14 Important Requirements for High-Quality PCB Assembly
If you are new to the PCB industry, you may feel that PCBs look very similar. Can we identify the internal quality of PCBs by appearance? In fact, if there are slight differences in the appearance of PCBs, PCB industry experts can also identify the differences, and a good appearance is essential for the overall durability and functionality of PCBs.
Whether in the PCB manufacturing assembly process or in actual applications, good materials are essential for the reliable performance of PCBs. Because defects in PCB assembly may cause failures in actual product applications, resulting in immeasurable losses. Therefore, we should not only pay attention to the cost of PCB production, but also the materials and quality of PCBs.
In all PCB applications, especially those high-value and compact products, failures caused by PCBs will bring huge disasters to production applications. When you are looking for a PCB assembly manufacturer, we should remember that although the initial cost of reliable, high-quality and long-life PCB products is high, they are still worth it in the long run. So, what are the characteristics of high-reliability PCBs?
14 Important Requirements for High-Quality PCB Assembly
No soldering or disconnection required
Benefits of doing this: Perfect PCBs ensure reliability and safety, no maintenance, no risk.
Risk of not doing this: Without proper repair, the board will be damaged. Even with proper repair, there is a risk of failure under load conditions (vibration, etc.) in actual applications.
Hole wall copper thickness 25 microns
Benefits of doing this: Enhanced reliability, including improved z-axis expansion resistance.
Risk of not doing this: In actual applications, electrical connection problems during degassing, assembly (internal separation, hole wall cracking) or failure under load conditions may occur.
Cleanliness requirements exceed IPC specifications
Benefits of doing this: Improved PCB cleanliness and reliability.
Risk of not doing this: Residues and solder accumulation on the board pose a risk to the solder mask, while ionic residues pose a risk of corrosion and contamination to the solder surface, causing adverse reliability issues (bad solder/electrical failure) and increasing the possibility of actual failure.
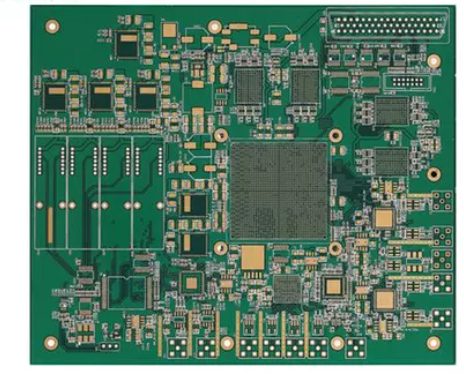
Use branded materials – don’t use unknown brands
Benefits of doing this: Improved reliability and stability performance.
Risk of not doing it: Poor mechanical properties make the printed circuit board unable to perform as expected under assembly conditions, for example, for higher scalability, this will lead to delamination, disconnection and warping problems, as well as poor impedance performance due to reduced electrical characteristics.
Strictly control every surface treatment
Benefits of doing this: Strong soldering ability, high reliability, and reduced risk of moisture intrusion.
Risk of not doing this:
Due to the change of the surface treatment of the old printed circuit board, solder problems may occur, and the ingress of moisture may cause delamination, separation of the inner layer from the hole wall (breakage) and other problems during assembly or actual application.
Resistor materials meet IPC-SM-840ClassT requirements
Benefits of doing this: Good ink is conducive to improving ink safety and solder resistance.
Risk of not doing this: Poor quality ink will cause problems such as adhesion, flux resistance and hardness. All these problems will cause the resistor layer to fall off the printed circuit board, and eventually lead to corrosion of the copper circuit. Poor insulation may cause short circuits due to unexpected electrical connections or arcs.
The tolerance of the copper clad board meets the requirements of IPC4101ClassB/L
Benefits of doing this: Strict control of dielectric thickness is conducive to reducing the deviation of expected electrical performance.
Risks of not doing this:
If the electrical performance may not meet the requirements, and it will cause a large difference in the output performance of the same batch of components.
Define the tolerances of shapes, holes and other mechanical features
Benefits of doing this: Strict tolerance control is conducive to improving the size and quality of the product.
Risks of not doing this:
Problems occur during PCB assembly, such as alignment/matching, and in addition, dimensional deviation problems occur when installing the base.
Appearance and repair requirements
Benefits of doing this: Careful processing during manufacturing will bring good appearance.
Risks of not doing this:
If all kinds of scratches and minor damage repairs occur on the PCB, they may bring invisible risks, adverse effects on assembly, and risks in actual applications.
Plug hole depth requirements
Benefits of doing this: High-quality plug holes will reduce the risk of failure during PCB assembly.
Risks of not doing this:
Underfilled holes may have residues in them, causing problems such as solderability, while tin beads may also hide in the holes and splash out, causing short circuits during PCB assembly or actual application.
Avoid using paper with scrap units
Benefits of doing this: Not using local assembly helps customers improve efficiency.
Risks of not doing this:
Defective units require special PCB assembly processing. If not clearly marked or isolated from the sleeve, defective PCBs may be produced, wasting parts and time.
Resistor layer thickness
Benefits of doing this: Improve electrical insulation, reduce the risk of peeling or loss of adhesion, and enhance resistance.
Risks of not doing this:
Resistor layers that are too thin can cause problems such as adhesion, flux resistance, and hardness. All of these problems can cause the resistor layer to fall off the printed circuit board, ultimately leading to corrosion of the copper circuit. Too thin resistor layers lead to poor insulation and accidental conduction/arcing leading to short circuits.
Peelable blue glue brand
Benefits of doing this: Peelable blue glue brand avoids potential risks.
Risk of not doing this: Poor quality or cheap peelable adhesive may cause blistering, melting, cracking or solidify like concrete during PCB assembly, making the peelable adhesive impossible to peel off.
Check every step
Benefit of doing this: Careful steps ensure that all specifications are confirmed.
Risk of not doing this:
If product specifications are not carefully confirmed, deviations may occur during PCB assembly or the final product.
We handle all types of PCB assembly projects with any quantity especially small batch assembly and low volume PCB assembly, from basic through-hole PCB assembly technology to standard surface mount assembly (SMT PCB assembly and THT assembly), mixed assembly, kit assembly to ultra-fine pitch BGA assembly.Our PCB types for our custom PCB assembly include: rigid PCB, Metal Core PCB, flex PCB and rigid flex PCB..etc.