder joints.
- Enhanced performance in electrical and thermal attributes.
IC Substrate Manufacturing Process
- Copper Patterning and Plating: Fine-line circuitry using uniform copper plating.
- Solder Mask Application: Hole filling and mask printing to ensure minimal height differences.
- Surface Treatment: Uniform finishes like ENEPIG or ENIG for corrosion resistance.
- Inspection and Reliability Testing: Ensures quality and reliability.
Advanced Technologies in IC Substrate Production
- Direct Imaging (DI): For fine-line imaging and semi-additive processes.
- Automated Optical Inspection (AOI): High-resolution inspection for defect detection.
- UV Laser Drilling: Precision drilling of micro-vias and blind vias.
- Inkjet Printing: Cost-effective, high-precision printing for advanced IC designs.
Key Design Considerations
- Material Composition
- Leadframes: Predominantly gold or silver finishes for conductivity.
- Laminates: Cost-effective options like BT resin and epoxy resins for rigid substrates.
- Substrate Selection
- Rigid Substrates: Preferred for structural integrity.
- Tape Substrates: Lightweight and flexible, ideal for mobile devices.
- Metal Conductor Design
- Copper conductors with nickel/gold finishes ensure conductivity and prevent oxidation.
Future Trends in IC Substrates
- Increased adoption of organic substrates and advanced laminates.
- Innovations in flexible and ceramic substrates for emerging applications like IoT and AI-driven devices.
- Rising demand for cost-effective yet high-performance materials driven by consumer and industrial needs.
KKPCB conducts research on special processing technologies such as ordinary double-sided boards, thick copper circuit boards, high-frequency circuit boards, HDI circuit boards, rigid-flexible circuit boards, FPC flexible boards, buried blind hole circuit boards, and IC carrier boards. Provides PCB design, PCB layout, PCB prototyping and PCB assembly services.