Copper Core PCB: A Revolution in the Electronics Industry
In the ever-evolving world of electronics, the demand for high-performance, reliable circuits continues to soar. Copper core PCBs (Copper Metal Core PCBs) have emerged as a key solution, providing unmatched thermal management and structural integrity for countless applications.
In this article, we will briefly outline the scope of our exploration, highlighting the characteristics of copper core PCBs and their importance in contemporary electronic products.
What is Copper Core PCB?
Copper Core PCBs (CCPCBs) fall under the category of Metal Core PCBs, which use metal as a substrate, hence also known as Copper-Based PCBs. Similarly, Copper Core PCBs also use copper as a substrate, mainly because of the thermal conductivity properties of the material while maintaining the durability of the board itself. They are mainly used in circuits that generate a lot of heat and require adequate heat dissipation to maintain the proper functioning of the mounted components. The thermal management of the product automatically means that the efficiency of the product can be greatly improved while also mounting high-performance components and ICs.
Construction of Copper Core PCBs
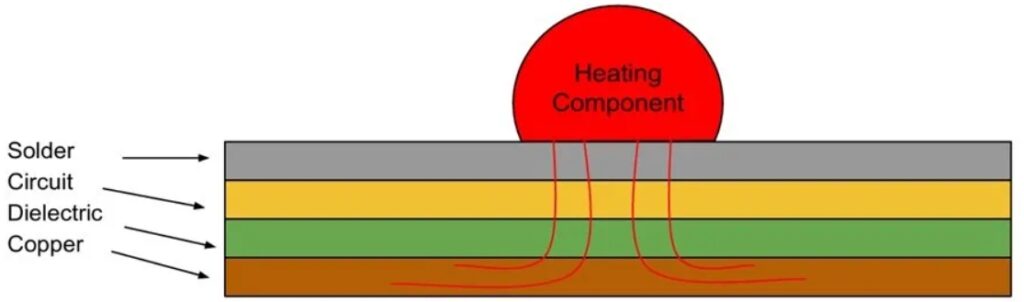
Solder Layer: The solder layer is where the components are soldered to the PCB.
Circuit Layer: The circuit layer is where all the wiring and traces are placed to form the circuit.
Dielectric Layer: The dielectric layer absorbs the heat from the components and transfers it to the copper core layer.
Copper Layer: The copper layer absorbs the heat from the upper layers and dissipates it, cooling the entire device.
Why do we need thermal management in copper core PCBs?
Ensure components operate on ideal curves
High-performance electronic components have several parameters that affect their ability to operate. One of them is the operating temperature range. Effective thermal management is essential to keep the temperature of all components within the range declared in the datasheet. The PCB needs to be as thermally efficient as possible so that the performance of the electronic components does not change or the components do not start operating near their derating curves. Moreover, overheating can temporarily or permanently damage the components, rendering the overall electronic circuit design useless.
Maintain Signal Integrity
Thermal management helps maintain signal integrity, which is essential for versatile and powerful electronic products. Essentially, the telecommunications industry and the defense industry rely heavily on high-frequency signals and their accuracy.
Maintain ideal resistance of components and traces
Also, increased temperature increases the resistance of components and traces, causing operational changes and significant changes in speed. Complex and high-performance systems use these copper core PCBs due to their excellent thermal management properties.
In order to sell these products, strict safety standards in thermal management also need to be adhered to. Aerospace, automotive, and medical devices, in particular, have extremely high thermal standards as they are extremely critical systems that can handle critical situations. Copper core PCBs allow manufacturers to better comply with these standards.
Features of Copper Core PCBs
High Heat Dissipation Performance
Essentially, the copper core layer of these PCBs acts as an efficient and effective heat sink, dissipating thermal energy away from delicate and critical components such as semiconductor ICs, transistors, MCUs, and power electronics. As a result, they eliminate the need to install separate heat sinks for components for thermal management, thus reducing the overall size of the product. In addition to the performance of the components, the thermal management of copper core PCBs will also help improve the lifespan and longevity of the components, thereby improving the lifespan of the entire product, significantly improving the reliability of the end product.
High Stability and Durability
In addition, copper is a transition metal and is the core of the PCB circuit board, which makes it very durable and structurally strong. Since copper is less likely to corrode or deform over time, it greatly improves the reliability and strength of the product. Copper core PCBs are believed to be more durable than ceramic or fiberglass boards, which are known for their durability. Being a more robust PCB, it also makes copper core PCBs resistant to any wear and tear during the manufacturing or use of the end product.
Copper core PCBs are versatile products that are suitable for a wide range of industries. Any industry that requires a durable, compact, high-performance, heat-resistant, and adaptable motherboard will definitely need copper core PCBs. These industries include aerospace, automotive, power electronics, and audio industries, as each field is racing to produce electronic products that are as compact and powerful as possible.
Applications of Copper Core PCBs
- Power Electronics
The power electronics industry includes power supplies, inverters, converters, solar energy, and more. All of these power electronic systems use switching circuits to convert or invert various voltages for use by multiple modules in each system. The switching circuits have high-frequency switching, so there are some switching losses, which generates a lot of heat that needs to be dissipated to keep the system cool. In addition, they employ delicate and complex circuits in these applications, which need to be protected from heat to achieve accurate performance. - Audio
The audio industry also adopts copper core PCBs because of their higher signal integrity and noise immunity. Audio output, input and power amplifiers, filters, etc. have a great demand for such PCBs that can manage temperature well and maintain signal quality. - Automotive
As the automotive industry gradually shifts to electric vehicles (EVs), the demand for advanced components will continue to rise. In addition to the conveniences in the car, modern fuel vehicles also emphasize features such as ADAS, cruise control, GPS, driving modes, screens with more applications, and better entertainment systems. Each of these innovations requires reliable and well-performing hardware. The circuit boards for these modern automotive systems are very suitable for copper core PCBs because of their extremely strong thermal management capabilities and shock resistance.
As the world rapidly shifts to smaller and smarter electronic devices, the demand for copper core PCBs will continue to grow. In addition, copper core printed circuit boards (copper-based PCBs) will greatly contribute to the improvement of quality, reliability, and performance of existing technologies. The superior electrical performance, excellent thermal management capabilities, high reliability, and amazing strength of metal cores (especially copper core PCBs) are revolutionary developments in the PCB industry and the various electronic industries associated with it. In particular, the reason why copper core PCBs play a vital role in the electronics manufacturing industry is because they can reach out to the multitude of industries they cater to and serve, and will continue to play a role in shaping the future of modern technology.