Complete Guide to ESD Prevention in PCB Design
Electrostatic Discharge (ESD) can damage sensitive components such as MOSFETs, CMOS gates, and PN junctions, leading to issues like gate damage, short circuits, and even melted wiring. This guide offers practical strategies to design PCBs that effectively prevent ESD from harming the circuit.
Key ESD Prevention Techniques for PCB Design
1. Layering Techniques
- Multi-layer PCBs: Use multi-layer boards whenever possible. With added ground and power planes, the common-mode impedance and inductive coupling can be reduced by 90-99% compared to double-sided PCBs. Place signal layers close to power or ground planes to enhance ESD protection.
- Ground Grid on Double-sided PCBs: For double-sided boards, create a power and ground grid with a maximum grid size of 60mm, ideally less than 13mm, for better connectivity and reduced interference.
2. Optimized Layout
- Compact Circuitry: Keep circuits as compact as possible to reduce ESD vulnerability.
- Connector Placement: Group all connectors on one side of the board to facilitate consistent grounding.
- Power Line Entry: Route power lines through the card’s center, away from high-ESD zones.
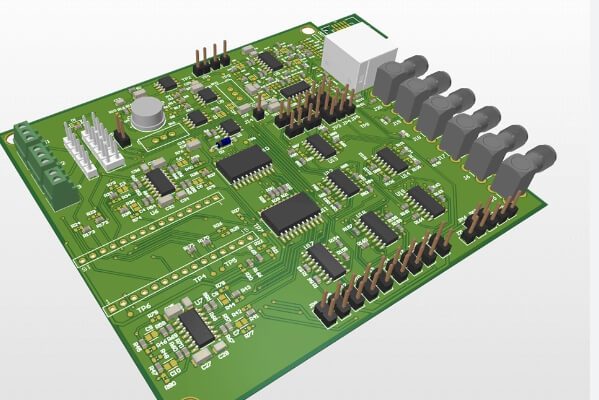
3. Chassis Grounding
- Chassis Ground Placement: Place wide or polygonal chassis ground fills on all PCB layers near external connectors to prevent direct ESD impact, with vias spaced 13mm apart for grounding continuity.
- Mounting Holes: Situate mounting holes at the board’s edges and connect them to the chassis ground using solder-mask-free pads on top and bottom layers.
4. Circuit Grounding and Isolation
- Isolation Zones: Maintain a 0.64mm isolation zone between chassis ground and circuit ground across all layers.
- Periodic Connections: Add a 1.27mm-wide ground connection every 100mm along the chassis ground near mounting holes to maintain a stable ground reference.
5. Ring Grounding
- Ring Ground Path: Establish a 2.5mm or wider ring ground path around the circuit, connected every 13mm with vias.
- Open Gaps: Leave a 0.5mm-wide gap on the ring ground (across layers) to prevent large-loop formation, minimizing ESD potential across the ring.
6. Signal Line Grounding
- Parallel Ground Lines: In high-ESD areas, lay ground lines near signal lines and ensure ground continuity.
- Central Placement of Sensitive Circuits: Place ESD-sensitive components close to the board center to benefit from shielding provided by surrounding circuitry.
7. Series Resistors, Ferrite Beads, and Transient Protectors
- Receiver-side Resistors: Place series resistors or ferrite beads on the receiving end, and use similar components at the driving end for sensitive cable drivers.
- Transient Protectors: Install transient protection devices at the receiving end, with short, thick ground wires for effective ESD mitigation.
8. Filtering and Capacitance Placement
- Connector Filtering: Use filter capacitors within 25mm of connectors to intercept ESD, with short, thick wires for grounding.
- Loop Area Reduction: Alternate signal and ground paths on longer signal lines to minimize loop areas and enhance ESD resilience.
9. Power and Ground Optimization
- Minimized Power-Ground Loop Areas: Keep loop areas between power and ground small, with high-frequency bypass capacitors at each IC power pin.
- Connector Proximity: Add high-frequency bypass capacitors within 80mm of each connector for rapid ESD grounding.
10. Unused Area Fills and Power/Ground Openings
- Ground Fill Connections: Connect unused ground areas every 60mm for added grounding robustness.
- Power Plane Openings: For openings >8mm in power/ground planes, use narrow connections to bridge gaps and maintain a continuous ground.
11. Reset, Interrupt, and Control Line Placement
- Sensitive Line Placement: Avoid routing reset and interrupt lines near PCB edges and input/output circuits. Implement high-frequency filtering on these lines for added ESD protection.
12. Chassis Insertion and Signal Routing
- Chassis Mounting: Insert the PCB directly into the chassis to reduce the risk of ESD exposure.
- Magnetic Bead Placement: Route signal lines under magnetic beads carefully, as some beads have conductive paths that may unintentionally bridge circuits.
By integrating these design principles, PCB layouts can achieve enhanced ESD protection, improving the resilience of the design to environmental and handling-related static electricity while ensuring reliable performance in demanding applications.
As a leading PCB manufacturer, members of our printed circuit board (PCB) design service team are practical partners working with you on every project and can help you achieve your goals at any time. They can complement your engineering expertise, which helps speed up time to market, reduce the time from concept to production, and ensure that quality is integrated into the manufacturing process to maximize your profits.