Automotive PCB Assembly
- Home
- Automotive PCB Assembly
Top Automotive Electronics PCB Assembly Supplier
Automotive PCB are key components used in a variety of automotive electronic systems, including sensor systems, engine controls, GPS, security systems, digital displays, and LED lighting. Automotive PCBs must have high reliability, durability, and high quality to ensure safe driving. KKPCB strictly abides by IATF16949 and ISO13485 automotive industry manufacturing standards, adheres to strict quality control process, and has established a 100% comprehensive inspection and control system from source to final.If you’re looking for the best automotive electronics PCB suppliers, We are your trusted partner
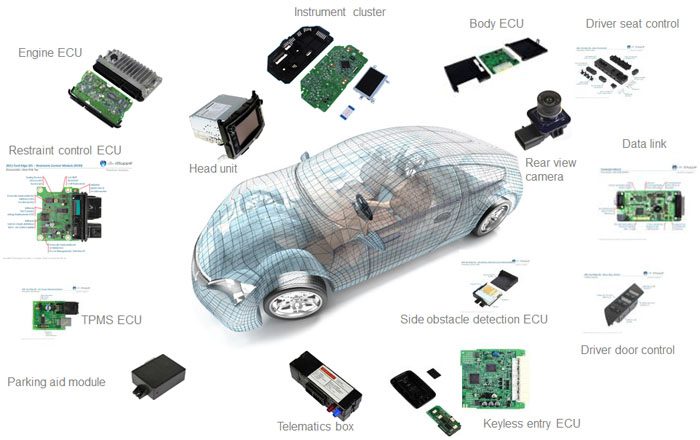
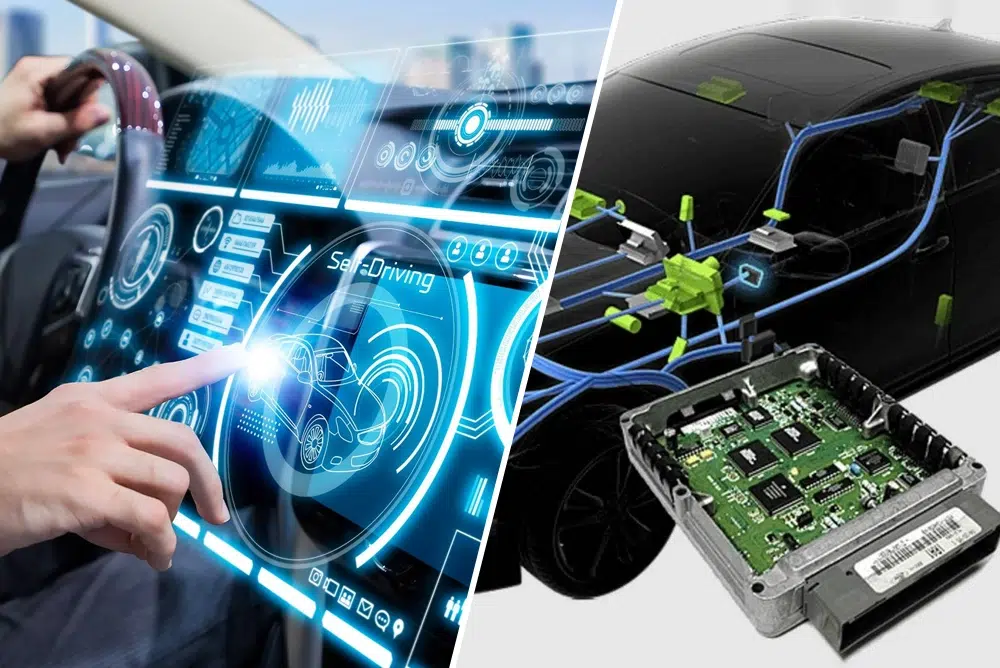
Electric / Autonomous Vehicles Applications
KKPCB offers extensive PCBA, wire harness, cable, and box build assembly services for commercial and industrial markets, with a strong focus on the electric vehicle industry. Our experienced team works with customers to fully realize their electric vehicle designs, regardless of the complexity.Automotive electronics is the combination of electronic information technology and traditional automotive technology. It is the general term for body electronic control and vehicle electronic control. PCBs are widely used in automotive electronics, including power control systems, safety control systems, body electronic systems, entertainment communications, etc.
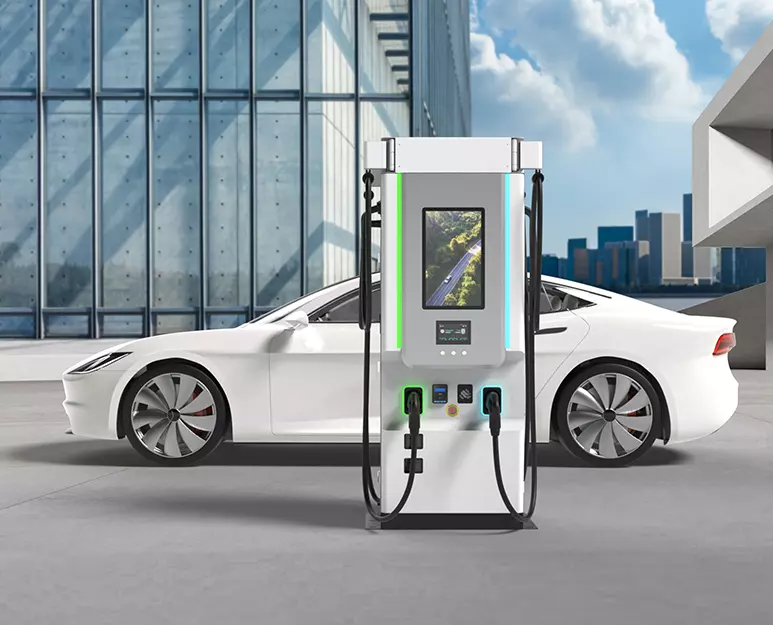
PCB Assembly
The compact and high-density designs of EVs demand robust PCB assembly techniques to handle complex circuitry, high-power requirements, and thermal management challenges. Additionally, PCB assembly ensures the seamless integration of sensors, communication modules, and safety systems, enabling critical functions such as regenerative braking, traction control, and vehicle diagnostics.
- Motor Controllers
- Battery Management Systems (BMS)
- Power Distribution Modules
- On-Board Chargers
- Inverter Modules
- DC-DC Converters
- Vehicle Control Units
- Instrument Clusters
- Charging Infrastructure Components
- Safety Systems (e.g., Airbag Control Units)
- Body Control Modules (BCMs)
Cable & Wire Harness
With the high-voltage power distribution, complex signal routing, and numerous interconnected components in EVs, cable, and wire harness assembly ensures reliable and efficient transmission of power, data, and control signals. Organizing, protecting, and securing the wiring, cable, and wire harness assembly minimizes the risk of electrical interference, short circuits, and malfunctions.
- Battery Pack Wiring Harnesses
- Motor and Inverter Wiring Harnesses
- Charging System Cables and Connectors
- High-Voltage Power Distribution Harnesses
- Vehicle Control Unit Wiring Harnesses
- Sensor and Actuator Wiring Harnesses
- Communication System Cables and Connectors
- Safety System Wiring Harnesses (e.g., Airbags)
- Lighting System Wiring Harnesses
- Interior and Infotainment System Wiring Harnesses
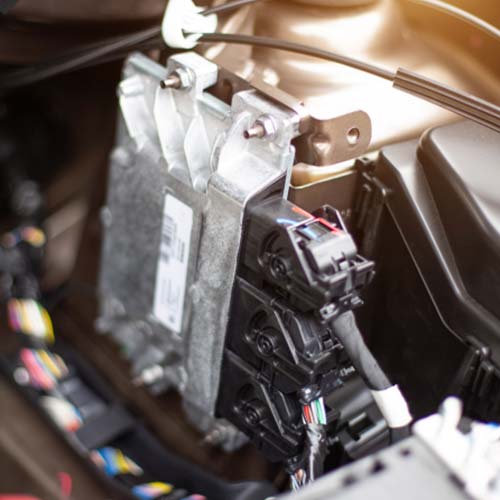
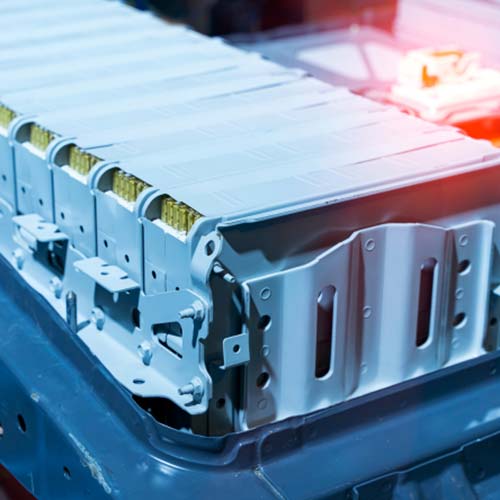
Box build assembly
Box build assembly holds significant importance in the electric vehicle (EV) industry as it encompasses the integration and construction of complex electronic and mechanical systems within an EV. Box build assembly ensures the seamless integration, compatibility, and functionality of these systems, contributing to the overall performance, reliability, and safety of electric vehicles.
- Battery Pack Assembly
- Motor Controller Units
- Power Distribution Boxes
- On-Board Charging Systems
- Inverter Assemblies
- Energy Management Systems
- Vehicle Control Units
- Electronic Control Modules
- Safety System Enclosures
- Infotainment System Assemblies
- Telematics Control Units
Characteristics of PCB manufacturing in the automotive field
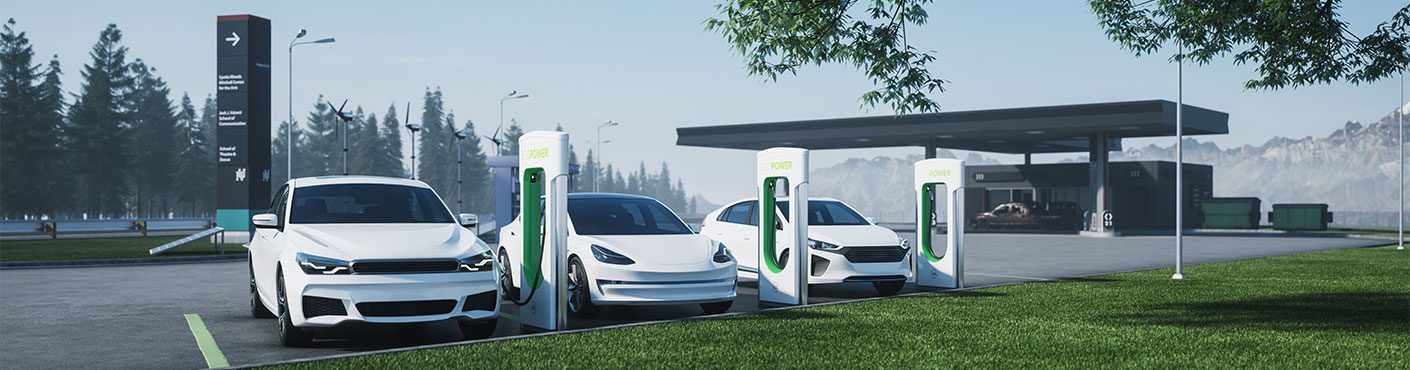
PCB manufacturing in the automotive field requires specific characteristics and considerations to meet the stringent requirements and standards of the industry. Here are some key characteristics of PCB manufacturing in the automotive field:
High Reliability
Automotive PCBs must exhibit high reliability and durability to withstand the demanding conditions and operating environments of vehicles. They should be able to withstand temperature variations, vibrations, moisture, and other harsh conditions without compromising performance.
Thermal Management
Automotive PCBs often encounter high-temperature environments, especially when located near the engine or in the vicinity of heat-generating components. Effective thermal management techniques, such as the use of heavy copper layers or thermal vias, are employed to dissipate heat and maintain optimal operating temperatures.
Design for Manufacturing (DFM)
PCB manufacturers in the automotive field employ robust Design for Manufacturing practices to optimize the manufacturability of automotive PCBs. DFM considerations involve ensuring proper component placement, optimized trace routing, impedance control, and effective signal integrity to minimize potential issues during production.
Quality Control and Testing
Rigorous quality control measures are implemented throughout the manufacturing process to ensure the reliability and performance of automotive PCBs. This includes comprehensive testing procedures, such as automated optical inspection (AOI), in-circuit testing (ICT), and environmental testing, to identify any defects or weaknesses and ensure adherence to specifications.
Robust Materials
The materials used in automotive PCB manufacturing are carefully selected to ensure resilience and longevity. High-quality substrates and laminates with excellent thermal and mechanical properties are chosen to withstand temperature extremes and provide stability in automotive applications.
Compliance with Automotive Standards
Automotive PCBs must adhere to industry-specific standards and regulations to ensure safety, reliability, and compatibility. Standards such as ITAF16949 and AECQ100 define the requirements for automotive electronic components, including PCBs, to meet the quality and performance expectations of the automotive industry.
Traceability and Documentation
Automotive PCB manufacturing requires meticulous traceability and documentation. This includes capturing and recording key information such as material sourcing, manufacturing parameters, testing results, and quality control measures. Traceability ensures transparency and facilitates investigations if necessary.
Long-term Availability
The automotive industry often relies on long product lifecycles, and therefore, PCB manufacturers in this field need to provide assurances of long-term availability and support for their products. This involves maintaining a stable supply chain, obsolescence management, and offering extended product life cycles to meet the needs of automotive manufacturers.
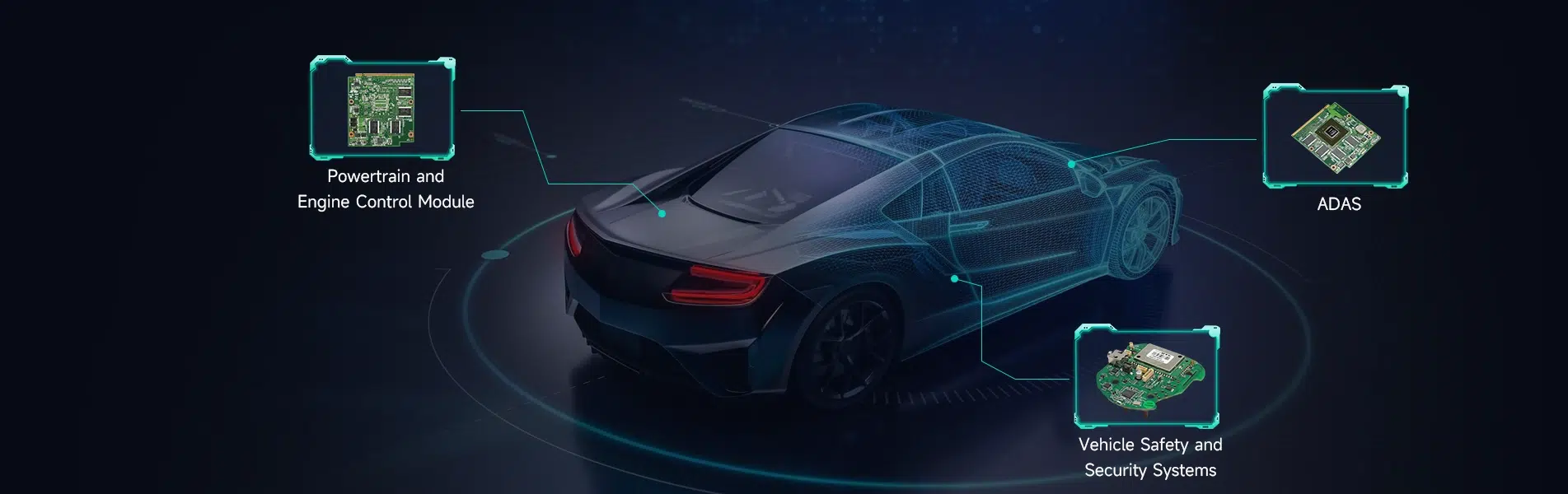
Automotive PCB Assembly
Frequent Questions
Automotive PCB assembly involves designing, manufacturing, and assembling PCBs for use in vehicles, ensuring high reliability, effective thermal management, and compliance with industry standards such as ISO/TS 16949. It utilizes advanced technologies such as HDI and SMT, and requires rigorous electromagnetic compatibility (EMC) and functional safety testing. These processes ensure that automotive PCBs can withstand harsh environmental conditions and meet the stringent quality and safety requirements of modern automotive electronics.
Automotive PCBs are critical to a variety of vehicle systems, including engine and transmission control, safety features, advanced driver assistance systems (ADAS), infotainment, lighting, climate control, battery management, sensor integration, telematics, power management, and instrument clusters. They enhance vehicle performance, safety, efficiency, and user experience, making them essential components in modern automotive electronics.
Automotive PCB assembly quality assurance includes adhering to standards such as ISO/TS 16949 and IPC-A-610, validating designs and processes, inspecting components, and ensuring high-quality soldering. Key practices include automated optical inspection (AOI), in-circuit testing (ICT), functional testing, and environmental stress testing to ensure reliability and performance. Comprehensive documentation, traceability, and continuous improvement processes are essential to maintaining high standards, while RoHS compliance ensures the restriction of hazardous substances. Together, these measures ensure that automotive PCBs meet stringent quality requirements for safety and durability.
Automotive PCBs are essential to modern cars, powering essential control systems, safety features, infotainment, lighting, and sensor integration. They ensure optimal performance, fuel efficiency, and compliance with safety and emissions regulations. Designed to withstand harsh conditions, automotive PCBs are critical to the reliability and durability of automotive electronic systems, making them essential for the functionality and safety of today’s cars.
For automotive PCB production and assembly, the necessary documents include design documents (schematics, Gerber files, BOM), manufacturing specifications (manufacturing and assembly drawings, template files), quality assurance documents (inspection plans, compliance certificates, environmental test reports), process documents (manufacturing processes, assembly instructions), traceability records (production components, certificates), change management records (engineering change orders), and customer specifications (design requirements, contracts). These documents ensure compliance, quality, and effective management of the entire production process.
Designing automotive PCBs requires special attention to reliability, durability, and thermal management to withstand harsh environments and extreme temperatures. Effective electromagnetic compatibility (EMC), mechanical stability, high component density, and compliance with industry standards are essential. In addition, signal integrity, cost optimization, and design for manufacturing (DFM) considerations ensure that the PCBs are reliable, cost-effective, and suitable for efficient production and assembly. Together, these factors ensure that automotive PCBs meet the demanding requirements of modern vehicles.
Automotive PCBs feature high reliability, effective thermal management, robust materials, electromagnetic compatibility, miniaturization, compliance with safety standards, environmental resistance, use of advanced technology, multi-layer design, and focus on functional safety. These features ensure that PCBs can meet the demanding requirements of automotive applications and provide reliable and durable performance in a variety of vehicle systems.
In the automotive industry, PCB assembly includes surface mount technology (SMT), through-hole technology (THT), hybrid technology, flexible PCB, rigid-flex PCB, high-density interconnect (HDI) PCB, metal core PCB, and double-sided or multi-layer PCB. The choice of these methods depends on the specific requirements for reliability, durability, and performance of various applications such as engine control units, infotainment systems, safety features, and high-power applications such as LED headlights.