Aluminum PCB vs. FR4 PCB: A Powerful Comparison of Cost, Materials, and Performance
When selecting the right substrate for your printed circuit board (PCB), understanding the key differences between aluminum PCBs and FR4 PCBs is crucial. From material properties and thermal management to cost and application suitability, this guide breaks down all the essential aspects to help you make an informed decision.
Key Differences Between Aluminum and FR4 Substrates
1. Material Properties
- Aluminum PCBs:
- Composed of an aluminum core infused with glass fiber.
- Features a thermal cladding layer for efficient heat dissipation, making it ideal for high-temperature applications like LED lighting.
- Provides mechanical strength and durability due to its metal base.
- FR4 PCBs:
- Made from woven glass fiber and epoxy resin, laminated with copper foil.
- Offers excellent electrical insulation and flame-retardant properties (FR stands for “flame retardant”).
- Lightweight and versatile, suitable for a wide range of low to medium-power applications.
2. Thermal Conductivity
- Aluminum PCBs:
- Superior thermal conductivity, making them the go-to choice for LED lighting and power electronics.
- Dissipates heat efficiently to prevent hotspots and improve component longevity.
- FR4 PCBs:
- Lower thermal conductivity compared to aluminum.
- May require additional thermal management techniques like heat sinks to handle excessive heat.
3. Coefficient of Thermal Expansion (CTR)
- Aluminum PCBs:
- CTR: ~50 × 10⁶ cm/cm-°C.
- Low thermal expansion coefficient ensures better reliability and prevents cracks in copper traces or metal holes.
- FR4 PCBs:
- CTR: ~110 × 10⁶ cm/cm-°C.
- Higher thermal expansion can lead to potential reliability issues in high-temperature applications.
4. Laminate Layers
- Aluminum PCBs:
- Typically consist of a three-layer structure: aluminum substrate, dielectric layer, and copper conductive layer.
- Designed for applications exposed to high temperatures.
- FR4 PCBs:
- Available in single-layer, double-layer, and multi-layer configurations.
- Offer greater flexibility in complex designs.
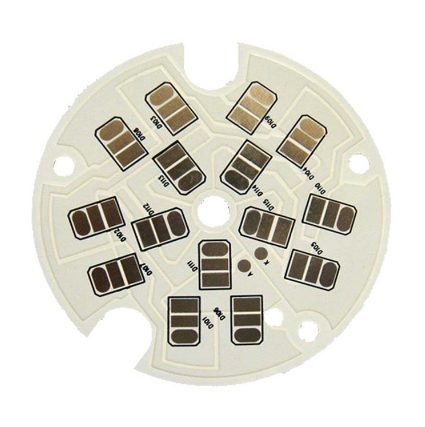
5. Mechanical Strength and Rigidity
- Aluminum PCBs:
- High rigidity and mechanical strength due to the metal core.
- Suitable for applications requiring large, durable boards that can handle multiple electrical components.
- FR4 PCBs:
- Lightweight and less rigid, ideal for compact devices where weight and flexibility are key considerations.
6. Manufacturing Differences
- Aluminum PCBs:
- Require specialized processes like PTH drilling for smooth and precise holes.
- Include additional heat sinks for enhanced cooling.
- FR4 PCBs:
- Simpler manufacturing process with layers of copper foil laminated onto fiberglass.
- Do not inherently include heat dissipation mechanisms, requiring external components for thermal management.
7. Thickness and Dimensions
- Aluminum PCBs:
- Limited thickness range, often dictated by the dielectric and backing layers.
- Thin aluminum PCBs may have reduced pressure resistance but provide superior heat dissipation.
- FR4 PCBs:
- Wider thickness options due to multi-layer lamination.
- Thicker boards allow for complex designs but may increase overall weight.
8. Cost Comparison
- Aluminum PCBs:
- Generally more expensive due to the cost of the aluminum core and specialized manufacturing requirements.
- Offer high-end performance and reliability in industrial and power applications.
- FR4 PCBs:
- More affordable and widely used due to the low cost of fiberglass and simpler manufacturing.
- Suitable for budget-sensitive applications.
9. Applications
- Aluminum PCBs:
- Ideal for LED lighting, automotive applications, and power electronics due to excellent thermal management.
- Commonly used in industrial devices requiring efficient heat dissipation.
- FR4 PCBs:
- Preferred for consumer electronics, telecommunications, and low-power devices.
- Suitable for complex, multi-layer designs like HDI (High-Density Interconnect) PCBs.
Feature Comparison: Aluminum vs. FR4 PCBs
Feature | Aluminum PCB | FR4 PCB |
---|---|---|
Substrate Material | Aluminum or copper core for heat dissipation | Woven fiberglass and epoxy resin for electrical insulation |
Thermal Conductivity | High, ensures rapid heat dissipation | Lower, may require external heat sinks |
Flexibility | Rigid, limited flexibility | Versatile, supports flexible and multi-layer designs |
Weight | Lightweight for high-performance applications | Heavier, especially in thicker multi-layer designs |
Cost-Effectiveness | Cost-effective for high-power applications | Affordable and widely available for various applications |
Applications | LED lighting, power electronics, automotive systems | Consumer electronics, telecommunications, industrial devices |
Thermal Management | Excellent, with built-in heat dissipation | May require additional thermal vias or heat sinks |
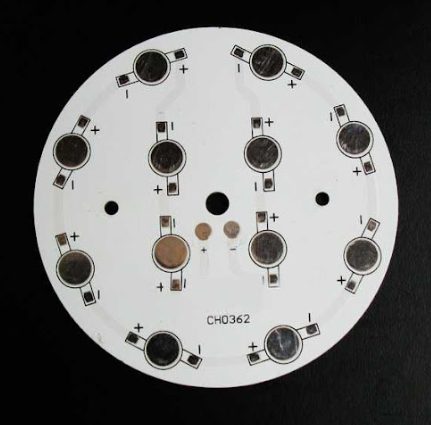
Aluminum and FR4 PCB Solutions
Our Aluminum PCB Offerings
- Double-Sided LED Aluminum Substrates
- Layers: 4
- Thickness: 1.6mm
- Outer Copper: 0.5 OZ
- Surface Treatment: ENIG
- Application: LED Lighting
- Single-Sided LED Aluminum Substrates
- Layers: 2
- Thickness: 1.2mm
- Outer Copper: 0.5 OZ
- Surface Treatment: OSP
- Application: LED Lighting
- Double-Sided Power Boards
- Layers: 4
- Thickness: 1.6mm
- Surface Finish: HASL
- Application: Power Electronics
FR4 PCB Solutions
- Suitable for multi-layer designs in telecommunications, industrial devices, and consumer electronics.
- Offers excellent electrical insulation and flame-retardant properties.
Aluminum and FR4 PCBs differ significantly in terms of material properties, thermal conductivity, cost, and applications. Aluminum PCBs are the best choice for applications requiring high thermal conductivity, such as LED lighting and power electronics. On the other hand, FR4 PCBs are more cost-effective and versatile, making them suitable for a broader range of low-power and complex designs.
Choose aluminum PCBs for performance-driven applications and FR4 PCBs for affordability and design flexibility. By understanding their strengths and limitations, you can select the ideal PCB substrate for your specific needs.